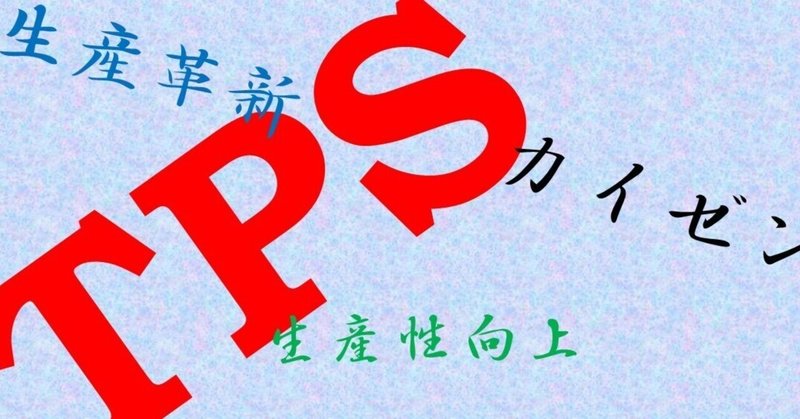
TPSでは生き残れなかった日本半導体製造現場
1980年代に隆盛した日本半導体製造は、その直後に吹っ掛けられた日米半導体戦争に屈して、強制的な売価制限と米国製品の購入義務により、競争力が大きく弱められ、加えて、1990年代のバブル崩壊後の経済状況と相まって、日本の半導体産業は壊滅的な打撃を受けました。この状況で体力を奪われたことから、大きな投資を必要とするメモリ生産を諦め、システムLSI製造への打開策を求めて行きました。この多くの半導体デバイスメーカーも、専用顧客であった自前家電製品の競争力の低下から、事業縮小を迫られました。今では車載製品に活路を見出したルネサスエレクトロニクスのみが生き残ったと言っても過言ではありません。一方、ソニーセミコンダクターはイメージセンサーに特化した形、旧東芝であるキオクシアはNANDメモリで躍進を続けていますが、これは例外的な事例であると思われます。
1990年代にこの様な危機を受けて、実は、日本の半導体メーカーは手をこまねいていたわけではありません。各社とも、生産改革に着手しました。具体的には、製造プロセスの効率化、製造装置の生産性向上及びコスト削減などが行われました。コスト削減活動に関しては、その具体的な手法を下記に詳しく触れているので、ご覧いただければ幸いです。
製造プロセスの効率化とは、正に製造工程の手直しでありました。半導体デバイスの製造工程は、当時でも500工程程度、現在では1,000工程を超えるような長大な製造プロセスとなっていますが、その内、1割でも削減する様な、血のにじむ努力が行われました。実際には、工程削除の影響に関しては、製品で評価しながらの検証を経ての実行なので、時間と手間が掛かってしまい、デバイスの価格低下に中々追いつかない状況でした。これと並行して、現場で直結した製造装置の生産性改善活動を実施しました。製造装置の生産性向上達成により、一枚でも多くのウェハーを処理して出荷に結び付ける努力が行われた分けです。これが達成されましたなら、大きな設備投資を伴わず生産量が増える分けで、事業改善効果も大きく、また、それ以降の生産拡大投資の場面でも、投資金額を抑制することが可能となり、大きな意義がありました。
当時の生産革新で、お手本とすべきとなったのは、「トヨタ生産方式」でした。経営陣はこまった時には「トヨタ経営」に学べと言った短絡的な指示でした。さて、製造形態には、ライン方式、セル式、ジョブショップ式の3つの主要なタイプに分類できるとされています。これらの生産方式は、それぞれ異なる特徴を持ち、製品の種類や生産の要件に応じて選択されます。ご存じのように、「トヨタ生産方式」は、車生産のために進化してきたものであり、その根底には、思想的にどの様な業務にも共通することが謳われていますが、実際に体験した立場から申し上げると、やはり車生産ラインで採用されているライン方式に適したものであると言わざるを得ません。半導体生産は、装置産業とも呼ばれており、投資の効率性からジョブショップ式で構成されており、実際に「トヨタ生産方式」による生産革新では効果を上げることが難しかったと思います。
まず、各生産方式の説明ですが、ライン方式は、連続的な流れの中で各作業者が特定の作業を行う方式です。この方式は、少品種大量生産に適しており、作業の標準化と効率化が可能です。自動車産業の組み立てラインなどが典型的な例です。ライン方式の主な利点は、生産効率の高さと、低コストでの大量生産能力構成が可能です。フォードによる車の大量生産で編み出されて以来、機器の組み立てラインで発達してきたもので、トヨタによって成熟したと言えます。一方、セル式は、日本の小型電気機器製造の場で編み出されたとされていますが、作業者が複数の工程を担当し、製品や部品の組み立てが完結するように設計された生産単位(セル)で作業を行う方式です。この方式は、多品種少量生産に適しており、市場の変化や製品の多様化に柔軟に対応できます。セル式の利点は、生産変動への高い適応力と、少人数での多品種少量生産の可能性です。最後に、半導体製造現場で採用されている生産ラインの形態は、ジョブショップ式です。多品種少量生産に最も適しているこの方式は、特にカスタマイズが必要な製品や、特殊な技術を要する製品に適しており、専門性の高い作業者もしくは装置を準備することにより、高い効率で多くの品種を生産出来る特徴があります。ジョブショップ式の利点は、特徴のあるそれぞれの製品に合わせたカスタマイズが可能であることです。端的にライン式とジョブショップ式の比較を認識するために、下記を示します。
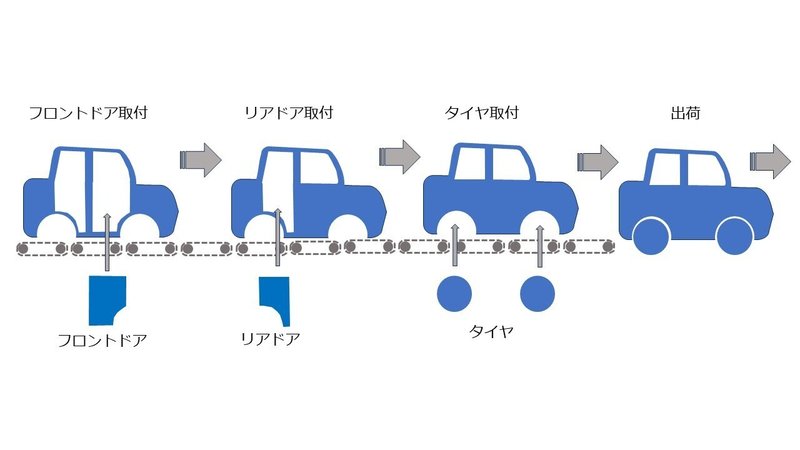
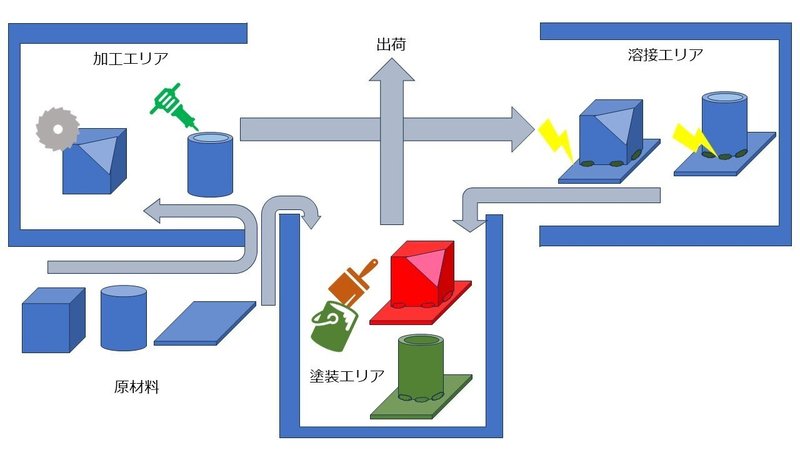
改めての「トヨタ生産方式(Toyota Production System, TPS)」の説明ですが、製造業における生産性向上のための革新的なアプローチとされています。トヨタの生産ラインでの経験を生かした形で、多くの先生方が、「トヨタ生産方式」を提唱し、独自コンサルビジネスを展開されています。このシステムは、ムダを排除し、効率を最大化することを目的としています。TPSの核となるのは「ジャストインタイム」と「自働化」の二つの主要な原則です。ジャストインタイムは、必要な部品を必要な時に必要な量だけ供給することを指し、在庫の過剰を防ぎます。これにより、在庫コストの削減とスペースの有効活用が可能になります。理想的なジャストインタイムは、生産ラインの平準化を促進し、生産プロセスの効率化に寄与できますが、例えば、事故や天変変異で、部品入手が滞った場合に、ライン停止を招き、大きな混乱を起こすことは、最近、大きなニュースとなっています。一方、自働化は、フローライン上に配置された機械や設備で一か所でも異常が発生した場合、直ちにライン全体が停止するので、誰の判断を乞うまでもなく、ラインが自動で停止するシステムです。トラブルで直ちにライン全体が停止されるため、これを原因とした不良品の生産を防ぎ、品質の維持と改善も図られます。また、従業員が機械の監視から解放され、より価値の高い作業に集中できるようになるとされていますが、一度、トラブルが発生するとこの障害が取り除かれるまでラインは停止しますので、非常事態に陥ります。私としては、非常事態に全集中して、順次問題を解決していく手法が、「トヨタ生産方式」による生産革新であると認識した次第です。
一方、半導体製造ラインは、ジョブショップ式を取るために、一部装置でトラブルが発生して生産が低下していても、少数の現場で活動する担当者やライン管理者は認識出来ません。トヨタのフローラインでは、トラブル発生時にはフローライン自体が止まりますので、現場全体で、トラブルが認識されますが、ジョブショップ内の装置一台が故障して停止しても、他の装置が、同じ工程を処理し続けるために、一台のトラブルは注目されません。停止ならまだしも、一部スループットの低下や、小さな品質異常ならなおさら注目を集めることはありません。この様に毛色の全く異なるライン形態で構築された「トヨタ生産方式」のオオソリティの方々からご指導いただいたのは、この異常による装置停止からの復帰速度の向上でした。半導体製造装置には、装置状態を示すための赤青緑黄色の光を発するパトライトが装着されていました。青点灯が製品を待っている状況、緑点灯時には製品処理中で、赤点灯は装置異常による停止を示す仕様になっています。この赤の状態を如何早くになくすかという課題です。製造担当者が忙しいと、赤点灯でも処置に手がつかないことが問題視され、最終的には、青や緑の表示を隠して、赤の点灯のみを見えるようにするという対策でした。即ち、この故障の見える化の実施と、故障からの復帰状況のトレースを強化した次第です。次の段階では、見える化された異常の発生状況と復帰へのアプローチの様子をまとめ上げて、根本対策を打っていく「カイゼン」アプローチの充実が図られました。
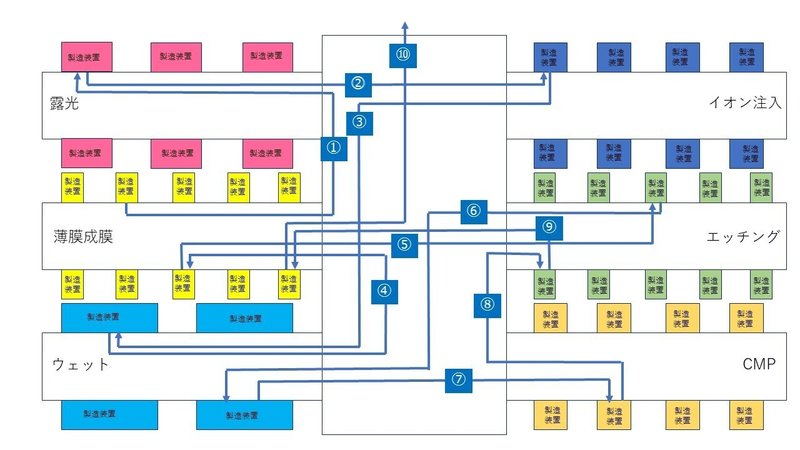
「カイゼン」活動は、今では、製造現場で広く進められていますが、装置数台の稼働安定性が、「カイゼン」により向上したとしても、直接経営へ貢献することは少ないと思います。そこで考案されたのが、ジョブショップのそれぞれのショップにおける仕掛数の把握・制御で、すなわち、対象の装置の稼働を確保もしくは向上することによるショップからのアウトプット数の増大です。ジョブショップ毎のアウトプット数を把握できる仕組みの整備とともに責任者を設定して、「カイゼン」活動を推進するというものです。これは即ち、仕掛低減と生産量アップに繋がってくる活動です。
しかしながら、ジョブショップ毎の「カイゼン」が進んでも、製造ライン全体の革新には遠いものでした。そこで提案されたのが、数百ある半導体製造工程のフローを数十工程単位で区切り、あたかも数工程のグローラインの様に見立て、「トヨタ生産方式」の管理を行う試みです。区切られた数十工程を一つの仕掛棚と捉え、前後の棚とのインプット、アウトプットの動機を取っていこうという手法です。即ち、これをジャストインタイムで制御すべきという手法です。ジャストインタイムが達成されない場合、ライン全体としてこれに注目して、「カイゼン」を集中するというもので、ライン管理者にも分り易い、即ち、経営資源の投入判断が容易になるという活動です。しかしながら、半導体デバイスの種類は、数種類では無く、特にロジックを生産するラインでは、数百にも達するわけで、仕掛棚の設定がポイントです。同じような工程フローの製品を集めて、同じ仕掛棚に、想定上で集めて管理するのも手間が掛かります。
何れの改善活動でも最終的には、生産装置の健全な稼働の確保が重要であり、個別装置の稼働状況の把握、故障・異常の発生状況の分析、故障対策の立案・実行が重要であり、最終的には、このPDCAに修練されます。故障・異常の対応が行われていけば、装置の稼働状況も向上し、ライン全体として生産量の増大が期待できるわけで、将来予定されている増産への投資の抑制にも大きな効果を生み出すことになります。また、フローラインでもジョブショップによる複雑な生産方式でもボトルネックの製造装置を見出し、この稼働向上を図る必要性は同一であると言えます。
半導体製造装置の稼働状態の区分は、半導体製造の世界的な規格団体であるSEMIによりE10という規定で定められています。SEMI E10では、装置の状態を6つの基本的なカテゴリに分けて定義しています。
① 製品処理状態:装置が正常に動作し、生産を行っている状態。
② スタンバイ状態:装置が生産を待機している状態。
③ エンジニアリング状態:装置がテストやメンテナンスのために使用されている状態。
④ 計画内ダウンタイム状態:装置が予定された停止(例えば、定期的なメンテナンス)のために稼働していない状態。
⑤ 計画外ダウンタイム状態:装置が予期せぬ問題(例えば、故障)により稼働していない状態。この状態は、装置システムの「故障」状態と定義される。
⑥ 未計画状態:上記のいずれにも該当しない状態。
これらの状態は、装置の信頼性、可用性、保守性、利用性の性能を測定するための標準的な数値として利用され、生産現場と装置メーカー間の議論における共通の言語として共有されています。改善活動の進め方としては、6つのカテゴリの科学的な把握と、生産工学的なアプローチにより、総合的な稼働向上施策を実行し、ボトルネックの生産を拡大していく作業を実行しました。実際の生産現場での実効性は、この活動により確立したと信じています。何故なら、例えば、ボトルネックである生産装置の生産性が改善され、追加購入1台が不要となった場合、それだけで1台分数億の投資が削減される分けで、活動成果は絶大です。具体的な活動の方法は、次をご参照ください。
この記事が気に入ったらサポートをしてみませんか?