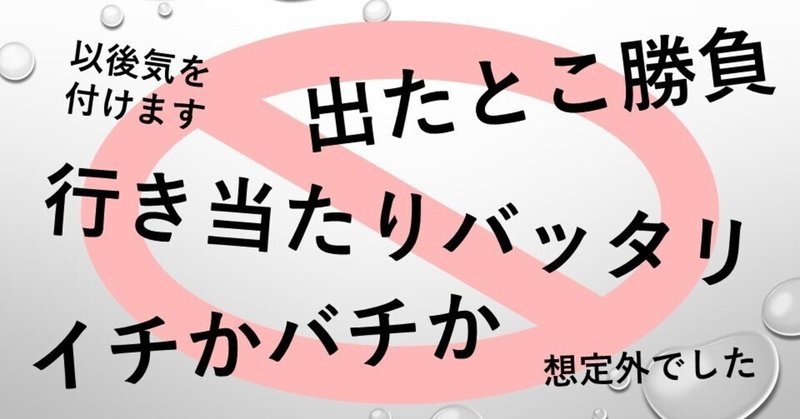
必要な品質コストと不要な品質コスト
不良が発生することで、いくら費用が掛かっているかご存知ですか?
以下を例に、自社の数値に変えて年間の費用を算出してみましょう。
不良が発生すると掛かる平均費用 10,000円/個(件数)
年間の不良個数(件数) 500個/年
年間の不良コスト 5,000,000円/年
但し、社内と社外(出荷後)で、費用が違う場合は分けて計算し、合算すればOKです。
仮に1年間不良がゼロならば、500万円の原価低減です。
不良が発生すると、どんな費用が掛かるか。
手直しの労務費、補修部品代、廃棄費用、再生産の費用、不良発生に伴う管理費用(労務費、交通費、通信費、手土産代など)。
これら全ては、不良ゼロならば0円でした。
尚、不良ゼロを実現したい場合は、以下を参照してください。
https://note.com/kid839/n/n5f165763f51b
ここ迄は不良コストのお話でしたが、他に2つのコストがあり、今回は3つの品質コストがあることを押さえます。
1.不良コスト 不良発生により発生した全ての費用
2.予防コスト 不良発生を防ぐために使う費用
3.評価コスト できばえを確認&検証するための費用
これらは、少ないほど良いとも言えますが、5Sの整理「必要なモノと、不要なモノを分ける」を思い出し、「必要な品質コストと、不要な品質コストを分ける」と良いでしょう。
「必要な品質コスト」は掛け、「不要な品質コスト」は減らします。
従って、短期間だけを見て費用を掛けないことが良いのではなく、1年とか3年、5年、10年といったトータルで費用を抑えるという考え方です。
具体的には、不良コスト(失敗コストとも言われる)を下げるために、どのように予防コストと評価コストを使うか、ということになります。
経済性の計算はこうなりますが、経営の最前線では生産3原則QDC
https://note.com/kid839/n/nb2100db8b32a
を思い出し、顧客に良い品質の商品を届けることが大前提です。
つまり、良いモノを造るために、どの様に予防コストと評価コストを掛けるかがポイントになります。
ここ迄をまとめます。
・品質が悪いと顧客の評価が下がるだけではなく、不良コストが掛かり、経営を圧迫する
・更に、不良コストを下げるためには、予防管理をしますが、そこにはコスト(予防コストと評価コスト)が掛かる
・不良コストをゼロに近づけるために、必要な予防コストと評価コストを掛け、トータルの費用を抑える
これまでは費用の話が中心でしたが、予防管理をしないと、現場で働く社員に何が起きるのかを考察するので、お付き合いください。
予防管理をしないと品質トラブル(不良)が発生し、最悪の場合は購入者(取引先/消費者)から品質クレームが来て、対応を迫られます。
これは、突発的に発生するトラブルです。
この状況を好む社員は存在せず、これに対応することは、誰にとっても嫌な仕事です。
これが続くと、社員はどう思い、何を考えるか。
仕事が辛い、つまらない、ヤリガイを感じない、逃げたい、辞めたい。
これは健全な姿ではなく、この状況を打破する、またはこの様にならないように解決すべきでしょう。
経営活動で「突発的」というのは非常に厄介で、できるだけ無くすことが安定経営に結び付きます。
つまり、できることならば計画的に業務を遂行し、事前に予算を組み、計算通りの経営をしたいものです。
突発的よりも計画的且つ安定的
緊急対応よりも平準的な対応
従って、社員の労働意欲だけではなく、安定経営を阻害するという、質が悪いのが突発的品質トラブルなので、以下のスタイルは捨てましょう。
「出たとこ勝負」「行き当たりバッタリ」「イチかバチか」
そのために、そもそも品質トラブルが起きないように、予防管理を強化する必要があるのです。
更に、そのためには品質トラブルを予測し、対策し、回避できる技術が求められます。
仮にスグには結果が伴わなくても、方向性が大事です。
《正しい結果=正しい思考✕正しい行動》を思い出し、たとえ時間が掛かっても正しいことを貫きましょう。
この記事が気に入ったらサポートをしてみませんか?