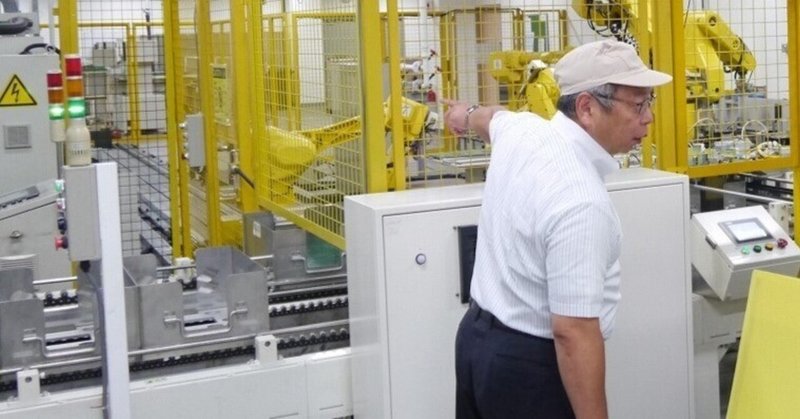
私の工場経営ノウハウ(17) 品質管理と品質保証
最近、大企業でも品質に関する問題が多く聞かれるようになりました。 その理由を考えてみると、終身雇用に問題があるのではないかと思えてくるのです。 1つの会社でしか働いたことがない、これがプロ意識の形成を邪魔しているのではないでしょうか。 一度会社を辞めた人が他社を歩いてまた戻ってくるのも良いと思いましたが、日本ではあまり聞かないですね。 仕事ぶりが、やらされ仕事になっていて、仕事の中身が浅くなっていないか気になります。 昭和から平成にかけての時代、愚直に、一つの仕事に打ち込んでいた技術者達が会社を去りました。 上司と喧嘩をしてでも思った通りに仕事を進め、時には失敗し反省する。 上司もそれも育成過程のプロセスと理解していた。 そんな昭和20年前後生まれの先輩方が職場を去ってから日本の、特にメーカーの技術者魂の炎が小さくなったような気がします。 その意味では技術の伝承がしっかりできていないことも要因と思います。
ここで、基本に戻って品質管理と品質保証の仕事について整理したいと思います。以下は、私の工場生活から得た考え方です。参考になればと記しました。
品質管理と品質保証の仕事
品質管理は社内向け、品質保証は社外向けの品質マネージメントを一般に指します。
品質管理は、設計仕様通りに製品が製造できているか、製造プロセスと出来栄えにフォーカスします。 品質保証は、売買契約書や納入仕様書、図面で約束した性能を守っているかにフォーカスします。 品質管理は製造部門が責任を持ち、品質保証は会社経営陣が責任を持ちます。 品質管理に問題があると会社経営に影響を与えますが、品質保証に問題があると社会に影響を与えます。 これらの考え方から品質管理と品質保証に関する対応も異なります。
1) 品質管理の仕事
品質管理ができる製品を投入させること、プロセス毎に製造条件と出来栄え確認を制御・管理できることが品質管理に必要です。すなわち、新図品・新規品に対してデザインレビュー(DR)を行うことで、工程能力が担保できる構造・材料・動作を公差を付けて設計し、正しい工程能力をもって加工して、設計仕様通りに完成したことを確認します。 この時、過去にトラブルがあれば、それを改善して設計仕様や図面、作業基準などが修正され、最新版管理していると思いますが、これも品質管理として重要な作業です。
設計支援ツールとしては、熱分布・応力・歪シミュレーション機能が付いた3D-CADなどがあります。 製造・検査ツールとしてはCAM、CATなどがあります。 これらのツールは業務効率を上げますが品質管理そのものには直接役には立ちません。 設計から製造、検査に至る業務フローを明確化し、これを守って活動します。業務フローや指示書、作業基準が間違っていたら、これらの基準類を修正し、その後基準類に従って作業をし、記録に残すことが基本動作になります。 この考え方はISO-9001 に通じます。設計に関しては業務フロー図(図1 「新図設計の品質管理プロセス」を参照)があり、製造・検査に関してはQC工程表と作業基準(図2 「QC工程表フォーマット」参照)があります。
品質管理の日々の作業としては、工程毎の検査・出来栄えチェックで管理の状況を確認すると同時に、最終検査の項目別不良率の変動で確認をします。 DR時の社内認定試験に合格した後、4M(Man, Material, Machine, Method)の変動によって不良は発生します。 量産品の製造で一定の不良率を肯定していれば、不良率の大幅変動は4M変動が原因となりますから、フィッシュボーン分析等で根本原因を調査し、対策していくことになります。
プロセスの途中で異常な不良率が発生した場合は、生産を止めて原因究明と対策をしますが、最終検査で発生した場合には、原因となった工程の推定と不良の波及範囲の確定を行い出荷を停止します。 万一、出荷されている場合には、品質保証担当に報告して共同で対策をします。
品質管理の中でも重要なのが継続的品質向上活動です。 週又は月に1回関係者で過去1週間又は1か月の不良発生とその原因・対策状況を議論しPDCAを回す活動です。このアウトプットとして、設計仕様、作業基準、QC工程表、検査基準などの改訂が行われます。 ここで関係者とは、設計、製造、品証を指しますが、工場長も出席して活動状況を確認し適切な指示を出すなどします。 特に、新規品は初期流動管理が大切なので、その状況をここで検証します。 以上の活動の総括として四半期又は1年に1回は経営陣に報告をします。ここで、設計、製造、品証は社会活動でいう立法、行政、司法になぞらえて三権分立が要求されます。 どこかの部門が強すぎて小さな不良やクレームを放置すると大きな品質事故を招きます。 これはハインリッヒの法則に従って発生します。 引いては品質保証問題につながるので、営業部門や経営陣は後から後悔しないよう品質管理活動にも目を向けて頂きたいです。
2) 品質保証の仕事
対外的な活動であるため保証の要否から入ります。 そのためには見積書や納入仕様書、提出図面が重要です。これらは一種の契約書なので、この内容を満たしていることが品質保証の内容となるためです。 無理のない仕様で見積書や納入仕様書を提出します。仕様はDRで工程能力が確保された状態で決められ、社内認定試験を合格したものを提出します。 品質保証の立場からは、社内認定条件として設計仕様に制限を加えることができます。
製造が開始されてからは、不良品を社外に流出させないことが仕事です。 最終検査結果から正常でないロットの出荷承認をしないことです。ロットアウトです。量産品の場合で納期の関係から出荷したければ全数全項目検査して良品を1つ1つ確認して出荷可否を判断します。 その判断基準の作成と運用が大切です。 原則として、1つでも仕様を満たさない項目があれば出荷はしませんが、顧客の承認があれば条件付きで出荷する場合もあります。 これは納期が重要で、不良項目が性能に影響しない擦り傷や色むらなどの場合があります。
客先で出荷した製品に不具合が発生した場合、品質保証担当は現物が不良かどうかの確認をします。この段階では「不良」ではないので「不具合」と言います。不具合品が納入仕様を満たしていないことが、品質保証担当によって確認できたら「不良品」となり、賠償対象となり得ます。 商法では受入時に顧客が発見できなくとも、6ヶ月以内であればメーカー側に瑕疵担保責任があるため賠償対象となります。賠償内容は売買契約等も踏まえて顧客と協議の上決定します。一般には金銭ではなく代替え品又は交換部品の納入等をメーカー側は希望します。 ちなみに、B to Cビジネスとして個人に販売された場合、民法が適用され瑕疵担保責任期間は1年間になります。
細かいポイントですが、納入仕様書の記述テクニックは重要です。 例えば、「傷なきこと」と記載した場合、目視で傷が無くても顕微鏡では「ある」となってしまいます。 板厚や穴径などは製法や測定方法、測定位置によって異なる値が出てしまいます。 従って、目視検査を前提にしていれば、「目視で」と記述します。 板厚や穴径などは図面に測定箇所と測定機器、測定条件を記載しておきます。 笑い話になりますが、アジアでは国によって標準視力が違っていて日本で外観OKでもフィリピンではNGになった経験がありました。 外観検査員の視力が「4.0」だったのです。結局、使用する拡大鏡の倍率を変えて調整しました。
賠償対策としては保険に入っておくのも品質保証担当の仕事です。但し、賠償支払いをすると保険掛け金が上がるので、不良賠償が少額の場合、保険を使わない選択も考慮します。 PL保険の場合、出荷した製品は保険対象ではなく、社外不良で損害を被った顧客の財産、顧客の完成品、最終製品の動作異常で怪我をした場合などに保険金が支払われます。 顧客の受入検査で発覚した場合はメーカーの損金として賠償金が支払われます。 賠償金額が大きい場合かつ長期に渡る場合、会計上のテクニックとして未払いを取ったり、決算処理方法に影響が出ますので経理と相談してください。
3) 共通の仕事
共通の仕事として、検査員の教育訓練と認定検査員の認定があります。 工程検査や最終検査は製造部門で行う場合、品質管理の責任となります。抜き取り検査や破壊検査を含む出荷前最終検査は品質保証の責任となります。 出荷許可は品質保証が行います。 もう一つの仕事にトレーサビリティがあります。 万一、不良や不具合が出荷前後に指摘された場合、波及範囲の確定は重要です。 トレーサビリティのできる仕掛け作りとその実行は非常に重要です。 これは自社工程だけでなく、購入材料など、サプライチェーン全体に及びます。受入検査担当や購買部門との協力体制の整備も大切です。
いずれにせよ、あらゆる機会をつかまえて品質管理や品質保証の担当者は関係する全ての部門とのコミュニケーションを良好に保つ必要があります。 DR会議や品質向上会議、不良対策ミーテングの常連、かつ報告者、質問者、提案者になってください。

図1 「新図設計の品質管理プロセス
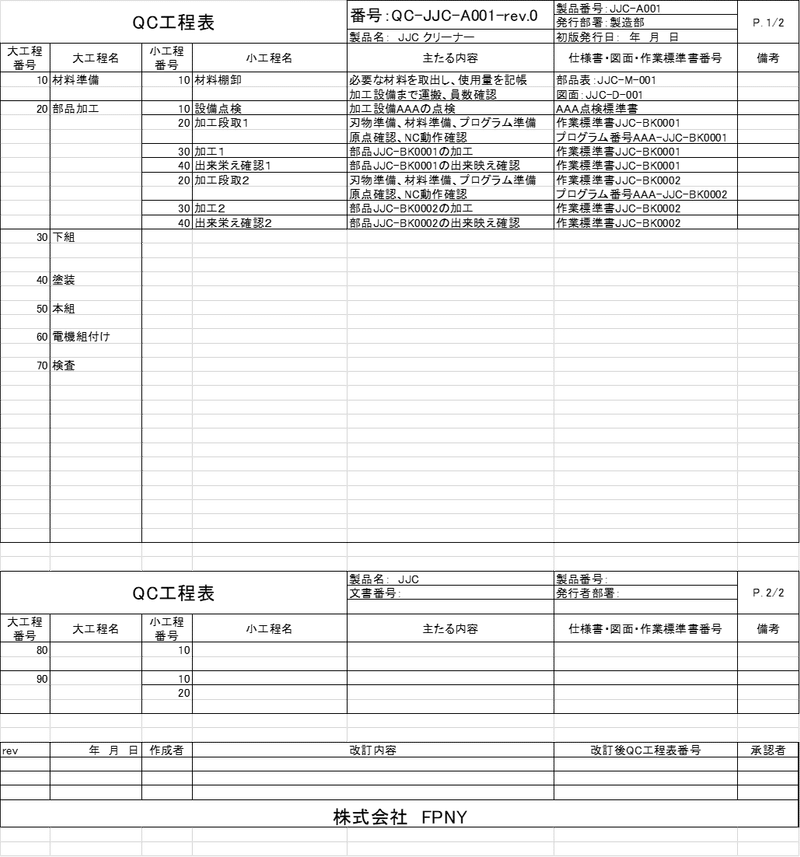
図2 QC工程表フォーマット
以上
この記事が気に入ったらサポートをしてみませんか?