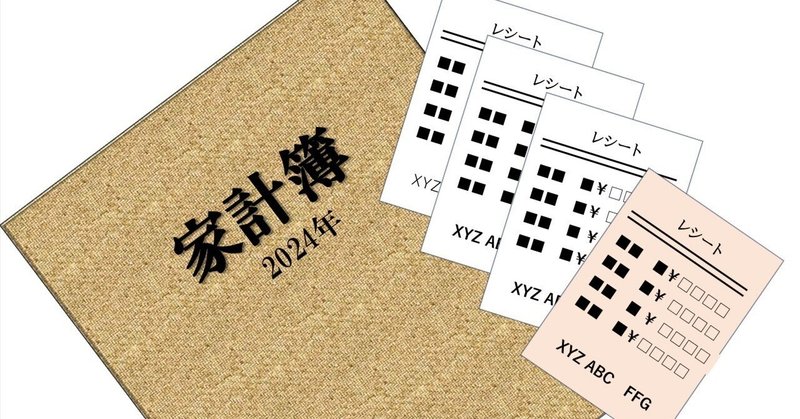
「見える化」による『コストダウン』=家計簿作成と出費削減
1990年台のバブル崩壊とこれに続き半導体戦争に敗れた半導体製造の現場では、新規技術、新規デバイスの開発よりも『改善』、『コストダウン』に力を入れなければならない状況が続き、その中で、経験してきた活動の中で、得られた各種手法の習得とともにその裏にある哲学にも触れたいと思います。製造現場でのコスト削減活動と家計簿を丁寧にまとめて出費を抑える活動は、似ています。スタートポイントは、「見える化」です。
何よりも改善に必要なのは、「見える化」の実現とこのデータを用いた分析に限ります。利益を上げるために高付加価値の新製品を創出出来なければ、『コストダウン』と『生産性向上』しか取るべき道はありません。只、『コストダウン』、『生産性向上』と念仏を唱えても何も起こりません。まず着手すべきことは、現状の「見える化」の作業であることを叩き込まれた次第です。
ちょっと身近な例に立ち戻りますが、個人の家庭でも限られた収入を基に、貯蓄を増やしていくためには、収入を増やすか、or、出費の削減しか手はありません。収入を増やすトライは、色々とチャレンジはするものの、環境の影響が大きく、社会情勢や経済状況に依存して自力ではどうにもならないことが多いことはお分かりかと思います。一方、出費の削減は、独力で進められるものであり、賢い皆さんは、日々血のにじむ様な努力をされていると思います。ここで力を発揮するのが「家計簿」でしょう。日々のお金の使用状況を記録して、この状況を把握するためのデーターベースを作り上げるわけけです。これが正に、「見える化」ということです。家計簿の結果から、月ごとや年ごとにその傾向を分析し、どの出費に手をつけるのかを考えます。まずは、保険料、電気代、水道料等の固定費と、食料、外食や遊興費等の変動費に分けてみるのではないでしょうか? この中から、無駄の洗い出しとともに削減すべき、or、削減できる出費を選び出して施策を検討することになるでしょう。固定費は、毎月定期的に出ていく金額なので、これが削減できれば、年間を通して大きな効果が期待されます。例えば、節水しようとか、節電しようとかということは直ぐにでも出来ます。一方、変動費用は、日々の変動が大きく、中々打つ手が分からないのですが、変動費の中身を更に分類を明確にしていき、例えば、外食出費が大きいのであれば、外食機会を抑えようとかということになると思います。また、家計簿の過去のデータと比較して、前の年に比べ増えているものをピックアップするのも大きな効果を得る場合があります。例えば、それが電気代であれば、契約自体を見直すことも行うでしょうし、食費であったならば、食材のメーカーを変える等の方法が検討されるでしょう。この様に、家庭の出費もまずは「見える化」がスタートポイントで初めて具体的な活動が開始されるのでしょう。また、「見える化」の家計簿があれば、節水節電や購入商品の廉価品への変更で、月当たりの削減効果も予測されるでしょうし、また、実際にそれらの行動が行われた結果としてどの位の効果が得られたのかも「見える化」され、PDCA=Plan Do Check Actionの改善サイクルが回りだすことになります。これにより、改善の維持と、更なる改善行動の推進に繋がっていくことなると思います。この様に「見える化」こそが、改善活動の原動力なのです。
企業での『コストダウン』、『生産性向上』の活動も、この家計簿による家庭の出費削減行動と同じです。何れもアプローチすべき対象は異なりますが、「見える化」がスタートポイントになります。「見える化」からスタートする製造の改善活動は、1990年台の後半から苦境に陥った筆者の所属した日本半導体の製造現場で強力に進められた活動でした。それまでは、会社運営に必須の管理会計の手法による原価計算や事業計画に寄与する製造能力の把握の作業は行われていましたが、製造現場での改善活動という形では着手されてはいませんでした。まず、製造現場での『コストダウン』は、製造原価をそれぞれの製造工程で洗い出し、原料、材料、消耗材費用、必要人件費からメンテナンス費用まで、漏れなく「見える化」することにより問題点を洗い出すことが、スタートポイントとなります。具体的な手法は、某外資系大手コンサルティング会社(マッキンゼー)から教授して頂いた手法です。後の寄稿で、必要な方には別途、具体的な手法をご説明申し上げたいと思います。一方、『生産性向上』では、製造に必要なすべての製造装置の生産能力=単位当たりの製品処理能力を洗い出し、生産のボトルネックを洗い出し、ボトルネックの装置に関しては、稼働、不稼働の状況の「見える化」とともに時間当たりのスループットを把握する作業が進められました。これも後の寄稿で、必要な方には別途ご説明申し上げたいと思います。出来上がった「見える化」されたデータは、出来るのであれば、競合他社と比較して問題点を洗い出しますことが望まれますが、多くの場合、競合のデータは知ることが出来ないことから、社内の工程間、装置間で比較して、すべての「見える化」されたデータを、ベストなものに調整するための施策を検討し、実行していくというものです。これにより得られたベストな工程間、装置を統合し、最も合理的な生産体制を再構築するというものでした。簡単な、そして、地道な作業になりますが、ベストを総合すると、相当大きな効果を達成することが出来ました。
以上のように、家計管理と製造業のコスト削減及び生産性向上は、見える化の観点から、データの収集と分析という共通のフレームワークで理解することができます。これは、個人の家計管理から大企業の改善活動まで、幅広い領域で応用可能な原則であり、見える化の重要性を示しています。
「見える化」による製造現場でのコスト削減活動の進め方は下記に・・・
この記事が気に入ったらサポートをしてみませんか?