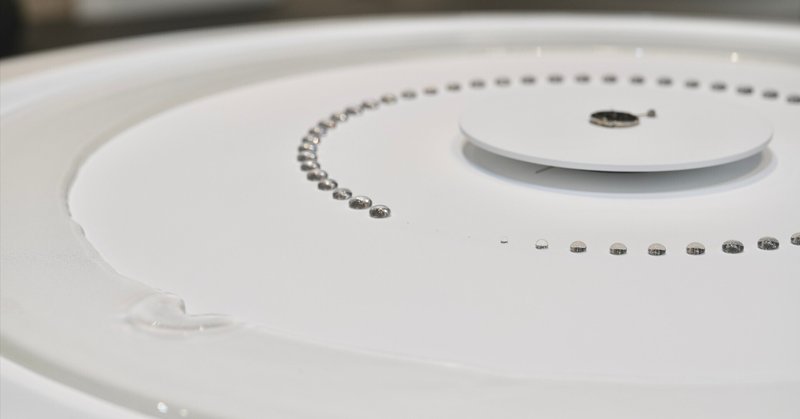
「時のしずく」について語る #3
現在開催中のSeikoSeed「からくりの森」で展示してる新作「時のしずく」について語るシリーズ第三弾。
過去記事はこちら。
前回の記事で、全体の構成が確定した感じのところまで来ましたね。さぁ、今回はいよいよ本制作のプロセスなど紹介してみます。
全てはCADで設計
松山はFusion360使ってます。メンバーの神山くんはSolidworksとFusion360と両方使うみたいです。今回は合わせてFusion使ってくれてたのかも。
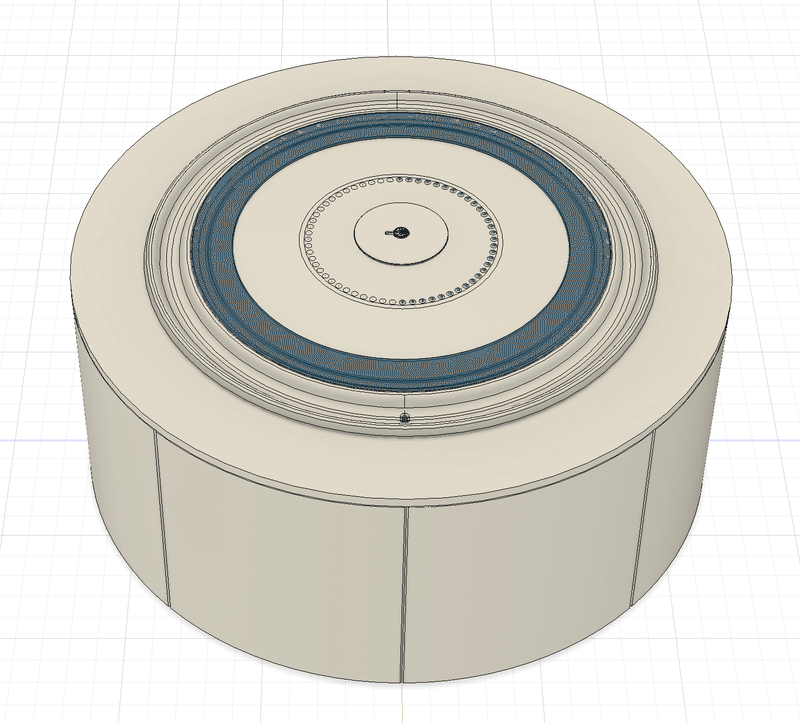
これ見ても何もわかんないと思いますが、中身もチューブ以外はだいたいCAD上で組み立てています。
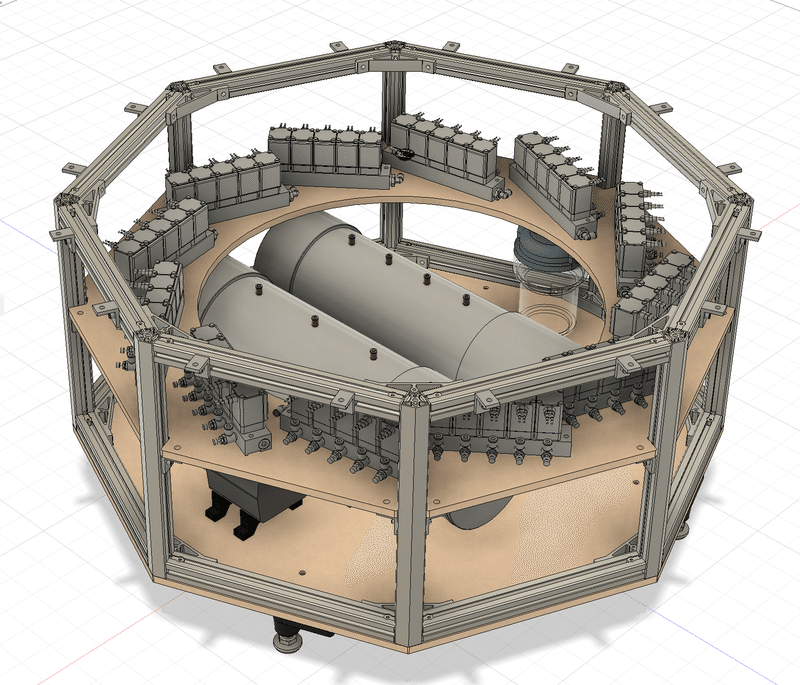
すでに「おぉ、中はすごいことになってる!」と思ったと思いますが、本当に結構ややこしいです。
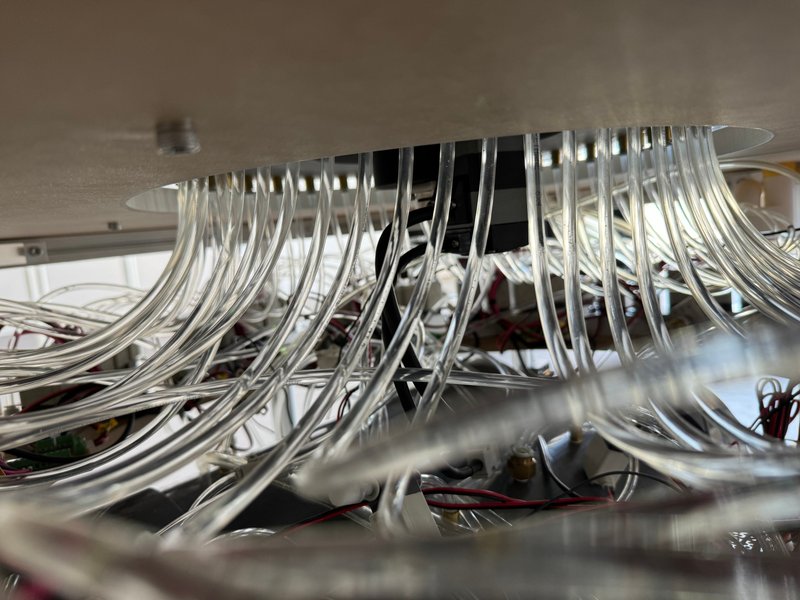
1秒1滴で1分60滴って話をしてましたが、つまりは60チューブです。何もかもが60式。1分の重みを味わいました。
制御について
皆さん馴染みがないと思いますが、水をどうやってコントロールするのかについて説明してみます。特許性は特に無いと思うので。
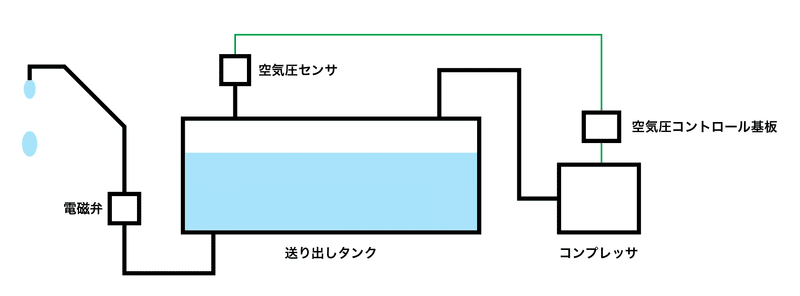
上の絵を見てください。まずタンクがあります。そこに水が入ってます。水が入ってるけど空気もあります。その空気の部分にコンプレッサーで空気を追加していきます。すると、空気圧は高くなり空気圧センサの値は高くなります。設定した圧力を超えたところで、コントロール基板を通じてコンプレッサーの電源を落とします。すると、気圧は指定した値でとまります。圧力が下がるとまたコンプレッサーが動くので、結果的にタンクの空気部分は指定した圧力を維持されます。
その加圧した空気に押された水は、下に穴があれば「ピューッ」と吹き出すことになります。その穴にチューブをつけて、電磁弁をつなぎます。すると、電磁弁を開くまでは水がでないけど、弁を開くと水が出るという状態が完成します。
これが、#2で話してた「圧縮空気方式」です。つまり図の電磁弁が60個あるってことです。
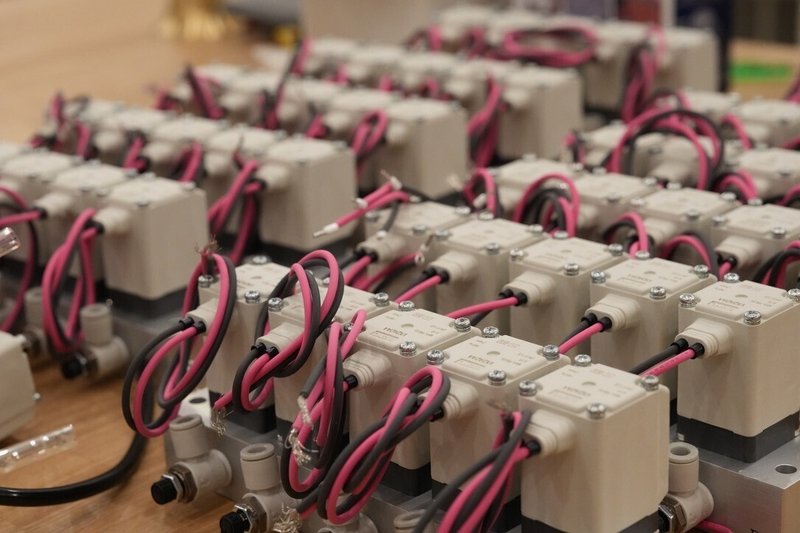
電磁弁はマニホールドと言って今回は5連の状態で購入しました。本来はエアー用なので水を流すとじわっとしか流ません(オリフィス径が小さい)が、今回の用途では問題ないのでマニホールドを優先しました。
タンクは実際には2つあって、排水用と送り出し用で分かれます。排水された水を一旦貯めるために、排水タンクがあります。
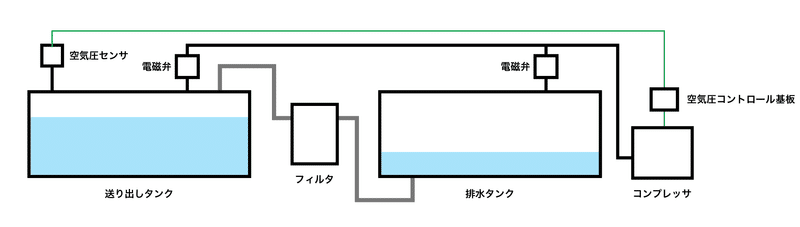
このぐらいから、興味ない人にはさっぱりだと思いますが、興味ある人が多いと踏んで説明すると、排水タンクは実際はちょっと負圧にします。金魚ポンプを改造して吸い込みにし、それをつなぐことで排水性能を高めるわけです。
で、動かしてると排水された水がたまり、送り出しタンクの水が少なくなるので、ある程度の時間が経過したら排水タンクの水を送り出しタンクの方に移動させたいです。そこもコンプレッサーでいけちゃいます。
排水タンクの方を加圧し、送り出しタンクは排気用の弁をつけてあけておく。すると、排水タンクの水はフィルタを通って送り出しタンクに移動します。
(実際は、フィルタにも電磁弁つけてたりとか、排気弁がそれぞれにあってそれも電磁弁つけてたりとか、とにかくたくさん制御パーツが接続されています)
説明してても難しいので、この辺にしといてやりますが、実際はたくさんの電磁弁と配管で繋がっています。それを制御しないといけません。
基板作る
電磁弁を合計70個近くコントロールする必要があります。なので、基板が必要になります。

人に話すと「は?」と言われますが、イラレで基板設計します。エッチングで基板つくるような時代(昔はプリント基板をWebで入稿するのはレアだった)からやってるのと、最初にイラレマスターになってしまってたので、イラレで基板も設計してます。
いや、siro社全体でいうと基本はFusionとかイーグルとかで設計するんですけど、自分の場合は明日までに必要みたいなときに担当するケースが多いので、イラレで1~2時間で設計して、CNCで1時間程度で切削完了。
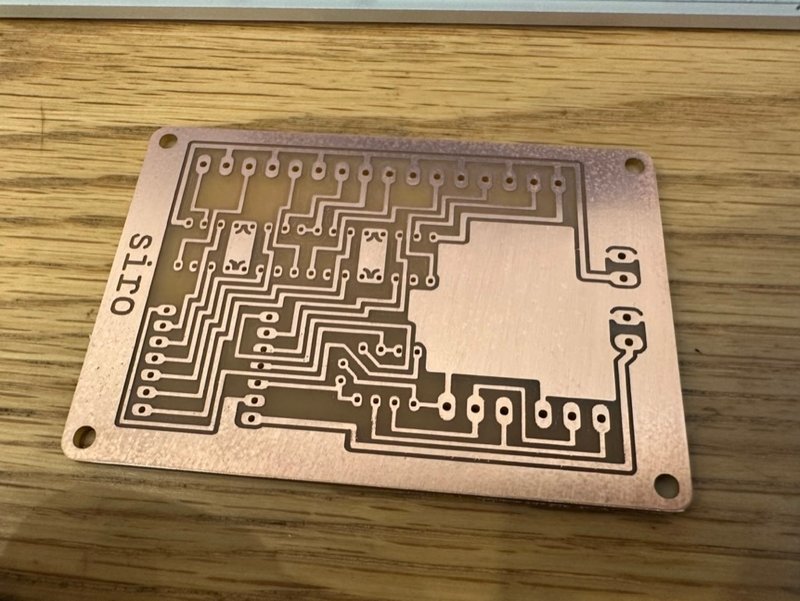
エッチングは廃液がでて嫌なので、あるときからCNCで切削して作るようになりました。こういう感じで穴も開けてくれるのでとても便利です。大体シンプルな基板しか作らないので、片面基板です。
ではんだ付けしてコーティングして完成したらこう。
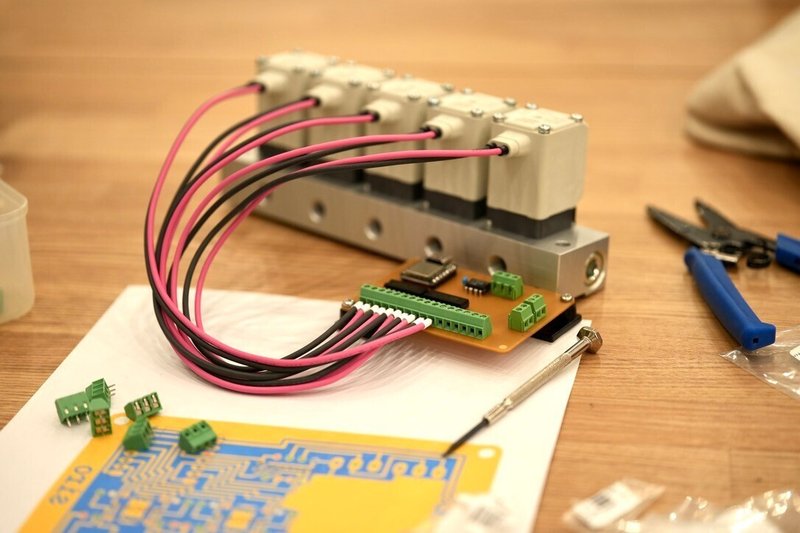
8chのOutput基板(RS-485搭載)を作りましたが、5連の電磁弁使うことにしたので、3ch余らせて12枚基板作りました。その他もろもろの制御もあるので、追加1枚で13枚ですね。ちなみに電磁弁は24Vタイプ。
あと基板の話しでやや余談気味な話を。3Dプリンタを新しくして出力時間がかなり短縮できたので、3Dプリントパーツで基板マウントしてみようと考えて下のを作ってみました。
アルミフレームの溝にはまります。た、楽しい。
音のピックアップ
今回は時計の音をピックアップして、その音から時計の進むスピードを検出して連動させるという要素があります。
そのピックアップは時計の歩度計でも使われてました。が歩度計からセンサー取るわけにもいかないので、なんか上手くピックアップしたい。ここは神山くんの方でサクッと試作してくれました。
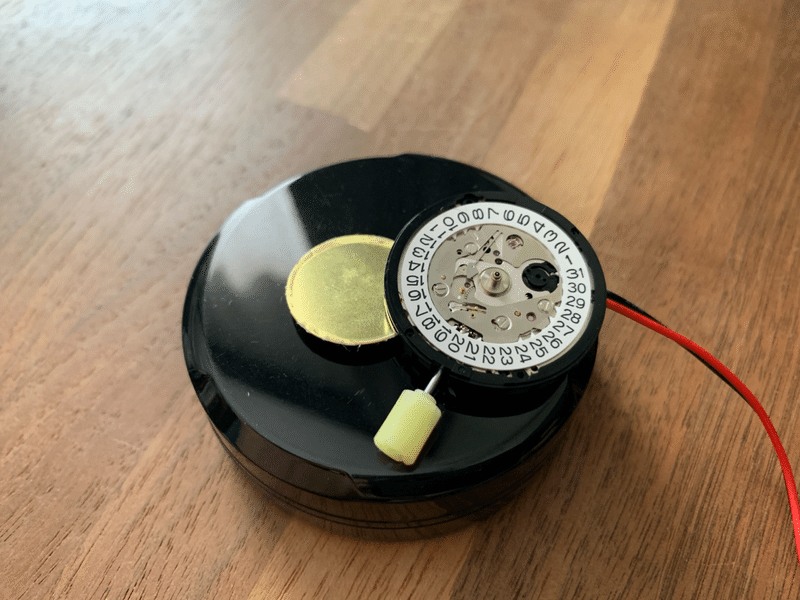
ピエゾをそのままパソコンのマイク端子に繋いで取り込めたとのこと。フィルターなどの処理をプログラムでかけたところ、時計の6Hzの振動を検知できたというところまで4月の段階でやってもらってました。
風をどう回転させるか
風で水滴を落とせることはわかってました。風を出すノズルを回転させる必要があります。見た感じシンプルにまとめたく、時計を置く部分はど真ん中に柱を立ててその柱の中に配線を通したい。でも空気を出すノズルは回したい。
柱とエアーのチューブが絡む姿が想像できた人は設計がわかる人ですね。その人向けに書きますが、ロータリージョイントを使いました。
回転部分は神山くんに設計してもらいました。
モーターはオリエンタルモーターのAZにしてゼロだし動作不要にしました。シンプルでいい。
組み立て
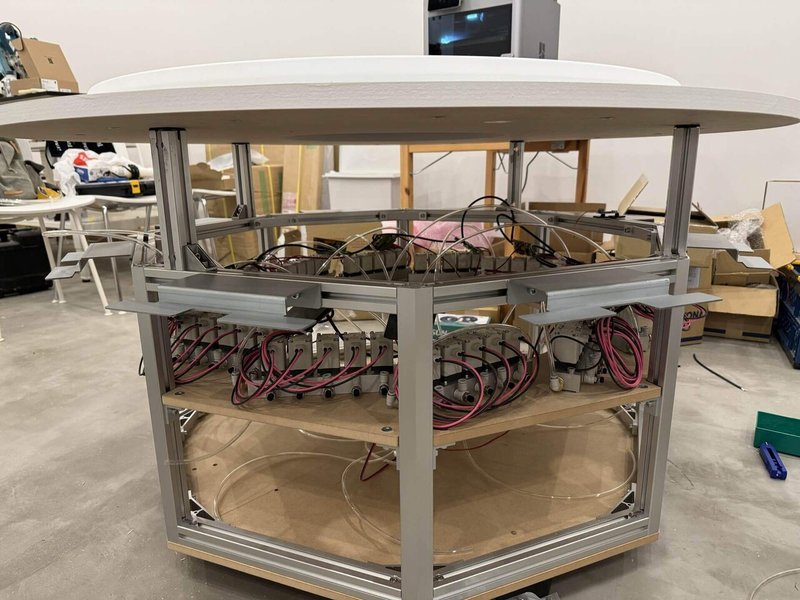
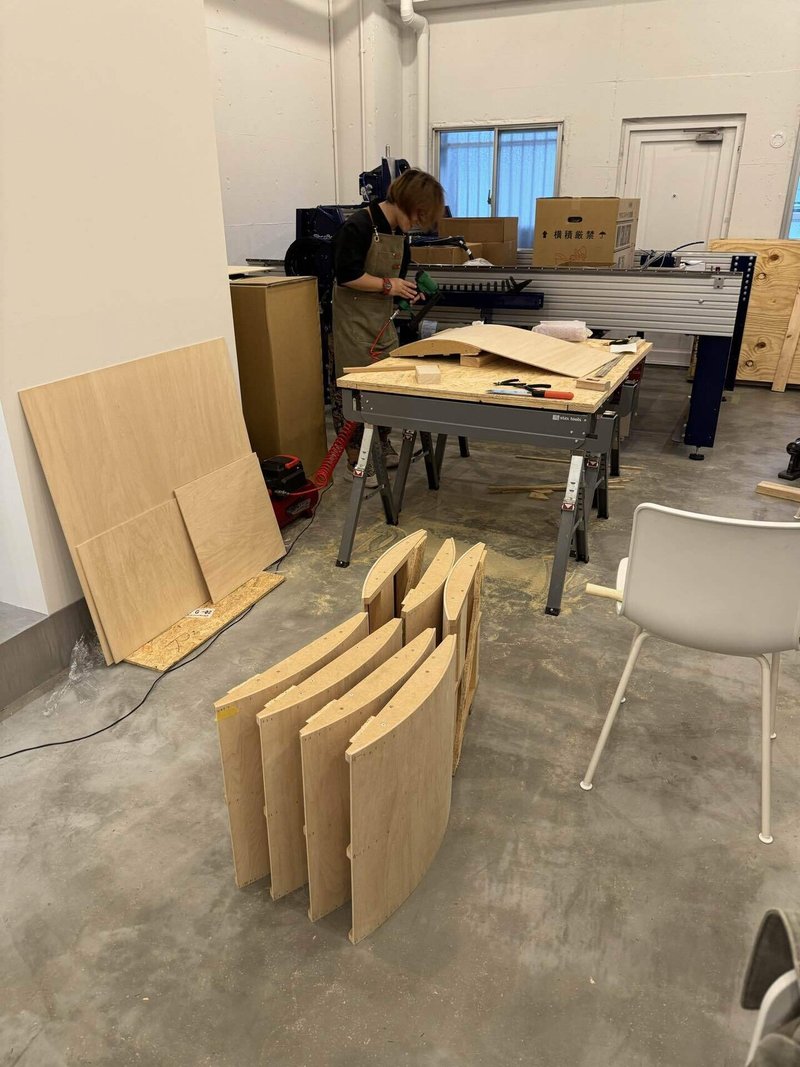
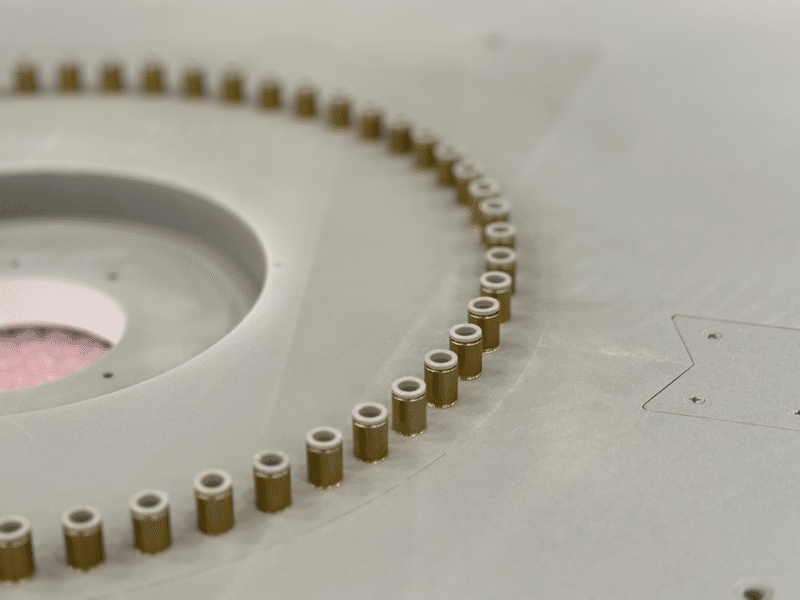
とにかく大変。怒涛の設計発注、組み立て組み立て。
美しく完成
組み立てが終わったので、サクッとプログラム書いて動作検証。動いた!
お堀の水が初めて溢れる時。
声が出ちゃってますね。これ夜中です。現場に運ぶ前日夜の夜中。
あれれ、排水がゴボボボって鳴る、、、。これは嫌。
最後の調整
排水の音問題は、排水穴の下の構造でなんとかなりました。3Dプリンタ様様。
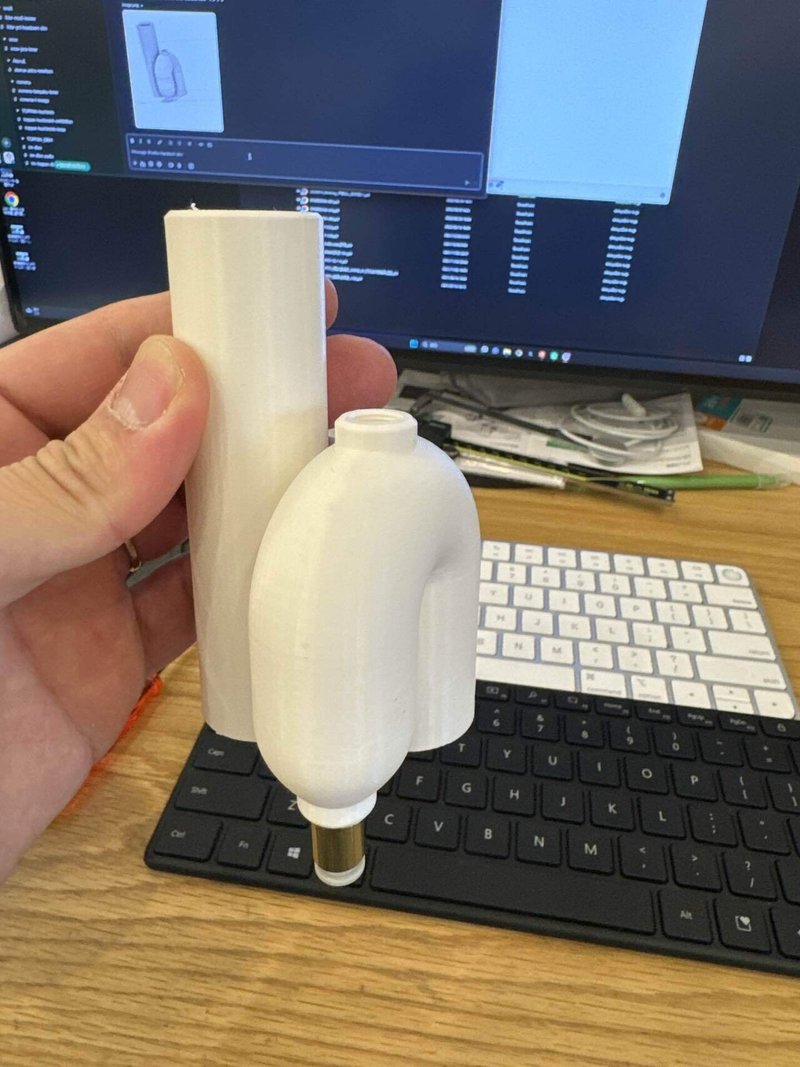
説明が難しいので、端折りますが、とにかくこれでゴボゴボは改善。あとは水滴の大きさ揃えたりなんとかかんとかで現場で完成!
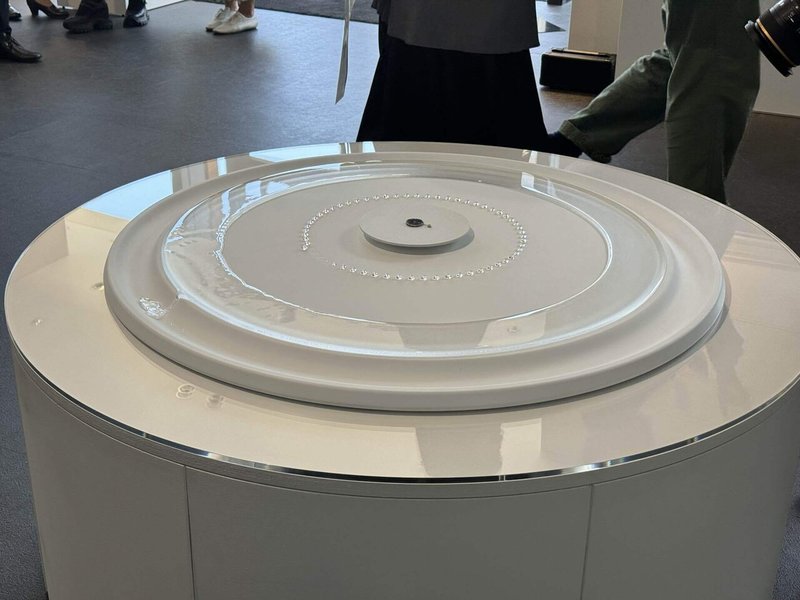
天板に載せたアクリルも最高。全てやり切った。お疲れ様!
終わりではない、始まったのだ
会期は長く、2ヶ月半ほどあります。つまり、メンテナンスが始まりました。
いろいろ繊細な作品ですので、調整が必要。まだその辺のノウハウはよちよちです。とにかくメンテナンスで維持していく作戦しかない。水も交換しないとだし。
最後にカメラマンの大木さんが撮ってくれた映像を貼っておきます。
まとめ
自分で読み返してみましたが、情報量多いッ!これはテクニカル系の人向けの記事ですね。完全に。。。
次回、最後のまとめ記事みたいなのを書こうと思います。
この記事が気に入ったらサポートをしてみませんか?