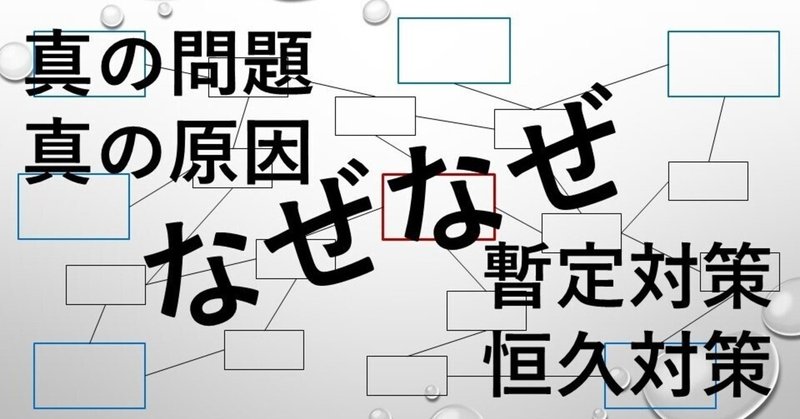
知っておきたい問題解決の正しい手順
問題(トラブル)発生に対する2つの活動として、未然防止と再発防止があります。
前者は問題が起こる前に対策し、
後者は問題が起きてから二度と起きないように対策します。
双方に共通する問題を解決するという行為は、皆様も日々実行していると思います。
問題解決に正しい手順があることはご存知ですか?
問題を確実に解決するためには、正しい手順を押さえておきましょう。
答を伝えると「なんだ、そんなの知っている」と言う方が多いですが、実際には、そのとおりに出来ていないケースが多いと感じています。
問題解決の正しい手順は、問題を定義し→真の原因を追究し→その原因に対する有効な対策を取ることです。
私は企業様の現場指導で、これを「問原対(もんげんたい)」とし、何度でも繰り返し伝えています。
先程は、出来ていない例が多い旨を記しましたが、先ず問題が曖昧なことが挙げられます。
そう感じた時は、「現場に行って、現物を使って説明してください」と私からお願いして問題をハッキリさせ、全員で共有してからスタートです。
次に、問題→対策の順番で解決しようとする、原因追究をしないパターンで、ベテラン社員に多い傾向があります。
「その問題ならば、こうすれば大丈夫だから」と。
それが当たる場合もありますが、当たる/当たらないでは無く、正しい問題解決に徹するべきで、それをしないと同じ問題が繰り返されます。
他に多いのは、原因追究はしていても、掘り下げが甘く、真因に至らず、過去と同じような対策をして、問題が再発するケース、更に、原因と対策が結び付いていないケースもあります。
原因追究が上手く進まない時には、主に2つの助言をします。
一つ目は、事実情報の列挙です。
問題解決の鉄則は3現主義(現場、現物、現実)であることを思い出し、事実情報を箇条書きで可視化してもらいます。(以下参照)
https://note.com/kid839/n/n9f9c37411981
原因が出せない原因は、想像や思い込みで進めることであり、事実に基づいた原因追究を勧めます。
この件に限りませんが、
仕事が上手く出来ない人ほど、無理な進め方をし、
仕事が出来る人ほど、原理原則に従った進め方をします。
二つ目に、なぜなぜ分析の提案をします。
トヨタ生産方式では「なぜなぜ5回」として、深く原因を追究することを教えていますが、真の原因に辿り着くまで何度でも行います。
私が勧める「なぜなぜ」分析は、「言い訳図法」という独自の手法で、問題解決の思考プロセスを全て可視化し、解決まで導きます。
「言い訳図法」の研修は、これまでに100回以上実施し、企業様の安全対策や品質活動に組み込まれ、実利に結び付いています。
1日~2日研修→職場実践→フォローアップ研修(実践内容の発表と講師助言)といった流れで、効果の刈り取りまで支援する、スキルアップ型実践的コースです。
ご参考までに研修一覧を添付します。
(添付ファイルパスワード kid2006pro)
次に対策には、暫定策と恒久策があることを押さえます。
例えば、怪我をした時に、看護士による応急処置は暫定策、専門医による縫合処置が恒久策です。
生産現場でよくあるケースとして、暫定策と思われる「目視確認」が恒久策として定着し、根本原因の対策が取られていないことです。
「目視確認」は漏出原因の対策なので、発生原因の対策が求められます。
暫定策で留まらず、確実に恒久策を取ることで、高品質な生産プロセスを構築しましょう。
ところで、今回多く触れた「問題」とは何でしょうか。
次回お付き合いください。
この記事が気に入ったらサポートをしてみませんか?