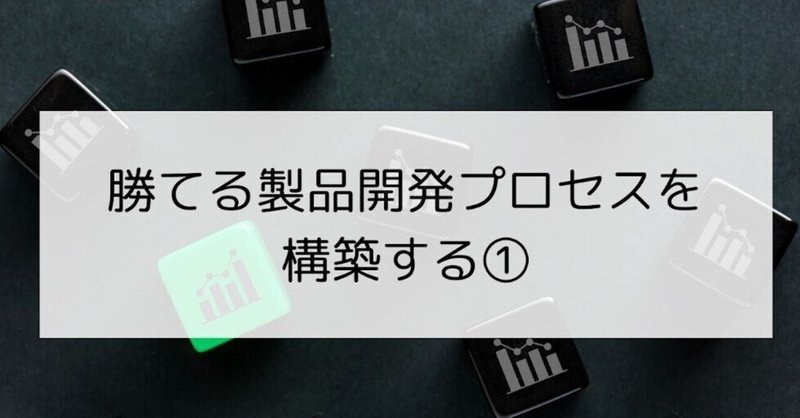
勝てる製品開発プロセスを構築する①
■日本の製造業はなぜ「技術で勝って事業で負けた」のか
「製造業の変革期に求められる日本のトランスフォーメーション」でも述べたように、日本の製造業は「技術で勝って事業で負けた」とよく言われます。
1988年には日本メーカーが世界シェアの50%を占めていた半導体、1970年代に世界に先駆けて日本が初めて産業化に成功した液晶パネル、2019年にノーベル化学賞を受賞した吉野彰氏らが開発して日本企業が世界で初めて市販化したリチウムイオン電池といった現代の私達の生活に欠かせない製品において、21世紀に入り、後発の韓国、台湾、中国のメーカーに、なぜことごとく打ち負かされてしまったのでしょうか。
これらの製品を活用したパソコン、掲題電話、薄型テレビ等でも、日本企業の多くは撤退や事業売却を余儀なくされました。
こうした背景には、技術流出、投資判断のミス、政府支援の有無等様々な要因が挙げられますが、もっとも重要なポイントとして、1990年代から本格的に始まっていた「ものづくりのあり方」そのものの変化を理解することが重要です。
「ものづくりのあり方」が変化すれば企業の競争戦略も変わり、製品開発・製造・販売の方法も変わってきます。
以下では、企業の競争力に大きな影響を与える製品開発に注目して、開発現場でどのようなトランスフォーメーションが行われており、今後、日本の製造業が世界で勝つためにどのような戦略が必要なのかを考えていきます。
■製品開発を取り巻く3つの変化
「ものづくりのあり方」が変わったことにより、企業の製品開発には以下のような3つの変化が起こってきています。
(1)製品アーキテクチャーの変化
(2)利用できるデジタル技術の変化
(3)製品価値に対する考え方の変化
1つ目の「製品アーキテクチャー」とは、製品の基本設計思想と言い換えることもできます。工業製品においては、各部品やコンポーネントにどのような機能を与え、それらをどのように組み合わせて製品全体の機能を実現するのかを決める考え方を称して「製品アーキテクチャー」と呼びます。
主要な考え方としては、「モジュラー型」と「インテグラル型」が挙げられます。「モジュラー型(組み合わせ型)」の製品は各部品やコンポーネントの持つ機能が比較的シンプルに決まっており、それぞれをつなぐインターフェイスの設計ルールに従えば簡単に製品が作れるという特徴を持っています。
これに対して、「インテグラル型(擦り合わせ型)」の製品では、部品と機能が必ずしも1対1の対応をしておらず、1つの製品性能(例えば、自動車の乗り心地)を実現するためには多数の部品(エンジン、サスペンション、シート等)の設計を微妙に調整することが必要となります。
「メーカーと部品メーカーの主従関係の変化①」でも解説したように、20世紀後半のエレクトロニクス産業の発展に伴い、製品内の各機能を組み込みソフトウェアで制御する「モジュラー型」の製品へのシフトが始まりました。
これに伴って、製品の機能にけるソフトウェアの比重が高くなり、パソコン、スマートフォンやデジタル家電はもちろん、自動車を始めとした従来はメカニクスで動いてきた機械や機器においても電子機器やそれを制御するソフトウェアの役割が拡大をしてきています。
新型コロナウィルスの影響で半導体のサプライチェーンが寸断した際に、自動車の生産に大きな影響が生じたことは皆さんの記憶にも新しいと思います。これこそが、現代の自動車では様々な機能の制御にソフトウェアが使われている証左と言えます。
このように製品におけるソフトウェアの占める重要性が高まっていることは、製品開発の進め方にも多大な影響を与えています。
2つ目のポイントは利用できるデジタル技術の変化です。かつてはアナログで引かれていた図面や実際の試作機を用いて行われていた解析は、2D-CADや3D-CADや様々なデジタルツールの活用により、CAE(コンピュータ支援開発/エンジニアリング)によりデジタル上でシミュレーションを行うことができるようになりました。
さらには、3Dプリンターの活用による試作費の削減や業界によっては製品開発へのAIの活用も始まっています。例えば、食料品・飲料産業では、これまで経験豊富な開発担当者の試行錯誤により生み出されていた新商品のレシピをAIの需要予測を活用する試みが始まっており、日清食品の「カレーメシ」シリーズとして販売された「トマトチキン味」は、2,400万通りの材料の組み合わせの中からAIが選び出した商品です。
また、膨大な材料データから素材開発を行う化学産業でも同様にAIの活用は行われており、旭化成、東レ、ENEOS等で開発期間の短縮に貢献しています。これらの取り組みは、マテリアルズ・インフォマティック(MI)と呼ばれています。
3つ目のポイントは製品が持つ価値に対する考え方への変化です。これまでの製造業では、製品のQCD(品質、コスト、納期)が顧客価値と捉えられてきましたが、近年ではエコロジーや人権に配慮した原料調達などの環境価値や社会価値も求められるようになりました。
また、製品に占めるソフトウェアの比重の増加や製品開発プロセスのデジタル化に伴い、以前に比べて顧客の幅広いニーズに対応することができるようになってきました。
従来の製造業では、少品種・大量生産に基づく「マス・プロダクション」でコスト効率を追求してきましたが、より細かな顧客のニーズ応える「マス・カスタマイゼーション」を追求する方向に向かいつつあります。こうした製品が持つ価値の変化に伴い、製品開発のプロセスの変革も並行して進められています。
■製品開発DXの3つのポイント
具体的な製品開発のDXについて見る前に、改めて企業が製品開発を行う目的は何かという原点に立ち返ってみましょう。
企業が製品開発を行う最大の目的は、予想される市場の変化に備えて企業の競争力を高めて、将来における企業価値を上げることが命題となります。市場のニーズを予測して価値の高い製品をタイムリーにかつ適正価格で新製品を投入することが、競合企業との差別化につながるからです。
このためには、製品開発にコストをかけるための収益を確保しつつ、開発プロセス自体もできる限りコストを削減しながら進化の早い市場に合わせてスピードアップをさせていく必要があります。
このような前提に立つと、企業が製品開発DXを進めるうえでのポイントが明確になります。
(1)開発コストの削減
(2)開発期間の短縮
(3)販売部門や保守サービス部門とも連動することによる市場ニーズを
先取り
1点目の開発コストの削減は、製品のモジュール化や2D-CADや3D-CADなどによるコンピュータでのシミュレーションを活用すること等が進められています。モジュール化は各部品の機能と関係性を明確化することができるため、各開発工程の役割分担が明確になり、スムーズな開発につながります。
また、モジュール化により、部品やプラットフォームを他の製品と共有することも可能となり、大幅な開発コストの削減につながります。ただし、自動車の乗り心地の例でも示したように、あらゆる機能から擦り合わせの要素を排除することができません。
このため、多くの製品が完全な「モジュラー型」にはならず「一部モジュラー型」に留まります。コンピュータによるシミュレーションは、様々な分野で活用が広がっています。かつては自動車の新車設計には、開発段階や目的に応じて数百台もの試作車がつくられており、これらは1台ごとにカスタマイズして作成されるためそのコストは数億円にものぼると言われていました。
こうした実機を作成する手間とコストを削減する上で、デジタルデータによるシミュレーションは大いに役立っています。
2点目の開発期間の短縮は、コスト削減ともつながる重要な視点です。もちろん開発の各工程でのデジタルツールの活用は、開発のリードタイムの短縮や人件費の削減につながります。しかし、それ以上に製品開発においてもっとも避けたいのは、開発プロセスの後工程で予期せぬ不具合が生じて発生する手戻りが生じることです。
このため、現在の製品開発では初期の設計段階で想定される限りの課題やリスクを洗い出して検討をしておくことで、後工程での手戻りを防止する努力が図られています。シミュレーションで必要なるデータは、過去の設計・開発時の実験データ、部品・素材等の調達データ、製造工程における各種データ、販売・保守部門からのデータ等膨大な量となるため、デジタルデータを活用したシミュレーションやAI等の活用が必須となってきています。
3点目の販売部門や保守サービス部門とも連動した製品開発は、開発における手戻りを防止する上でも重要ですが、それ以上に短期化する消費者のトレンドサイクルに対応するために重要な取り組みとなっています。
特にこうした傾向が顕著なのはソフトウェア開発の分野で、社会的なニーズや課題を先取りした製品開発を行うことで競合他社に対して大きなアドバンテージを確保することが可能となります。ハードウェア製品におけるソフトウェアの占める比重が高まっている今日では、最終的な販売・保守までの製品サイクル全体で最適化を行っていく重要性はますます高まっていると言えるでしょう。
以上の3つのポイントを踏まえた改革を進めていく上で、近年の製造業ではどのような取り組みが行われているのかを次のパートで見ていきたいと思います。
■製品開発現場で進む3つのトレンド
「失われた30年」と言われる経済停滞の中で、世界の製造業の現場では製品開発にも大きなトランスフォーメーションが起こっています。代表的なものとして以下の3つを取り上げたいと思います。
(1)モデルベースの製品開発
(2)共通プラットフォームによる開発
(3)ソフトウェア・ファーストに伴う開発のオープン化
1点目のモデルベースの製品開発(MBD)は、初期設計の段階で作成したモデルをベースに徹底的にシミュレーションを行う製品開発手法です。この手法は航空宇宙産業で始まりましたが、背景には自動車などと比べて気軽に試作機を作成して課題をつぶしていくことが難しいという製品特性があったと言われています。
モデルベースの製品開発では、製品のもつ機能ごとにモデルを策定してCAEによるシミュレーションで評価をしながら、検証、修正、評価の流れを繰り返して課題をクリアしていきます。実機を作成して実験をする場合と比べて、製作コストの削減を行うことがでるだけでなく、開発スピード自体のアップ、複数の機能を同時に開発していくことが可能となる点も魅力的です。
また、一度の開発で蓄積されたデータが次の開発にも生かせるのは、技能継承の面でもメリットがあると言えます。
MBDは製品機能が複雑化している自動車業界でも、1990年代から2000年代にかけて各社で取り入れられるようになりました。これにより試作車の台数を大幅に減らすことが可能となりました。
例えば、かつては試作車を実際に走らせて行われていた衝突安全性能の実験についても、現在ではかなりの部分をシミュレーションで行うことができるようになりました。自動運転技術が実用化の段階に入ってきている中で、ますますMBDは重要性を増しています。
経済産業省も日本の製造業が伝統的に強みとしてきた「擦り合わせ」型開発を深化させる手段として、MBDをサプライチェーン全体で取り組んでいくプロジェクトである「SURIAWASE2.0」を2017年に発表しました。
MBDを成功に導くカギは、開発の初期段階でできる限り精密なモデルを設計することにあります。これには正確なデータの測定と精密なモデルの両方が必要となり、実現のためにはIoTを活用した正確なデータの収集とAI等も活用した精緻なモデル化が有効です。
これらにより、「デジタルツイン」と呼べるほどに正確なシミュレーションモデルが形成できれば、設計時点での様々な検証をデジタル上で行うことができるようになります。ここから3Dプリンターを活用して「仮現物モデル」と呼ばれる試作機を使った物理試験を組み合わせることで、より効率的な開発を行っていく手法も模索されてきています。
2点目の共通プラットフォームの活用は、膨らむ開発コストを抑える手法として有効です。例えばかつての自動車メーカーでは、車種だけでなく販売地域が固有の特性や規制に合わせて最適な部品やユニットを開発していたため、多種多様なニーズに合わせた製品開発が費用の高騰を招き、最終製品の価格競争力にも影響を与えていました。
このような事態に対して、車体の一部を複数の車種を跨ぐ共通プラットフォームとして共用化して、カスタマイズが必要な部分のみを新規に設計する方式への大きな転換が図られました。
例えばトヨタは、2015年から「トヨタ・ニュー・グローバル・アーキテクチャー」(TNGA)を始動して、車台、エンジン、トランスミッション、ハイブリッド用ユニットの共通化を図り、4代目プリウスから採用を始めました。
この際にこれまでの自前主義の制約を外して、グローバル標準規格での調達も行うようになり、これは部品メーカーにとっても製品開発の進め方を変える大きなきっかけとなりました。プリウスに始まったTNGAによる共通プラットフォームは、カムリやレクサス、さらにはダイハツのミライ―スやタントにも採用され、これによりグルーピング開発(定められた「アーキテクチャー」をベースに、複数車種を同時並行で開発すること)が可能となりました。こうした共通プラットフォームの活用は、独フォルクスワーゲングループやルノー・日産アライアンスにも波及しています。
3点目のソフトウェアのオープン開発は、IT産業では古くからとられてきた手法で、開発スピードのアップや開発コストの抑制に効果があります。情報通信機器やデジタル家電だけでなく、精密機械や自動車においてもソフトウェアによる機械の制御が重要となってきている中で、ハードウェアの製造においてもソフトウェアが製品の価値を決める比重は高まってきています。
こうした考え方は、「ソフトウェア・ファースト」の製品開発と呼ばれ、自社製品を「洗練された車輪付きのコンピュータ」とCEOのイーロン・マスク氏が呼ぶテスラがその最たる例と言えます。ここまで極端ではないにしても、元来自社や系列などの閉鎖された空間での開発を推進してきた自動車業界でも、製品に占めるソフトウェアの重要性を踏まえてオープン開発の取り組みが部分的に始まっています。
もっとも顕著な分野が自動運転技術に関するもので、トヨタは2023年に、子会社のウーブン・バイ・トヨタが自動運転用のソフトウェアをオープン開発するプラットフォーム「アリーン(Arene)」を2025年に実用化すると発表しています。
また、半導体設計大手の英アーム(Arm)は、2020年に通称ソフィー(SOAFEE: Scalable Open Architecture For Embedded Edge)と呼ばれる各社が開発中の自動運転用のアプリケーションを定義する社会インフラとしてのミドルウェアを提供することを発表しました。自動車メーカーの各社がOS、ネットワーク、セキュリティといった「非競争領域」(誰が提供しても大きな差別化要因にならない領域)で不要な重複開発を防ぐ役割が期待されています。
自動車産業以外でも、脱炭素の取り組み等自社だけでは解決できない社会的な課題を求められるケースが増えてきており、ますます企業や業界の垣根を超えたソフトウェア主導の開発のオープン化は進んでいくものと考えられています。(山縣敬子・山縣信一)
後半は「勝てる製品開発プロセスを構築する②」をご覧下さい。
<<Smart Manufacturing Summit by Global Industrie>>
開催期間:2024年3月13日(水)〜15日(金)
開催場所:Aichi Sky Expo(愛知県国際展示場)
主催:GL events Venues
URL:https://sms-gi.com/
出展に関する詳細&ご案内はこちらからご覧ください。
<<これまでの記事>>
諸外国の「ものづくり」の状況とトレンド①
日本の製造業の歴史を紐解いてみる
日本の製造業の成長を促した構造的要因とは?
日本の製造業の競争力を低下させた構造的要因
「Next Industry 4.0」に向けて動き出した世界の潮流
少子高齢化に伴う製造業従事者の多国籍化
後継者不足の解消と事業承継支援の取り組み
製造業の変革期に求められる日本のトランスフォーメーション
日本の製造業に求められる4つの視点
社会課題の解決にむけたものづくり
日本のものづくりの特徴は「多様性」と「もったいない」?!
勝てる製造業のDX
勝てる製品開発プロセスを構築する②