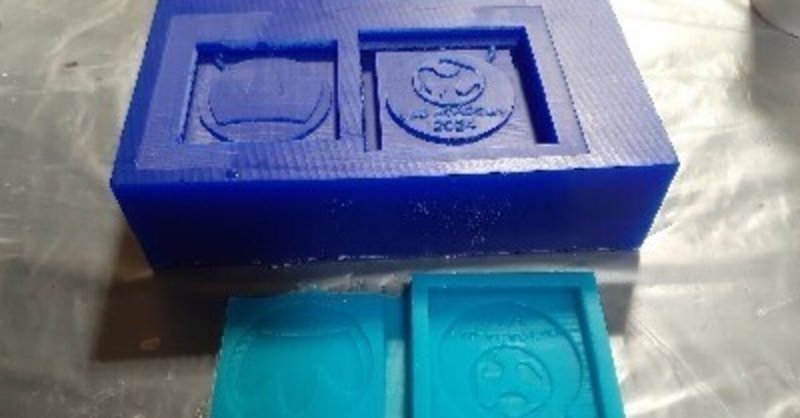
これは面白い!成型鋳造の世界
私が今年のファブアカデミーを受講開始してから3カ月が経とうとしています。できれば毎週取り組んでいて英語でのドキュメンテーションにまとめている内容を、日本語にして逐次レポートしたかったのですが、あまりにも毎週のアサインメントがきついので、とても紹介できません。過去にnoteでそれをやろうとした先輩方の手記をたまに見かけたりもしますが、たいていの場合1回アップしてあとが続かない形で終わっています。
なんとか卒業までこぎつけることができたら、その時にはnoteで回顧録を書いてみるのはありかなと思っています。それくらい、英語でのドキュメンテーションはしっかりやっているので、それをDeepLあたりで翻訳するだけでも、結構リッチな日本語コンテンツができ上がりそうな気がします。
ただ、さすがにまるまる1カ月noteで何も書かないというのは淋しい。そこで、最近ファブアカデミーで実習して、面白かったテーマについて、今回は紹介してみたいと思います。それが、第12週で行われた「成型と鋳造(Molding and Casting)」です。
3Dプリンターを使っていると、ほぼ何でも作れそうだという感覚にとらわれることがありますが、実は課題もあります。1つは、特に熱積層方式(FDM)のプリンターの印刷速度の遅さ、2つめは印刷精度の粗さ(それを克服する試行錯誤の手間とその過程で生み出す「屍」の数々)です。後者については、試作の過程ですので3Dプリンターじゃなかったら減らせるという性格のものではありませんが、それじゃデザインが決まっていざ量産となった時、3Dプリンターでは生産速度は遅すぎ。しかも、金属製品を積層印刷するのは市販のプリンターだと難易度が恐ろしく高くなります。試作段階ならともかく、量産段階で3Dプリンターというのはちょっとなしですかね。
そこで、鋳型を作ってそこに素材を流し込んじゃったらどうかということになります。しかも、FDMプリンターだと克服が難しい(少なくとも今の僕の実力では…)積層痕が残る鋳型ではなく、本来思い描いていたようなツルツルの表面を作るのだったら、わざわざFDMプリンターでマイナスの鋳型を作らなくてもいいかもしれません。
この辺は、以前、UVレジンを固めてキータグを作ってみた時の苦い経験に依拠しています。3Dプリンターで鋳型を作るとレジンが固まったあとにブツをほじくり出すのが大変だと考え、ちょっとやわらかめのTPUフィラメントで積層してみたところ、結果出来上がった鋳型の表面のザラザラ感や「糸挽き(stringing)」がそのままレジン成型にも反映されてしまい、あまりいいキータグができなかったという記憶があります。
そこで、ファブアカデミーで今回取り組んだのが、シリコンでマイナスの鋳型を作ってそこに液状ウレタンを流し込むという手法でした。
当然ながら、出来上がりイメージ(ポジの鋳型)は3D CADプログラムでデザインしました。私の場合はFusion360を使用。ここから、2枚おろしのの鋳型をデザインし、これを固形ワックスの大きさに合わせた直方体の箱の表面に配置します。最後に液化ウレタンを注ぎ込む穴と中の空気を抜く穴を作っておきます。
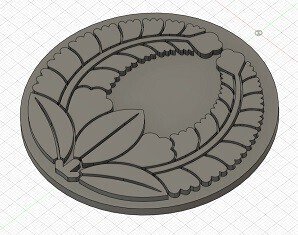
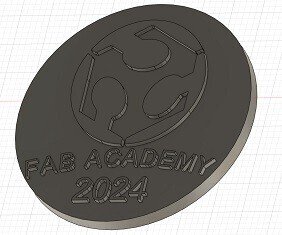
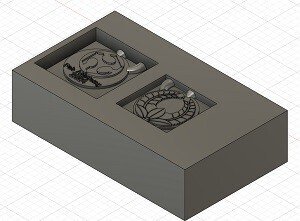
この固形ワックスのSTLファイルをエクスポートし、CNC切削加工機を使って切り出しました。これが、マイナス(ネガ)の鋳型となります。
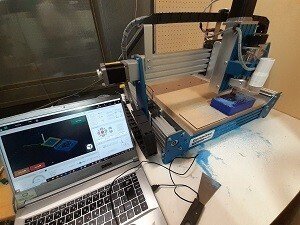
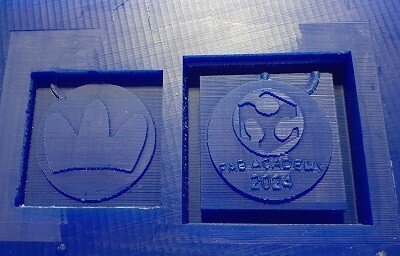
次に、そこに液状のシリコンラバーを注ぎ込みます。使用するシリコンラバー液の性格にもよりますが、だいたい30分程度で固まります(2つの液体の配合比率や、撹拌時間、その他取り扱い上の注意事項は、SDS(Safety Data Sheet)で要確認。そしたらそれをほじくり出して、2つの鋳型を組み合わせたら、3D成型用の鋳型になります。
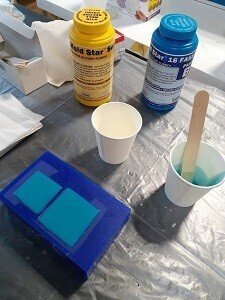
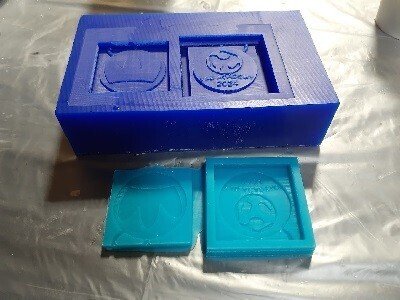
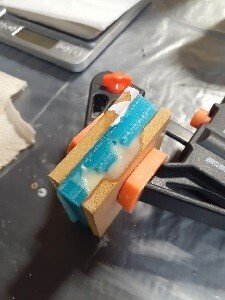
もう1つは空気穴
最後はそこに液状ウレタンを流し込みます。空気穴から液状ウレタンがあふれ出してきたら、中がウレタンで充填されたサイン。あとは10分少々待って、ウレタンが凝固したのを見計らってシリコン鋳型をパカっと開けてみると、中から成型されたブツが出てきます。
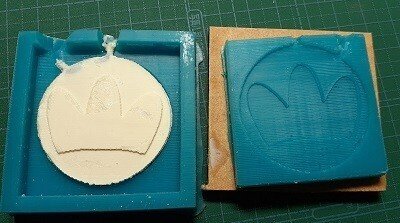
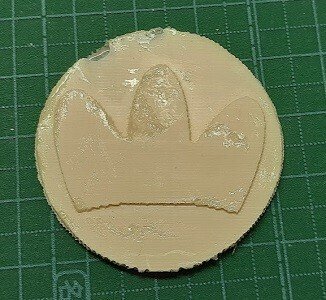
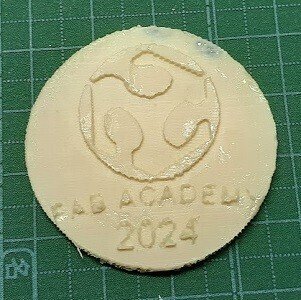
実習では、表裏ともにエンボスを施したメダルを作ってみることにしました。デザインが細かすぎたようで、エンドミルの直径を下げてもきれいに切削できず、しかも細かくてその分余計に時間がかかってしまうので、表面のザラツキ感で妥協を強いられました。出来はあまりよくなかったけれど、シリコン鋳型を使った一連の鋳造プロセスを体験できたのはよかった。
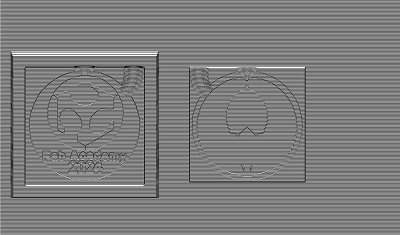
表面の家紋は、もっとシンプルなロゴに変更してから切削加工に入った。
今回はもう1つ、同じデザインのメダルをビスマス合金で作るのにも挑戦しました。しかも、鋳型はなんとレーザー加工機で切削したMDF板。一般的に金属を溶かすと融点が高くて木材は鋳型としては適さないと勝手に思っていましたが、ビスマス合金の融点は138℃と低めなので、MDF板を焼き焦がすといった事態は起きません。
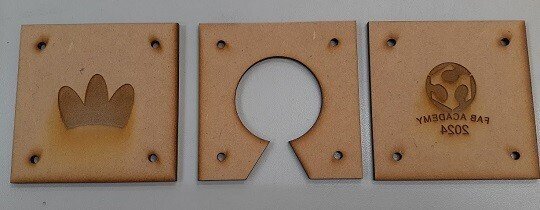
真ん中にコインの切り抜き穴を切削。空気穴を忘れずに!

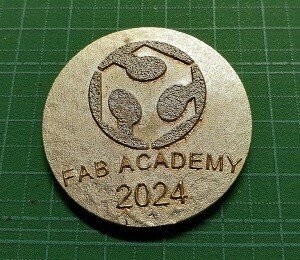
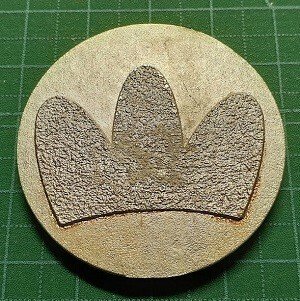
エンボスはきれいに出たと思う
融点がこれくらい低いなら、シリコンラバーで作ったネガ鋳型に溶けた合金を注入してもたぶんできたでしょう。でも、合金が溶けているからといって表面温度が138℃だというわけではないため、溶けた合金の温度が230℃を超えていると、シリコンラバーに何らかの影響が生じるかもしれません。そのへんの注意は必要です。
金属鋳造は、対象とする金属の融点を考慮しつつ、適切なアプローチを考える必要があります。例えば、私はブータンで働いていた頃、配属先だったCSTのキャンパス周辺で道端に捨てられていたアルミ製のビール缶を集め、電気溶解炉で溶かしてアルミのインゴットを作っていましたが、アルミの場合、融点は比較的低めだといっても660℃あります。この鋳造にシリコンラバーを使うのはリスクが高いでしょう。MDF板は現地で入手困難なので、代わりに合板でメダル鋳造をやってみましたが、ちゃんとアルミ製のメダルができ上がりました。
アルミインゴットが何本かできると、これを用いて何が作れるのかを考える必要があります。でも、それをCSTの狭いコミュニティの中だけで考えるのではいいアイデアが出てこない。それで、外部の人も交えてオープンにアイデアを出し合う場を設けようと考え、昨年7月のFab Bhutan Challengeで、アルミ缶廃棄物を自助具としてアップサイクルするテーマを打ち出しました。
Fab Bhutan Challengeでは、下肢に麻痺を抱えて「ウォーカー」と呼ばれる歩行器をふだん使っている地元の女の子の歩行器の修理のために、「砂型鋳造」という方法によってパーツが作られました。高温のアルミで鋳造するのであれば、この方法になるのでしょう。
本稿では、書いているうちに融点が高い素材の方にどんどん話が向かっている気がします(笑)。逆に石膏や3Dプリントのように、常温に近い状態でも鋳型が成型できるアプローチも考えられます。指輪やペンダントトップのような金属製のアクセサリー作りでも、ポジ鋳型をまずワックスを削って作り、これを石膏で固めた後で熱して、中のワックスを溶かして蒸発させ、出来上がった空洞(ネガ鋳型)に溶けた金属を注入する「ロストワックス法」というのもあります。
もう少しブータンに長くいられたら、CSTで問題視されていた「紙ゴミ」についても、水を含ませてパルプ状にして、鋳型に押し込んでプレスをかけるという方法も挑戦できたかもしれません。鶏卵の運搬用のコンテナも、この方法で作ることができないか、あるいは鶏卵に限らず、梱包の際の内容品の緩衝材を作ったりはできた可能性があります。
こうして見てみると、成型鋳造はけっこう奥が深そうです。今回はCNC切削加工機、FDMプリンター、レーザー加工機等を利用した鋳型成型でしたが、もっといろいろな方法を経験して、いろいろな生産要素賦存状況に合わせていろいろなアプローチを提案できるよう、これからもいろいろ体験してみたいと思います。
本日のお話は以上となります。ファブアカデミーでの実習体験レポートは、英文ですが下記の個人アサインメント、グループアサインメントのページにまとめました。写真だけでもプロセスはご理解いただけると思うので、本日の記事でご興味を持たれた方は、是非ウェブサイトの方もご笑覧下さい。
この記事が気に入ったらサポートをしてみませんか?