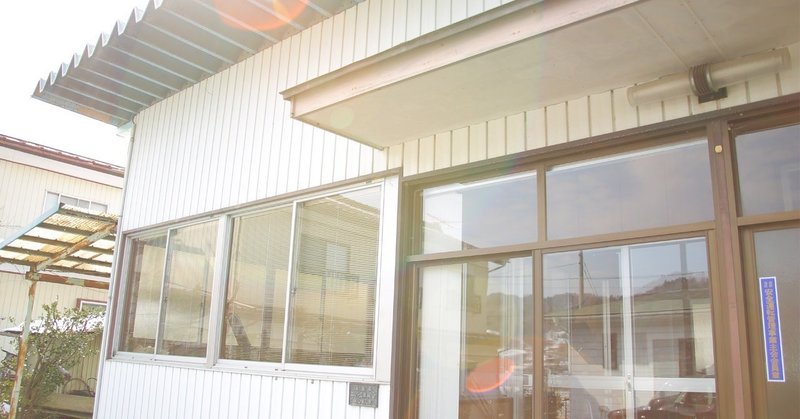
渾身の一着にたどり着くまで
こんにちはKNITOLOGYの山口です。。
さて、今回は今から7年前にニットコート開発に取り組み始めた頃のお話です。
阿部ニットさんにご協力いただき、いざ製品開発と思ったわけですが
本当に1型目のニットコートの製品開発は苦労が多かったようです、、
なんと言っても1年かかっていますからね、、途方も無い。
実際に鬼久保はニットに関しての勉強はしていたとはいえ、
当時、機械での操作に関しては素人。
逆に、阿部ニットさんも鬼久保が作りたいと思うような製品を開発しようとしたことが今まで一度も無く、
まさに手探り状態からのスタートでした。
まずは「何を作るのか。。。」
そこでまず 一番稼働していない12GGの機械を使って製品づくりをすることを決めました。
そうすれば、阿部ニットさんの請け負っている仕事を邪魔することがなく、工場全体の生産量を増やせると考えたからです。
次に「編み目の細かい生地を使って何を作ろうか。。。」
シーズンに関係なく毎年、オールシーズン使ってもらえるもの。
白衣のようなワークコートをつくろう!!
と思いつき、ここからパターンなどのデザインに入りますが、
ここのお話は話すと長くなるので、また追々ご紹介していきます。
いざニット機を使って制作をスタート!
糸を見て、良い!と思った糸で編んでみると、
全然綺麗じゃない。。。
そこからシルク、コットンや化繊など何十種類ものサンプルを編み試し、やっと一つの素材にたどり着きました。
ワークラインに関しては、この初期段階でたどり着いた素材で様々なアイテムを作り続けていますが、
今の素材は扱いやすくニットなのに張りがあって、目面も美しい
私が2年前に入社して以来、新製品のサンプルができる度に
様々な試し編みをして考えられた極上の素材なのだなと、
本当に感動を覚えます。
そんな万能な素材にたどり着くのに、まず多くの時間を要しました。
それでも、まだまだ製品のクオリティが完成までいきません。
工場のお仕事の合間を見て、編み試作をお願いしていました。
阿部ニットさんには、KNITOLOGYのプロジェクトよりも大事な生産のお仕事がたくさんあります。
まだ、生産の見通しも販路も開拓できていなかったKNITOLOGYに時間を割くことはとても大変なことだったと思います。
忙しい現場の合間を縫って、サンプル製作をしていただくわけですが、
それは失敗、、、失敗、、、の連続でした。
ニット製品を作るのはそんなに大変なの?と疑問に思うかもしれません。
形通りのデータを作って、機械をポチッと押せば良いだけじゃないの?と。
はい、私もKNITOLOGYに入るまでそう思っていました。。
複雑な曲線を描くパーツを編むのはとても難しく、傷や機械の故障が頻発します。
編み上がっても、乱寸という問題があり、パターンぴったりの寸法に仕上がりません。
同じ機械なのに毎回寸法が違う、違う機械で編むと寸法が違う、編む季節が違うと寸法が違う
スチームをかける人が変わると寸法が変わる、、、
などなど、一定の寸法に仕上がらない問題を解決するのに何ヶ月も費やしました。
KNITOLOGYのニットはパターンをこだわっているためパーツ数が多く
全てのパーツが完成する時には既に1年が経っていました。
その間、鬼久保は数え切れないほどの回数工場に通い、
途方も無い失敗を繰り返し、製品化までたどり着きました。
生産の段階でも通常のニット製品の制作の10倍ぐらいの手間がかかっているため、
KNITOLOGYと同じような仕様で製品を作って欲しい!!
とデザイナーが工場にお願いしても確実に断られるような仕様になっているのです。
当時はCADでのデータ作りや、編機の機械操作も全くできなかったため、
開発の中で、CADや機械の操作も根気よく鬼久保に教えてくださったそうです。
忙しい生産を抱えている状態の中でも、ブランドの製品開発をサポートしていただいたことには感謝しかなく、
私が鬼久保にブランドを始めた頃の話を聞くと、苦労エピソードと共に「ブランドとして阿部さんたちに恩返していくことが、まず一番」といつも言っています。
そんなたくさんの試作と、失敗、研究改良の日々を経て、
阿部ニットとKNITOLOGYによる渾身の一着、「ニットコート」が出来上がったのです。
この記事が気に入ったらサポートをしてみませんか?