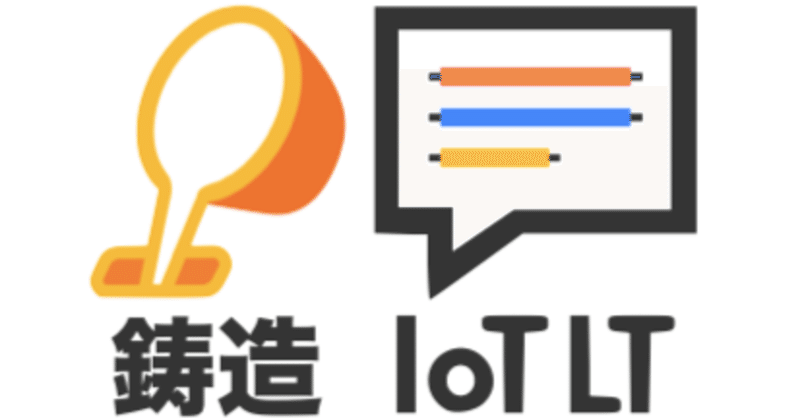
【動画レポ】鋳造IoTLT Vol.7
今回は先日(2023年3月29日)に開催された鋳造IoTLTの動画を見てレポートします。鋳造IoTLTは仕事でやっているという真剣さと、その過酷な環境というかいろんな制約の中での話が多いせいなのか独創的な取り組みがもあったりしてなかなかおもしろいスピンオフです。今回もどんな話が出てくるのか楽しみです。
<動画です>
オープニング
オープニングはIoTLTのコミュニティ紹介とイベントについての説明からスタートしました。今回は8人のスピーカーが登壇します。
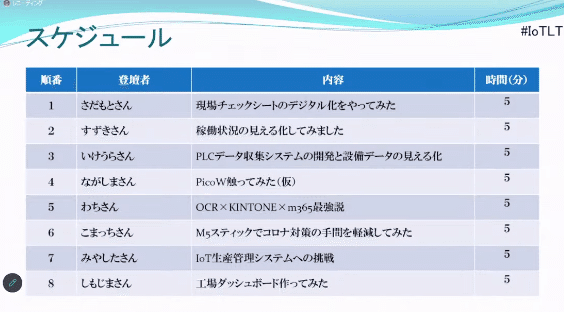
そこからは「鋳造」というものについての紹介です。
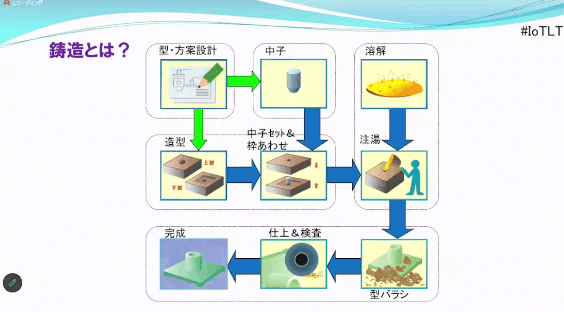
鋳造とは金属を熱で溶かして型に流し込んで成形するものづくりのひとつの方法で、複雑な形状の成形ができ、様々な材料への対応、少量から大量生産まで対応できる特徴があり、マンホールの蓋から大仏、そして自動車などの部品まで様々なものを作るために行われています。
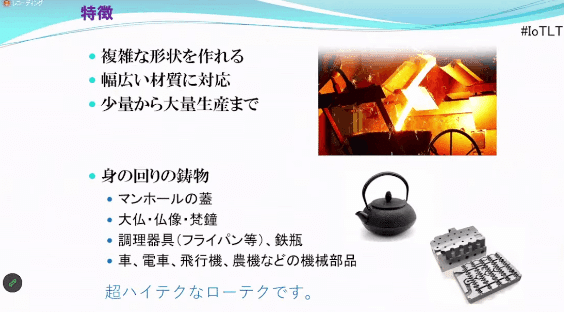
古くからある加工方法ですが最近ではセンサーなど様々な機器を使って行われるハイテク産業になってきています。「超ハイテクなローテク」と読んでいるそうです。
IoTLTをはじめた目的は、企業の担当者がなかなか交流がなくいろんな悩みがある中で各担当が孤軍奮闘されている反面、業界の外からは遠く感じられてしまっているという状況をなんとかしてみんなで取り組もうというものです。
LT1:現場チェックシートのデジタル化をやってみた
トップバッターは広島県で自動車部品用の金型などを作っている友鉄工業の定本さんの発表です。友鉄工業さんはマツダスタジアム周辺のマンホールも作っているそうです。

定本さんの発表は製品ごとに作られた各工程の確認項目や温度などを記録する「現場チェックシート」をデジタル化した話です。紙のチェックシートでは汚損したりするうえに確認しにくくデータとして活かしづらいなどの問題がありました。
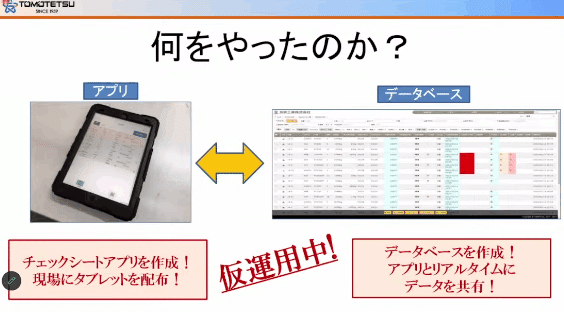
今回はアプリとデータベースを作ってリアルタイムにデータ共有するシステムを作りました。作業者が簡単に操作できるようにタッチとリスト選択のみで入力し、写真撮影・保存もできるようになっています。
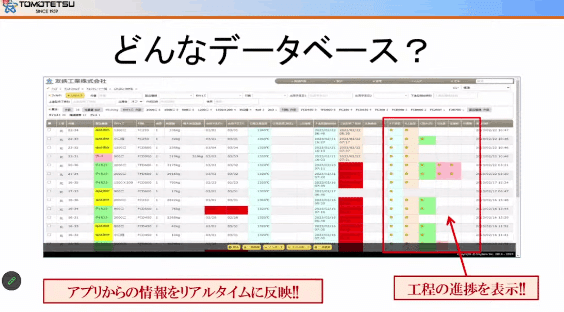
データベースはPCだけでなくタブレットからもアクセスでき、校庭の進捗状況を確認できるようになっています。またチェック内容や写真も確認できます。
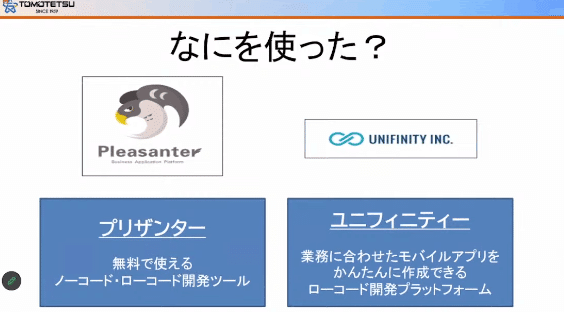
開発に使ったのはローコード・ノーコードツールのプリザンターとユニフィ二ティーです。
作る際には現場にヒアリングを行ってからツールを探し、教えてもらいながらアプリとデータベースの作成を行い、仮運用して現場で確認しながら改善を繰り返しているそうです。自然発生なアジャイルですね。アプリの開発方法の理解や現場との仕様のすり合わせに苦労したそうです。
高齢な現場メンバーに慣れてもらうため、現在は仮運用中で現場への浸透とバグの確認解消を行っているそうです。
LT2:稼働の見える化してみました!
次は静岡県と群馬県を拠点にフルモールド鋳造法をメインに行なっている木村鋳造所の鈴木さんのLTです。
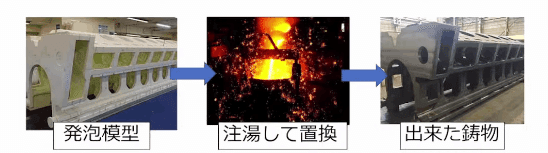
フルモールド鋳造法で使用する発泡スチロールの型を作成するNC機械の稼働状況の見える化が今回紹介する内容です。
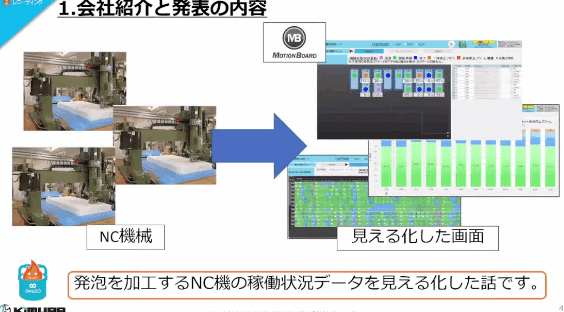
NC機械からは稼動ログがテキスト形式で出力されていますが、活用されていなかったので、このデータを使って稼働状況の表示に取り組みがスタートしました。
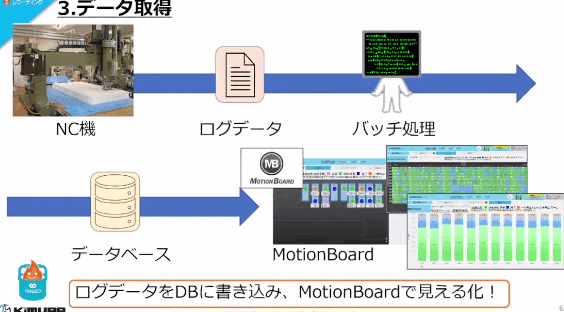
このログデータをバッチ処理を使ってデータベースに保存しそれをMotionBoardを使って見える化する仕組みを構築しました。
見える化したのは向上のマップに合わせた稼働状況、問題点抽出に使用するためのガントチャート、稼働率の3種類です。
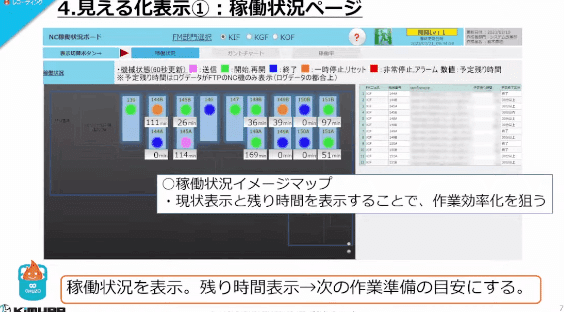
今回発泡スチロールを加工するNC機械の稼働状況を可視化しましたが、今後はNC機稼働日報を手書きから自動入力に切り替えたいとのことです。
LT3:PLCデータ収集システムの開発と設備データの見える化
次は自動車の部品製造で鋳造加工をしているアイシン高丘株式会社の池浦さんによるPLC(プログラマブルコントローラ)データ収集システム開発のお話です。
工場の中で鋳造設備の制御に使われているPLCからLANケーブル経由で100ミリ秒単位で取得するデータをSQLiteに集めてPythonで開発を行いました。
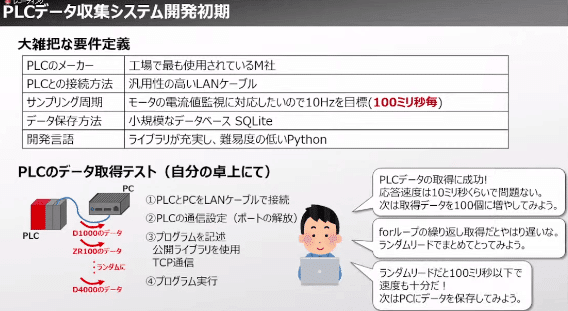
処理を並列処理にし、データを100ミリ秒単位で取得できるようにし、一覧表やグラフなどのUIやデータベースサーバでのデータ共有をするようにしました。これを内製で開発することにしました。
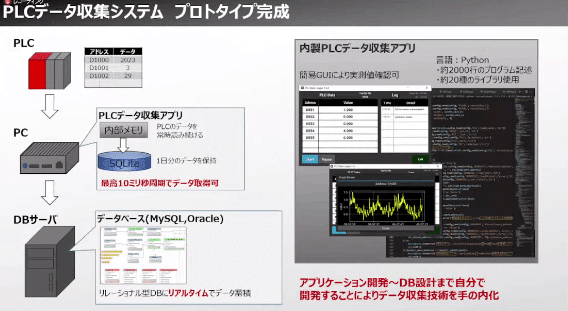
プロトタイプが完成したあとは上司にPLCデータ収集システムのメリットを訴えた結果、上司のアドバイスによりBIツールを使うことになりました。
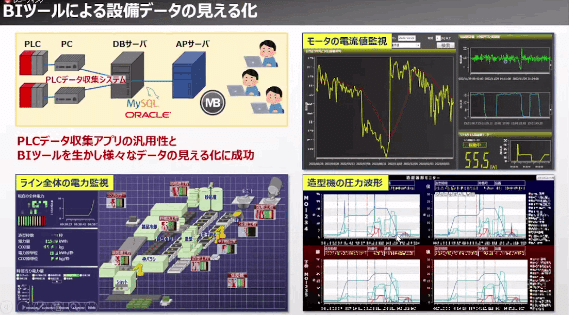
活動の結果PLC収集システムの開発に成功し、BIツールにより設備データの見える化も実現しました。
今後の課題としては、このシステムの保守性を向上させ、大規模データの解析にも取り組みたいそうです。
LT4:Raspberry Pi Pico W触ってみた
4番手は栃木の那須塩原で鋳物を作っている錦正工業株式会社の長嶋さんです。テーマはIoTLTっぽい、新しく出た(まだ技適でてなかった)Raspberry Pi Pico Wを使ってみたお話です。
安くて頑丈で電源がいきなり切れても大丈夫で簡単にネットに接続できるRaspberry Pi Pico Wは期待でいっぱいなのですが、電波法の壁がありまだ日本では使えません。
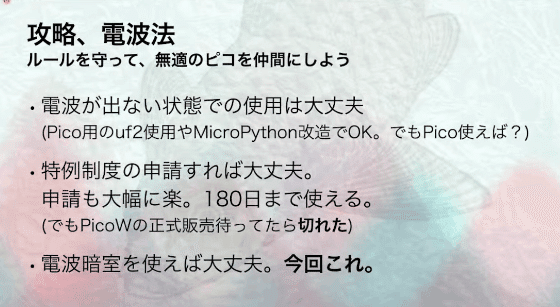
でも法律を守って電波暗室で試せばOKということで今回、アルミ箔を無線アクセスポイントと一緒に巻くことで「平成18年総務省告知第173号の要件を満足する試験設備」をクリアする電波暗室を作成しました。
しかし、狭い今回の電波暗室では内部が発熱で熱くなってしまう課題がありますが、これは内部温度をPicoWで測定するようにしたそうです。
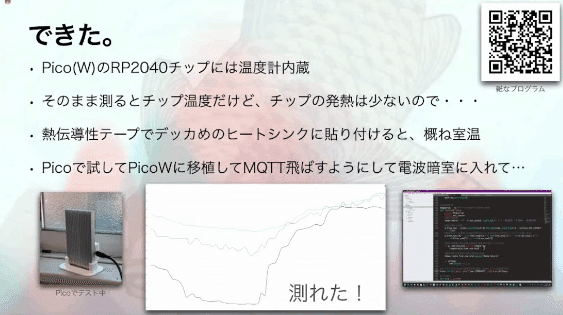
次に試したのは「CTセンサ」。CTアンプを繋いで商用のクランプメーターと比較してみましたが問題ないレベルだったそうです。
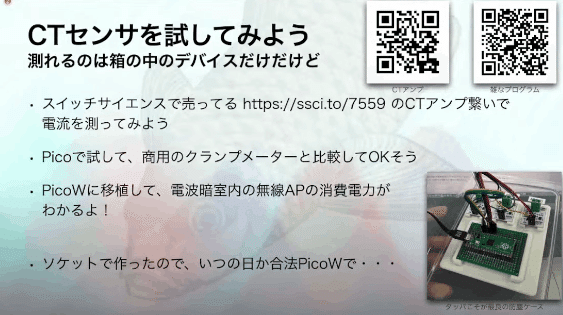
苦労した点としてはPicoWはメモリが少ないこと、SSLがものすごく遅いことですが、別の方法などで工夫して克服したそうです。
ついに技適適合のRaspberryPi Pico Wが届いたので即時実戦投入となるそうです。
余談ですがGPT4もいろいろ試したそうです。
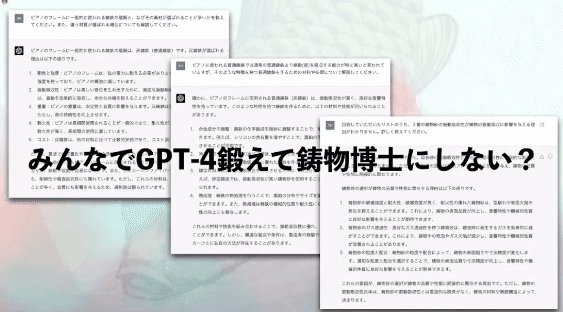
LT5:OCR×KINTONE×m365最強説
後半の最初は茨城県つくば市のIT企業である株式会社LIGHTsの和地さんのLTです。
事業としての鋳造との接点は南部鉄器の技能継承を若い担い手に伝えるためにAIを活用して支える取り組などをしています。
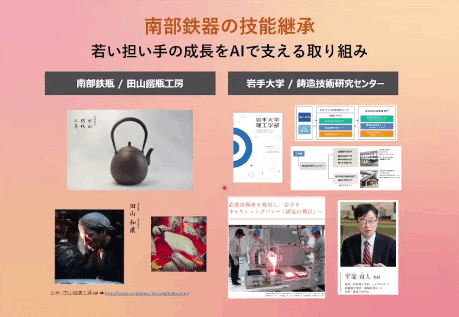
今回のテーマは現場にある紙の書類をデジタル化する話です。デジタル化したくてもスキャナもないし、人も居ないところからのスタートです。それをOCRやKintoneと連携したものづくりコネクトというサービスで実現しました。
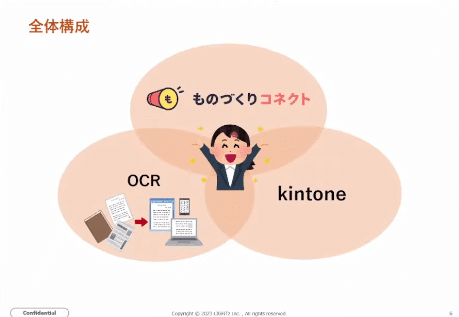
kintoneと連携して保存した書類を手書きOCRで文字化をして、それをものづくりコネクトで編集できるようにしました。これでスマホで撮影したものをすぐにものづくりコネクトでデータ活用できるようにしました。
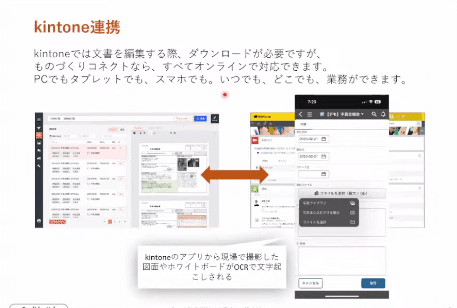
この仕組みを活用した事例としては見積書業務を手書き見積書に追記した見積もり根拠までをものづくりコネクトでデジタル化して検索可能にして作成時の参考にできるようにしたものがあります。
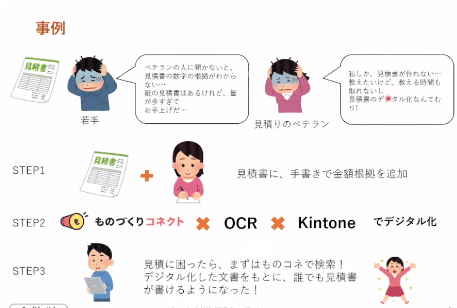
こういった取り組みにより製造業で成功している中小企業の勝ちパターンを実現する取り組みを続けていきたいということです。
LT6:M5スティックでコロナ対策の手間を軽減してみた
6番手は建機や自動車の過酷な状況下で使用される鋳造部品の量産を手掛ける。アサゴエ工業株式会社の総務課で働くこまっちさんのLTです。
今回は社内でIoTの取り組みが増えている中、総務課でもなにか出来ないかと考えて社内8箇所にある「アルコール消毒液設置」に関して取り組みを実施した話です。
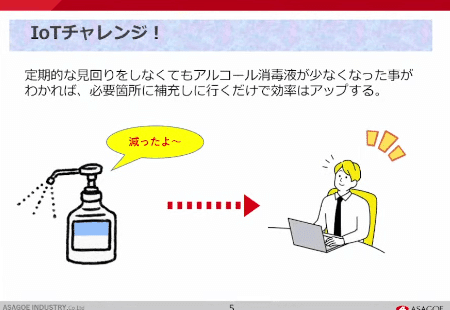
アルコール消毒液の補充を効率化するために残量をM5Stackと重量センサーと組み合わせて残量を知らせる仕組みを作成しました。
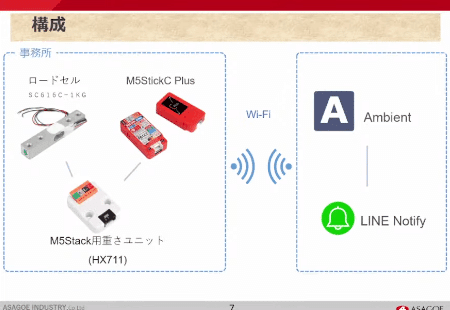
プログラムはArduino IDEのスケッチ例を参考にして作成しました。しきい値を切ったときのLINE通知やM5Stack上での数値確認ができるようになりました。
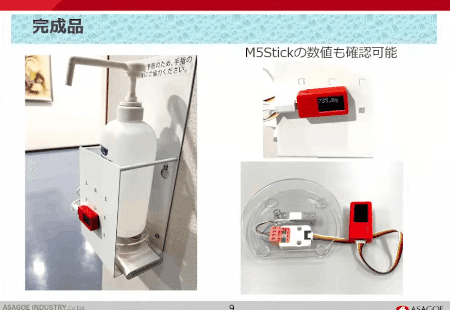
プログラムは参考例があり1からの作成ではありませんでしたが、M5Stackの表示を派手にすると電源問題が発生するなどありました。IoTは製造部門だけではなく販売管理部門でも取り組めることを実感することが出来たとのことです。
LT7:工場ダッシュボード
株式会社小林の宮下さんのPC不調により繰り上げで登場したIoT可視化サービスのアンビエントデータ株式会社の下島さんの登場です。下島さんのテーマはアサゴエ工業さんに導入している「工場ダッシュボード」です。
工場全体の設備稼働状態をひと目で見えるようにしたいと作ったシステムです。正常稼働もトラブル発生も人目で見え、主要な設備についてはWebカメラの映像も同時に見えるようになっています。
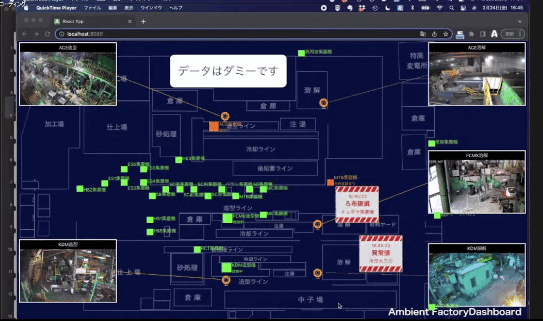
特徴としては実際の工場のレイアウト図上に表示され直感的にわかりやすく、既存設備には独自開発のIoT端末で状態をデータ化、APIを経由して他社IoTシステムの見える化も可能になっています。
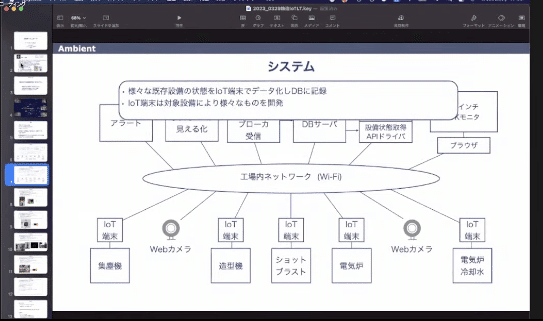
IoT設備は対象の設備の特徴に合わせて様々なものを個別に開発して(カメラで情報を取ったりして)機器の状態データを取得しています。
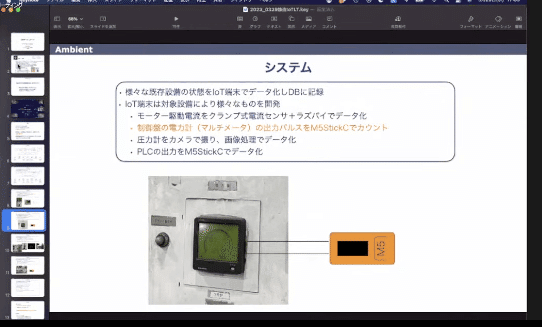
データベースは今回はローカルに置いていて、それをWebアプリで作ったダッシュボードで見える化し、55インチの大きなディスプレイをオフィスに置いて常時監視できるようになっています。
わかったこととして、常に見えている「見える化」は有効であることや、大量のIoT端末を安定稼働させるのにはノウハウが必要なことがわかりました。
LT8:IoT生産管理システムへの挑戦!
7番手は新潟県長岡市にある工作機械、製造機械のメーカー株式会社の小林宮下さんによる2018年に行われた取り組みについての発表です。
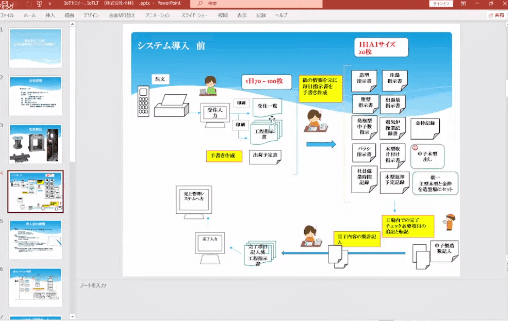
元々は受注はFAXでもらい、それをシステムに入力して受注一覧表や工程指示書などの紙帳票を数百枚出力し、それを工程管理者がチェックして工程を組んで、そこから手書きの指示書を毎日書いていました。それを使って作業をチェックし、回収し・・・のような煩雑なプロセスでした。紙の使用量も多く、作業状況の確認が遅く、さらに売上時に二重に登録が必要で、各工程の進行状況などの集計にも何時間も時間がかかっていました。
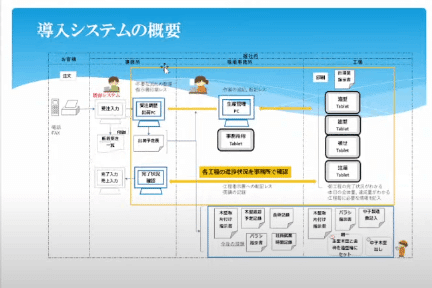
これを受注入力のシステムはそのままに、次の工程に情報が伝わるようにし、システム内で工程指示を組めるようにしました。指示は現場でタブレットにより確認と完了報告を送るようにしタイムロスも発生しなくなりました。
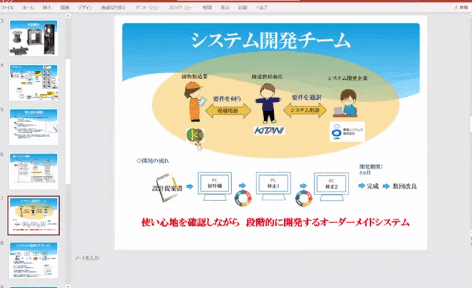
社内にシステム開発のノウハウがなかったので鋳物を扱う商社を商流の間に挟んでシステム開発会社に依頼し社内メンバーとグループで開発をしました。
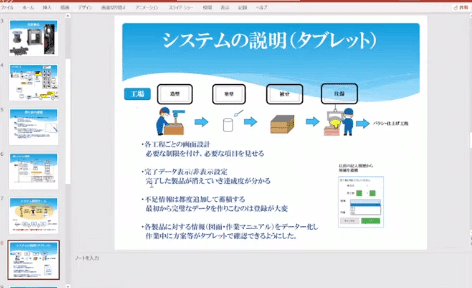
工場内の各工程ごとにタブレットを配置し管理をし、操作性も簡単になるようボタンひとつで処理されるようにしました。
導入の成果としては紙の印刷量が数十万円相当減り、作業時間が短縮され、ヒューマンエラーが減ったので不良率も減りました。活動による宣伝効果もあり受注も増えました。
課題としてはWi-Fiの環境障害に対応するための印刷機能やタブレットの強度の補強がありましたが今後は製品情報のデータ化やラインの一分作業を自動化してシステムと連携ができるようにしたいとのことでした。
クロージング
最後は大川さんの「今回はわかりやすいものが多く、ダッシュボードによる見える化が多かった、次は人材とか活用の話になるのかと思いました」とのコメントによりイベントは締まりました。
感想ですが、たしかに今回は見える化の話が多かったと思います。工場だとフロアマップに合わせて表示するというのも大事だということも実感しました。相変わらず面白かったです。
この記事が気に入ったらサポートをしてみませんか?