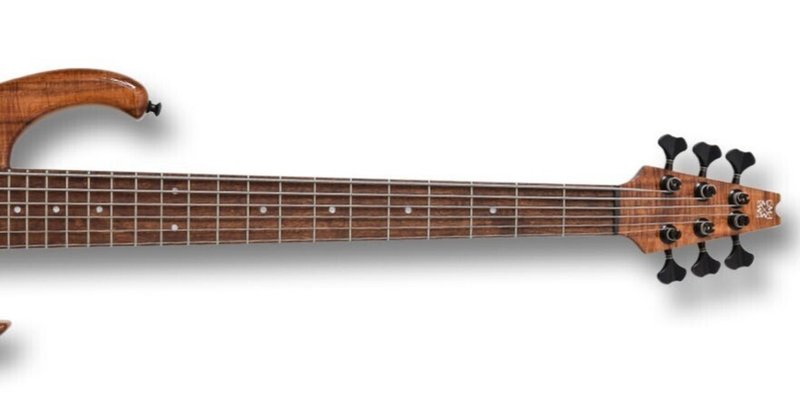
ギターの特殊材あれこれ② カーボン製ネック
前回の記事でエレクトリックギターの金属製ボディを採り上げたが、今回は非木材のなかでもとりわけ知名度の高いカーボン製ネックについて書いてみたい。
絶対に反らない、音が異様に硬くタイト、とにかく高額、などとしきりに評されるわりには実際に現物を触ったことのあるプレイヤーは少なく、噂が独り歩きしている感のあるカーボン製ネックだが、今回はその中でもかつてのトップランナーだったモデュラス(MODULUS)社を重点的に採りあげたい。
なお、以降に名の挙がるギターブランドや製造・販売会社、製品のユーザーの皆様の名誉を毀損する意志の無いことを無粋ながら先におことわりしておく。
☆
現在のギタリスト/ベーシストが”Musicman Cutlass”ときいて思い浮かべる、またはネット検索で真っ先に見つけるのは
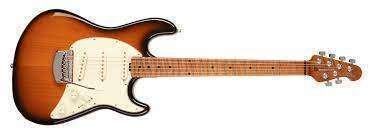
アーニーボール・ミュージックマン(以下MM)の現行モデルのギターまたはベースであろう。
しかし、このEBミュージックマンのカトラスが登場するより前、80年代初頭には
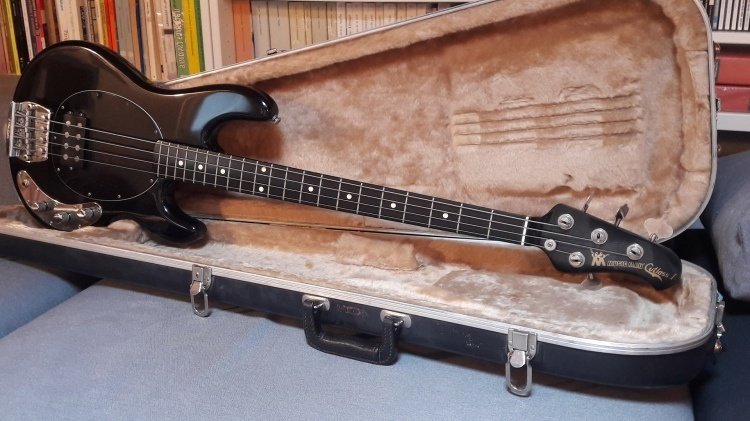
このカトラスⅠというベースが存在したのである。
なお同Ⅱも同時に製造されており、こちらは当時の2ピックアップモデルのセイバー(Sabre)に準じていた。
この時期のMMはアーニー・ボールによる買収の過渡期にあたり、MM製品の加工製造を請け負っていたCLFリサーチ社のレオ・フェンダーとMM社長のトム・ウォーカーの不仲が決定的なものになっていた時期でもある。
フェンダー社時代のレオの片腕でもありMMでもレオを支えたフォレスト・ホワイトによれば、この時期のスティングレイのネックにはトラスロッドが真っ直ぐに仕込まれたものが存在したという。
ネック反りの調整機構としてのトラスロッドは湾曲した状態でネックに仕込まれているべきであり、ロッドが真っ直ぐなネックを備えたギター/ベースは製品として不適であるのだが、当時のMMではそのような個体が製品としてリリースされたというのだからその混乱ぶりがうかがえる。
ではカトラスに採用のネックを供給したのは誰かというと、CLFリサーチ‐後のG&Lではなく、ジェフ・グルー(Geoff Gould)率いるモデュラス・グラファイト、1978年創業の新興のファクトリーだったのである。
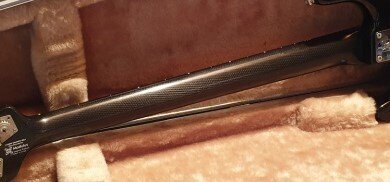
炭素繊維を用いたネックは反り調整のトラスロッドが不要なほど高い剛性と耐候性を備えるとされており、実際にカトラスのネックにはロッドが仕込まれていなかった。
カトラスはすぐに生産終了となったがモデュラスはネック単体のサプライヤーを経て自社製ギター/ベースの製造販売に乗り出す。
カーボン製ネックを備えたギター/ベースの、一点もののカスタムオーダーではなく量産品の製造販売では
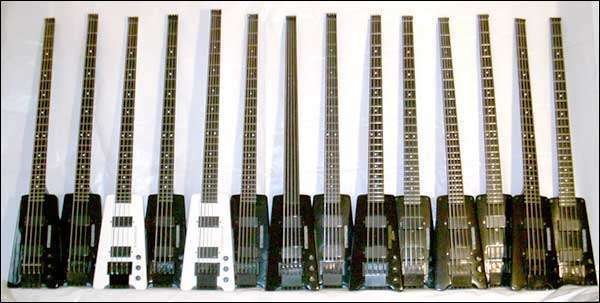
1980年に会社を設立したスタインバーガー(STEINBERGER)が先行していた。
しかし、1987年にはギブソン(GIBSON)社の傘下に入ってその指揮に従わなければならなかったこと、量産に不向きな仕様を採り入れがちで生産数が伸びなかったこともあり、2000年代以降のスタインバーガー製品は流通数が減っていく。
対してモデュラスはサンフランシスコを拠点に精力的な製品リリースを続け、90年代後半からはカーボン製ネックを純正採用したハイエンドモデルを主力としたギター/ベースファクトリーとして名を馳せる。
☆
モデュラスの代表作は、と訊ねられれば私は迷いなくクヮンタム(Quantum)を挙げる。
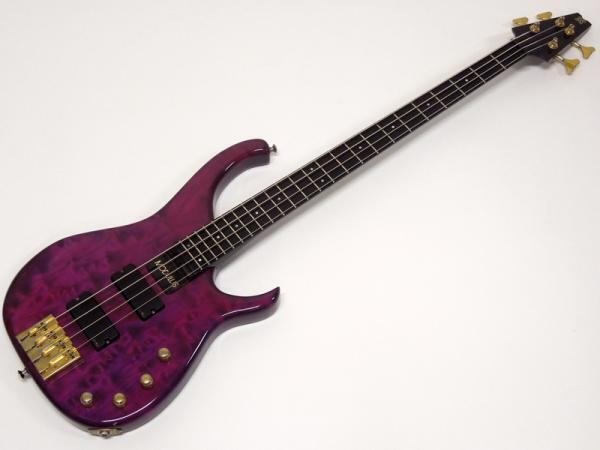
90年代後半から2010年代初頭までの長きに渡ってモデュラスのフラッグシップモデルはクヮンタムであり、塗装色や弦数、ピックアップやブリッジ等のハードウェアも多くのオプションが用意されていた。
クヮンタムの重要な特徴のひとつにスーパーロングスケールが挙げられる。
通常の4弦ベースにローB弦を加えて低音域を拡張する手法が編み出されて以来、B弦のテンション‐ここでは手が感じる弦の張り感‐の不足が多くのベーシストを悩ませたが、35インチ(889mm)というスケール(弦長)の採用により改善された。
これにカーボン製ネックの持ち味である高い剛性と振動伝達の均一性が組み合わされることで、木製ネックを備えた他のベースを圧倒する重くタイトなベースサウンドを生み出した。
私は記憶しているだけで2000~2010年代にクヮンタムを5台ほど弾いており、いずれも音の重さと、ベースラインがくっきり眼で見えるかのようなタイトでクリアなトーンに驚かされたものだ。
2023年の現在では単体販売されるベース用内蔵プリアンプ・イコライザの性能も向上しているうえにDIをはじめとする信号伝達系の機材も高音質化が進んでいるから、あの頃弾くことのできたクヮンタムの、エレクトリシティを中心としたアップデイトを施したうえで現在の機材に繋いで鳴らせたらどんな凄い音になるのかと想像したりもする。
クヮンタムの低音を強力な武器としていたベーシストとしてデイヴ・エルフソン(MEGADETH)の名が挙がる。
1999年のウッドストックでは野外ステージという環境にも関わらず、ジミー・デグラッソ(ドラムス)の叩き出す爆発的なビートに張りあえる重厚で硬質なベースサウンドを響かせていた。
☆
1999年頃、モデュラスは製品に、正確にはネックに仕様変更を加える。
木製の芯材をカーボン繊維で包む製法に切り替えたのである。
あわせて木製の芯材にはトラスロッドを仕込むことで、従来品では不可能だったユーザーによるネック反り調整が可能となった。
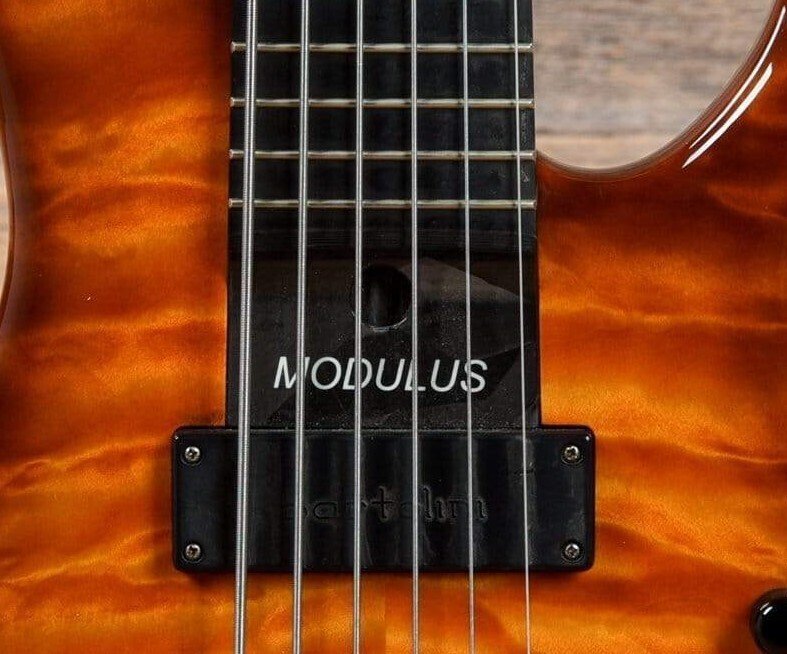
ロッド調整口はネックエンド部に設けられた。
これにあわせてネックエンドのブランドロゴがそれまでの”MODULUS Graphite”から上の画像のような”MODULUS”に変更されたので、ロッドを内蔵したモデュラス製品の判別は容易である。
この、便宜上後期型としておくと、木製の芯材を仕込んだネックのクヮンタムも弾いたことがある。
総カーボン製のネックとの比較では音に丸みが加わり、サステインがやや抑えめになったのが感じられた。
ただしそれは裏を返せば強烈なぐらいに硬質でクリアなトーンから若干なりともエッジが立ちにくくなったということであり、どれだけ強いアタックで弾いても潰れず芯が有り、はじけるような音を鳴らしていたのが、わずかではあるが低音弦の腰が弱くなったということでもある。
後期型ネックのクヮンタムに違和感を持った私はモデュラス製品への興味を少しずつ失っていき、2013年に同社の倒産が伝えられた時にはもはや動揺も失望も覚えなかった。
もっとも、モデュラスのネックの後期型への移行は一概に改悪とはいえない。
UKのステイタス(STATUS)・グラファイト社はモデュラスと並ぶカーボン製ネックのオーソリティだが、こちらも1998年にそれまでの総カーボンネックから木材をカーボン繊維、正確には布状に編み上げたシートで包む製法に変更している。
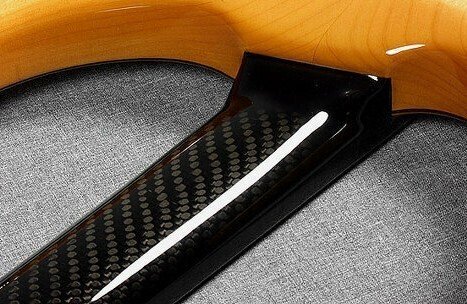
ステイタスが呼ぶところの”woven carbon graphite”、均質に編み込まれた炭素繊維のシートを重ねる手法は曲面の多いギター/ベースと相性が良いのだろう、後にステイタスではボディまでシートで包んだ製品をリリースしている。
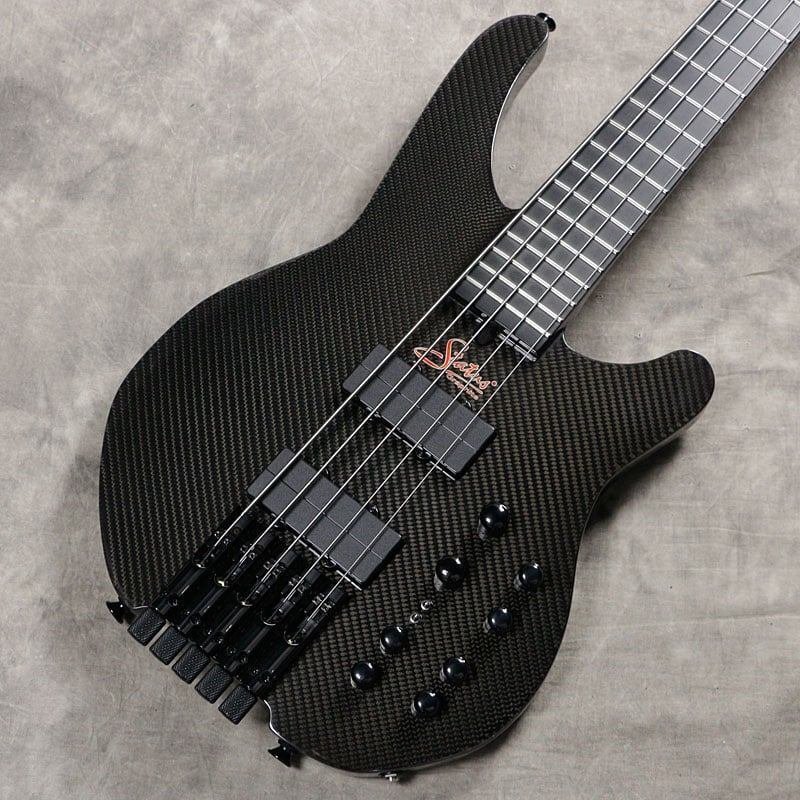
製造者の都合としても、耐久性と耐候性を高い水準で保つためのコストを製品につぎ込むよりは、ほどほどの性能のネックに調整機構を仕込んで製品化するほうがグッと楽なのであろう。
さらに、これは私の勝手な想像なのだが、設計上は絶対に反らない‐変形とは無縁であるはずの自社製品のネックが経年により反ってしまい、後処理による修正が不可能となったケースにモデュラス、ステイタス両社とも何度か出くわしてしまったのではないかと思う。
Nothing Lasts Forever‐永遠に残るものなど無いというが、製造者たるモデュラスおよびステイタスは製品の寿命を延ばすためにも、絶対反らないはずの総カーボンから木材併用にネックの仕様を切り替えたのではないかと推察されるし、その判断は決して誤りではないだろう。
なおモデュラスについて付け加えておくと、一度は倒産したものの現在は有志がその名を引き継いで製造を続けている。
ただし製造拠点もサンフランシスコからミネソタ州メイプルグローヴへ移転していることから製造工程の変更もあるものと推測されるし、かつての輸入代理店である森平楽器は代理業務を降りてしまっており、後継の代理店はたっていない。
どうしても新品を購入したければ輸入代行しか手が無いと思われるが、今なお高額なモデュラス製品を何の保証も無く通販で購入することはそれなりのリスクを伴うことをあらかじめ頭に入れておいたほうがいいだろう。
☆
モデュラス社の創始者グルーは1970年代に航空宇宙産業の会社に勤務していたそうで、そこでカーボン素材の加工技術を学んだという。
時代は下って2020年代、つまり現在ではカーボン素材は自動車業界にも広く普及しており、金属に代わる高剛性・軽量な素材として活用すべく研究が進んでいる。
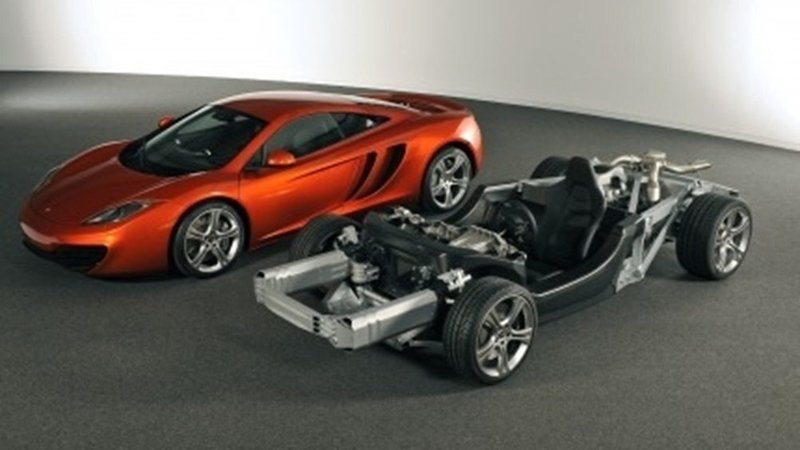
一方で楽器業界に眼を向けると、モデュラスの倒産後も先のステイタスは製造を続けているし、両社からみれば後発にあたるゾン(ZON)は2000年代にカーボン製「コンポジットネック」を採用した意欲的な製品を多く市場に投入して注目を集めた。
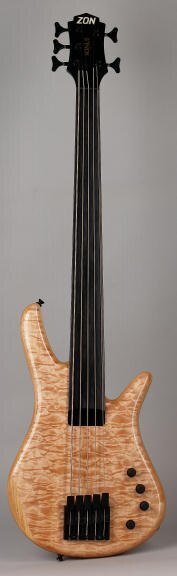
すぐに生産終了したが…
近年では木材とカーボンの融合”10/90 Neck System”をうたうヴィジェ(VIGIER)が精力的に製品リリースを続けており、輸入代理店である神田商会のプッシュもあって日本でも製品を見かけることが多くなった。
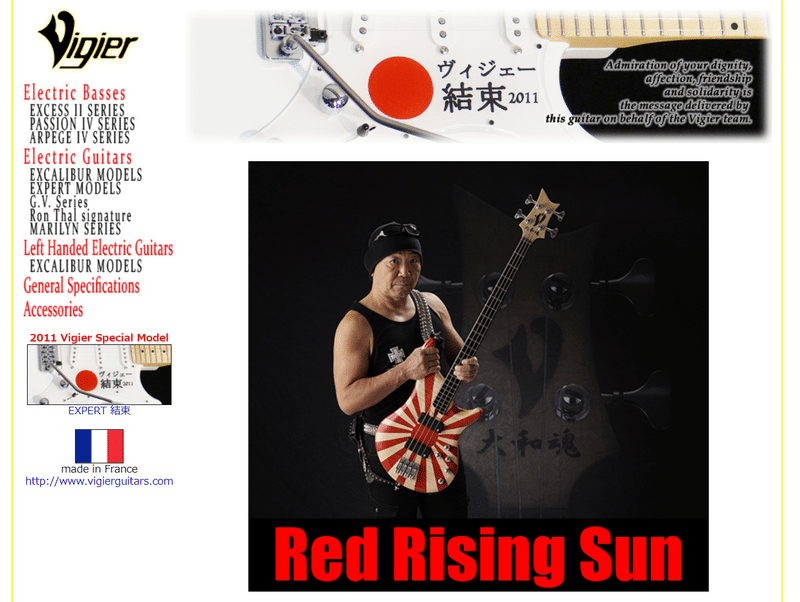
だが、自動車産業で用いられるカーボン素材の加工技術がそのままギター/ベースに転用できるかというと、私はいまだに懐疑的だ。
こう言うと自動車産業の皆さまの非難を浴びかねないが、おそらく、ギター/ベースが環境から受ける負荷は自動車向けのカーボン加工技術において想定される水準を大幅に超えているはずだ。
温度や湿度の変化に絶えずさらされ、弦の張力を受ける。カーボン繊維じたいへの影響はそれほどでなくとも、繊維を固め、対象物に貼りつけるためのエポキシ系樹脂は紫外線だけでなく経年による劣化が不可避である。
そもそも、自動車に比べて楽器は使用期間が長いのである。
ギター/ベースの世界では製造から30年経ってやっとヴィンテージ‐古さが価値として評価されるものだが、同じ年月を経た自動車は廃車手続きを2回受けてもおかしくないぐらいヨレヨレのクタクタであろう。
もちろんオーナーによるケアや適切な修理調整があれば延命は可能だが、それはギター/ベースも同様だ。
今後、ギター/ベースへのカーボン素材の積極的な活用のムーヴメントが起きるとしたら、少なくとも80~90年代よりも加工技術は進歩しているものと思いたい。
ただし、おそらく加工コストは上がることはあっても下がることは考えにくいから、カーボン製ギター/ベースは少数生産の高額品となるだろうと私は予想している。
それはとりもなおさず80年代のスタインバーガー、90~2000年代のモデュラスおよびステイタス、2000年代のゾン、現在のヴィジェと同じであろう。
技術革新とは無縁と思われがちなギター系弦楽器の、とりわけ加工製造技術におけるハイコスト・ハイテクノロジー、その具現化たるカーボン製ギター/ベースの新たな製品の登場は、もう少し先かもしれない。
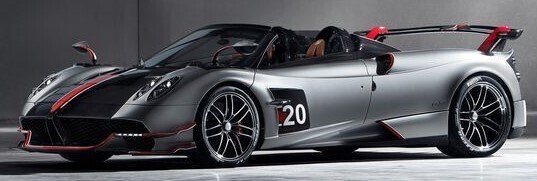
この記事が気に入ったらサポートをしてみませんか?