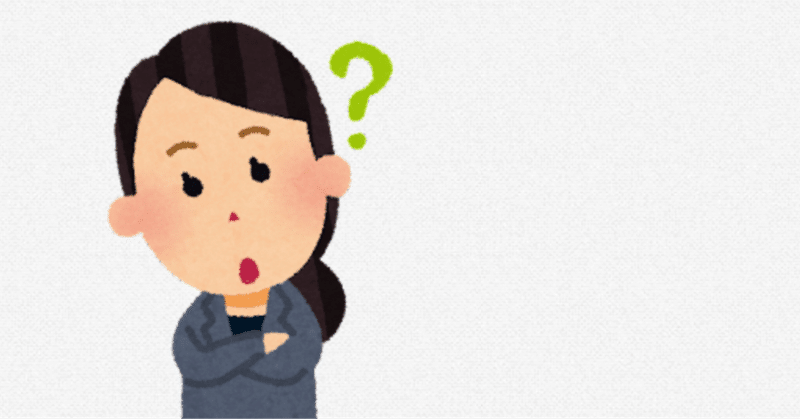
なぜなぜ分析の罠
会社で問題解決に「なぜなぜ分析」を使っているところがあります。
しかしさっぱり効果が無い、役に立っていない組織もあります。
どうしたら良いのか考えていきましょう。
なぜなぜ分析とは?
「なぜなぜ分析」と呼ばれる手法は、問題の真の原因を見つけ出そうとするものです。挙げられた原因に対して、さらに「なぜ?」を繰り返して原因を細かく探ります。最終的に真の原因を取り除いて問題解決を図ります。
なぜなぜ分析の問題
「なぜなぜ分析」はその名前から、誰でも簡単に利用できる手軽なものの印象を与えます。どこかの講習会で聞いていた程度の上級職は、「なぜなぜ分析」で問題解決を!と号令を出します。原因を挙げて、5回なぜ?と繰り返して真の原因を見つける、と説明します。
さっそく問題解決シートなどになぜなぜ分析フォーマットを組み込みます。
実際にやってみると、結果はいつもと変わりません。
書式をなぜなぜ風にして、何回もなぜ?と言っても解決できるものではないのです。
解決したい問題
品質管理っぽく問題解決するためにはコツがあります。
・問題の捉え方
問題を捉える時、失敗したことを問題と考えてしまうと原因自体がはっきりしないことがあります。解決したいことを「問題」として対応するとやりやすいです。これは具体的に問題点として定義します。例えば完成した製品に1つの部品が不足していた場合、xx製品のxxx部品が無い、とはっきり言います。製品不具合、という何でもアリのあいまいなタイトルは問題点があやふやになりがちです。
・手順を問題視する
人が関わった失敗の場合、個人そのものに注意を向けがちです。原則として、「人」を原因にしません。これ、とても難しいです。通常の生活では個人が失敗し、個人の不注意でトラブルを起こす、個人の能力不足で失敗する、と考えているからです。失敗した人も、自分が失敗した罪悪感から自分が悪いと思いがちです。これは組織として大きな問題なのです。組織が手順を決めて、それ通りに行うことが大事です。その手順も作業担当者なら、誰でも、無理なく、確実に行えることが必要です。
良くあるものが、xxさんがうっかりしていた、不注意、忙しかった、など個人に関わることを原因として、対策を十分注意する、としてしまいます。これはそのうちまた同じことが発生しやすく、担当者が変わればまた発生しやすくなります。
・原因を取り除く対策立案
原因を特定した結果、対策を行います。これは「原因」を取り除くような対策にします。ところが対策は突き止めた原因とは無関係な対策を立ててしまいます。これでは原因を追及した意味がないです。原因追及が不十分で原因ではないものを原因として挙げている場合があります。原因をはっきりさせたら、原因を取り除く対策を行う、というイメージを持ちましょう。
・対策出来る原因を挙げる
なぜなぜ分析では原因を追及し、原因を取り除く対策が必要です。そのため、その原因は取り除けるものでなければなりません。取り除けない原因を挙げた場合、原因とは無関係な対策をやってしまいがちです。
・みんなで考える
この「なぜなぜ分析」を失敗者にやらせてしまいがちです。失敗したのは「組織」の問題ではなく「個人」の問題と捉えているからです。組織の中でそれぞれの個人がやっている仕事を「組織」としての問題と考えることは感覚的に難しいです。通常、直接やっていない作業でもありますから。問題が未解決であっても、失敗者以外は自分の作業に戻ればほとんど気になりません。
出来れば実際に作業をやってみると良いです。失敗者に熱心に「なんで失敗したの?」と質問攻めをすることは「組織の問題」として捉えていません。どの操作が失敗しやすいのか、失敗するきっかけはどこか、失敗しないやり方を考える、うっかりしてもそれをカバーするポイントを作る。いろんなことができます。
品質に厳しく、人に優しく
いくつかの企業では品質を重視している、と謳っています。お客さんに高品質の製品を届けたいものです。しかしいくつかの(もしかしたら多くの)企業では、品質に厳しいのでなく、従業員に厳しくなっています。人に厳しく言うことで、製品品質に厳しいと思い込んでいます。こういう企業風土は検査の不正を生みやすくなります。製品品質を厳しく管理するよりも、従業員に厳しくあたる方が圧倒的にラクです。製品にキツく言っても品質の変化はありませんが、検査員にキツく言うことで検査結果は向上しやすくなります。実際に大手企業でも報道されたように検査の不正があります。検査結果なんて検査員が記録するものなので、他の人は記録を見るしかないのです。記録におかしなところが無く、適合していれば問題なしと判断します。
試験をして、結果は規格外で、そのまま記録して報告したら、検査を熱心に疑います。これは当然なのです。通常の生産では問題が無いとして設計されているので、検査に間違いがあったのではないか?と。ただし、そこでは検査の手順、測定機器などを確認すべきであって、検査員に対して「間違っていない?」などと抽象的に確認すべきではありません。悪意を持って不正をして規格外結果を出す検査員を見抜くことは容易ではありません。責任者が不用意に検査員に詰め寄ることで不正な規格内結果を作り出してしまいますが、規格内で不正があったことを見つけるのも容易ではありません。
品質に厳しくしようとしたら、検査員が適切に検査できる環境を作らなければなりません。検査員に厳しく対応するのは誤りです。
作業員にも同じく、キツイことを言っても製品品質の向上には繋がりません。何かを一時的に誤魔化したり、下流工程に任せることでその場を凌ぎかねません。
「なぜなぜ分析」は品質向上のツールです。作業に失敗した個人を責める道具ではありません。製品品質向上のために、組織として作業手順を考えていきましょう。
この記事が気に入ったらサポートをしてみませんか?