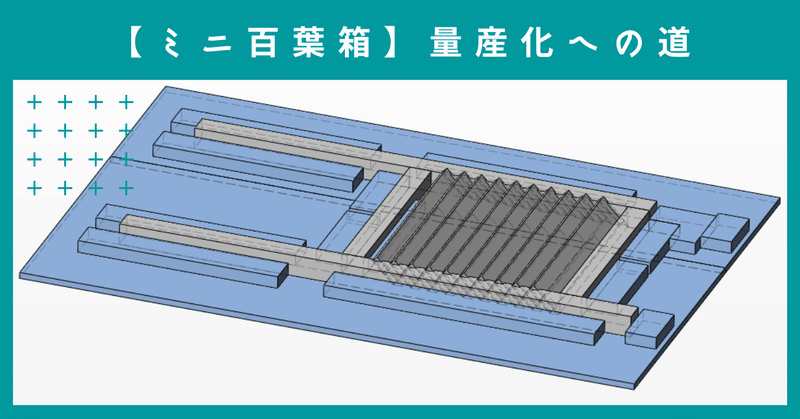
【ミニ百葉箱】量産化への道
工作がとにかく苦手で、でも大好きで、何とか上手くする方法はないか、いつも考えています。
前回、前々回の記事で何とか自分の満足できるレベルで素敵なミニ百葉箱が完成し、Switchbot温湿度計を保護する容器になっています。
前回の記事を書き上げて十分満足したので、一度ミニ百葉箱から離れて、自動水やり機の製作に戻ろうとあれこれ取り組み始めたのですが、テストで組んでみた装置が思った値を返してくれず、先が見えない状態になってきました。悩んでいても仕方がないので、部品を追加発注して試そうとしたところ、これがなかなか納期が長く、作業が一時中断となりました。
となると、気になるのはやはりミニ百葉箱です。
ミニ百葉箱をいくつか作って知り合いの方にお使いいただこうかと思いました。
前回作成時は、偶然うまくできたレベルの出来で、再現性がないと考えています。また、部品点数が多く、部品の切り出しがとても大変でした。前回の失敗を改善し、程度良くスマートに作るための方策を探っています。
前回の工作でうまくできなかった点は、
1.部品の長さが不揃いで、組立時に隙間が出る。
2.切断面が斜めで組み立て時に直角にならない。
3.ルーバーの組み立てにとても時間が掛かる。
4.部品点数が多い。
などです。
1.部品の長さが不揃いで、組立時に隙間が出る。
に対する対策を考えます。
長さが不揃いになるのは、材料を切断したあとの長さチェックをしていない。またはチェックをしていても、何もしていないためです。
私の悪い癖で、最初はあれこれ細かく考えるのですが、作り始めると細かいことはどうでもよくなってきて雑に作業を進めてしまいます。この丁寧さの欠如が原因であると考えます。
言うのは簡単ですが、やるのは難しいことです。
正直なところ「丁寧に作業をする。」こと自体が私にとっては無理なことかもしれません。このあたりが、器用不器用の差が出るところだと思います。
木材の切断には、カッターナイフ、クラフトのこを使用していました。
カッターナイフは落ち着いて切れば正確に切れますが、材料を押さえる手が痛くなってしまいます。
クラフトのこはどんどん切断できますが、切り口が荒いです。
作成工程を振り返ると、
1.長さを測って、鉛筆で罫書く。
2.線に沿って切る。
を行っています。
工程が2つあるということは誤差が2倍になっていることになります。
このあたりも改善できるとよいと思います。
2.切断面が斜めで組み立て時に直角にならない。
の対策とも合わせて考える必要があるのですが、
部品の長さを揃える。
切り口を直角にする。
を目指すことがとても大切なことに気づきました。
これを実現するために、あれこれ探した結果、ユニバーサルカッターにたどり着きました。
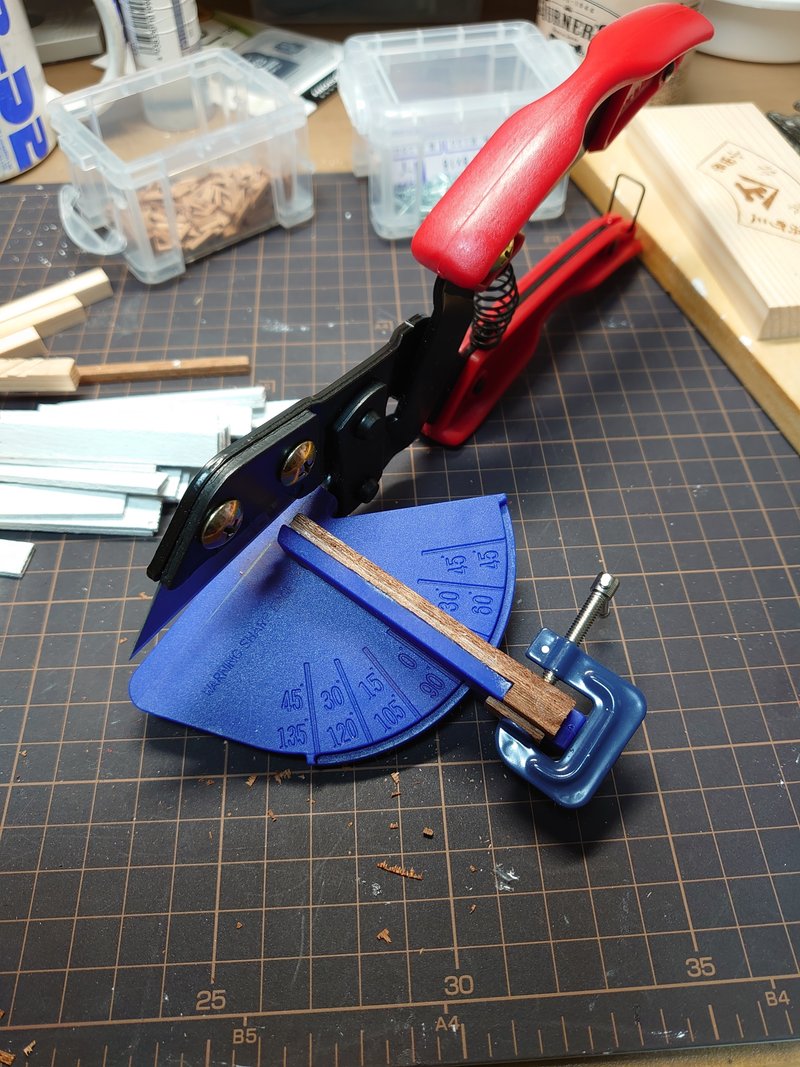
ルーバー部の10x2のマホガニー材を切断してみました。
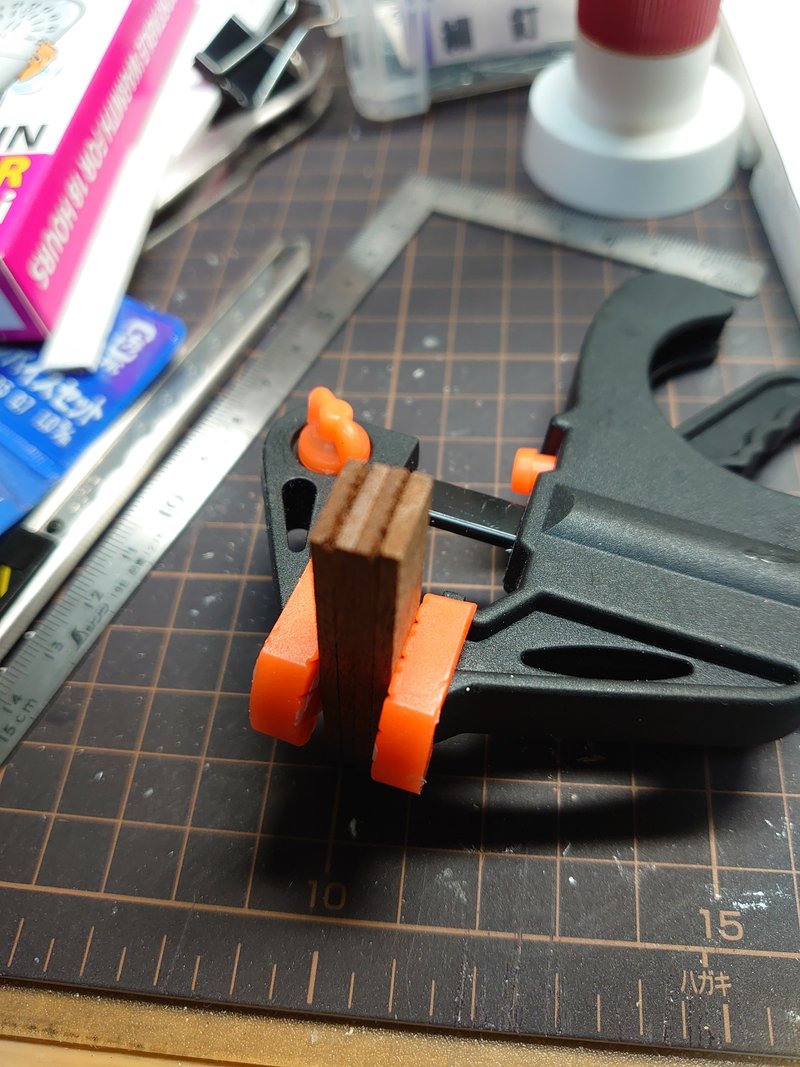
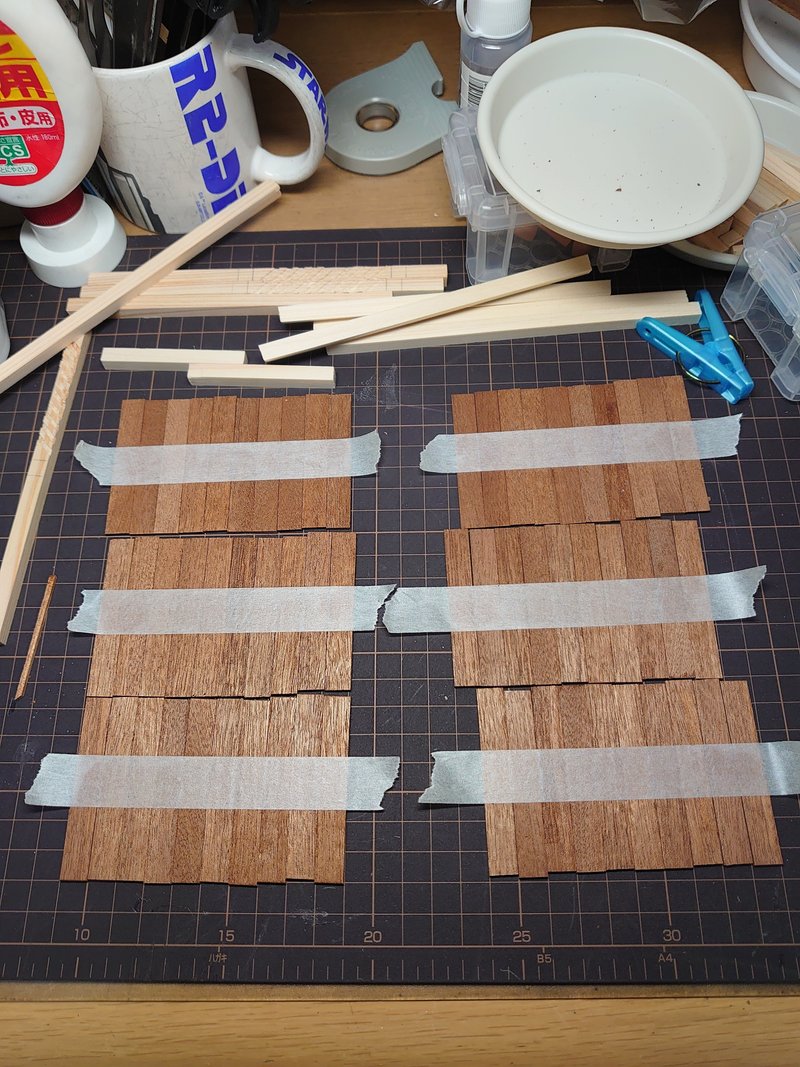
少しの力で切断でき、切り口も直角になりました。
切断面のバリが少し出て、きれいな木口にならなかったため、マスキングテープを巻いて切断してみましたが改善しなかったため、課題として残っています。ただ、十分実用レベルです。
長さを一定にするため、材料の長さを測るのではなく、ユニバーサルカッターに材料の付き当てをクリップで作りました。切断時に長さを決めるのは付き当てに材料を押し当てるだけで良くなりました。
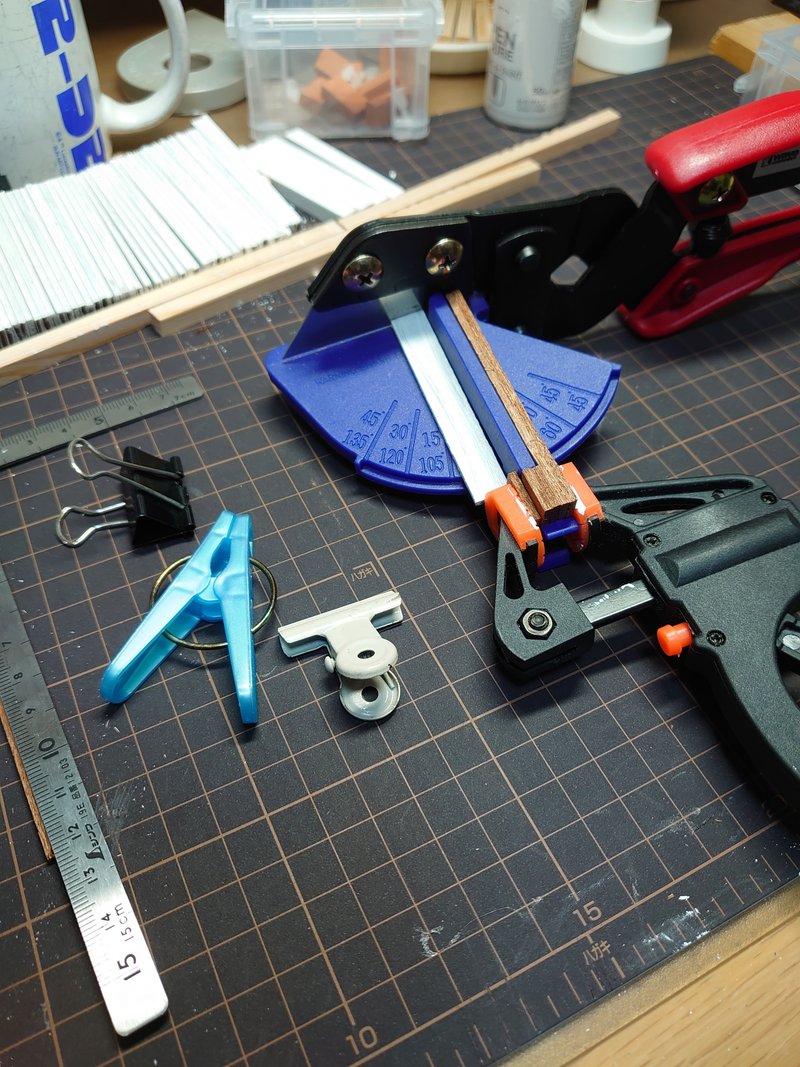
3.ルーバーの組み立てにとても時間が掛かる。
材料を固定して接着するための治具(ジグ)です。
部品同士が正しい場所で張り合わせできるようガイドします。
小ロットの部品の組み立てに、専用ラインを組まず、組立治具を用いる方法を仕事でよく見てきました。
ベーク、アルミ、フッ素樹脂などの加工しやすい材料を組み合わせて、治具を作っていました。
この手法を取り入れることで、不器用な私でも精度よく組み立てができるかもしれない。と期待が持てました。
さて、この組立治具をどうやって作るかで悩んでいました。工場では設計のためのCADもあるし製造のための工作機械もあり、必要な部品を簡単に正確に作ってしまうことができます。
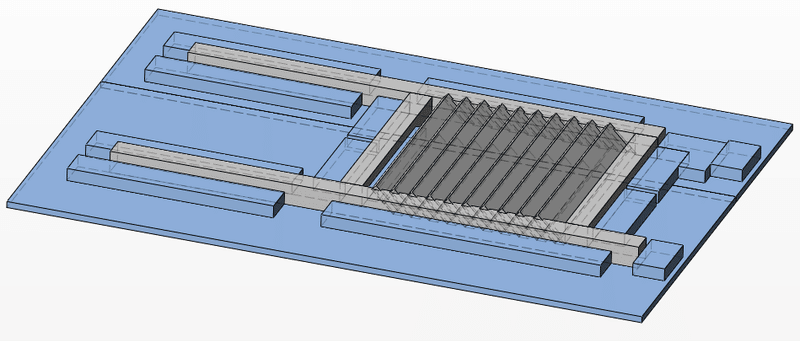
試しに思いつくまま組立治具を設計してみました。
ルーバーの斜め部分をサポートしながら、部品を組み合わせる事を考えた作りです。
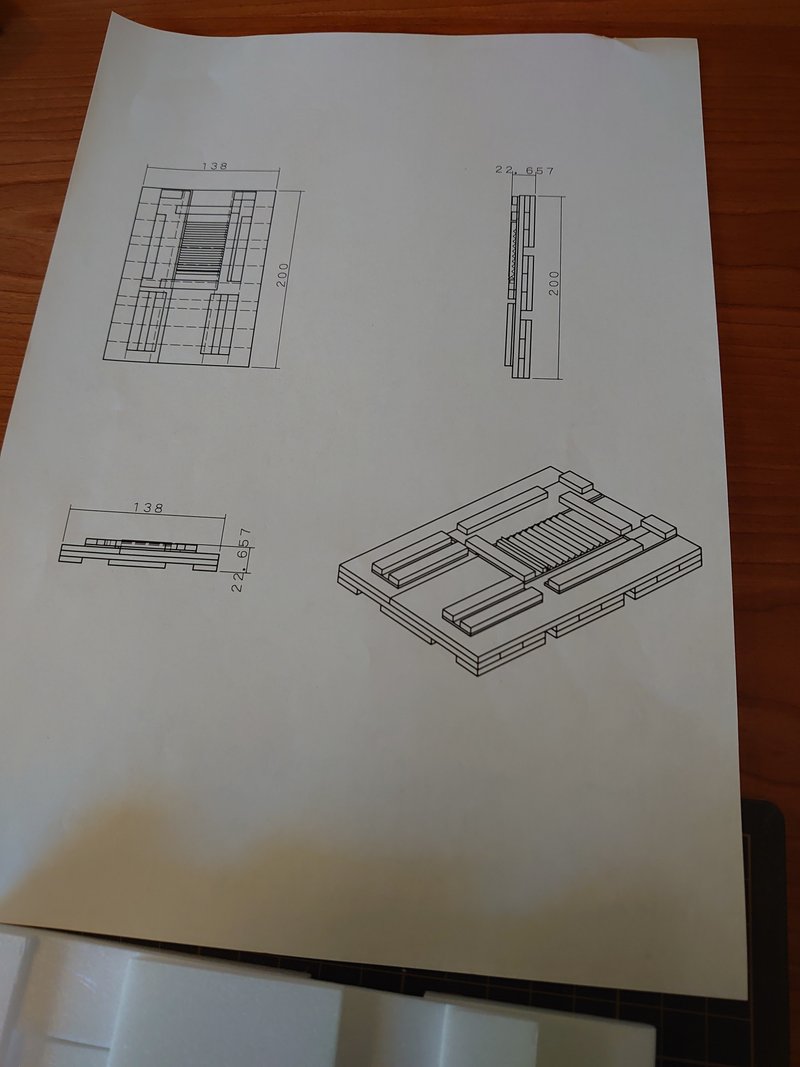
以前、治具用具メーカーの方に治具設計の勘所について教えていただいたことがありました。
3-2-1の法則(ナベヤ)
という考え方があるそうです。
例えば、z軸方向を固定するためには3点で支えると固定できます。次にx軸方向に固定するために2点で押さえると固定でき、最後にy軸方向に1点で固定する。
これが基本だそうです。
言われると理解できるのですが、いざ設計となると、点で固定することを忘れ、面で受けてしまいます。
組立治具を簡単に作るために、加工のしやすい素材を探していました。木材→プラスチック板→スチレンボードと進んでいきました。
木材は私にとってはまだ硬い材料です。どんな形の治具が必要なのかわからない状態で木材はまだ早いと思いました。
次にプラスチック板、通称プラ板が使えそうか考えます。模型売り場で色んなプラ板を見ていて、どれが良いか迷いました。厚い板だとしっかりするけど、切るのが大変そう。薄い板は重ねるうちに誤差が出そう。と考えてこちらも今回はパス。
ネットで模型づくりについて調べていくと、木材やプラ板だけでなく、スチレンボードを用いたものが使われていました。「スチレンボード」建築模型で使われるアレだ!
これは期待が持てます。見るからに切りやすそうです。
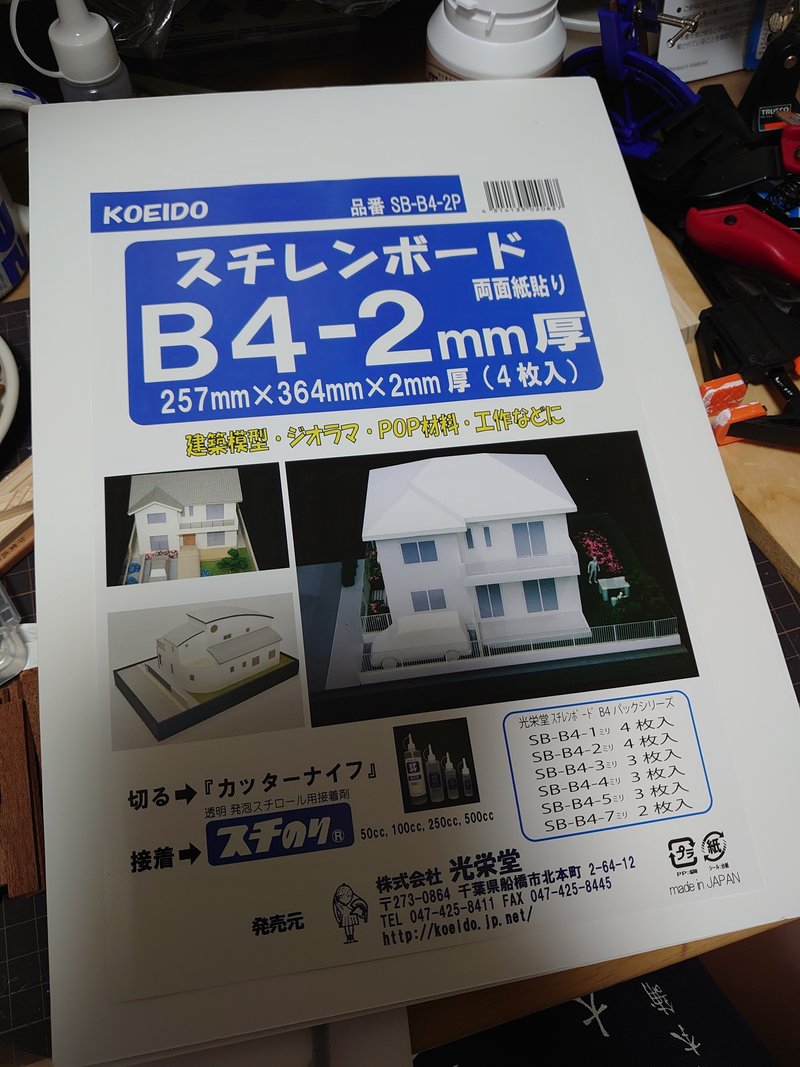
とりあえず試しに板厚2mmと5mmを試してみました。2mmのタイプは両面に紙が貼ってあります。
作り始めてスチレンボードがとても扱いやすいことがわかりました。図面を貼り付けてそのまま切っていくこともできます。
カッターナイフを力を抜いて何度か入れるだけできれいに切れます。
思い通りの形を作ることができるようになりました。
また、ルーバーを45度傾けて取り付ける必要があるため、三角形のプラ棒を並べて角度を出す工夫をしてみました。
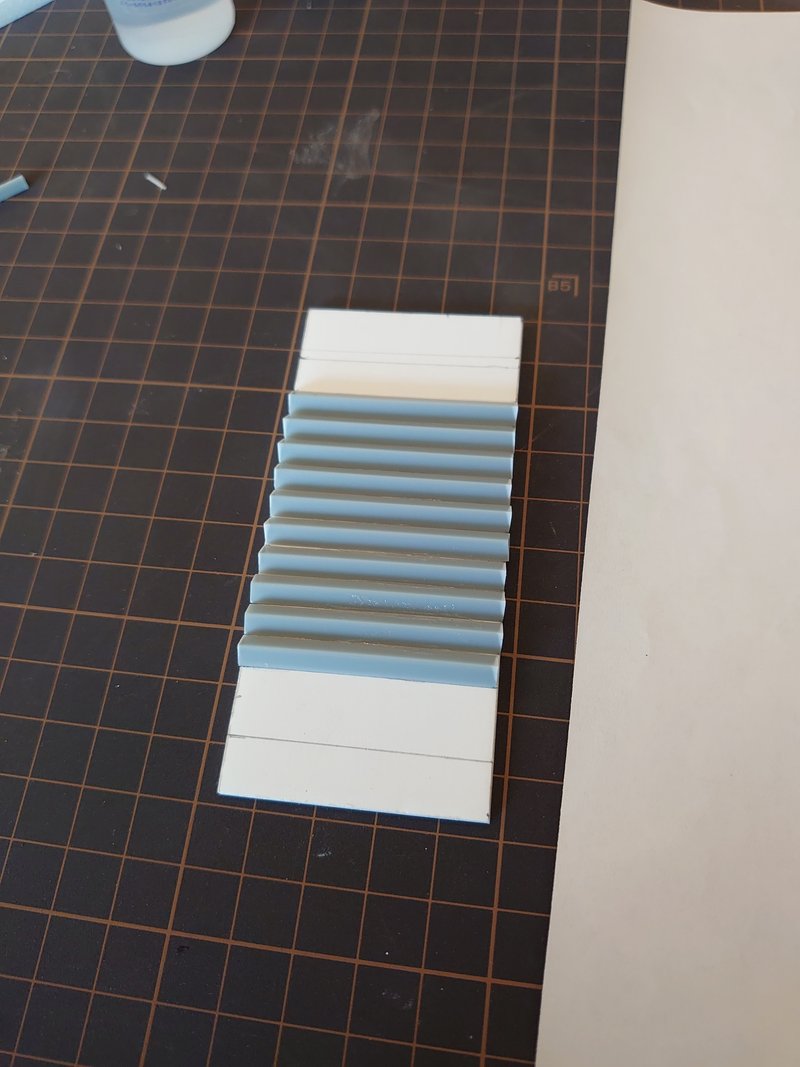
思い通りの形は作れますが、組立治具の形がなかなか見えてきません。
上から置く形にするのか、上下から挟み込む形にするのか、差し込む形にするのか。。。
よくわからないので、実際にミニ百葉箱を作りながら、必要に応じて治具も作る方針で臨みました。
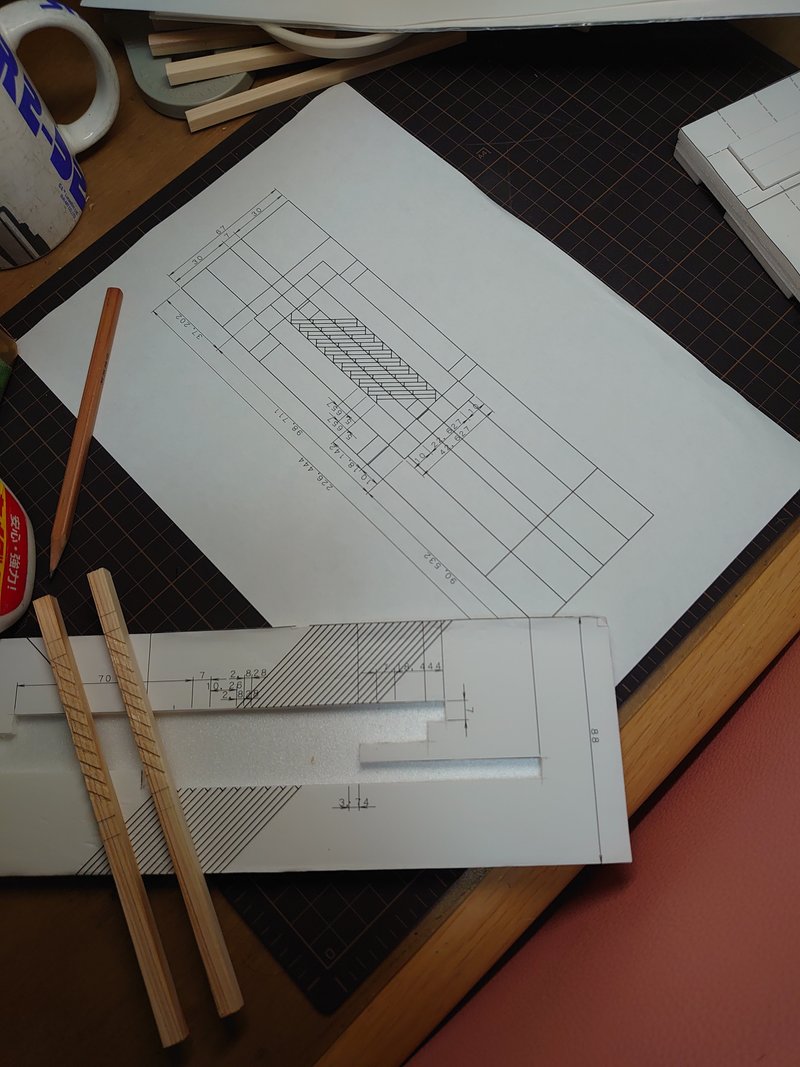
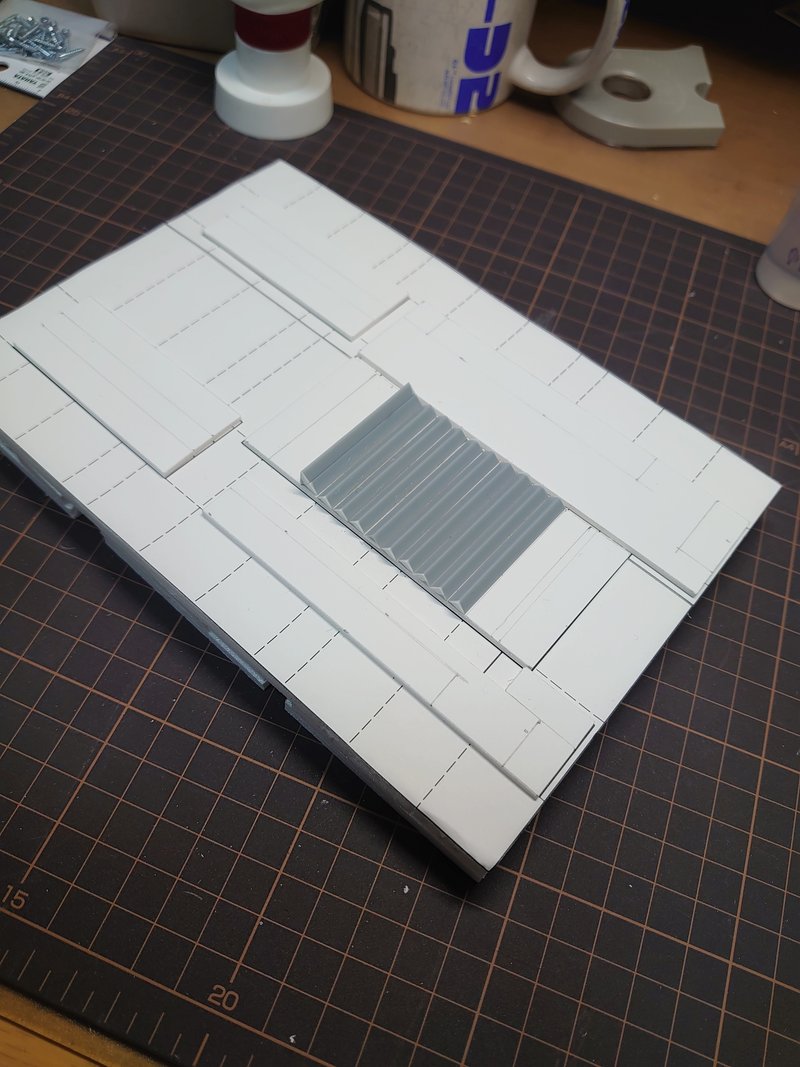
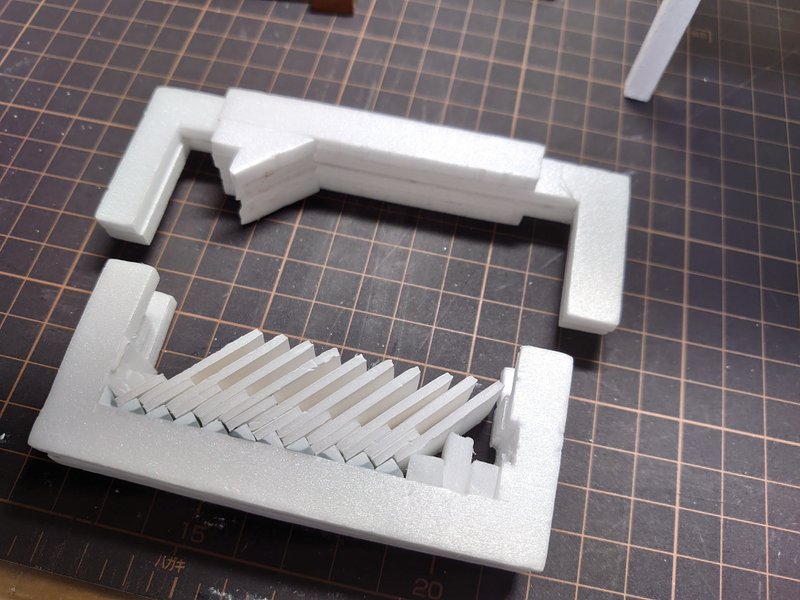
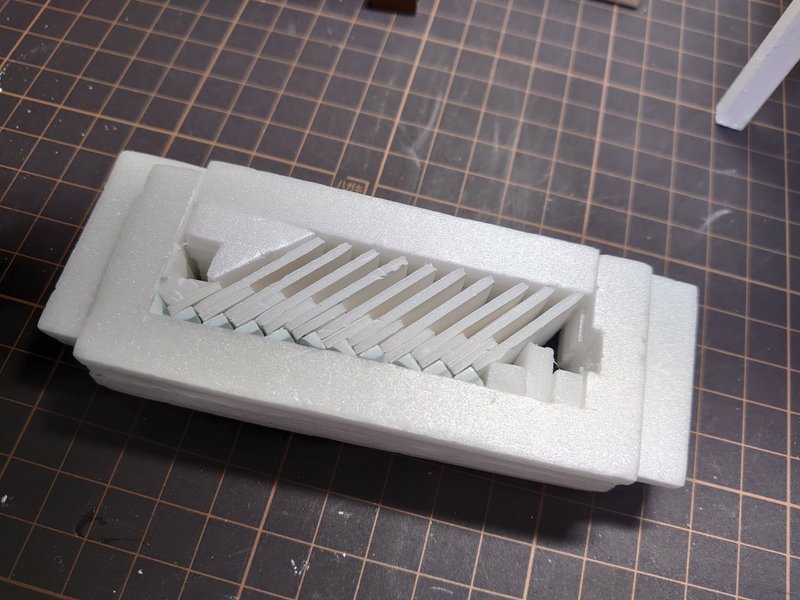
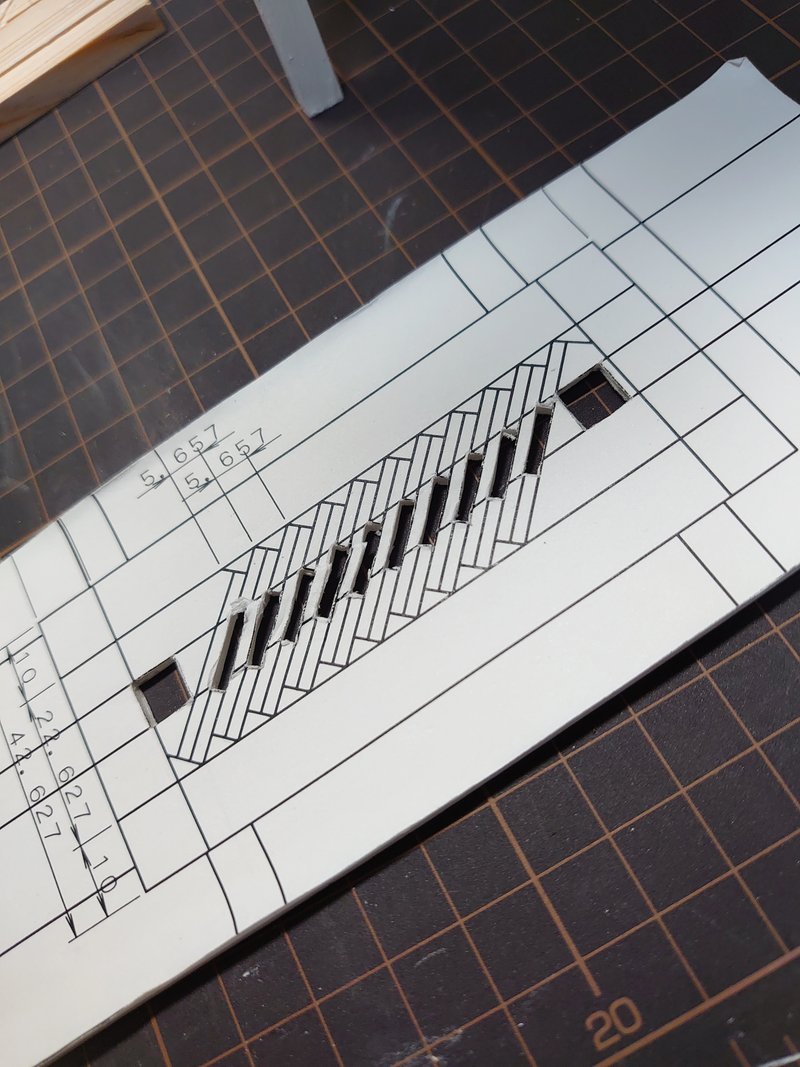
CADで設計した図面を原寸で打ち出し、スチレンボードに貼って、そのまま
切り出していきます。
4.部品点数が多い。
最初のプランでは、部品点数を削減するため、ルーバー部の支持角材□2をなくして、溝を彫り込むことにしました。
切り出しナイフや彫刻刀を持ち出して、溝切りします。
効率を考えて、4本一度に溝が彫れるように固定治具を作りました。
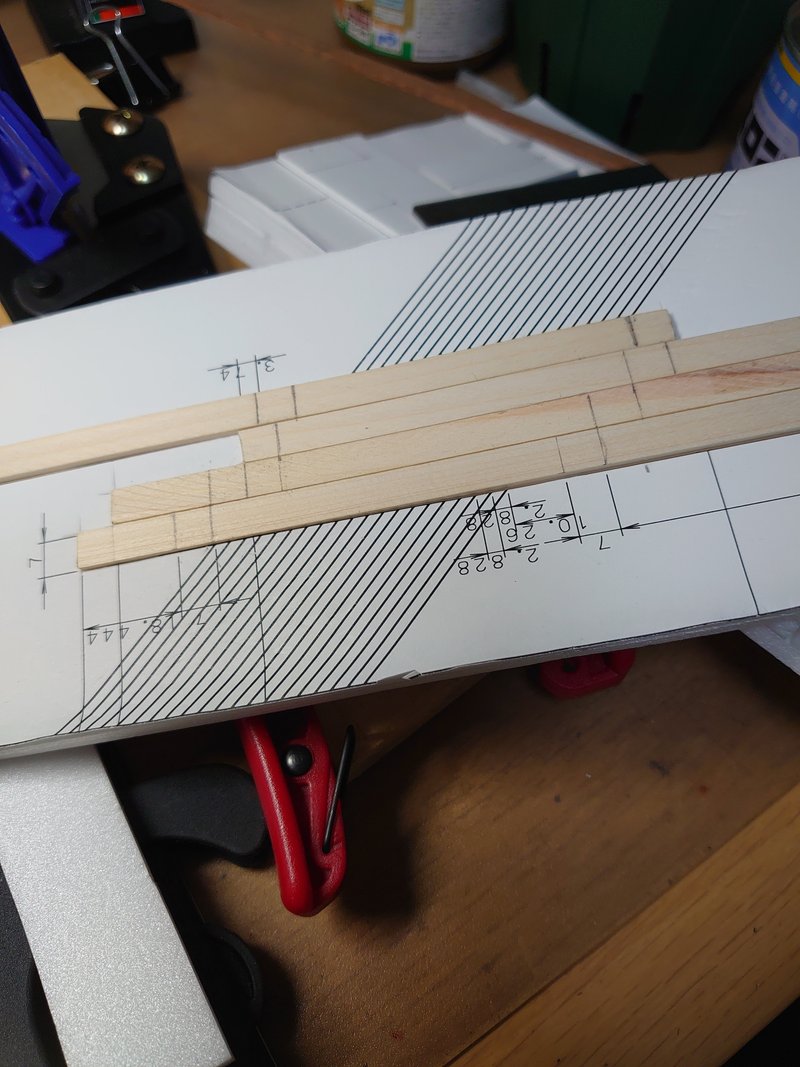
実はこの治具は正しくありません。
ミニ百葉箱でルーバーを取り付けるために必要な斜めさんは、
L=左下がり
R=右下がり
とすると、
左前:R
右前:L
左後:LR
右後:LR
となります。
なので、3本一度に彫れるような固定治具をL・R作る必要がありました。
上下をさかさまにしてもLR反転できず、そのままです。小学校で習う算数の点対称、線対称が解ってない感じです。
さらに、実際に彫りを始めてみると、力が要る上に失敗も多くうまい方法ではないことが分かりました。
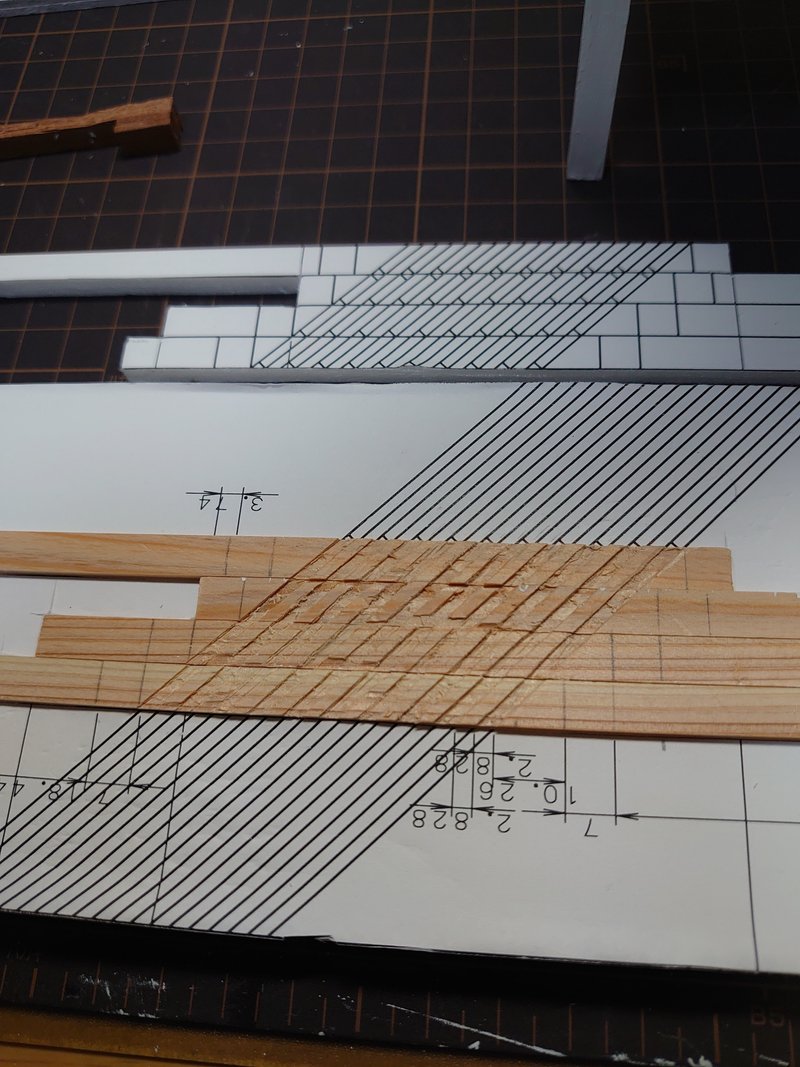
色を塗り始めて気が付いたのですが、ペンキに厚みがあるということです。素材のマホガニー材は厚さ2mmです。10枚重ねて厚さを測ると20mmでした。
ところがペンキを塗ったあと、10枚重ねると22mmになっています。
1枚あたりの厚さは2.2mmとなり、両面のペンキの厚さがあるので、0.1mmの被膜ができたことになります。
これまた当然と言えば当然なのですが、ペンキ厚を考慮しないで設計をしていたので、最大2mmのずれが生じます。治具の材料をスチレンボードにしていて正解だったと思いました。
ここで最初の目的に立ち返り、治具の目的を確認しました。
・部品同士の組み立て位置が定まること。
・組み立てが容易で正確になること。
実際に部品を組み立てながら使って見たところ、ルーバー部品を部分的に組み立てた状態で上に置くタイプの治具を使うと精度良く接着ができることがわかりました。
初号機は百葉箱の4本の柱にルーバーを支持するさん木を接着し最後の組み付け時にルーバーを差し込んでいました。ここまでの作業を一気に行っていたので、木工用ボンドが乾くまでの時間で微調整しながら何とかできていた感じです。
ただ一度にたくさんのことに気を付けながらの作業は、私にとってはとても難しく感じました。
もう少し工程をバラして工作できないか模索しました。
結局、私の取った方法はルーバー部を先に接着することです。ルーバーにさん木を貼り付けてそれを連結させて部品を作ります。細かな部品群を先に接着してしまうので、最後の組み立てが簡単になりました。
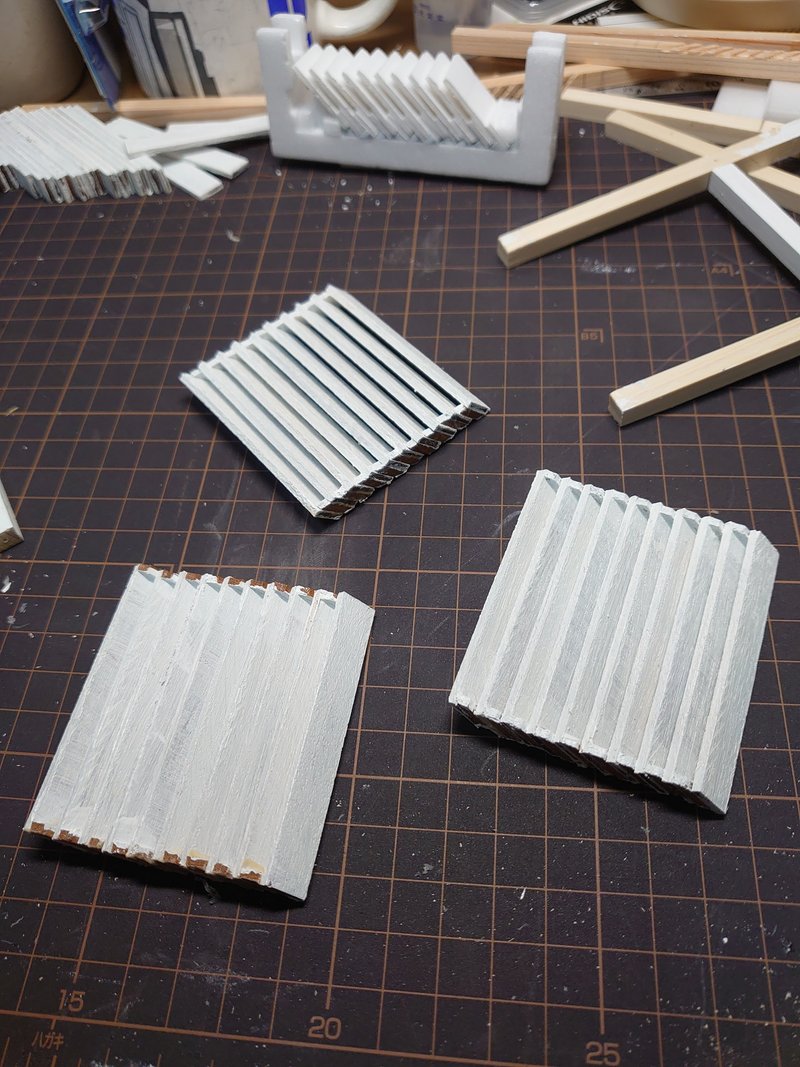
初号機は、本当に組み立てに苦労しました。この課題に対しての対策は「部品同士を釘留めすること」です。
ただ、釘の使用に関しては、今までの経験からできれば避けたい方法でした。理由は、木が割れてしまうからです。
細い木の端に釘を用いると、割り箸と同じで木が木目に沿って割れてしまいます。
これはどうしても避けたいことでした。
悩んだ結果、今回はあらかじめピンバイスで1mmの穴を開け、そこに0.8mmの釘を差し込む形を取りました。
釘はあくまでも位置決めのために用い、接合のために使わないことにしました。
木材の切り口も直角にまっすぐ切れたおかげで、ピンバイスもほぼほぼ狙いの場所に打ち込むことができました。
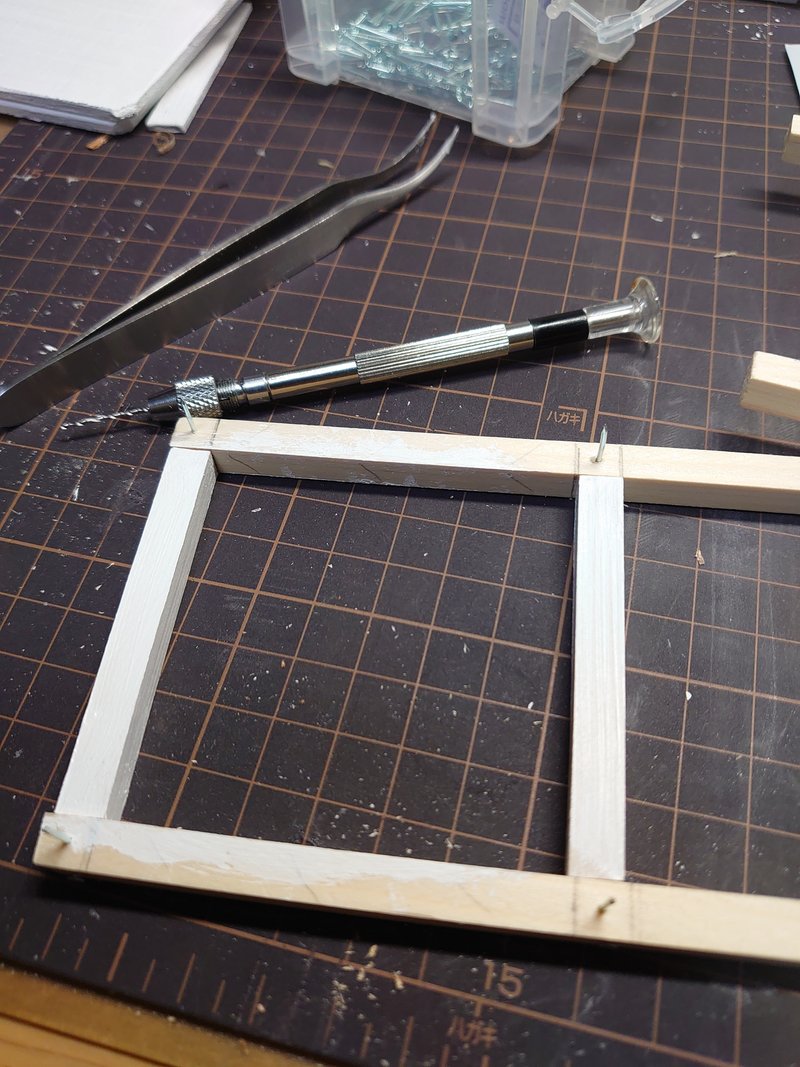
ただ今回も次への課題が見つかりました。4本の柱を横木を渡して組み立てるのですが、釘の穴あけ位置を少しずらしてやらないと、釘同士がぶつかってしまいます。また少し穴位置がずれているだけでも組み上がったときの出来栄えに影響することがわかりました。このことに対する対策が必要です。
もう一つ、ピンバイスで穴をあける時、垂直に開ける工夫が必要なようです。この部分がそのまま組み立て精度に影響します。
釘を固定のために使ったおかげで、骨組みだけで自立することができました。
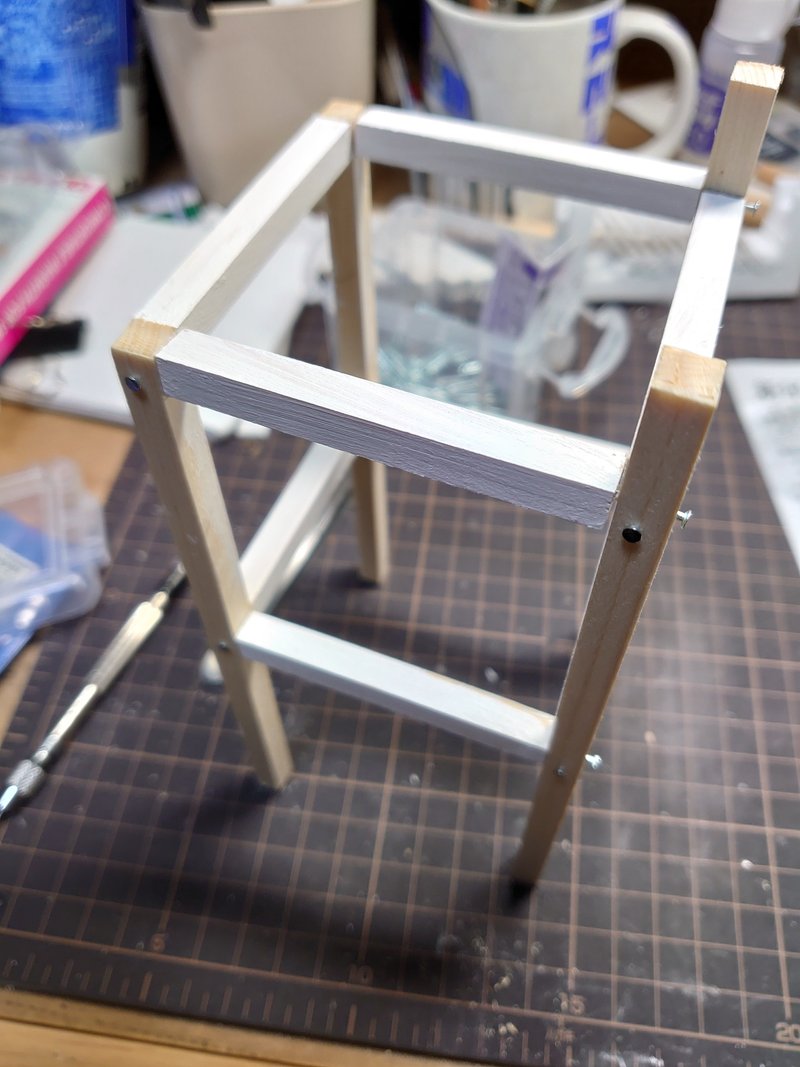
このような感じで、量産化への取り組みをはじめました。
実際の作成時間は計測していませんでしたが、まだまだ量産化には程遠いレベルです。
量産化というより、きれいに無理なく作りたい。
これが本当の目標です。
さいごに、ここまでの手法で作成した、試作2号機を紹介いたします。
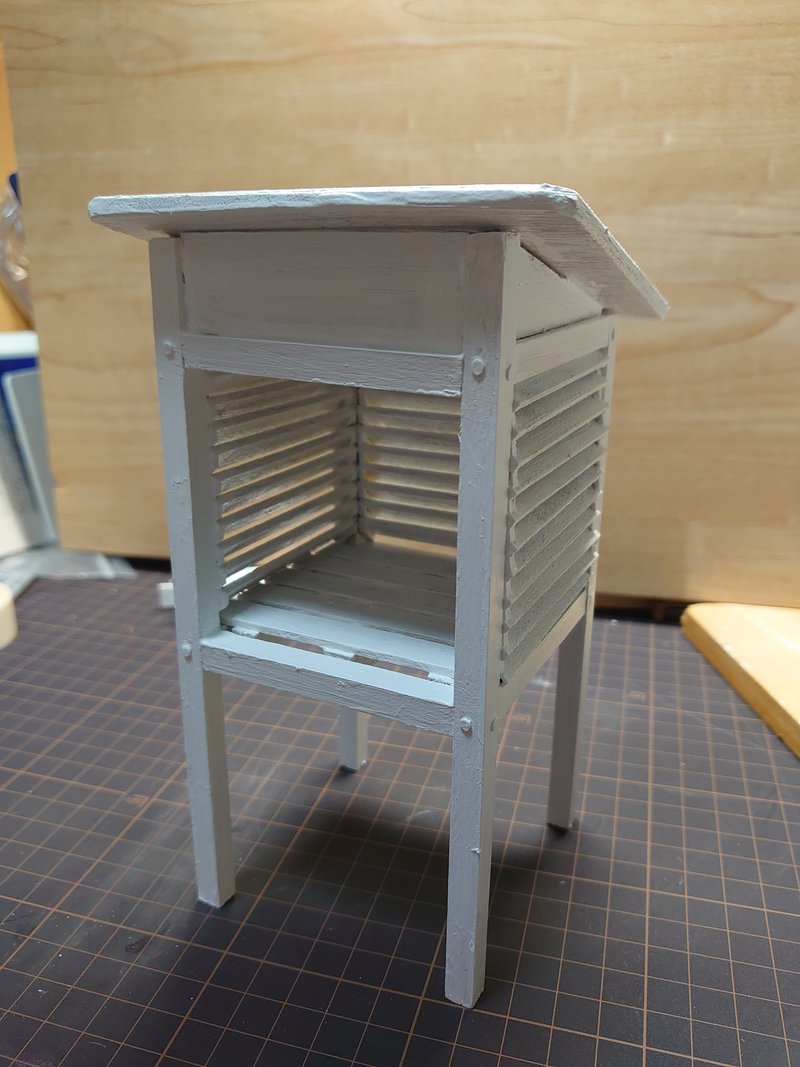
今回のチャレンジで今まであまり関心のなかった木工にも興味が湧いてきました。これからもミニ百葉箱を飽きるまで少しずつ手を入れながら作っていこうかと思います。
最後まお読みいただき誠にありがとうございました。
この記事が気に入ったらサポートをしてみませんか?