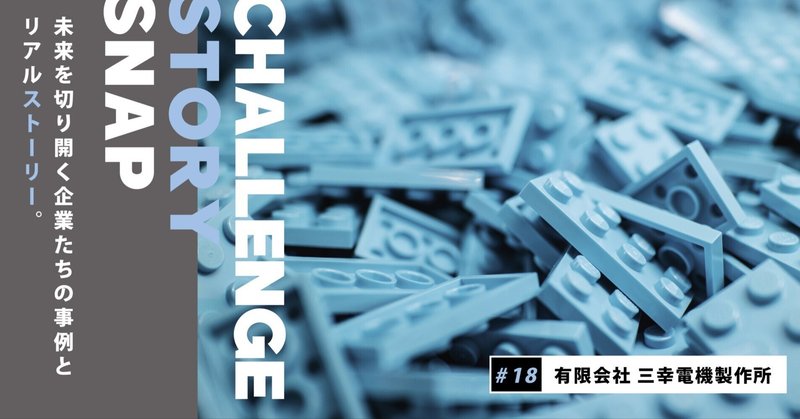
紙とプラスチックを混ぜる?常識を覆したのは地道すぎる努力だった
企業が挑戦をする。よく聞くフレーズではあります。そして、その挑戦は得てして大きな打ち上げ花火をイメージさせます。新商品、新発明、新開発、新発見など、今までになかったものが突然現れる驚きです。
しかし、実際の挑戦とは、もっと地味なものです。細々と続けていたものが少しずつ形になっていき、気づけば日の目を見るようになる。そんな連続的な変化こそが、挑戦の真の姿かもしれません。
今回お話しを伺った企業もまさにそのような挑戦を続けています。10年以上もかけて1つの素材に向き合い続けて、その結果、環境問題への突破口を開こうとしています。私たちは今環境問題に直面しています。そして、まだそこへの解答は見つかっておりません。
今回の主人公である三幸電機製作所は、一つの可能性を見出しています。それが、「東京未来素材」です。東京未来素材とはなんなのか。そして、それがどのように環境問題の突破口になるのでしょうか。
高度経済成長を支えた樹脂
1965年、日本は高度経済成長の真っ只中にいました。製造業が右肩上がりで成長曲線を描く、そんな時代に、三幸電機製作所は東京の武蔵小金井に誕生しました。創業者は現在の社長である近藤伸二さんの父親です。
当時の三幸電機は、ベークライト(フェノール樹脂)と呼ばれる素材を成形して電機製品のパーツ製作を請け負っていました。ベークライトとはプラスチックの一種で、今でこそ生産量も減っていますが、高い絶縁性などから電機製品のパーツには欠かせないものとして重宝されています。
まさに、高度経済成長の縁の下の力持ちとして、さまざまな電機製品のパーツを製造していきます。そこから、三幸電機は、フェノール樹脂だけでなく、新しい素材へも積極的に取り組みながら、成長を続けていき、現在も、プラスチック樹脂の成形をメイン事業としています。
外需からの転換を目指す
自社工場を持ち、プラスチック成形の高い技術を備えている会社が、なぜ「東京未来素材」という新素材を使った商品を開発するに至ったのか。それには、とても長い年月が必要でした。
最初のきっかけは、近藤伸二さんが当時の社長である父親から、中小企業振興公社の有志のグループに勉強も兼ねて参加するように進められたところからでした。
多摩地区には高い技術力を持った企業がたくさんあるにもかかわらず、企業同士の交流はとても少ないものでした。技術という無形資産をもっと活かすためにも、企業同士の交流を活発化させ、そこから新しい可能性が生まれてほしい、そんな思いもあったのでしょうか。多摩地区の企業21社が集まる有志のグループが誕生しました。
そして、この時の三幸電機は、1つの目標として外需からの転換を考えていました。電機製品や回路などのパーツを発注してくれる企業の多くは、輸出の動向から影響を大きく受けてしまいます。そして、その煽りを受けるのは三幸電機でした。自分たちの品質がどれだけ高くても、為替や海外の情勢の影響を受けて、注文数が50%減になってしまうこともしばしばです。
このように自分たちでコントロールできないところ、わからないところで、会社が不安定になるようではいけないと考え、外需から内需への転換を考えていました。そのような思いから有志のグループへ参加した、三幸電機ですが、その思いが形になったのは、そこから20年も経った頃でした。
20年越しの想い
有志のグループが結成されてから、約20年。さまざまな失敗やトラブルも経験しながら、安定的な自治が浸透していき、多くの仕事が生まれている中で、近藤さんの元に思わぬプレゼントが届きます。それも、最初は、プレゼントかどうかもわからない形で。
振興公社の多摩の担当者だった方から、紙をパウダーにする技術を持っている会社があるから、一度会ってみませんか、と言われたのです。
それが一体何になるのか確信もないまま、近藤さんはその会社へ伺い、紙をパウダーにする技術の紹介を受け、プラスチックに紙が混ざった素材に出会えたのです。
その当時、紙をプラスチックに混ぜて成形していた会社は日本には見当たりませんでした。そのことを面白いと思った近藤さんは、早速、紙を混ぜたプラスチックを新素材として、成形を進めていきます。
そして、すぐに気づいたのです。なぜ、日本に同じことをしている企業がいなかったのか。
常識を乗り越える
プラスチックの成形には熱がポイントです。樹脂をドロドロに溶かすために高温にした後に、金型へ流し込み冷やすことで成形が完成します。
これを紙の混ぜた樹脂でやるとどうなるか。答えはとても簡単です。木屑の薄く焦げた甘い匂いがしてしまいます。熱をかけてはいけない紙と熱をかけなければいけないプラスチック。この掛け合わせは、あまりにも矛盾を孕んだ組み合わせだったのです。
しかし、近藤さんはこの素材は使えないと諦めることはありませんでした。温度の調整、熱の掛け方、紙のパウダーの細かさなど、調整を進めながら、何度も何度もトライを重ねることで、匂いを極限まで抑えることに成功しました。
なぜ近藤さん以外には、それができなかったのかと伺うと、誰もが途中で諦めてしまうから、と答えてくれました。絶対に成功させようという執着心とできるという信念を持ち続けた近藤さんだからこそできたことかもしれません。
この成功をスタートして、近藤さんは、色のついたコップやカレー皿など様々な製品を作り出していきます。
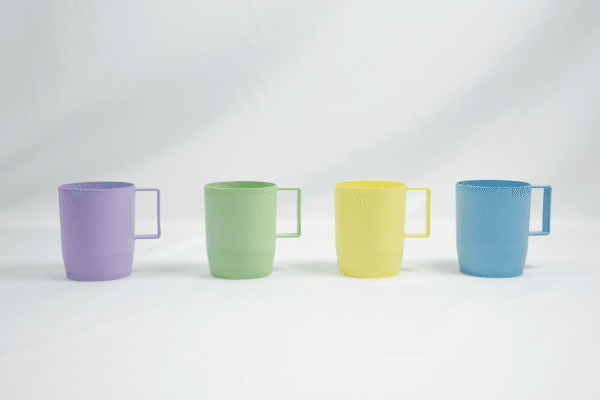
「東京未来素材」の誕生
この紙を混ぜたプラスチックの大きな特徴に、分類上、紙になるという点があります。紙の配合率に近藤さんがこだわった由縁でもあります。その結果、可燃物として処理できる上に、燃やした時に有害なガスを発生しません。
そして、プラスチックの特徴である耐水性や加工のしやすさはそのままです。
これは、紙とプラスチックのいいとこ取りをした新素材であり、今年、近藤さんはこの素材、そしてこの素材を使ったブランドを「東京未来素材」として登録をしました。
それは、この新素材が、未来を変えていく一助になってほしいという想い、そして、ずっと東京の多摩地区でコツコツと続けてきたプライドが重なっているようです。
大きな変化ではなく、地道に続けてきた活動が一つの花になる時、その花を支えているのは多くの人との出会いであり、表からは見えない仕事の積み重ねかもしれません。
三幸電機製作所の「東京未来素材」も多くの人との出会いや仕事の積み重ねによって誕生しました。
中小企業が変われば、日本が変わる。その思いをもとに、今まさに変わろうとしている、新しい挑戦に取り組んでいる、チャレンジしている中小企業をご紹介しました。
三幸電機製作所の新しいプラスチック「東京未来素材」が、あなたの明日の生活を変えるかもしれません。
それでは、次回のnoteもお楽しみに。
三幸電機製作所さんのホームページはこちらです