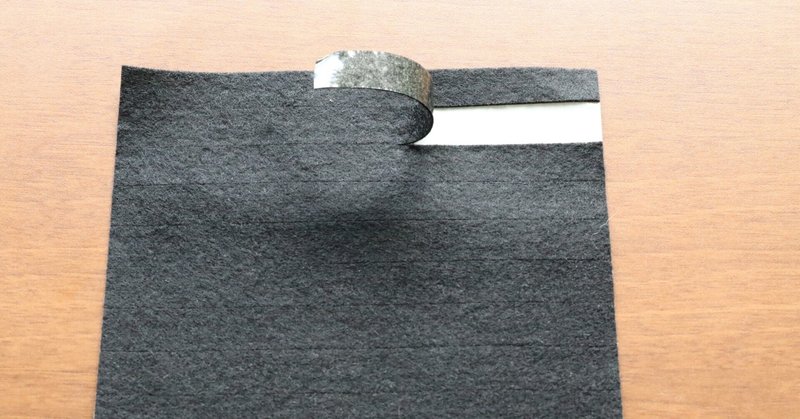
事業承継物語⑤
梅雨入り前ということですがもうすっかり梅雨ですよね。
今年は梅雨入りが早いんだとかで長梅雨になりそうで困ったものです。
今回は事業承継物語とは別で書くかどうか迷ったのですが、ここまでは歴史的な話を中心にしてきましたので少し趣向を変えて『何を承継したのか?』を書いておこうと思います。
まず、そもそも論ですが最初の頃に書いたように我々は型抜加工しかできません。
型の上に材料を乗せて機械でプレス打ち抜きをする!ガシャン!
これが基本中の基本です。
父の若いころはこれで十分仕事になっていました。
ところがある時からビクトリア抜きでも①ハーフカット加工 が出来ないか?と聞かれたそうです。
最初はビクでシールのように抜くのは無理だよ・・・と父は答えたらしいのですがそこでピンときた父はこれからの時代ビク抜き屋でもシール抜が出来ないと仕事が増えないのかもしれない!
そう思ったそうです。それから機械を整備し型も整備してハーフカット加工が出来るビク抜き屋として各方面から重宝されたそうです。
①両面テープのハーフカット
今となっては別に珍しいことではなかったらしいですが当時は自分たちの技術だ!ということでハーフカット加工をしている部分は他では見せなかったようです。
それから少し時代は進み、私が入社したころになるとハーフカットの更に進化版の②スリットカット加工 を求められます。
ハーフカット以上に精度のいる加工方法で機械と当て板と型をきちんと整備しておかないと作ることができない加工方法です。
②スリットカット
そしてその頃の話だと思うのですが、実は父は超画期的な型抜加工方法を考えていたらしいのですが実は未完成に終わってしまったと言っていました。
③転写抜き思考 これは実は今でも難しいなと感じます。しかもニーズが少ないのでなかなかこの技法を試す機会が少ないので進化が遅れています。
その後、さらにお客様から難しい要求が入り部分的に両面テープを貼ってほしいという依頼がきました。④両面テープ部分接着加工 この頃になると私もいっちょ前に加工方法を考えながら工作していました。25歳~30歳ぐらいだったと思います。
④両面テープ部分接着加工
これは1個だけ作るのであれば綺麗に貼り合わせることもできるのですが1000個、5000個と量産になると1個づつ作っていたのでは日が暮れてしまいます。実は多分ですがいまでも中国では1枚づつ貼り合わせている人海戦術で作業しているという話を聞きます。技術的には20年遅れていることになります。
そして我ながらこれは大発明だなと感じたのが⑤手動仕上げ抜き
これはとにかく早く仕事を上げるにはどうしたらいいのか?を考えて苦肉の策で試したところ上手くいってしまい、この技術のおかげで当時PHSのマイクパッキン部品はかなりの数を作ることが出来ました。
⑤手動仕上げ抜き(これはマイクパッキンではありません)
この辺りから現場での技術開発は私が先頭に立って進めていました。
そんなある日またしてもお客様から無理難題が。成形品のように滑らかなディティールにしてほしいと。。。それは成形屋さんに持ち込んだほうが良いのでは???と思ったのですが型代が高いのでビクでなんとかしてほしいという無理難題でした。そもそもエッジが立つのが樹脂抜きの基本です。
そのエッジ面をなくしてほしいと言われて発明したのが⑥裏抜き
⑥裏抜き(左が通常抜き、右が裏抜き)
こうして並べてみると面の違いが判ると思います。これも10年以上続いて流れていた製品です。後にも先にもこれ以外でこの技法を使ったことはないのですが加工実績として受け継がれていきます。
そして私が30歳を過ぎたころに父が未完成で終わらせた③転写抜き思考 を⑦転写抜き完成形 に仕上げました。これは仕事としては決まらなかったのですが試作を作り転写抜きによる量産加工が出来る実験をし成功させました。最初に図面を貰った時に私自身ピンときました。これは転写抜きしかない!すぐに父に話を持ち掛けて父の頭の中にあった転写抜きを図面を起こして説明し、完成形へと導いたのです。写真がないのが残念です。型は一つの製品を作るのに5面必要になりました。今でも残してあります。
その後もとにかくお客様からの要望に応えるたびに新しい技術を身に着けていきます。
分かると思いますが難しい、他社で断られてきた仕事というのはある意味ピンチですがそれを乗り越えるとチャンスに変わるのです。
こんな加工方法もあります。⑧バラシ合わせ抜き
⑧バラシ合わせ抜き
素材の全く違う材料を何層にも貼り合わせて抜く加工方法です。
これの難しい点は両面テープの相性です。ゴムにはゴム用の、アクリルにはアクリル用の両面テープがあり、水に強いだとか熱に強いだとか、基材がPETだとか基材レスだとか・・・とにかく接着強度も併せていろいろな角度から考えて作らないといけません。
このような感じでお客様から無理難題を出されたときに進化をし続けてきたのが精工パッキングです。
これらを踏まえていざ、じゃぁ、精工パッキングの『技術の可視化』を考えた時にどうしたらよいのか?を頭の中で巡らせて思いついたのが⑨極細輪ゴム加工技術 です。
⑨極細輪ゴム加工技術
この写真は実はあまり公式では使っていませんが、これこそが最初に作った1号品で0.2㎜幅という極細の輪ゴムの完成形です。
普通の輪ゴムが1㎜なので約1/5程度の太さになります。
今では強度のことも考えて0.3㎜幅にして展示会などで無料配布しています。
ある意味でこの加工技術は私が経営者になって精工パッキングの方向性を決めてしまった技術でもあります。
これを作るに至った詳しい内容は次回にしますが①~⑧の技術のどれが抜けても⑨には至らなかったのではないか?と感じています。
無理難題を言ってくるお客様にも感謝です。
そしてこの①~⑨までの技術の進化の過程は以前にも書いたように門外不出、一切外にはだすな!という父の鉄の掟によってガラパゴスのように守られてきたのです。
もちろん他にも仕上げ治具の作り方や接着加工技術、エアー抜き接着工法などなど指先の職人技も鍛えあげられて次の世代に受け継がれています。
次回こそは私が社長になってもがいていた部分を書いていこうと思います。
お楽しみに。
この記事が気に入ったらサポートをしてみませんか?