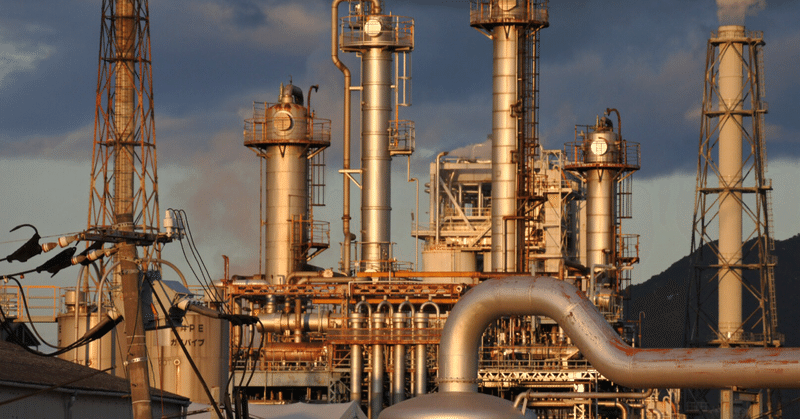
在庫とリードタイムの関係などを考えてみた
製造業では一般的に、なるべく少ない在庫がよいとされる。では適切な在庫量をどのように決めるか、をリードタイムの点から整理してみる。
まずは次の図のように、部材Aから製品Xをつくる工場を考える。製品リードタイム(製造LT)は3日とする。また製品Xの出荷数は一定とする。
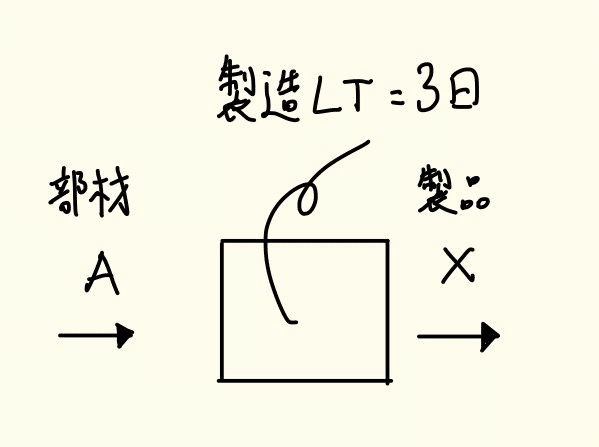
さて、この場合、工場内の仕掛在庫(加工中の部材A)はどのくらいの量になるだろうか。
答えは3日分(製品Xを3日間出荷できるだけの数量)だ。なぜなら、4日前に作り始めた分は、昨日完成し出荷ずみで工場にないが、3日前以降に作られた分は、今日以降に完成するので工場内にまだあるからだ。
つまり、仕掛在庫=製造LTとなる。
次に部材Aの在庫量を考える。発注してから納入されるまで1ヶ月かかるとする。(調達LT=1ヶ月)
このときの在庫量はいくらだろうか?
リードタイムに等しい分として、1ヶ月分必要だろうか?答えは納入頻度分だ。
1週間に1度、納入してくれるなら、今週使う分の在庫があればいい。来週使う分は来週持ってきてくれる。もっというと、すぐ持ってきてくれるなら、在庫は持たなくてもいいのだ。
トヨタ生産方式では、カンバンにより、不要な在庫を持たないようにしている。
ということは、調達に1ヶ月かかる部材も6ヶ月かかる部材も、納入頻度が同じなら同じ在庫量だけもっていればよいことになる。しかし、現実には調達に時間がかかる部材ほど、多く在庫を持つ傾向にある。なぜだろうか。
そう、それは製品Xの出荷数(部材A)が一定のではないからだ。未来になればなるほど、需要がわからなくなるため、部材Aの使用数量が確率的に変動するのだ。この変動から製造の流れを守るために必要なのが安全在庫となる。
安全在庫は次の場合に多くなる。
1. 調達にかかる時間+発注頻度が長い
2. 使用数量のばらつきが大きい
3. 発注者が欠品を心配しすぎる
さて、2. に着目すると、在庫をへらすには、使用数量のばらつきを抑える必要があることがわかる。つまりトヨタ生産方式でカンバンによる供給を実現するには、平準化生産が必要になるということだ。
次に3. に着目しよう。これは発注者が悪いというわけではない。欠品を責められるから在庫を持つようになるのだ。(そして、そういう工場では在庫が多すぎると責められる)
だから個人の判断ではなく、組織的な方針が必要となる。リーダーは欠品が起きたとき、単に個人を責めてはいけない。構造的に問題をとらえ、何が原因かをシンプルに考える必要があるのだ。
この記事が気に入ったらサポートをしてみませんか?