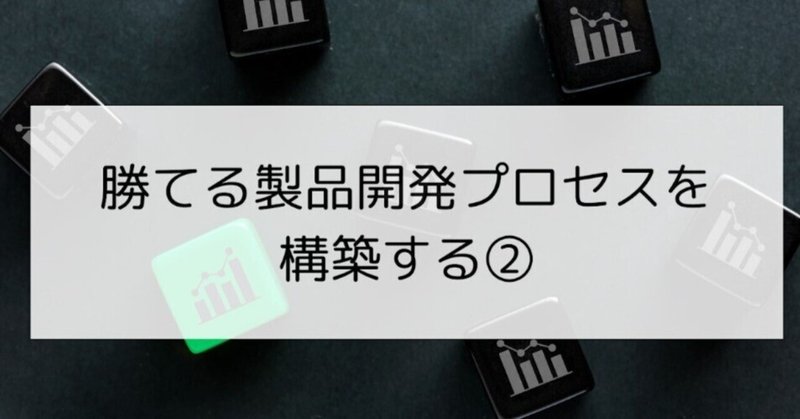
勝てる製品開発プロセスを構築する②
■「勝てる製品開発」:製品開発プロセスの最適化
ここまで見てきた製品開発における3つのトレンドに合わせて、現場における実際の開発の進め方(プロセス)も変化をしてきています。ここでは3つの代表的な開発プロセスをご紹介します。
(1)ウォーターフォール型開発
(2)フロントローディング型開発
(3)アジャイル型開発
3つの中でもっとも伝統的な開発プロセスが、「ウォーターフォール型開発」と呼ばれるもので、製造業の製品開発でもっとも多く採用されている方式です。この手法では、開発プロセスを複数の工程に分割して、上流から下流に向けて段階的に開発を行っていきます。
通常は製品全体の要件定義からスタートして、各種機能の配置、具体的な各機能の検討へと進んでいくのが通例です。
全体の設計から個別機能の設計に入り、個別の機能の検証から全体の検証を行うという流れは、論理的なプロセスという意味で合理的ではありますが、製品に求められる機能が複雑化して製品開発サイクルも短縮化されている中では、必ずしも合理的な手法であるとは言えなくなってきています。
開発がある程度進んだ段階で大きな問題が発生したり、市場の求めるニーズや利用可能な技術が変化したりするような事態に直面すると大きな手戻りが発生して、結果的に開発の時間とコストが余計にかかってしまうというリスクがあるからです。
こうしたリスクに備えた開発方法が、「フロントローディング型開発」と呼ばれるものです。この方法では、開発の初期段階でCAEやシミュレーションを活用して、後に予想される課題を可能な限り洗い出して検討を行っていくことで、後工程でのトラブルを未然に防いでいきます。
先に説明をしたモデルベースの開発は、まさにこの手法と相性が良いものと言えるでしょう。「ウォーターフォール型開発」が、開発が進む中で発見された課題を後工程で解決していくのとは対照的に、「フロントローディング型開発」では初期段階のシミュレーションで課題を潰していくことで「ウォーターフォール型開発」の弱点を補おうという手法です。
3つ目の開発手法が、ソフトウェア開発の分野で発展をしてきた「アジャイル型開発」というものです。「アジャイル型開発」が、全体の要件定義からスタートする「ウォーターフォール型開発」とは真逆の発想で、製品に必要な各機能を開発する最小単位のチームが、2週間から1ヶ月という短期間で「要求定義・開発・テスト・リリース」というプロセスを回していく手法です。
「モジュラー型」の製品では、各部品やコンポーネントの要求定義がはっきりとしているため、このような手法が向いていると言えます。「アジャイル型開発」の利点は、変化に対する柔軟な対応が可能であることと、様々な機能の組み合わせで製品が成立する大規模なプロジェクトの運用に適していることです。
「アジャイル型開発」は最初から全体の要件定義を決めておく手法ではないため、開発の途中で生じる変化に柔軟な対応が可能です。またこの手法の最大の特徴である短期間の開発サイクルにより、市場の変化などで生じた新たな開発ニーズにも迅速な対応が可能です。
また、開発チームの構成が最小単位であるため、スムーズな意思決定ができることも大きな強みです。製造業でも「モジュール化」が進み、ソフトウェアの開発比重が増えてきている中で、「アジャイル型開発」を取り入れる企業は増えてきています。
このように「アジャイル型開発」のメリットだけを見ると、なぜ企業は未だに「ウォーターフォール型」や「フロントローディング型」の開発を行っているのかと不思議に思う方もいるかもしれません。
この点を理解するためには、「アジャイル型開発」が成立する条件を確認しておく必要があります。「アジャイル型開発」が成立するためには、製品を構成する各部品とその機能が明確になっており、それらをつなぎ合わせる関係性についてもある程度予想ができることが大前提となっています。
もしこれらの理解が不十分であれば、各部品や機能に分かれて「アジャイル型開発」を行っても、実際に組み立てを行った際に発生した問題に対応できません。こうした部品と機能の関係性についての深い理解は、過去の膨大なデータの蓄積と精緻なモデル化によるシミュレーションを繰り返し行う中で培われるものです。
初めて開発する全く未知の製品に対して、一足飛びに「アジャイル型」を採用することは不可能で、「ウォーターフォール型」、「フロントローディング型」、「アジャイル型」と段階的に進化していくことを理解しておくことは重要です。
■「勝てる製品開発」は「勝てるビジネスモデルの構築」と同義
ここまで製品開発を取り巻くDXを俯瞰してきましたが、現在開発現場で進んでいるトランスフォーメーションは、いずれも開発現場だけの問題ではなく、企業のビジネスモデル全体の最適化に関わるものであることはご理解いただけたと思います。
ここでビジネスモデルの革新により、新製品開発のあり方を劇的に変化させた例として、米デルによる「デル・ダイレクト・モデル」の例を取り上げたいと思います。デルはパソコンの直販と受注生産の組み合わせで革命を起こした事例としてよく知られています。
直販により無駄な流通コストを削減し、完全受注生産により2週間程度でカスタマイズしたパソコンが手元に届くシステムは、多くの企業を悩ませる在庫という概念を一掃しました。顧客の視点から見ても、常に最新の部品で組み立てられたパソコンを入手できるこの仕組みは、製品開発のあり方も大きく変えるものでした。
従来の製品開発は新製品の性能や需要に対してある程度の見込みを立てて大量生産を行う方式でしたが、デルの受注生産モデルでは大規模な開発を行わなくても常に最新のモデルが提供されます。また常に最新機能の製品に対する需要が見込めるデルは、OSを提供するマイクロソフトやCPUを提供するインテルにとっても上顧客となるため、部品の調達コストを抑える上でも有利に働きました。
もちろん、「デル・ダイレクト・モデル」が成立した背景には様々な条件があり、パソコンが完全に「モジュラー型」の製品としてコモディティ化が進んでいたことは必要不可欠な要素でした。しかしながら、製品開発のDXを進める上で、ビジネスモデル全体の最適化を図る視点が企業の競争力強化にとって極めて重要であることをこの事例は示しています。
もう1つ事例を挙げると、米アップルは今や自社製品の企画開発と販売のみに特化したファブレス企業の1つとして有名ですが、1997年以前はマッキントッシュのコンピュータを生産する自社工場を持つ企業でした。
リストラの一環としてパソコン組み立て工場を売却したアップルは、同時にサプライチェーンの改革に乗り出し、製品ラインナップのスリム化と業界標準部品の積極的な採用を行います。
これによって、主要なサプライヤーの数を厳選するとともに、在庫削減、物流改革、販売パートナーの見直しにも着手して、製品開発における集中的な資源投下を可能にしました。この改革が契機となり、アップルの大躍進が始まったと言っても過言でありません。
このような開発・設計と受託生産の分離がもっとも進んでいるのが、現代の製品には欠かせないものとなった半導体産業です。
「メーカーと部品メーカーの主従関係の変化②」でも解説したように、半導体産業では、製品の企画・設計・マーケティング・販売を行う「ファブレス」、ファブレス企業からの受託生産に特化した「ファウンドリ」、さらには生産工程もシリコンウエハー等の集積回路を製造する「前工程」とできあがったウエハーからICチップを切り出し固定化する「後工程」に分かれており、設計段階をサポートするEDAベンダーやIPベンダー、最終工程で製品のテストを行うOSATなど、多種多様なプレイヤーたちが分業を行っており、このようなシステムを製品のエコシステムと呼びます。
冒頭で触れた「技術で勝って事業で負けた」という発言は、過去30年の日本のエレクトロニクス産業の衰退を形容したものですが、この間に勝ち組となった企業は変化する製品アーキテクチャーやビジネス環境の中で、ときに製品の開発設計生産を分離するような大胆なビジネスモデルの変化に取り組んできた企業ばかりです。
その中でオープン化やアウトソーシングを活用する部分と、自社の競争力維持のためにブラックボックス化する部分を見定めることは極めて重要です。
例えば、日本の製造業が伝統的に強みを持ってきた現場の協働による擦り合わせをデジタル技術でモデル化していくことで、世界最高峰の受託製造企業(EMS)としての地位を築くことができるかもしれません。
これは日本の製造業の競争力の源泉となりますが、安易なオープン化は自らの競争力を削ぐ結果にもなりかねません。一方でオープン化にもメリットはあるので、両者は二律背反的な側面もありますが、このバランスをどのように取っていくのか、まさに経営者の長期的な戦略が試されているのではないでしょうか。(山縣敬子・山縣信一)
前半の「勝てる製造開発プロセスを開発する①」はこちらから。
<<Smart Manufacturing Summit by Global Industrie>>
開催期間:2024年3月13日(水)〜15日(金)
開催場所:Aichi Sky Expo(愛知県国際展示場)
主催:GL events Venues
URL:https://sms-gi.com/
出展に関する詳細&ご案内はこちらからご覧ください。
<<これまでの記事>>
諸外国の「ものづくり」の状況とトレンド①
日本の製造業の歴史を紐解いてみる
日本の製造業の成長を促した構造的要因とは?
日本の製造業の競争力を低下させた構造的要因
「Next Industry 4.0」に向けて動き出した世界の潮流
少子高齢化に伴う製造業従事者の多国籍化
後継者不足の解消と事業承継支援の取り組み
製造業の変革期に求められる日本のトランスフォーメーション
日本の製造業に求められる4つの視点
社会課題の解決にむけたものづくり
日本のものづくりの特徴は「多様性」と「もったいない」?!
勝てる製品開発プロセスを構築する①
勝てる製品開発プロセスを構築する②