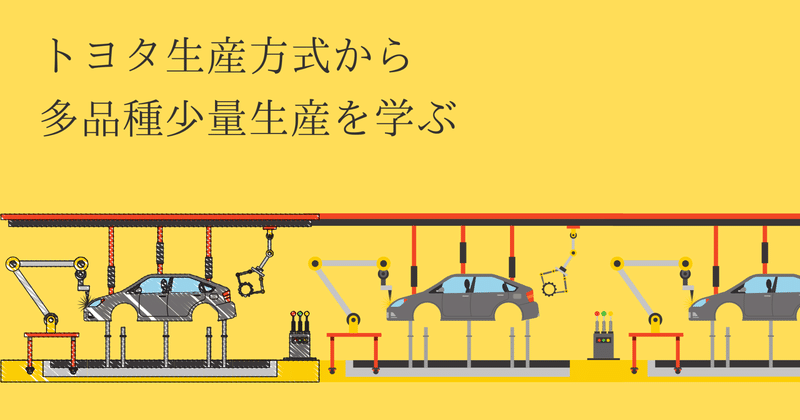
トヨタ生産方式から多品種少量生産を学ぶ
こんにちは。突然ですが、最近ものづくり系YouTuberのものづくり太郎さんの動画をよく見ています。半導体や自動車に関して、誰にでもわかるように丁寧に説明されていて非常に勉強になります。私自身もものづくり太郎さんのようなチャンネルを作ることが理想ですが、まだまだ経験、勉強不足もあり、情報量、密度、わかりやすさ、人脈、全てにおいて全く及ばないことを痛感しています。。。ものづくり太郎さんのように良い情報発信ができることを目指して、私には私のできることを少しずつコツコツと頑張ろうと思います。
さて、その中で参考文献を紹介されている動画があり、そこでまず「トヨタ生産方式」を一番に紹介されていました。日本のものづくりトップ企業の本質を語る本ですが、恥ずかしながらまだ読んだことがありませんでしたので、今回読ませて頂き感想を述べたいと思いました。
全体の感想
今までトヨタ生産方式は「かんばんで後工程から取りに行く」とか「あんどんにより進捗が見える化されている」といった部分的なところしか理解できていませんでした。トヨタ生産方式の全体を学ぶと、多品種少量生産を実現するために、何十年も時間と労力をかけて作られた「経営の考え方」なのだと理解できました。これらはものづくり全てに通じるものがあります。日本のものづくりをリードしてきて、さらに世界の目標にされたこれらの考え方を学ぶことができ、今後よりものづくりを深く理解していくことができると思いました。
0. あらすじ
トヨタ生産方式 = 多品種少量生産を実現する生産・生産管理・経営の考え方
大量生産ではなく、必要なものを、必要な時に、必要なだけ供給することで在庫を最小限にして、企業のムダを徹底的に省く生産方式。
ジャストインタイム
必要なものを、必要な時に、必要なだけ供給するという理念。
従来の前工程から順番に生産するシステムとは違い、
「後工程が前工程に必要なものを必要な時に取りに行く」 → 「前工程は取られた分だけ生産」するシステム。
最終組立ラインに「必要な車種を必要なだけ欲しい」と生産計画を示すことで、組立ラインで使われる各種の部品を前工程に取りに行く。これを全ライン、全協力工場で連携する。
その工程間のやりとりを「かんばん」を用いて行っている。かんばんには引取情報又は運搬・生産指示情報が載っており、かんばんのやり取りをするだけで、「いつ」作るのかも含めて生産管理ができる。引き取られない限り生産しないため、ムダな在庫ができない。かんばんで連携させることで生産ラインの全体の流れを作っている。
前工程は、常に標準手持ち量をストックしており、その中から後工程から引き取られた分だけ生産する。ロッド数が大きいと一度に大量に持ってかれるため、常に大量の在庫が必要になってしまい工場が回らなくなる。そのため小ロッドで何度も引取を繰り返すことになる。それを「生産の平準化」とよんでいる。このかんばんによる生産の流れと平準化された生産計画により、多品種の生産(品種の頻繁な変更)や需要の変動に強いラインができる。
その小ロッドで多品種の生産を実現するために、徹底的に無駄を省き、段取り替え時間を削減する工夫を施している。例えばプレスの金型交換作業は、2〜3時間かかっていたものを3分で行うまでに至った。
自働化
もう一つ、トヨタ生産方式を実現する考え方に「自働化」がある。単なる自動化された機械ではなく、「機械に人間の知恵を持たせること」である。具体的には、異常がでた時に自動で停止する装置がついた機械、生産ラインのことである。安全が重視される車を生産しているため、どの工場、ラインでも正常・異常の区別が明確で、誰が見てもわかるようになっている。生産計画・進捗を現場の大型モニタで移すことで一眼で理解できる「あんどん」などを用いて、人と在庫、機械の目で見る管理を徹底している。そのことによりムダを徹底的に省くことで、生産管理を行っている。
小人化とは、人がかける力を減らす省人化とは違い、人間の数を減らすこと。大きな生産数、同じ生産数をより少ない人で行うこと。そのためにまずは作業や作業現場の改善が必要、その後設備改善を考える必要がある。
感想
1. 経営視点から考えた「つくりすぎのムダ」の徹底排除
トヨタには「在庫は悪」という考えが徹底されていました。つくりすぎることによる在庫は、在庫の管理費、運搬費、設備の動力等様々な二次的なムダに派生するため、削減することを徹底されていました。全体の生産計画を小ロッドで「平準化」して、後工程から前工程に必要な分だけ引取に行くこと、工程ごとに「標準手持ち」(=在庫)を決めておきそれ以上は作らないことにより、生産システム自体が在庫ができないシステムになっているため、「つくりすぎのムダ」を失くせているのだと思いました。経営視点から現場での生産体制を考えて、トライ&エラーを繰り返したからこそ実現しているシステムだと思いました。
別の本では、「トヨタは在庫を持たないため、災害などでサプライチェーンがダメージを受けた時に、連鎖して生産できなくなることがある。一方、他社は生産を維持できていることがあるが、それは大量の在庫を管理していることを意味する。」(自動車工場の全て ダイヤモンド社)と書かれており、在庫を持たないことが徹底できていること、及びその考え方はトヨタ独自のものであることが理解でき、納得しました。
自動車以外の工場でも、自動車よりもはるかに多品種少量生産のところがほとんどです。そういった工場でも在庫を必要以上に持つことは非常にムダが発生しており、多品種だからこそ管理工数も多くなります。多品種といってもある程度量が出る自動車で在庫なし・最小限化ができているため、その他の業種では必ずできることだと思います。そのため、生産計画以上のものを作ったり、設備稼働率を上げるために作りすぎるというような、作りすぎのムダをなくすことは非常に大切だと理解できました。
2. 「情報も必要なものを必要な時に必要なだけ」
トヨタでは「情報」に関しても、ジャストインタイムの徹底が図られていました。生産計画は、車種ごとに月次生産計画がありそれを元に日次計画を平準化して並べて最終組立ラインに配布するだけでした。各工程は、かんばんを引き取られた分だけ作るため、前工程側に特別な生産計画は不要という考えからそのような計画にされていました。情報が溢れていると、何が大切な情報かわからなくなります。情報も必要な時に必要な分だけを与えていることからも徹底されていると感じ、ジャストインタイムの生産を実現する上で必要不可欠であると思いました。さらにこれは、どのような業界、職種でも同じだと思います。溢れすぎている情報をそぎ落とし、必要な情報を必要な分だけ得ることで生産性が向上すると思いました。
3. トヨタ生産方式が合う工場
ではどのような工場がトヨタ生産方式が合うかを考えてみました。多品種少量生産といっても、1つ〜数個のロッド毎に全く新しい設計・プログラミングが必要なところもあれば、請負加工で様々な加工依頼が急遽入るところ、輸送機械や家電など個数は出るが細かい種類が豊富にあるところ、自動車のようにロッド数も他業界と比べると多いが多品種なところ、と様々です。
トヨタ生産方式が合うか合わないかはそれぞれの業態にもよるとは思いますが、考え方はどの工場も見習うべきだと思います。企業の利益を考えて徹底的にムダを省く姿勢、必要な時に必要なものを必要なだけ生産するジャストインタイムの生産、それを実現する小ロッドで平準化された生産計画、機械を自動化させるだけでなく人間の知恵を持たせる自働化、人間の数を減らす小人化といった生産方式の考え方はどの企業も参考になり、その上で独自の工場、生産方式を生み出す必要があると考えました。
受託加工業者や中小の多品種少量(本当の少量)生産の会社は、必要なものを必要な時に、必要なだけ生産することは当たり前に行っていると思います。でもその生産管理を社長や各担当者の頭の中で行っていることが多いと思います。トヨタ生産方式とは、その生産管理を徹底した組織機能(ルール)として明確にしていることにより、量が多くても多品種で原価が低い生産が実現しているのだと思います。自社の立場や強み、特徴を生かしつつルールにしていくことでより徹底されると感じました。
4. 経営状況や工場全体から考える稼ぐ力を維持するための自動化
トヨタ生産方式からは設備をただ単に自動化して省人化すれば良いというわけではないことを学びました。一つの設備の価値は、「どれだけ稼ぐ力を維持しているか」で判断すると書かれていました。つまり、どれでけ生産能力があるかではなく、どれだけ使いたい時に使うことができるか、という意味です。
単に自動化するだけでは、その工程のみの時間は早くなるかもしれませんが、前後工程でネック工程がある場合や、段替え、メンテナンスにより時間がかかってしまうようなことになってしまっては、なんの意味もありません。設備を自動化する際は、作業者を減らしての原価削減やネック工程を早めて全体の最適化を計るなど、経営状況や工場全体を考える必要があります。さらに自動化するだけでなく、段替えやメンテナンス等、変化に柔軟に対応できる必要があります。それらを理解した上で、設備の自動化を図っていく必要があると改めて思いました。
5. トヨタ生産方式から考えるIoTによる見える化の目的
トヨタ生産方式は考え方であり、徹底した生産ラインの見える化による生産管理システムのことです。数十年もかけてトヨタが作りあげてきたからこそそのような管理ができるのですが、工場の見える化にいたってはIoTシステムを利用することで実現することもできます。
生産ライン・生産計画・進捗を見える化することで、離れた場所でも生産状況を把握することができ、何か起きた場合への対応や変化の対応が可能となります。見える化により設備毎の生産性の向上を求めるのではなく、工場全体を把握して、より多くの受注ができるようになること、その判断をするための情報を的確に随時容易に見れる状態にしておくことこそがIoTの目的になるのではないかと思いました。さらに予防保全をすることで設備故障によるライン停止を削減したり、稼働状況をみてネック工程の把握→改善、生産能力の余力の把握をできると思います。トヨタ生産方式では、かんばんを用いて協力工場含めて実現されていますが、それらを様々な製品、より多品種少量な製品でも実現するためにIoTを活用することができるのではないかと思いました。
以上となります。今回も長文となってしまいましたが、最後まで読んで頂きありがとうございました。今回は特にただの感想のようになってしまい、私自身のアウトプットが目的になっているため、得られることが少なかったかもしれませんが、今後はより価値のある情報を届けていきたいと思いますので、また今後とも宜しくお願い致します。
この記事が気に入ったらサポートをしてみませんか?