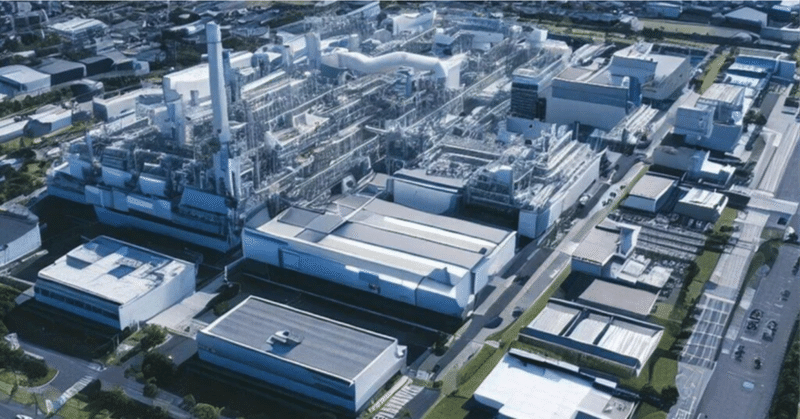
Functions and system image to realize the next generation factory “smart factory”
A smart factory is an advanced factory that utilizes the latest digital technology and automation systems to achieve efficient and flexible production. Compared to traditional factories, they integrate various digital technologies, Internet of Things (IoT) devices, robotics, artificial intelligence (AI), big data, and other technologies, and focus on automation and data utilization. I'm leaving it there.
What kind of functions and equipment will be included in a smart factory? I added the image and content of AI to the expected functional group and summarized it in a concrete form.
production control schedule
It is expected that smart factories will be equipped with production management schedule AI assist functions. This feature will be introduced to improve the efficiency of the entire production line by automating the creation of production plans and adjustment of schedules.
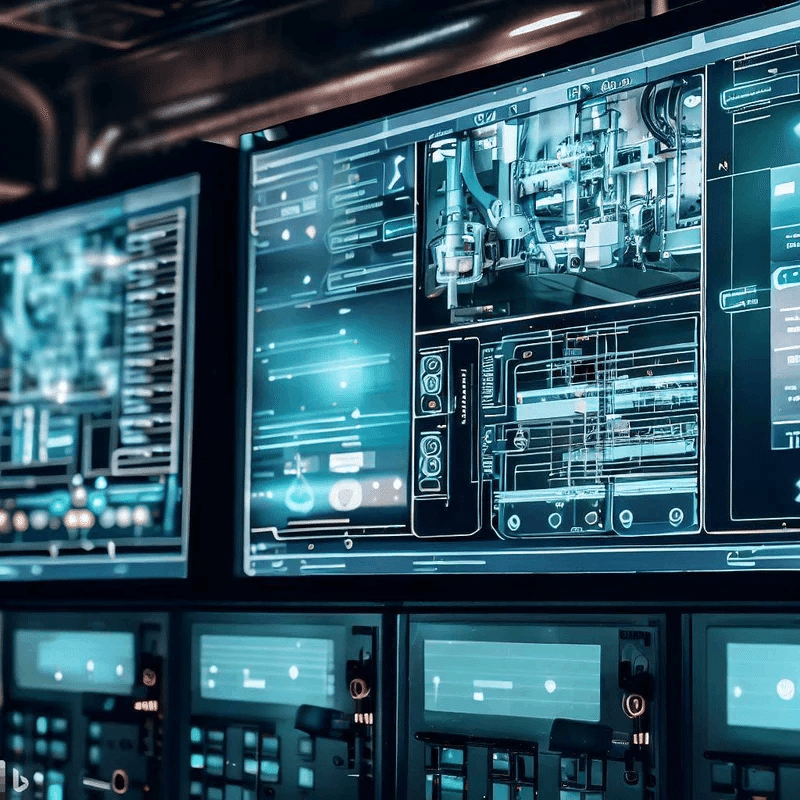
Real-time data collection:
Collect production data in real-time through sensors and monitoring systems on the production line. This includes production quantities, working hours, error rates, equipment utilization, etc. Data is automatically collected through sensors and IoT devices and accumulated in a central database.
Optimize production planning:
Production Management Assist analyzes collected data and provides decision support to optimize production planning. Based on demand forecasts and inventory level monitoring, you can create appropriate production schedules and material procurement plans. This improves production line utilization and production efficiency, and prevents wasted inventory and production delays.
Real-time monitoring and alerts:
Production Control Assist monitors your production line in real-time and provides appropriate alerts and notifications when anomalies or problems occur. When problems such as machine breakdowns, production line stoppages, or quality deterioration are detected, relevant parties are notified and can respond quickly.
Quality control and statistical analysis:
Production Control Assist is also used for quality control. Analyze quality indicators and abnormal patterns from production data and provide information useful for improving product quality. Furthermore, it is also possible to improve production processes and investigate the causes of defective products based on statistical analysis.
Worker support and training:
Production Control Assist also has functions to support workers. This includes displaying work steps and work instructions, measuring work time, and providing guidelines for quality checks. As part of training, the assist system also provides real-time feedback and advice to workers, helping them learn efficient work methods and quality standards.
Machine learning and predictive analytics:
Production Management Assist leverages machine learning and predictive analytics techniques to improve production processes and predict problems. By learning past production data and predicting future production performance, it is possible to optimize resources and prevent problems in advance. Examples include predicting machine failure risk and optimizing maintenance schedules.
Real-time visualization and reporting:
Production Management Assist visualizes the status of production processes and production lines in real-time and provides them as dashboards and reports. Important performance indicators such as production quantities, production efficiency, and quality indicators are visually displayed, allowing managers and stakeholders to understand production status and immediately determine necessary countermeasures and improvements.
The above are the main functions provided by Production Management Assist and their supplements. These features streamline production processes, improve quality, and provide real-time monitoring and response. In addition, by utilizing AI and data analysis technologies, more advanced prediction and optimization will become possible, improving the competitiveness and efficiency of production.
Order specification confirmation Raw material calculation
It is expected that smart factories will be equipped with AI-based order requirement confirmation and raw material calculation functions. This function was introduced to streamline requirements confirmation and raw material calculation work required when ordering parts and materials, which is one of the challenges in the manufacturing industry.
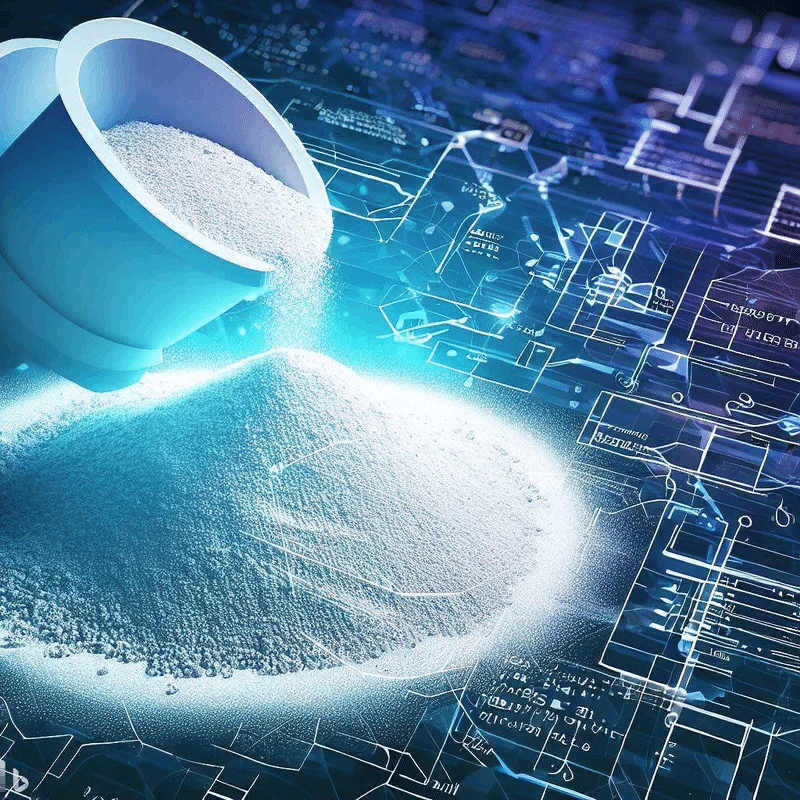
Specifically, by inputting information on the parts and materials to be ordered using AI, it is possible to automatically perform necessary requirement checks and raw material calculations. For example, by inputting information such as the quantity, size, weight, and characteristics of parts and materials to be ordered, it is possible to automatically calculate the amount of raw materials needed and the cost required for ordering.
This function allows you to reduce the time and effort required for conventional requirements confirmation and raw material calculation work. In addition, AI can perform accurate calculations to quickly and accurately provide the information needed when ordering parts and materials. This not only ensures product quality and on-time delivery, but also leads to more efficient production processes.
exchange survey
In future smart factories, it is also possible that AI-powered currency exchange research functions will be related to parts and materials used within the factory. This function is introduced to deal with exchange rate fluctuations when importing raw materials and parts from overseas.
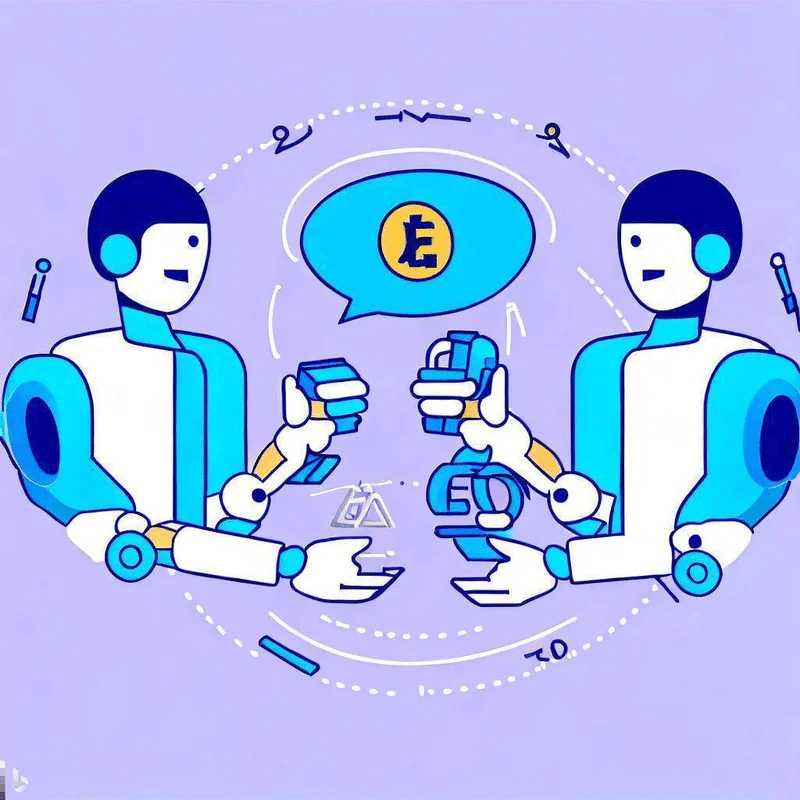
Specifically, AI collects information such as exchange rates and market conditions from external sources and uses that information to predict price fluctuations for materials and parts. Additionally, based on the information investigated by AI, it is possible to select suppliers for raw materials and parts at the most appropriate timing.
This feature allows manufacturers to reduce risks such as increased raw material costs and overstock due to exchange rate fluctuations. AI also provides accurate market analysis, allowing manufacturers to optimize the sourcing of parts and materials. This is expected to lead to greater efficiency in the entire manufacturing process, including reductions in raw material costs and appropriate inventory management on production lines.
Quotation request assist
It is expected that smart factories will be equipped with an AI quotation request assist function for suppliers. This function is being introduced to eliminate the complexity and time wastage of estimation work, which is one of the issues in the manufacturing industry.
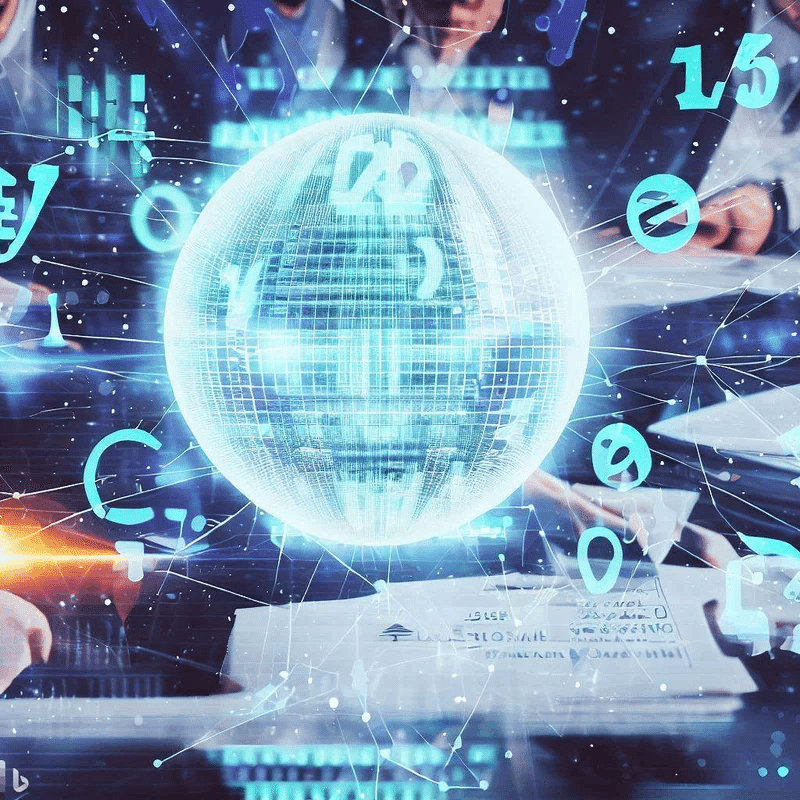
Specifically, by inputting information about the parts and materials to be ordered into AI, AI can automatically send a request for quotation. AI also helps in selecting suppliers. Based on past transaction results and reviews, it is possible to select the most suitable supplier by comprehensively evaluating conditions such as quality and delivery time.
This feature reduces the time and effort required for traditional estimation work. In addition, by using AI to select the most suitable supplier, risks such as the quality of parts and materials and delivery dates can be reduced. This not only ensures product quality and on-time delivery, but also leads to more efficient production processes.
Supplier AI selection
It is expected that AI-based supplier selection functions will be used in future smart factories. This function is introduced to select the most suitable supplier by considering various conditions related to the products and services to be ordered.
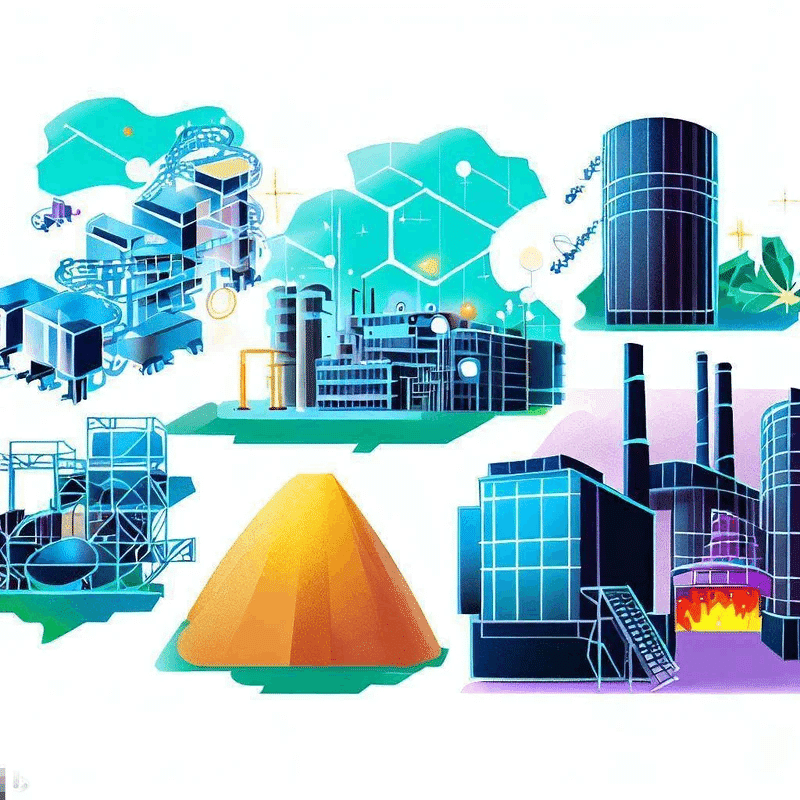
Specifically, by inputting the terms and conditions of the product or service to be ordered by AI, it is possible to automatically select the supplier. Conditions include quotation details, delivery date, quality, price, past transaction results, etc. Based on this information, AI selects the most suitable supplier.
This feature allows manufacturers to streamline the process of selecting suppliers. In addition, by selecting appropriate suppliers using AI, we can ensure product quality and delivery times. Furthermore, AI can be used to appropriately select suppliers, which is expected to lead to reductions in ordering costs and other improvements in the efficiency of the entire manufacturing process.
Smart truck inter-base transportation
It is expected that future smart factories will utilize self-driving smart trucks for transportation between locations. This feature aims to automate factory logistics processes using trucks equipped with self-driving technology.
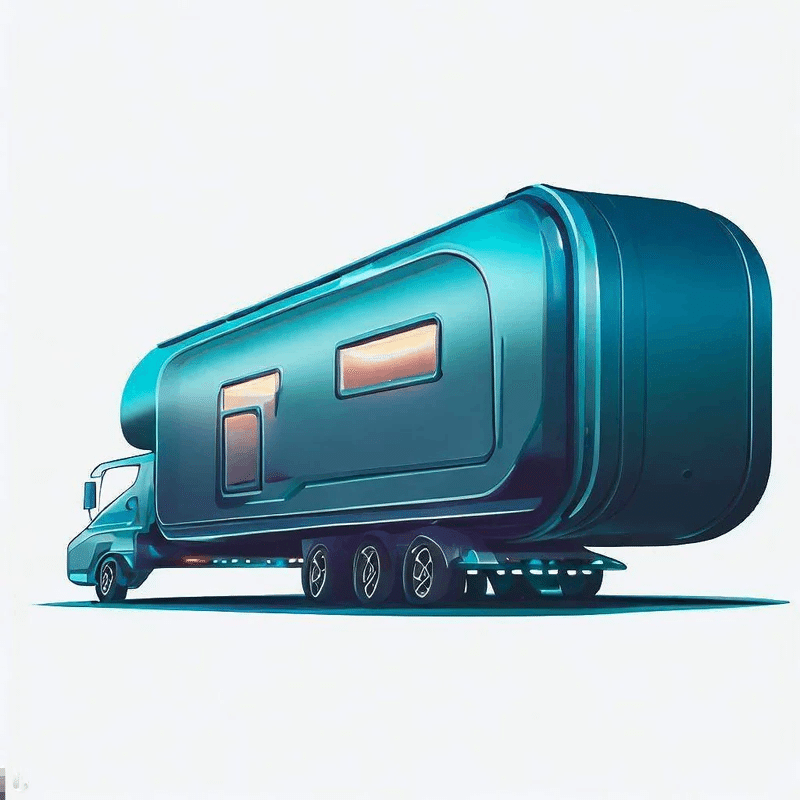
Specifically, smart trucks use self-driving technology to autonomously navigate roads within and between factories. In addition, AI monitors the truck's driving status and automatically controls it as necessary, ensuring a high level of safety.
This feature allows manufacturers to reduce the time and cost of inter-site transportation. Additionally, automated truck driving is expected to reduce the burden on drivers and reduce the risk of driving errors and traffic accidents. In addition, AI monitors truck driving conditions, allowing for more efficient routes and appropriate speed management, reducing fuel consumption and truck wear and tear.
This feature allows manufacturers to automate the entire logistics process, increasing productivity and efficiency.
Automatic receiving check
It is expected that future smart factories will use an automatic receiving check function for incoming goods. This feature is aimed at increasing the automation of logistics and increasing the efficiency of the entire manufacturing process.
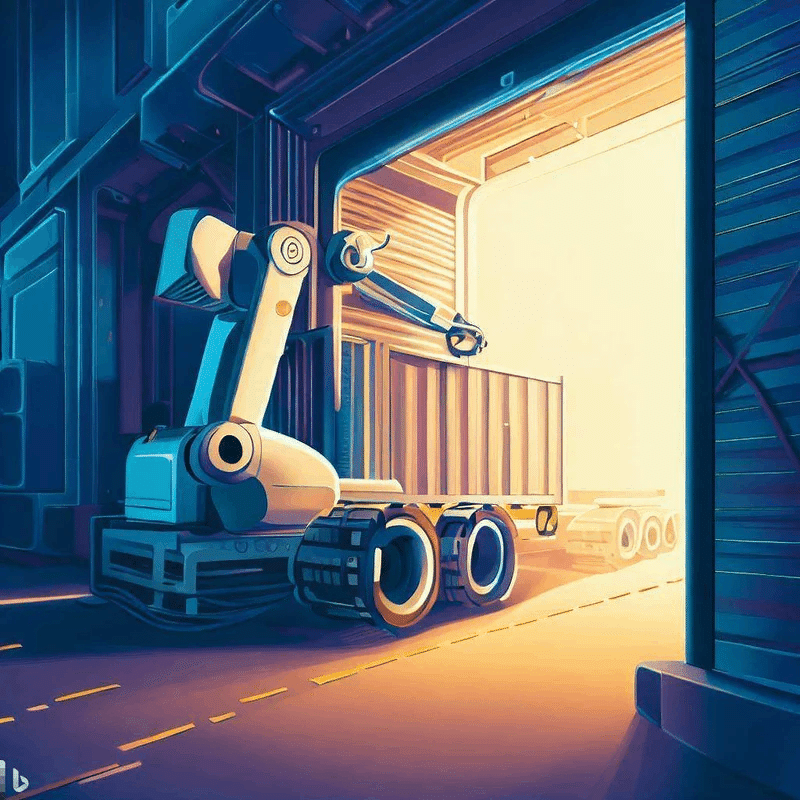
Specifically, cameras and sensors installed in smart factories can automatically check the packaging, quantity, quality, etc. of incoming items. This allows the traditional manual inspection work to be omitted, reducing work time, reducing errors, and eliminating human error.
In addition, by analyzing images and sensor information using AI, it is possible to accurately understand the condition, quality, weight, size, etc. of the cargo. This makes it possible to automatically send alerts in the event of an abnormality, such as if the packaging of the incoming items is different or if defective items are mixed in.
This feature allows manufacturers to perform quality control more accurately and quickly. In addition, the entire logistics process of a smart factory can be automated, leading to shorter work times, lower costs, and the elimination of human errors. Additionally, an automated warehouse management system combined with an automatic receiving check function can also automate inventory management.
Movement within the factory
Future smart factories are expected to use AI-equipped robots to move around the factory. Since this system can automatically transport various equipment, materials, and components, it is expected to improve work efficiency, reduce human error, and improve safety.
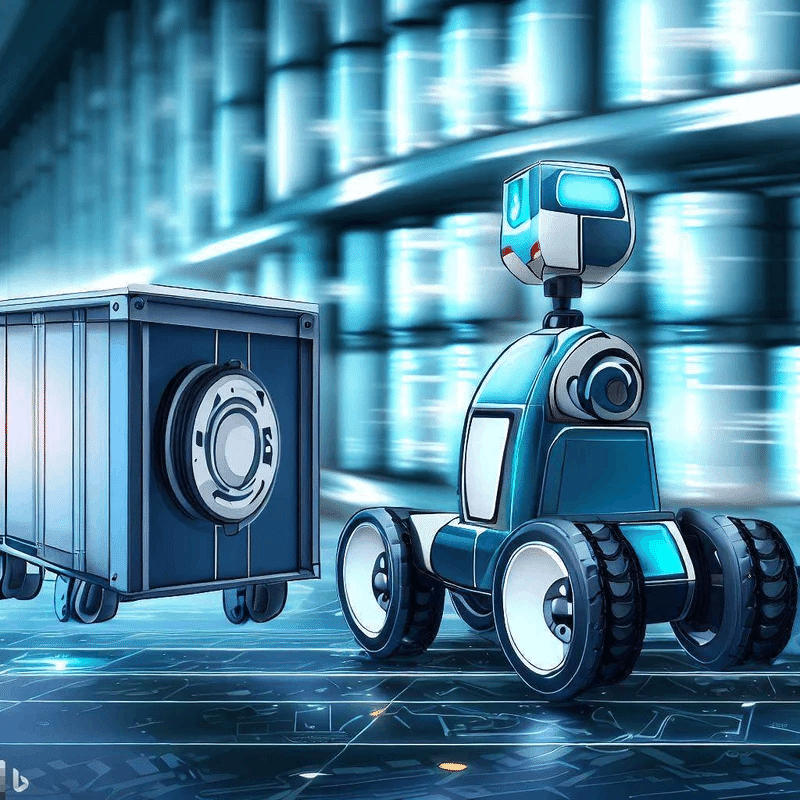
Specifically, it can be used in various locations within the factory, and can be used for a variety of purposes, such as transporting imported items, transporting equipment, and transporting products. The robot can operate autonomously using AI, read map information and obstacle information within the factory, select the optimal route, and move automatically. It is also possible for robots to communicate with each other and work collaboratively.
In-factory transportation robots are equipped with attached devices such as arms and hooks for carrying loads, and can carry loads of various shapes and weights. Furthermore, through image recognition using AI and analysis of sensor information, it is possible to accurately determine the condition, quality, weight, size, etc. of the baggage. This prevents accidents such as falling cargo or collisions.
Mobile robots in factories can automate traditionally manual tasks, reducing work time and eliminating human error. In addition, robot automation can replace heavy and dangerous work that was traditionally performed by humans, leading to improvements in the working environment. In-factory mobile robots will become one of the important functions in smart factories to improve work efficiency, improve productivity, and reduce costs.
Raw material check measurement
Smart factories have high demands on the quality of raw materials. In the future, it is expected that AI-powered raw material check metrology will be introduced to automatically check and measure the quality of raw materials. This function prevents low-quality raw materials from entering the production line, leading to improved production quality.In a smart factory, the materials used in the products made are important, and must be of high quality. In the future, material checking machines equipped with artificial intelligence will be used to automatically measure the quality of materials.
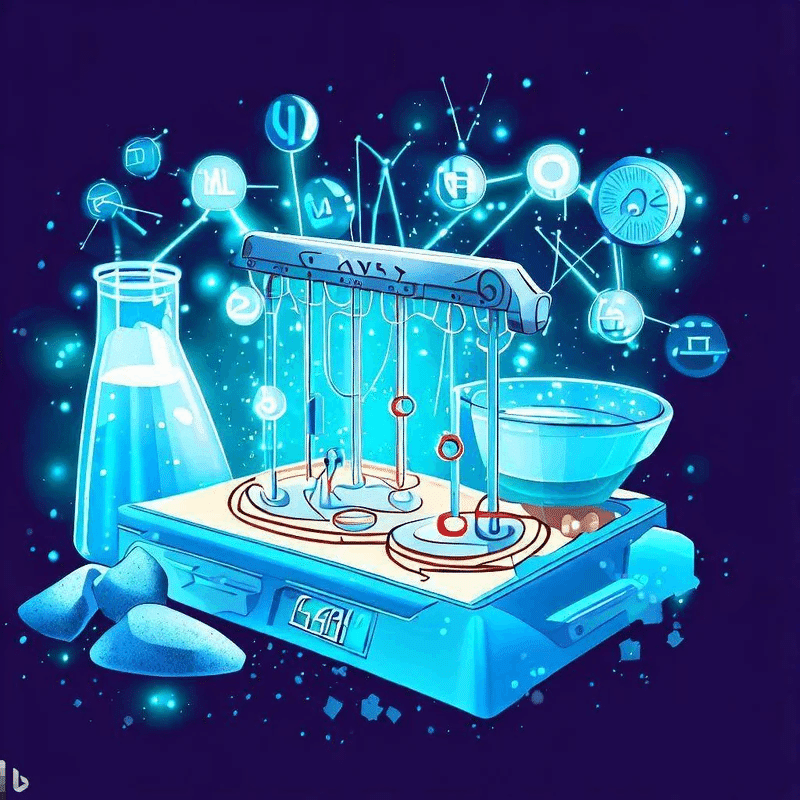
This helps improve product quality by preventing products from being made with low-quality materials. We can expect that artificial intelligence will analyze the data and automatically determine the method of manufacturing that best suits the material, leading to improved efficiency in manufacturing methods. In addition, data analysis using AI makes it possible to automatically set optimal production conditions according to the characteristics of raw materials, which is expected to improve the efficiency of the production process.
Operation schedule management
In next-generation smart factories, it is expected that operation schedule management for the entire production line will become more sophisticated. Compared to current factories, next-generation smart factories will be able to monitor the status of equipment and systems in the factory in real time and automate schedule management for the entire production line.
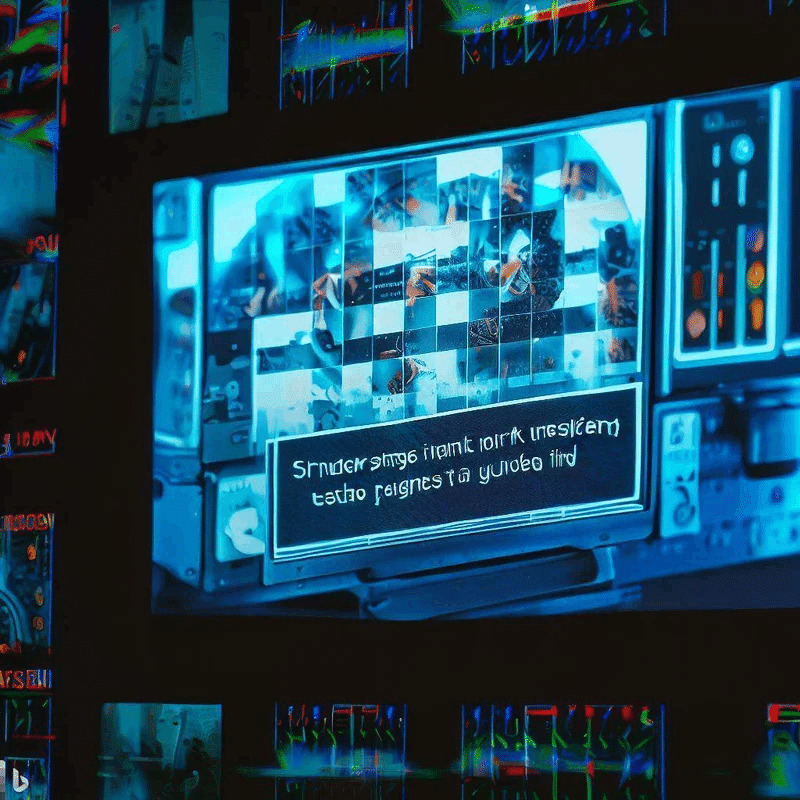
These capabilities include AI capabilities that automatically optimize production schedules, taking into account information such as production line conditions, production plans, and scheduled maintenance. Additionally, by detecting abnormalities on the production line, it is possible to automatically adjust production schedules and maintain optimal production efficiency.
In addition, in smart factories, real-time data analysis allows you to monitor the entire production process and provide information for increasing efficiency and making improvements. These functions are expected to improve operation schedule management for the entire production line and improve production efficiency and quality.
Utility bill real-time monitoring
Next-generation smart factories will introduce automation technologies such as AI and robots, and will require energy-saving and ecological factory operations. Therefore, it is expected that real-time monitoring of utility bills will be included to reduce utility costs.
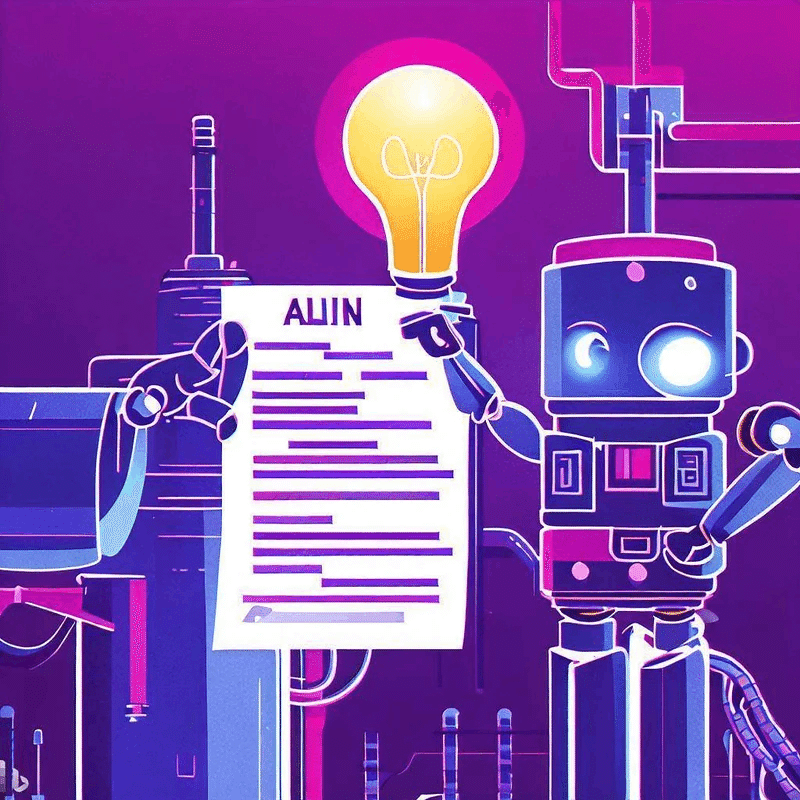
Specifically, by collecting data using sensors and analyzing using AI, we will identify the usage status of utility costs and areas where reductions can be made, improve operations, introduce automation technology, etc., and aim to optimize utility costs. I can. It is also possible to reduce utility costs by adopting equipment and systems that specialize in energy conservation. Real-time monitoring of utility costs is expected to contribute to cost reduction and environmental conservation.
Real-time inventory management
Smart factories are expected to improve productivity and reduce costs by automating inventory management. Therefore, real-time inventory management functions that utilize AI and robots are expected to become widespread in the future.
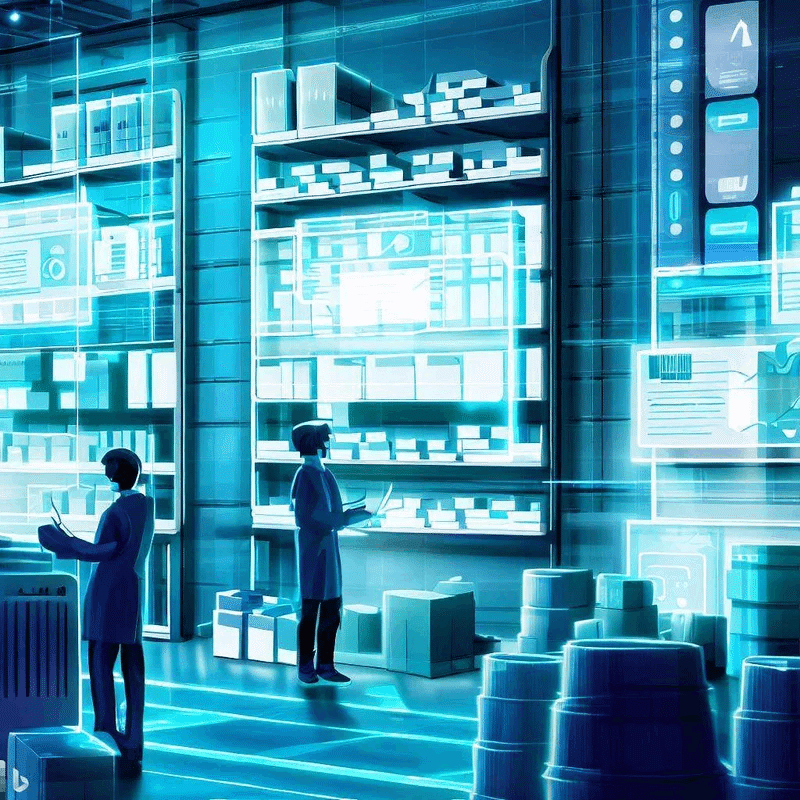
Specifically, sensors installed on production lines and warehouses monitor the amount and status of inventory in real time, and by collecting and analyzing that data, it is possible to accurately understand the status of inventory. In addition, by using AI to predict inventory demand and calculate the optimal order amount, it is possible to prevent overstocks and shortages and optimize production plans.
This real-time inventory management function is expected to reduce production line stoppages and worker rework, leading to improved production efficiency and cost reductions.
ERP-linked hourly settlement
In a smart factory, various data such as production, inventory, and ordering are generated, and it is important to manage them efficiently. For this reason, a company integrated system called ERP (Enterprise Resource Planning) is generally introduced. ERP can centrally manage data generated in all departments of a company, making operations such as production management and financial management more efficient.
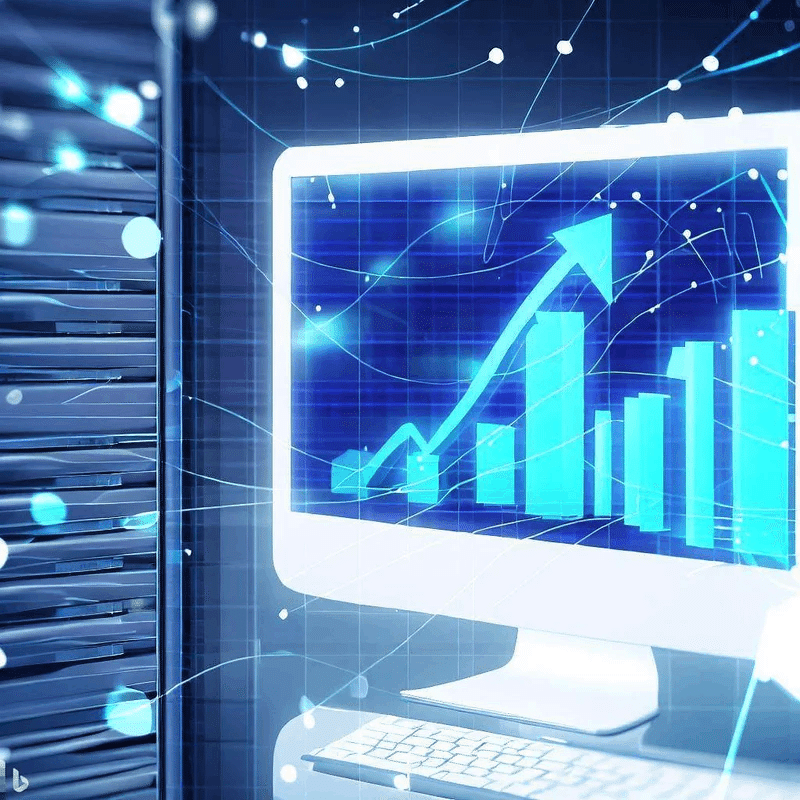
Furthermore, smart factories are expected to introduce hourly settlement functions linked to ERP. The hourly settlement function is a function that allows you to analyze data accumulated in ERP in real time and understand the status of business performance. This enables faster and more accurate management decisions, leading to improved competitiveness for companies. In addition, the timely settlement function makes it possible to understand a company's financial situation and manage future risks.
AI weather information linked analysis
In smart factories, possibilities include optimizing operating schedules using weather information and reviewing raw material purchasing prices.
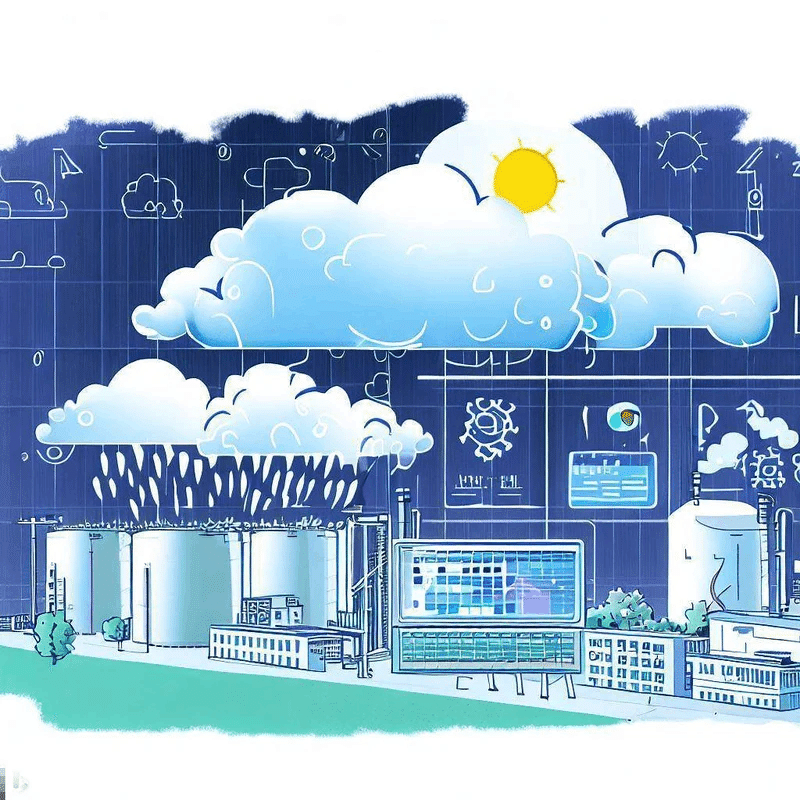
The AI weather information linked analysis function uses data from local weather stations and satellites, as well as APIs provided by weather information distributors, to collect weather information. By using AI to analyze and predict data obtained from these information sources, it can be used to adjust factory production plans and logistics schedules. In addition, by combining data from IoT sensors and cameras, it is possible to obtain more accurate weather information.
Predictive monitoring of delivery dates for materials and components, sea routes, air routes, and land routes
A function to check the delivery schedule status that is expected to be used in smart factories is a delivery date status confirmation management function based on the supplier, delivery company, traffic information, etc.
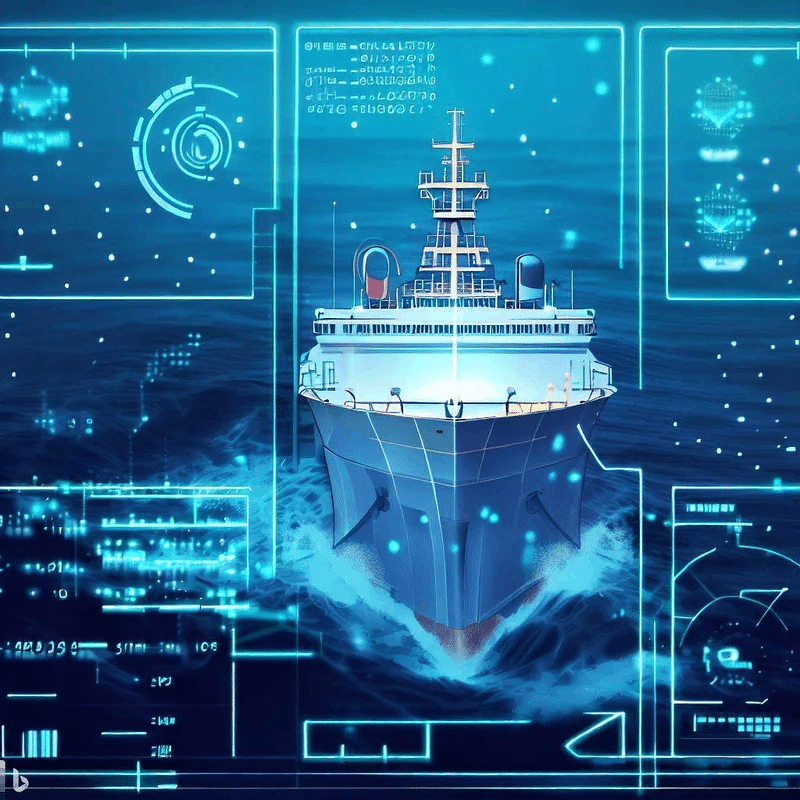
This function collects various information such as how long it will take to deliver ordered parts and materials, how the delivery is progressing, whether it may be affected by traffic information or weather, etc. You can understand the situation in real time.
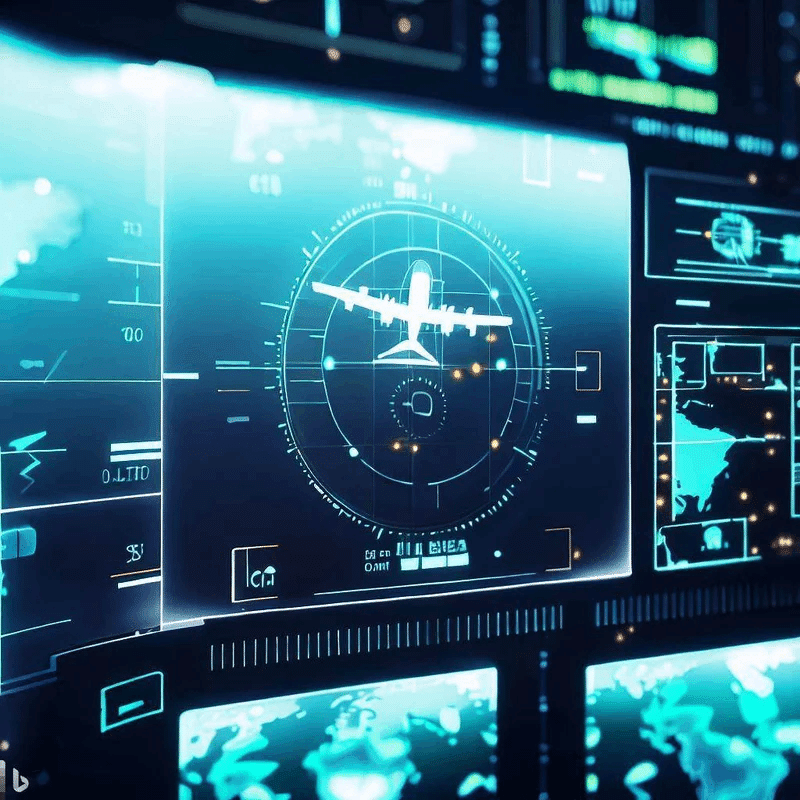
This function also allows you to predict the risk of delays and stockouts in advance and take countermeasures. For example, for parts that are likely to be delayed in delivery, you can take measures such as securing other substitutes.
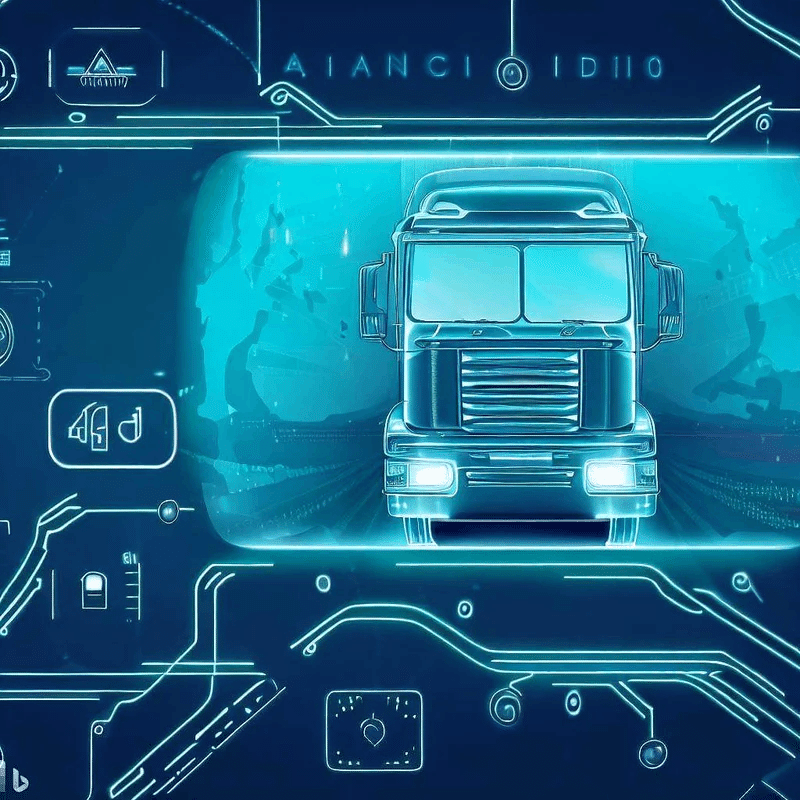
In this way, the delivery status confirmation management function can prevent problems such as delivery delays and stockouts in advance, leading to improved production planning accuracy and production efficiency.
Terminal store sales trends
The following functions are expected to be used in next-generation smart factories, including sales trend functions linked to sales information at stores where products are sold.
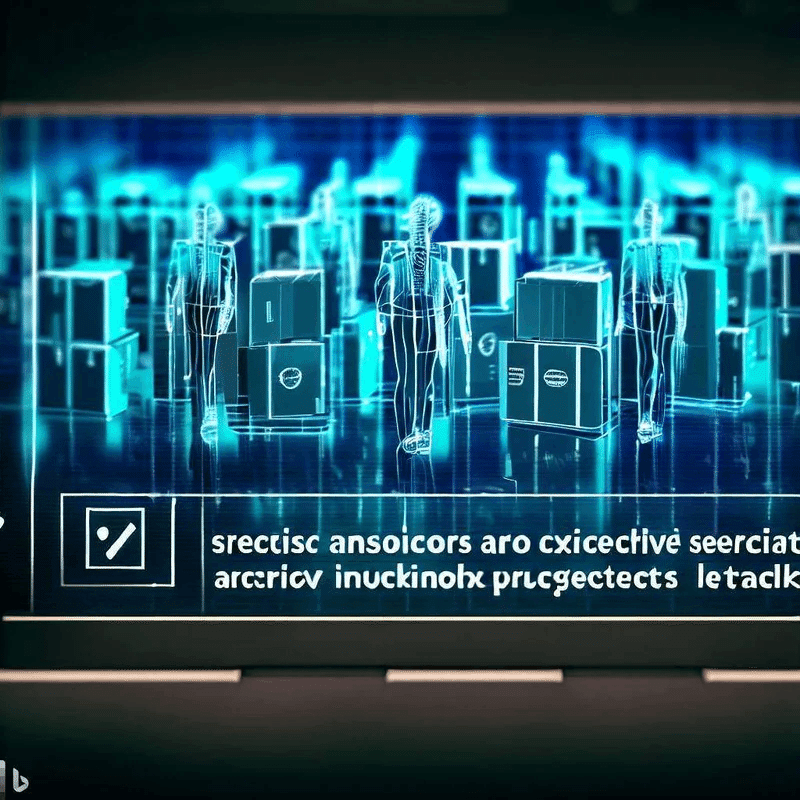
First, it will be equipped with a system that captures real-time sales data from retail stores. This data is categorized by product or product type and visualized according to conditions such as time of day and region.
Next, sales trends are analyzed using AI. This analysis comprehensively considers past sales data, seasonality, weather, and other information to predict future sales trends.
Finally, manufacturing planning and inventory management are optimized based on the predicted sales trends. For example, if demand for a popular product increases, you can respond by increasing the production volume of that product. This kind of optimization reduces risks such as overstocking and stockouts, and enables efficient production and sales.
News information collection Delivery destination impact Foreign exchange raw material costs AI analysis
The AI function that collects news and information that may affect factory operations and analyzes how it affects them is considered to be one of the important functions in smart factories.
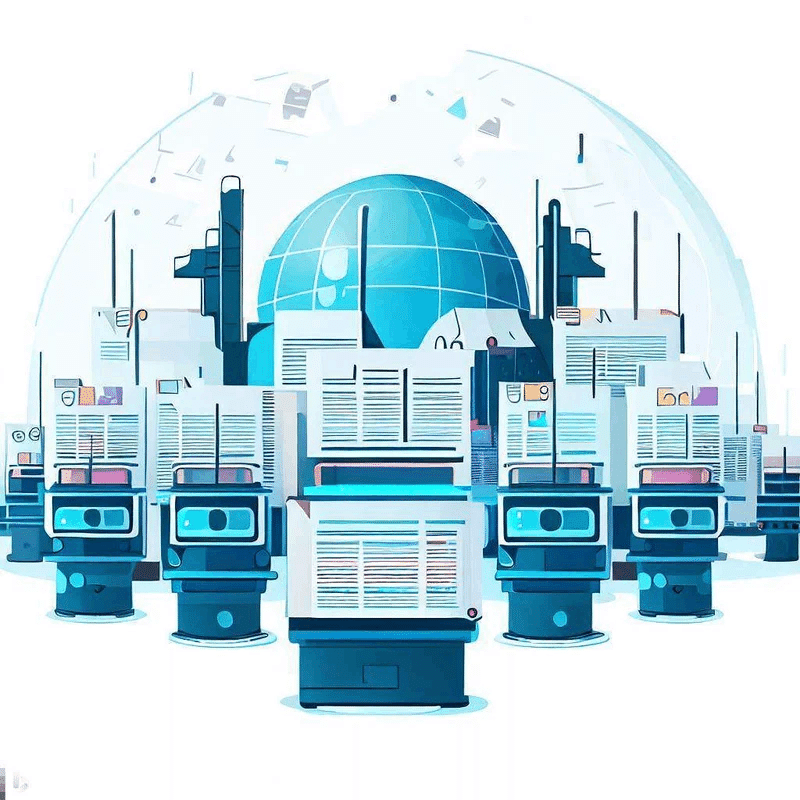
For example, fluctuations in the price of raw materials, natural disasters, changes in the political situation, etc. can affect factory operations. By collecting such information and analyzing it using AI, factory operators can respond faster and more accurately.
Analyzing this information is also useful for predicting product demand and analyzing purchasing trends. This allows us to respond quickly, such as by expanding our production lines, when demand increases.
Waste reuse check
The waste reuse check function is a function that monitors the type and amount of waste generated within a factory in real time, and if there is waste that can be reused, it can be reused. is.
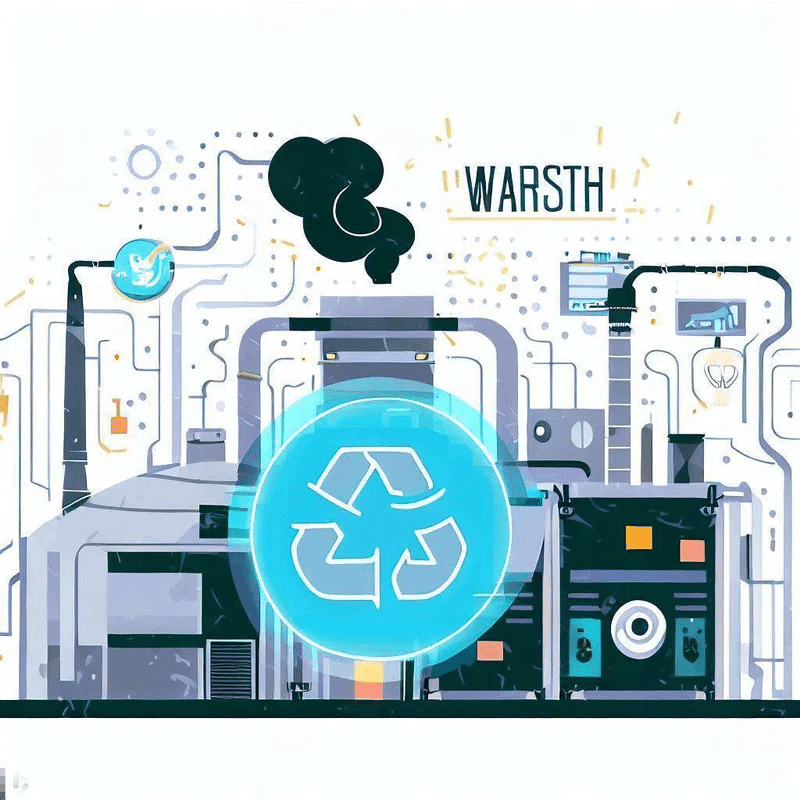
For example, waste generated during manufacturing processes may include parts and materials that can be reused. The waste reuse check function can improve recycling rates and reduce environmental impact by identifying these reusable wastes and managing them appropriately.
Real-time power mix control
Energy conservation is an important issue in smart factories, and power consumption can be optimized by controlling the power mix in real time.
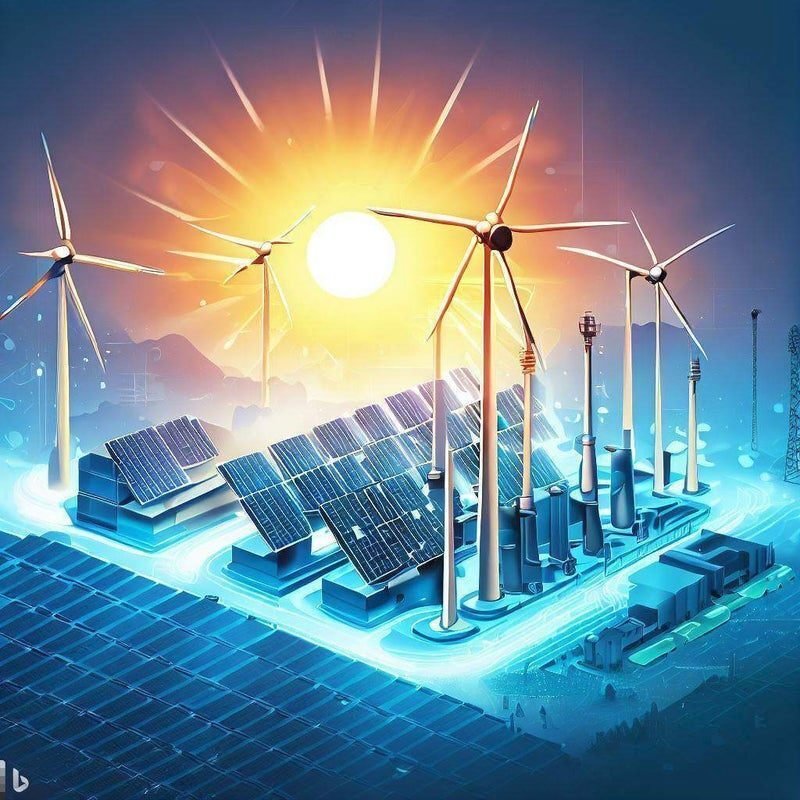
This feature minimizes power consumption by monitoring power demand and supply and automatically optimizing the power supply from power plants and utilities and the use of renewable energy. It is also possible to automatically reduce the device's power consumption if the power consumption exceeds expectations. This makes it possible to reduce costs by saving energy.
air conditioning control
Air conditioning control functions play a very important role in smart factories. By efficiently managing heat and cold sources, this function maintains a comfortable temperature environment while reducing energy consumption.
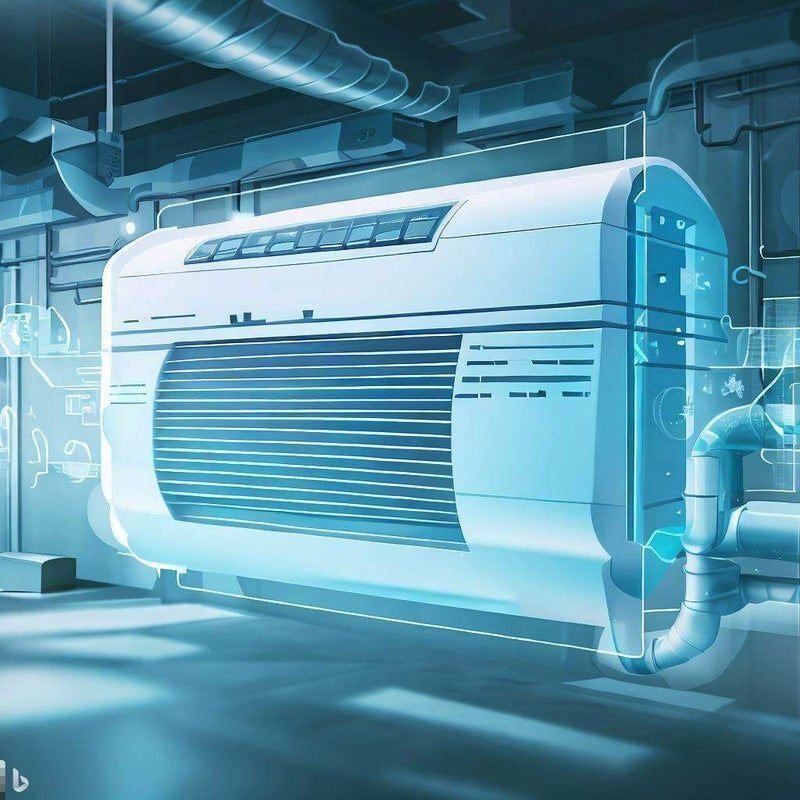
Specifically, smart factories use sensors and actuators to control heat and cold sources to automatically adjust indoor temperature, humidity, airflow, etc. We also expect AI functionality to analyze these sensor data and provide optimal control to improve the efficiency of air conditioning systems.
Furthermore, smart factories can also capture weather data such as outside temperature and humidity of buildings and use this information to optimize air conditioning systems.
As mentioned above, the air conditioning control function in smart factories is one of the important functions that not only provides a comfortable working environment, but also contributes to energy saving and reducing environmental impact.
Abnormal odor detection Danger prediction
The odor detection and danger prediction function that is expected to be installed in smart factories is a function that detects the occurrence of odor in the factory and predicts danger before it occurs.
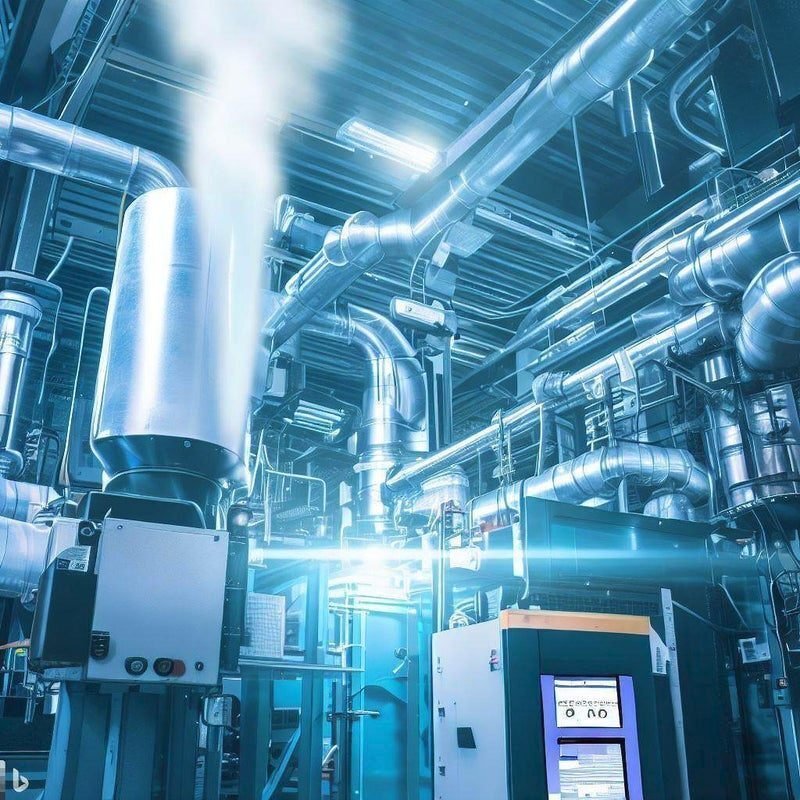
This feature helps reduce the risk of occupational accidents and health hazards. Sensors and monitoring systems are used to detect abnormal odors, and if abnormal values are detected, countermeasures such as alarms and automatic shutdowns may be taken. In addition, by identifying the cause of the odor, it is possible to consider improvement measures, which leads to quality improvement.
Temperature monitoring Hazard prevention
It is expected that smart factories will be equipped with temperature monitoring and hazard prevention functions. This feature allows you to monitor the temperature of equipment and products on the production line in real time, and quickly take action if an abnormality is detected.
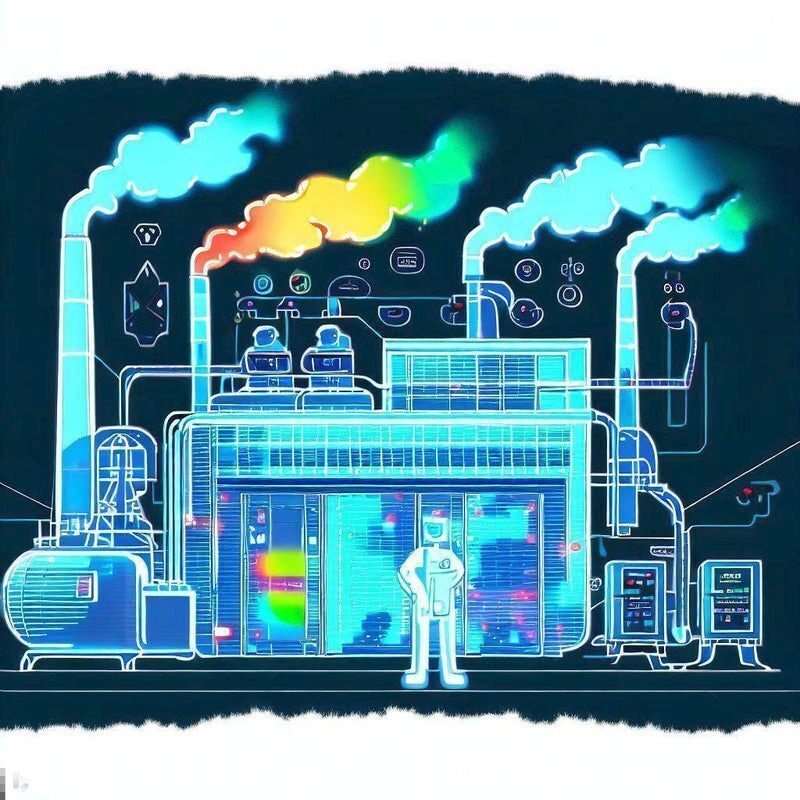
Specifically, temperature is measured using a temperature sensor and the data is monitored in real time. If the abnormal temperature detected by the sensor exceeds the set value, an alarm will be issued and the operator will be notified. In this way, you will be notified of temperature abnormalities before they occur, allowing you to respond more quickly.
Temperature monitoring and hazard prevention functions play an important role in the quality assurance of equipment and products. For example, on an electronic device manufacturing line, high temperatures can cause equipment failure, so appropriate temperature control is required. Additionally, on food production lines, improper temperature control can lead to poor product quality. In this way, temperature monitoring and hazard prevention functions have become one of the essential functions for maintaining product quality.
Emergency response
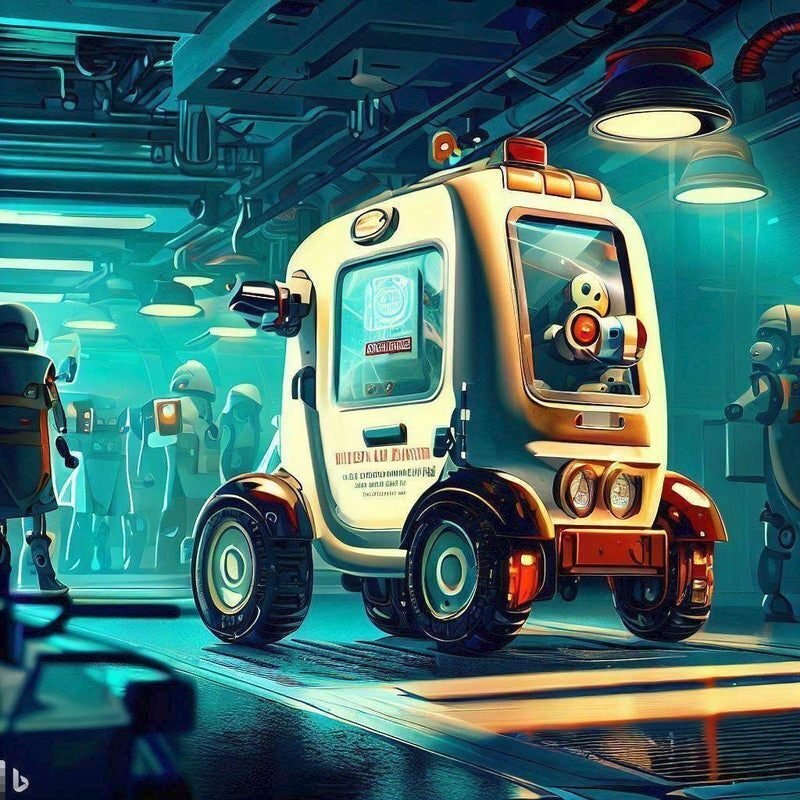
The emergency response AI functions that will be installed in next-generation factories include the following.
Automatic emergency contact notification function This function automatically notifies contact information for accident response personnel, emergency services, etc. when an abnormality is detected in the factory.
Automatic evacuation guidance function This is a guidance system that allows personnel in the factory to safely evacuate in the event of an emergency such as a fire or earthquake.
Employee safety confirmation function This function is used to confirm the safety of employees in the factory in the event of an emergency.
Vehicle guidance function This function provides appropriate guidance for vehicles within the factory in the event of an emergency.
Automatic remote control function This function allows managers who are not on site to remotely control equipment in the factory and check the status in the event of an emergency.
By implementing these functions, it will be possible to respond safely and quickly even in emergencies.
Inter-factory cooperation network
A smart factory requires mutual cooperation not only with the company's own factories but also with other companies' factories and distribution centers involved in the supply chain. Therefore, mutual cooperation network functions between smart factories are required.
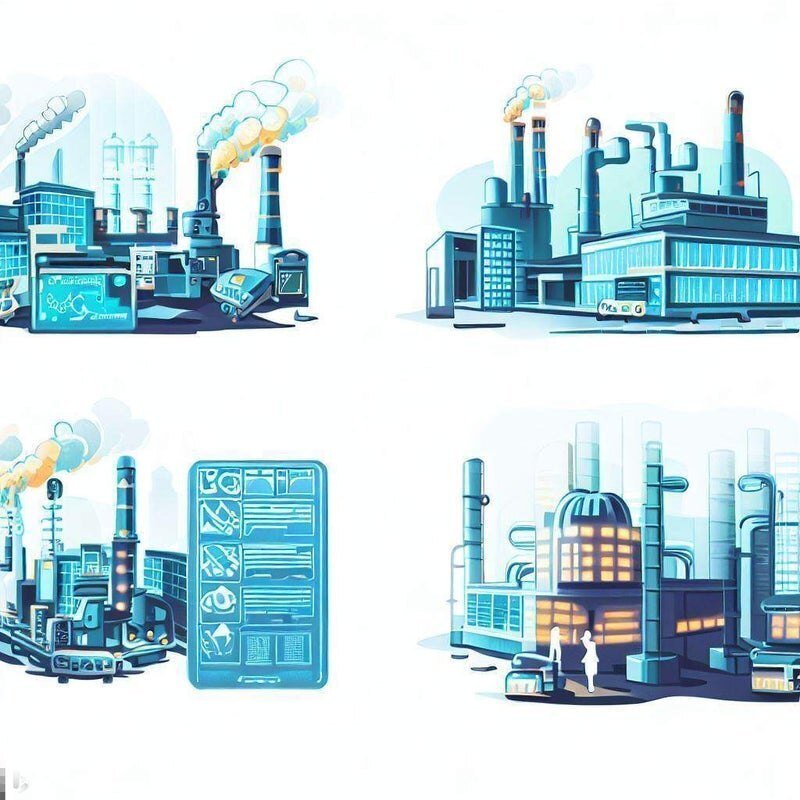
The following functions can be considered for the inter-factory cooperation network.
Data sharing function between smart factories using IoT technology
A function to understand the production status of other companies in real time and reflect it in your own production plans and inventory management.
A function to understand the logistics situation of other companies in real time and reflect it in your own logistics plan.
Mutual sharing of quality information and recall information
Providing a collaborative platform between smart factories
Integrated management of manufacturers and collaborating companies using cloud-based services
Coordination of automated transportation management systems using electronic data interchange (EDI)
By realizing these functions, mutual cooperation between smart factories will be strengthened, and it is expected that the efficiency and productivity of the entire supply chain will be improved.
Inter-factory raw material adjustment
The inter-factory raw material adjustment function is for when multiple factories share raw materials, each factory automatically determines the optimal raw material mix according to changes in raw material quality, quantity, price, etc. With the function of.
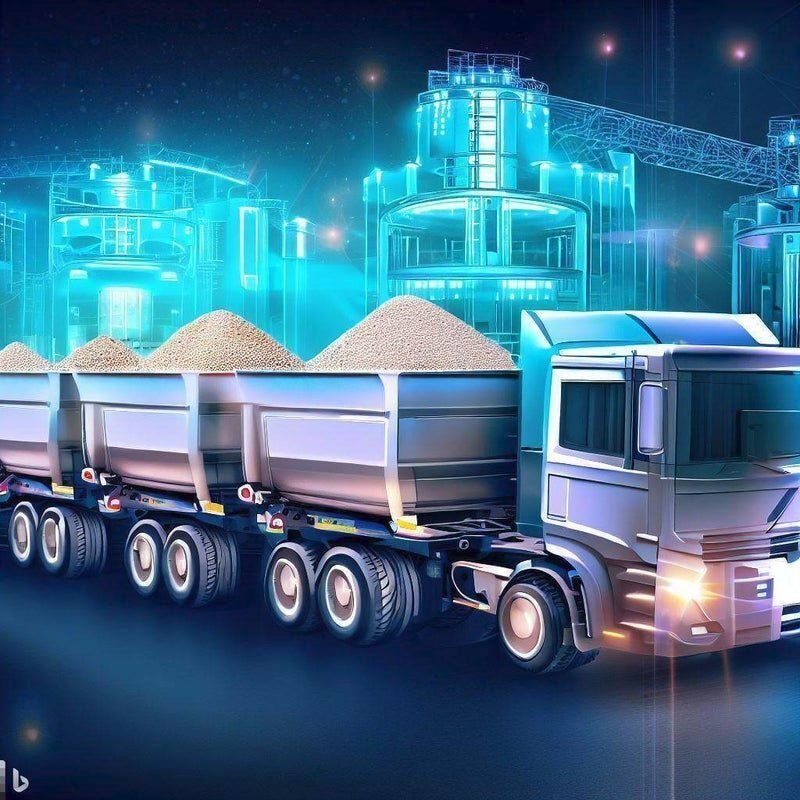
The inter-factory raw material adjustment function is thought to include the following elements:
Sharing of raw material data: By creating a database of information on raw materials used at each factory and sharing it, we can share raw material information between factories.
Raw material quality control: We regularly evaluate the quality of raw materials and, depending on the quality, change the factory that uses the raw materials in order to maintain production quality.
Respond to fluctuations in raw material prices: In order to respond to fluctuations in raw material prices, it is equipped with an algorithm that automatically determines the optimal raw material mix.
Determining the optimal blend using AI: AI automatically determines the optimal blend of raw materials based on raw material information sharing, quality control, and response to price fluctuations.
In this way, the inter-factory raw material AI adjustment function is expected to improve production efficiency and quality by automatically sharing raw materials between factories, controlling quality, and responding to price fluctuations.
Inter-factory production adjustment
The inter-factory production adjustment function includes functions for adjusting production plans between different factories. With this feature, if one factory has excess production, the other factory can increase production. This allows us to respond quickly to market needs and maximize production efficiency.
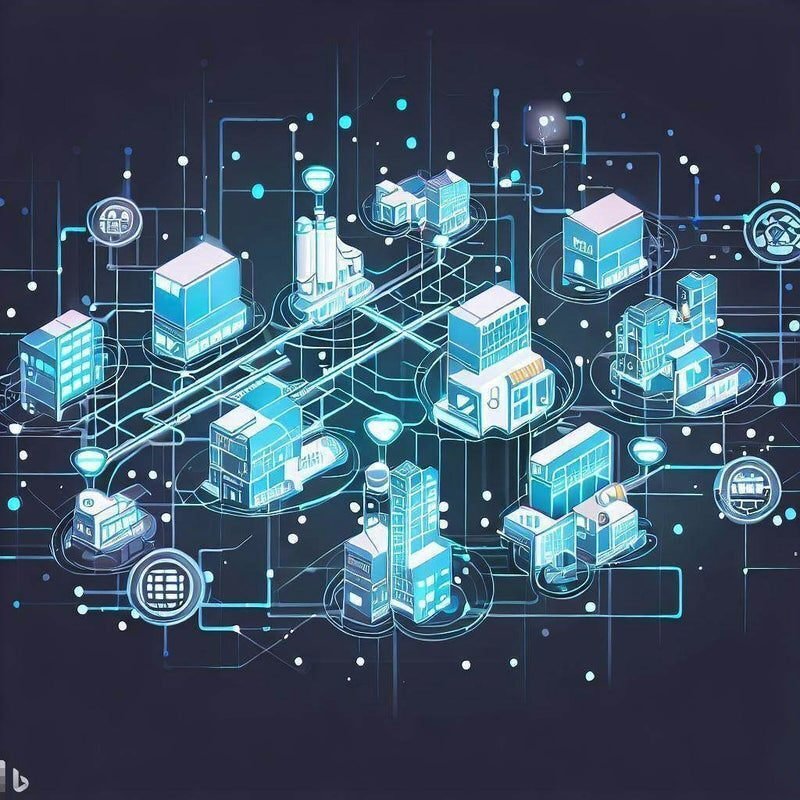
Specifically, we collect data such as production line operating status, inventory status, and order status, and adjust production volume based on AI-based production plan optimization. Additionally, a network connecting multiple factories allows the status of production lines to be shared in real time. Therefore, it is expected that production adjustments will be made more smoothly and quickly.
central control room
In a smart factory, a central control room is required for machines, robots, sensors, and other devices to collect, process, and control data. The central control room can monitor and manage the status and operating status of equipment and devices in real time, and control them as necessary.
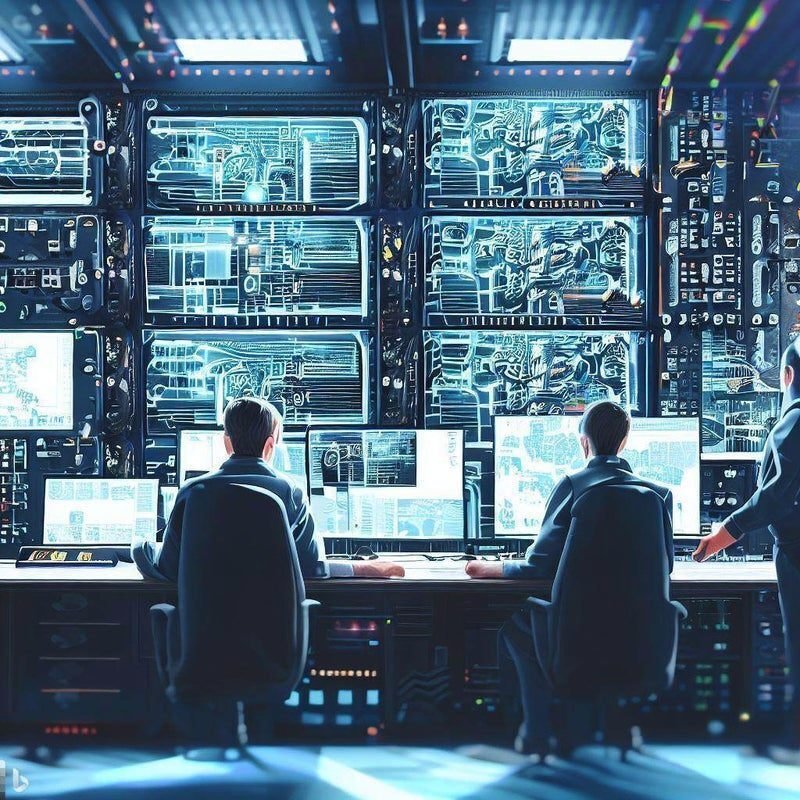
The central control room collects and analyzes sensor data and IoT device data, detects signs of equipment failure and malfunctions, and is able to develop appropriate maintenance plans and optimize production lines. Masu. Additionally, production data can be visualized and analyzed, which can contribute to improving productivity, reducing defective products, and optimizing the workforce.
A central control room can also be built using the cloud. By consolidating data in the cloud, you can grasp the status of the production site in real time and control and monitor the production line even from a remote location, leading to improved operational efficiency.
この記事が気に入ったらサポートをしてみませんか?