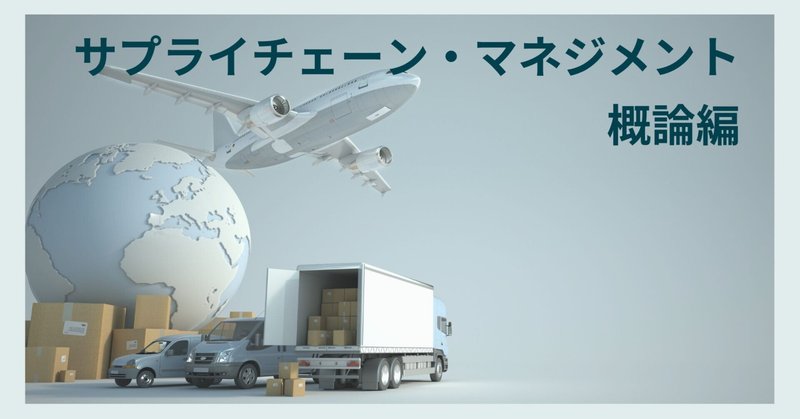
SCMと発注
サプライチェーンマネジメント(SCM)は、製品やサービスが生産者から最終消費者に至るまでの一連のプロセスを管理し、最適化することを目的としています。
SCMは、物流、在庫管理、需給予測、購買、生産計画、そして情報技術の活用など、多岐にわたる活動を含んでいます。
この記事では、SCMにおける発注の意思決定に必要な能力、需要予測の方法、定量発注と定期発注、リードタイムの種類、安全在庫の設定、そして経済的発注点(EOQ)に焦点を当てて詳しく解説します。
発注に必要な能力
サプライチェーンマネジメント(SCM)における発注の意思決定に必要な能力は多岐に渡ります。
発注プロセスは複雑であり、さまざまな要因を考慮して正確かつ迅速に行われる必要があります。
以下は、発注の意思決定において特に重要とされる能力の一部です。
市場と需要の理解: 市場の動向や顧客の需要を正確に把握し、予測する能力が必要です。これには、歴史的データの分析、トレンドの認識、そして将来の需要予測が含まれます。
データ分析能力: 大量のデータを効果的に分析し、意思決定に役立てる能力が求められます。SCMでは、在庫レベル、リードタイム、サプライヤーのパフォーマンス、製品のライフサイクルなど、多岐にわたるデータを扱います。
リスクマネジメント: 供給遅延、需要の変動、原材料の価格変動など、サプライチェーンに関わるリスクを識別し、対処する能力が求められます。リスクに対する適切な緩和策や代替計画の策定も重要です。
コミュニケーション能力: サプライヤー、製造部門、物流部門、販売部門など、サプライチェーン内の異なる関係者と効果的にコミュニケーションを取る能力が必要です。これにより、情報の共有が促進され、より良い意思決定が可能になります。
テクノロジーの活用: SCMシステムやERP(Enterprise Resource Planning)システムなど、最新の情報技術を活用して、効率的な発注プロセスを実現する能力が求められます。これには、システムの操作能力だけでなく、新しい技術の導入や改善提案の能力も含まれます。
戦略的思考: 発注の意思決定は、単に現在の需要に対応するだけではなく、長期的な視点で企業の戦略に沿ったものである必要があります。企業の目標や戦略と連携した発注計画の立案能力が重要です。
柔軟性と迅速な意思決定: 市場の変化に迅速に対応し、柔軟に計画を調整する能力。サプライチェーンは常に変動するため、状況の変化に応じて発注戦略を柔軟に変更する能力が求められます。
これらの能力は、SCMにおける効果的な発注の意思決定を行うために不可欠です。企業はこれらの能力を持つ人材を育成することで、サプライチェーンの効率化と競争力の強化を実現することができます。
需要予測の方法
需要予測は、将来の顧客の需要を予測し、サプライチェーンの効率性と効果性を高めるために非常に重要です。
効果的な需要予測は、在庫管理、生産計画、調達戦略、物流および配送戦略を最適化するのに役立ちます。以下では、需要予測の主な方法とその適用について詳しく説明します。
定量的予測法
時系列分析: 過去のデータパターンを分析して、将来の値を予測します。季節性、トレンド、周期性などの要素を考慮に入れます。
因果関係モデル: 需要に影響を与える外部変数(経済指標、市場のトレンド、価格変動など)を使用して予測を行います。
指数平滑法: 最近の観測値に重みをより多く置くことによって、過去のデータを滑らかにし、将来の需要を予測します。
定性的予測法
デルファイ法: 専門家の意見を集約して将来の需要を予測します。複数ラウンドにわたり意見を調整し、合意に達します。
市場調査: 顧客アンケートやフォーカスグループを通じて、顧客の意見や嗜好を直接収集し、需要を予測します。
組み合わせ法
複数の予測手法を組み合わせることで、より正確な予測を目指します。各手法の予測結果を重み付けして統合することが一般的です。
定量発注と定期発注
定量発注と定期発注は、在庫管理とサプライチェーンマネジメントにおける重要な発注方法です。これらの方法は、需要予測、在庫レベル、サプライチェーンの効率性、コスト削減などの観点から、どのように商品や原材料を発注するかを決定するために使用されます。
定量発注(Quantity-based Ordering)
定量発注は、特定の数量に基づいて商品や材料を発注する方法です。この方式では、在庫がある一定の再発注点(リオーダーポイント)に達すると、事前に決定された固定数量を発注します。定量発注の主な目的は、在庫レベルを最適化し、品切れを防ぎつつ過剰在庫を避けることにあります。
定期発注(Periodic Ordering)
定期発注は、定められた周期ごとに発注を行う方法です。この方式では、一定期間(例えば毎週、毎月)の終わりに在庫レベルを確認し、目標在庫レベルに達するように注文します。定期発注の主な目的は、発注プロセスを簡素化し、定期的なレビューを通じて在庫レベルを調整することにあります。
定量発注と定期発注の比較
柔軟性: 定期発注は発注量の柔軟性が高く、需要の変動に応じやすい。一方で定量発注は再発注点に達したときのみ発注するため、需要の予期せぬ変動に対応するのが難しい場合がある。
管理の複雑さ: 定量発注は管理が比較的シンプルで、在庫レベルが再発注点に達すると自動的に発注が行われる。定期発注では、定期的な在庫レビューが必要となり、管理が複雑になる可能性がある。
適用状況: 定量発注は安定した需要が見込める場合に適している。定期発注は需要が不規則で、周期的なレビューを通じて最新の需要予測に基づいて発注したい場合に適している。
それぞれの発注方法は、企業の特定のニーズやサプライチェーンの特性に応じて選択されます。
ABC分析を行い、重要なアイテムは定期発注、そうでないアイテムは定量発注など、カテゴリー分けをして運用するのが良いと思います。
リードタイムの種類
発注におけるリードタイムは、商品やサービスが注文されてから受領されるまでの時間を指します。
サプライチェーン管理において、リードタイムを理解し管理することは、在庫管理、生産計画、顧客満足度の向上などに重要な役割を果たします。
リードタイムにはいくつかの異なる種類があり、それぞれがサプライチェーンの異なる側面を反映しています。
1. 購入リードタイム(Procurement Lead Time)
定義: 購入リードタイムは、原材料や部品などの購入発注を行ってから、それらが受領されるまでの時間です。
構成要素: このリードタイムには、サプライヤー選定、発注処理、輸送、受領および検査までの時間が含まれます。
2. 製造リードタイム(Manufacturing Lead Time)
定義: 製品の製造を開始してから、製造プロセスが完了し出荷準備が整うまでの時間です。
構成要素: 材料の準備、製造または組み立て、検査、梱包などのプロセスが含まれます。
3. 納入リードタイム(Delivery Lead Time)
定義: 製品が出荷されてから顧客に届けられるまでの時間です。
構成要素: 輸送時間、通関処理、配送までの時間が含まれます。
4. 注文から納品までのリードタイム(Order-to-Delivery Lead Time)
定義: 顧客が注文を行ってから、最終製品が顧客に納品されるまでの総合的な時間です。
構成要素: このリードタイムには、購入リードタイム、製造リードタイム、納入リードタイムのすべてが含まれ、サプライチェーン全体を通じた時間を示します。
5. 再発注リードタイム(Reorder Lead Time)
定義: 在庫が再発注点に達したときから、補充された在庫が使用可能になるまでの時間です。
構成要素: 在庫の再発注処理時間、サプライヤーからの納品時間などが含まれます。
これらのリードタイムを適切に管理することは、生産計画の最適化、在庫コストの削減、顧客への納期遵守などに不可欠です。リードタイムの短縮は、競争優位性の向上にも寄与し、顧客満足度の高いサービスを提供するための鍵となります。
安全在庫の設定の仕方
安全在庫(セーフティストック)は、予測された需要の変動や供給遅延など、不確実性に対応するために保持する追加の在庫です。需要と供給の不確実性を考慮に入れ、品切れを防ぎつつ在庫コストを最小限に抑えるために重要な役割を果たします。
安全在庫はリードタイムの長さに比例して多く持つことが一般的です。
リードタイムが長い方が、より変動リスクが高いからです。
安全在庫の設定は、企業が直面する不確実性の度合い、在庫保持コスト、品切れによる機会損失のコストなど、多くの要因を考慮する必要があります。適切な安全在庫レベルの設定は、企業のサプライチェーンの効率性と顧客満足度の向上に貢献します。
経済的発注点について
経済的発注点(Economic Order Quantity, EOQ)は、在庫管理とサプライチェーン管理において、最小の総在庫コストを達成するために、一度に発注すべき最適な商品量を決定するためのモデルです。
このモデルは、発注コスト(商品を発注するたびに発生するコスト)と保持コスト(在庫を保管するためにかかるコスト)の合計が最小になる点を見つけることを目的としています。
EOQの計算式
EOQの基本的な計算式は
D:1年間の総需要量(単位:個)
S: は1回の発注にかかるコスト(単位:通貨)
H:1単位の商品を1年間保持するのにかかるコスト(単位:通貨/単位)
として
EOQ=√(2SD÷H)
で表せます。
なんとなくこういう式があることを覚えておくとよいかと思います。
EOQは静的な計算モデルであり、実際の需要の変動や供給遅延などのダイナミックな要素を直接的に考慮しません。
また、需要と単位あたりの発注コスト、保持コストが一定であるという前提に基づいています。
複数製品間の在庫管理の複雑さや相互作用を考慮しないなどの問題もありませんので、需要の変動やサプライチェーン全体の動きに柔軟に対応できるようなアプローチが求められます。
今回は、SCMにおける発注について取り上げました。
また今後もSCMに関する記事を書いていきますので、よろしくお願いいたします。
この記事が気に入ったらサポートをしてみませんか?