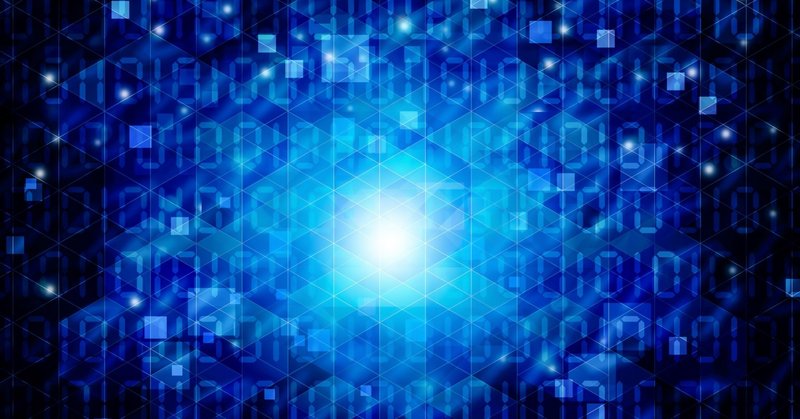
改善していない企業はデジタル化もムリ
こんにちは!中小製造業応援団のたつみです。
デジタルトランスフォーメーションがこれからの企業の存続・発展に大きく影響するこのご時世、準備はどのぐらいできていますか?何でもかんでもデジタル化すればいいというものではないですが、デジタルトランスフォーメーションが進んでいる企業とそうでない企業の生存確率は明らかに変わってくることが想像されます。デジタルトランスフォーメーションってツールなどを考えると難しいですが、準備として必要なことは日々の改善です。
結論を先に書くと「とにかくガンガン改善を進めましょう」です。デジタルトランスフォーメーションにも影響するので進めない理由はないです、ということを今回はざっくり解説します。
デジタルトランスフォーメーションのイメージ
超フレシキブル生産体制
多品種少量生産が主流になって久しいですが、さらに状況に応じた生産の変更が頻繁に行われることが多くなり、さらにさらにコロナ禍への対応で顧客の業種や製品構成まで変える必要が出てきました。
この短期的中期的にコロコロ生産を変動して状況に対応するためには、超フレシキブル生産体制が必要です。変更対応はムダですし、多品種少量生産は効率を落としますが、事業環境が求めている限り対応するしかないです。それを避けるにはiPhoneのように一国ではなくグローバルで大量の製品を売ることを考えなければなりません。
この超フレシキブル生産体制を実現するには、生産の計画・実行管理を超スピードで行うようシステム化されていることが重要となってきます。生産管理システムやMES(Manufacturing Execution System:製造実行管理システム)と関連システムが連携して機能していれば、なおいいですね。
<生産計画・実行管理がシステム化され、関連システムと連携できているメリット>
・注文の変更は自動的に製造予定に反映される
・顧客への納期回答も即答できる
・設備の制御とMESが連動していれば、人が手を加えなくても勝手に製造順序が変わる
・CAMと連動していれば、図面データを設備設定に反映できるので設定も不要
逆の見方をすると、これを全部人がやっていたら変化への対応スピードに時間がかかることは容易に想像できます。ある会社では受注担当1人と製造担当2人がなんと毎日1~2時間生産変更対応していました。今日反映した内容を翌日には見直しているので、無限にやり続けています。解けないパズルを永遠に繰り返しているようで終わりが見えない生産変更です。
エンジニアリング力のレベルアップ
研究開発ではデータで実証するのは当然ですが、その分析をAIを活用することが考えられます。また製品企画では市場や顧客に関する情報を分析する、設計データを蓄積・分析する、といった分析で主にデジタル化は有効です。毎回エクセルでデータを入力して分析し、結果を個人フォルダに保存するのではなく、データを連係して自動入力され、結果はいつでも取り出したりAIで分析できるようになってるとエンジニアリングのスピードは圧倒的に上がります。
また、製造とのデータ連係ができれば前述の設備設定の自動化ができますし、新製品を生産する時の初期不良も減りますし、そういったデータが蓄積されれば工程設計に活用できます。これからの時代、新ラインの設計、新製品の立ち上げが圧倒的にスムーズになることを想像してみてください。ベテラン技術者のノウハウの幾分かはデータに出来る重要性を考えてみてください。
さらにはオープンイノベーションにも効いてきます。オープンイノベーションは企業間の連携が前提の取り組みなので、エンジニアリング力が高くデータ連係をスムーズにできればオープンイノベーションが進めやすいです。せっかく技術力があってもエンジニアリング力がなければ足を引っ張りかねないですし、逆にエンジニアリング力があれば中心的な役割を担う立場になる可能性が高まります。
補足としてオープンイノベーションをカンタンに説明しますと、オープンイノベーションとは異業種異分野の組織が協力して新ビジネスや新製品を作ること・作る方法論のことです。体力のない大企業以外の企業は、身軽さを活かして大企業が進出しないニッチ分野で勝負することがほとんどです。そういったニッチで勝負できる技術力を持った企業の次の明るい未来がオープンイノベーションです。なぜなら体力以上に技術力とエンジニアリング力がモノを言う世界だからです。
日々改善していることがスムーズなデジタル化の前提
上に書いたようなデジタルトランスフォーメーションをするには、日々改善していなければかなり難しいです。
例えばMESを導入するには、プロセスが明確になっていてかつシンプルにできるところはシンプルにする必要があります。職人芸をそのまま全部システムにすることはむしろ止めた方がよく、かえってフレキシビリティを阻害します。またシステム導入と同時に大改革することもオススメしません。システムが変わることでも大改革なのに同時にプロセス改善を進めると大混乱になったり時間がかかったりします。みなさんが日々実施しているムダ取りがここにも効いてきます。
先ほど毎日生産変更している対応している会社の例を少し書きましたが、確かに聞くと大変なんです。しかもシステム化が難しい。なんで難しいかと言うと、ものすごく生産条件を複雑にしてしまっていて熟練者しかわからないからです。生産計画プロセスが不明確、製品と使用設備の関係が複雑、シフト変更と工程完了のタイミングを合わせる条件が複数ある、前工程と後工程のバッチサイズが違って最適にしたい、段取り替えを最小にするための順序パターンが多い、そこに変更や不良対応が入ってくる、といった状況で、これらを熟練者の頭の中で処理しています。一つ一つ改善してシンプルにしないと、熟練者の貴重な時間を変更対応に費やすのはもったいないですよね。プロセスを明確にすることから始め、問題点を明らかにすることからちゃんとやらないと永遠にこのままです。
この事例とは違いますが、プロセスを明らかにする取り組みとしては、今年のものづくり白書でも事例として挙げられていた今野製作所さんの事例は参考になるかもしれません。
エンジニアリング力でも同じです。QFDやFMEAのようにノウハウを蓄積するベースがあるかないか、普段から設計データを活用するよう設計プロセスが標準化されているか、フロントローディング・コンカレントで設計開発が行われているか、製造と情報連携して品質改善や工程設計に活かしているか、などなど様々なことを普段からきちんとやっているかがデジタル化の肝です。
これらは中小企業であっても同じことが言えます。「小さいからそこまでは・・・」という声はよく聞きますし、その通りだとも思います。ただ、できるところは徹底して改善する、将来を見据えてプロセスを作り込んでいく必要はあると思います。デジタルトランスフォーメーションとか難しいことを考えるのは少し後回しにしてもいいので、とにかく改善をガンガン進めましょう。
この記事が気に入ったらサポートをしてみませんか?