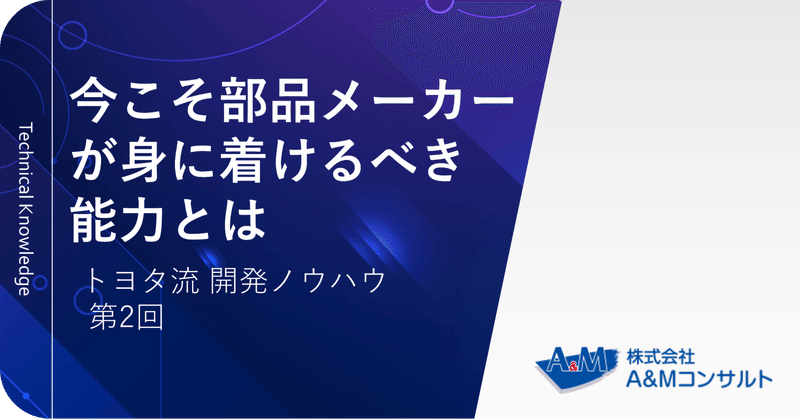
今こそ部品メーカーが身に着けるべき能力とは|トヨタ流開発ノウハウ 第2回
今の時代の様々な製品を見ていくと、単一機能の製品はほとんどなく、多くの機能を有し、さらに複雑な構造をしている製品が多くなっています。さらには、ハードウェアだけでなく、ソフトウェアが絡むとより一層複雑になっていっています。
その様々な機能を有している製品を1社のみで設計&製造している会社は少なく、製品メーカーと協力会社が一体となり、設計、製造しているのです(読者の皆さんにはすでに分かり切っていることだと思います)。
自動車は最たるものですね。自動車産業が創設された時から、すでに多くの協力会社と一緒に設計、製造をしてきました。そのような環境下で、協力会社のような部品メーカーの企業に話を聞く機会がありました。複数社、話を聞いていくと・・・。
「メーカーは製造のことが分かっていないので、むちゃな図面を描いてくるんですよ!これじゃ、どうやって金型を作れっていうんですかね?」
「今回はメーカーの若い設計者が担当なんですけど、図面が間違いだらけなんです。でも、検図印に上司のハンコも押してあるんです。これは全然見てもないし、教育もしてなさそうですね。」
「メーカーの新人の子が、「加工方法を教えてくれ!」って、よく来るんですよ。あのメーカーには加工のことがよくわかっているAさんがいるのに・・・。」
現在の日本の製造業の図面品質が落ちているのは、その通りのようです。このままほっておくと、モノ造りが出来ない図面が多く出図されてしまいます。
しかし、製造側にて対処できていることから、目立った問題が発生していないかもしれませんが、いずれ、製造側もベテランが引退していくと、いずれ、低い品質の図面でモノ造りをせざる得なくなり、結果、大きな不具合が発生してしまうことでしょう。
図面品質を向上させるために、メーカー側にも再度、図面に対する認識を改めてもらうと共に、図面の描き方、図面の整備が必要です。
上記の内容だけだと、いくらかの図面の品質は向上しますが、やはり、今問題となっている製造の内容を図面に反映することは難しいでしょう。
では、どのようにするべきか。「まさにその製造の内容を知っている人が図面に対して、フィードバックしてあげるべきですし、製造段階で発生する可能性がある問題点についても、対処の方法を考え設計者にフィードバックするべき」です。
私は、現在の図面品質のレベルがすべてメーカーにあると思ってはいません。製品の構造が複雑になり、より多くの協力会社と付き合っていかなくてはならなくなった結果、全ての検討内容を図面に反映させることは難しいですし、様々なメーカーと付き合うための時間も増加していることが原因と考えております。そのような状況で「完璧な、間違いのない美しい図面を出しなさい!」と指示するのは、設計担当者にとっては酷でしょう。
そのような状況のために、メーカーと協力会社が団結し、進めて行く必要があります。そのためには先ほど説明した「メーカーに提言できる能力」が必要になってきます。
モノ造りのことは、やはり現場が一番わかっていると、私は思っています。設計者がいくら知識をつけたとしても、現場のベテラン達にはかないません。(私も前職で製造現場のおっちゃんたちに怒られて育ちました。)
そんなベテラン達が協力し、モノ造り現場の意見をメーカーの設計に伝えていく。当たり前かもしれませんが、基本に立ち戻って実施していかなくてはなりません。
さらに「メーカーに提言できる能力」といっても、図面に朱書きして、提出すればいいわけではありません。より高度なモノ造り現場での内容を伝えていくのです。
その内容とは・・・。
『変化点管理+DRBFM』
だと考えます。
例えば、量産試作段階から協力会社に試作を依頼し、何度か試作を繰り返します。その何度か繰り返される試作というのは、製品機能に対しての問題点に対処するために変更を繰り返しています。その変化点を管理していますが、あくまでも製品機能に対しての変化点だけです。
本来は製造内容についての変化点についても管理しなければなりません。その製造方法の詳細内容を知っているのは、モノ造りの現場であり、部品メーカーです。製品機能の観点で変更されている内容が、製造現場の観点から考えたときに、その変更内容が最適かを検討していく必要があります。
製品機能を向上させようとすると、製造内容が複雑になって、加工しにくくなるなど、トレードオフの関係になることが多いです。その妥協点を見つけるためにも、製造としての「変化点管理」が必要になり、その変化点から問題点を抽出していく「DRBFM」も重要になってくるでしょう。
製造側の「変化点管理+DRBFM」をメーカー側で完璧に作成することは困難ですし、悩んで作成するぐらいであれば、プロである部品メーカーに作ってもらう方が精度も高く、的確な内容が抽出できるハズです。
これからの時代は、メーカーと部品メーカーが手を取り合って進めなければなりませんし、部品メーカーは、その部品の製造であれば、メーカーに意見を言わせないぐらいの力をつけて行かなければなりません。
また、「変化点管理+DRBFM」は多くの製品メーカーが導入していますが、正しく使うことが出来ている企業はごくわずかです。そのような状況の中、部品メーカーが完璧に「変化点管理+DRBFM」を活用し、製品メーカーに設計内容を提言することができれば、他社との大きな差別化を図ることが出来るようになります。
いかがでしょうか。私は、部品メーカーがあってこその製品メーカーだと考えておりますし、部品メーカーが今よりも力をつける事ができれば、さらに製品メーカーの力もついていくと考えております。ぜひ、実践してみてください!
この記事が気に入ったらサポートをしてみませんか?