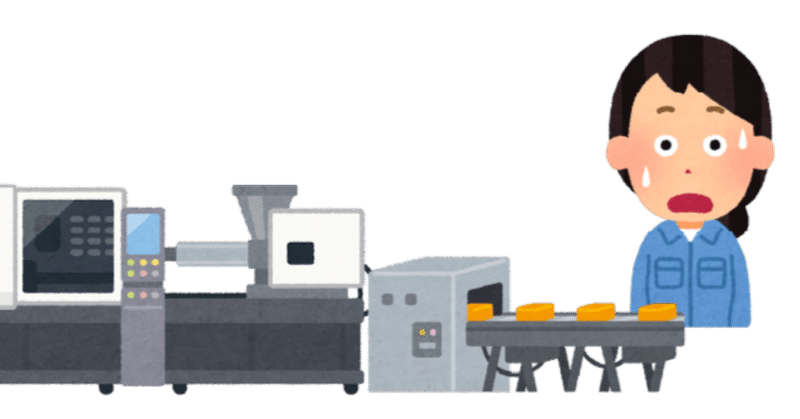
射出成形機の機械付き作業【体験談】
先日のお話です。
とある企業にてプラスチックの射出成形機に付いて作業をする体験しました。
プラスチック業界でいうところの、有人機作業です。
イメージでいうと・・・・
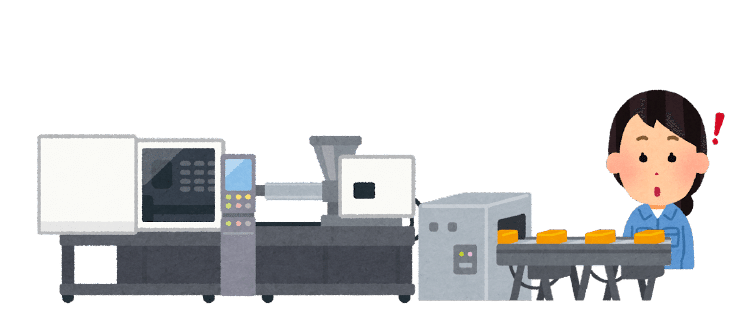
イメージ図はこんな感じですね。
有人機なので、射出成形機の扉を開けて、成形されたプラスチックを取り出します。
プラスチックとは、こんな感じの小さい粒、米のようなものが材料です。
この状態ものを「ペレット材」と呼びます。
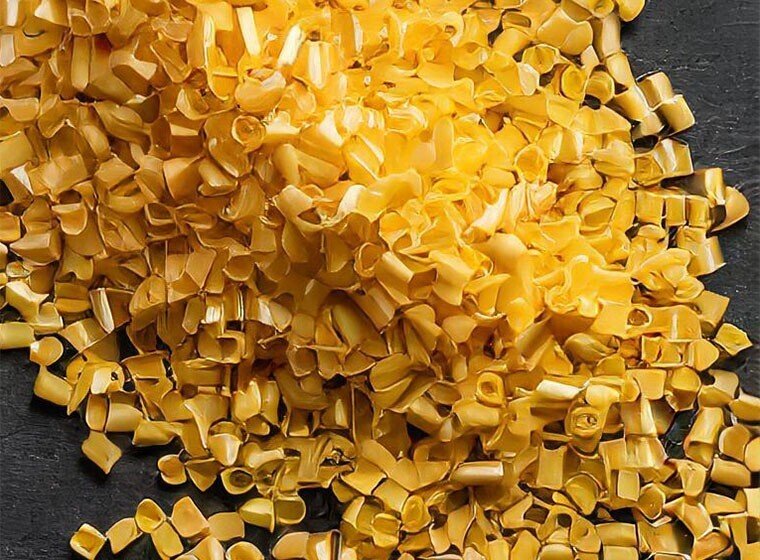
射出成形の流れは・・・
ペレットを熱で溶かします
解けた樹脂を金型へ流し込みます
冷やして固める
いう工程になります。
製品が固まったよーという合図があり、射出成形機の金型が両端にぐいーんと離れます。
そしたら、扉を開けて完成したものを取り出します。
冷却されているけど、成形直後は熱いので火傷に注意です。
物によっては、ランナーが残っています。
ランナーとは、溶かした樹脂を金型に送り込む通路のような役割です。
我々がコンビニに行くときに、道を歩くように、プラスチックにも通路があるんです。
そうしてプラスチック製品を金型から引っ張り出します。
ランナー(通路)は無駄な部分なので、ニッパーで切ります。
これを箱に入れて行きます。
纏めると、射出成形機の有人機作業は、
扉を閉める
成形されるのを待つ
金型から取り出す
ニッパーで切る
扉を閉める
成形されるのを待つ
検査
梱包
このような感じですね。ニッパーで切って検査、梱包している間に次の成形をするというのが多いです。
これを数時間やっていると、正直疲れます。
ニッパーで切る力が最後は無かった。
正直申すと、向いてない人には苦痛です(笑)
成形工場に久しぶりに行きましたが、これだけを1日するのはしんどいなあと思いました。
プラスチックの経験談はもっとたくさんあります!
これからも投稿していきます。
この記事が気に入ったらサポートをしてみませんか?