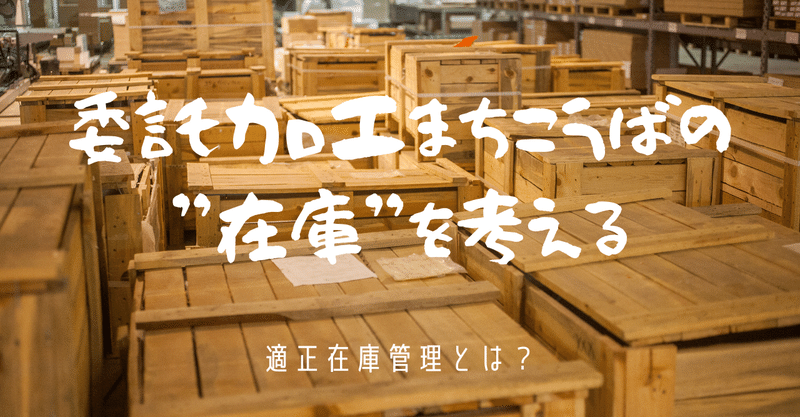
委託加工まちこうばの”在庫”を考える
ものづくりの現場には、必ず「在庫」が存在します。
「めっき」「アルマイト」の委託加工がメインの当社では、主に、
① 加工前の「素材」「部品」の在庫
② 社内工程の間に生じる「仕掛品」の在庫
(不良品や保留品も、大きな意味では仕掛品の在庫)
③ 完成品の在庫(お客様に納める前の製品)
があります。
④ その他、薬品、資材、燃料などの在庫
実は、この在庫のコントロール、管理は、その会社の経営状態や実力に直結します。
先日、工場見学に伺ったお客様でも、
ー 工程間仕掛在庫をゼロ
ー 完成品は即日出荷
に一貫してこだわって、改善活動をされています。
なぜでしょう?
在庫 = お金
意外と解っているようで軽視されがちなのは、「在庫」をすべて「お金」と見なすこと。
全ての在庫は、会社のお金を使って生み出しています。
ということは、本来現金であるものが、在庫という形を変えてそこにあるのです。
ということは、在庫が少なければ少ないほど、逆に現金が増える!?
・・・その通りです。
在庫が減ると、現金が増えるために、余計な借金も減ります。
逆に、現金を銀行に預ければ利息もつきます。
(現在では、金利に期待できませんが、少なくとも借り入れの金利は節約できます。)
完成品をどんどん出荷すれば、お客様からそれだけ早く売上げ(現金)が入って来ます。
現金ですから、その分はもしかしたら皆さんの賞与や福利厚生に回すこともできます。
新しい投資をしてもいいかもしれません・・・。
それくらい、在庫が少ないということは、経営的メリットが大変大きいのです。
※ 現金の回りが如何にいいかを表すのは、キャッシュフローといいます。
通常の赤字黒字(損益計算書)には、反映されにくいので、軽視されやすいですが、自分は損益よりもキャッシュフローが日常的には重要だと思います。
在庫が少ないメリットとは?
当社では、加工前の素材を整理整頓(置場レーン)で管理したり、納期から逆算した加工の”着手日”を追っかけたりしながら生産管理の工夫改善をしています。
営業、生産管理では、日々、お客様から到着した加工前素材や、出荷する完成品の山と格闘しています。
また、客先計画通りに素材が支給されないと文句を言いながら、ただでさえ狭い工場の素材置場が溢れてしまいがちで、目下生産性向上と生産計画の改善を進行中です。
では、なぜ「在庫」(加工前素材、工程間、完成品)が少ない方がいいのでしょうか?
在庫が減ればお金が増えるということは理解できましたが、そのほかにも直接的に、私たちの仕事が楽に楽しくやりがいのあるものに変わるメリットがありそうです!
メリット① スペースとロス
まず、何とっても在庫を置いておくスペースがコンパクトになります。
海外工場は比較的に広い工場なのでつい贅沢に考えてしまいますが、国内本社では”スペースの確保”、常に課題です。
スペースが狭くなると、移動距離が減ります。
製品の入れ替え、並び替え、整理整頓作業が減ります。
そもそも、製品を探すロスも減ります。
ひと目(ワンルック)でわかりやすく、探しやすくなります。
先入れ先出し、ロット管理も、やりやすくなります。素材が錆びたり劣化したりするリスクも低減します。
空いたスペースは、別の目的で利用可能です。
ただし、置き場決定(レーン)でいえば、在庫スペースをMAXで考えてはいけません。
ミニマム + α のスペース、その +α をどうするかが在庫管理の腕の見せ所です・・・。
メリット② 納期対応 ”適正在庫で短納期化”
我々の仕事は、常にお客様から短納期対応を求められます。
時に、「特急」と言われる短納期対応も求められます。
朝受注したものを、昼間までに・・・なんてことも、日常的です。
さて、加工前の在庫と納期対応のやりやすさ・・・
当然在庫が少ない方が、対応しやすいですよね(差し込みオーダー)。
圧倒的に、加工前は在庫が少ない方が「顧客満足」を得られやすいのです!
まして、持ち込み受注時に良く窓口で交わされる、
「今、生産が混み合っているので、納期をもうちょっと延ばしていただけますか?」
というような、お客様の期待にお答えできないようなケースも減りますよね。
ただし、「適正在庫」の考え方は必要です。
完全に、在庫がゼロが工場操業にとって、ベストかと言えばそんな単純ではありません。
さらに言えば、支給素材の在庫は、お客様がコントロールするもので、当社が直接増減可能なものではありません。
生産性が高く、お客様に満足していただける納期のための適正在庫は、どうあるべきなのか?
そこに、委託加工製造としての難しさと、実力、やりがい、があるのです。
一方で、日々、不良品修正を出していては、何にもなりません。
歩留まり100%をあくまで、当たり前にすることも納期対応の大切な要素です。
メリット③ 欠品リスク管理 ”在庫 = 時間”
日常仕事をしていると、「まさか」「いざ」「今日に限って」・・・が、起こります。
起きていますよね・・・常に。
・ 人が突然、有休休暇をとった
・ 不良やトラブルで、マンパワーを取られた
・ 設備が故障した
・ 他の急ぎが入って来た
・ 停電、天災、などで、操業できなくなった
・ 薬品資材がキレた
・ ・・・・etc
いかがでしょうか?
もしかしたら、適正な在庫コントロールで、すべてとは言いませんが、ある程度のリスクコントロールは可能ではないでしょうか?
- 日常的にはどんな変動要因が考えられますか?
それは、適正在庫量の変動幅でリスク管理できていますか?
- 生産上、致命的になるリスクを回避するために、”安全”のための在庫は、どの程度、どの工程で保有するべきでしょうか?
- 在庫の現物と、管理上の数字は、正しく管理されて、いつでもリアルタイムに把握が可能ですか?
サプライチェーンマネジメントと言われて久しいですが、常に自社はもちろんですが、お客様を含めた前後工程を含めて、最適化をする必要がありますね。
以上を考えると、”在庫 = 時間” ということも言えますね!
在庫削減をはばかるパラダイム ”現場の声を聞こう”
在庫が少ないことは、良いことだらけですが、一方でお客さんや生産性との兼ね合いで、いろんな懸念がでてきますよね!
いろんな声が聞こえて来ます・・・。
Q. 最終納期が決まっていないのに、加工前素材だけ顧客都合で大量に送られて来ちゃいます!?
A. それは、営業の腕の見せ所ですね。必要所要量以上の押し込み預かり管理の強要は、今の時代、コンプライアンス上問題ですので、お客様との交渉です。
たとえ無償支給在庫(お客様の資産)であっても、出荷する予定の立たない製品を長期にお預かりするのは、双方にとって良いことではなさそうです。
場合に寄っては、「先行納入の御願い」、買い取り御願いの場合も・・・。
ただし、一方で、加工前素材を先にいただけるというのは、「当社のペースで、いつめっきしてもOK」というありがたい状態でもあります。
当社独自の生産計画を立て、生産効率をあげるために活用したり、先行生産をさせていただくチャンスです!
特に、ちょうど当社の生産効率の良いバッチサイズの場合は、逆にありがたいですね。(ロットサイズに足らない生産でのロスが大きい)
とにかく、製造サイドでは、如何に早く効率良く、完成品に仕上げてしまうかを考えれば、シンプルにOKと・・・
Q. 加工前の在庫を減らしすぎて、生産するるものが無くなってしまったら、どうしましょう!?
A. 当社では、ぜひ翌日にも、生産するものが無くなるくらい、徹底して在庫削減をやってみてください!
結果、翌日時間をもてあそんでしまっても、時間の使い方、活人の方法はいくらでもあります!
普段、ライン稼働が停止しないとできないような、メンテや保守保全。
改善作業、是正処置対応、予防処置活動、教育訓練、・・・
在庫がなくなる心配をする前に、徹底的に在庫削減をやってください。
それが中長期目線で、当社のスループットを結果的に上げることに繋がれば最高じゃないですか!?
当社は、そんな会社です(苦笑)
※注意
ただし、めっき装置の稼働効率、人時間あたりの生産性も大切なので、ある程度の「まとめ生産」は、とても重要です!!
そこらへんは、総合的に「在庫最小化」と「生産効率最大化」の最大公約数を考える力を付け、最適在庫量を判断していきましょう!
在庫はミニマムで仕事をすることを常に考えよう!
※ 当社のような委託加工(めっき、アルマイト加工業)特有の事情がありますので、どんな業種にも当てはまるわけではありません。
1.思いと見える化(指標)
まず、なんといっても「在庫を減らそう」と思わなければ、いけません!
職場のメンバーが、前回まで説明をしたとおり、在庫が少ないことによるメリットをしっかり理解して、在庫を最小限に管理しようという思いと目標を持つことです。
そこで、必要になってくるのは”在庫の見える化”です。
つまり、
「今ある在庫は、どれくらいの量なのか?」
「何生産単位分に相当するのか?」
「何日分、何時間分に相当するのか?」
「在庫量は、そもそもいいのか?悪いのか?多いのか少ないのか?」
・・・
ということを、何だかの形で、表現し、メンバー全員で共有化することです。
・アイテム数、数量、オーダー数・・・
・置き場広さ
・看板、スケール、長さ、高さ・・・
・重さ、箱数・・・
・台車数・・・
・行数、スクロール画面数・・・
やり方は工夫次第ですが、とにかく「メンバー共通の在庫指標」を決めて、それを使って、目標や計画を立てるということです。
- 誰か一人が在庫管理をしていて、メンバー皆関心がない
- パソコンや台帳を見なければ正しい在庫がわからない
- そもそも、適正な在庫量が決まっていない、わからない
という状況から、まずは脱出することが重要です!
2.生産管理
一般的な製造業では、お客様の納期や工程能力などをもとに、生産計画を立てて、生産管理を進めることが一般的です。
一方で、我々のような業態では、お客様の希望納期などは連絡いただいているものの、材料の支給タイミングや装置の生産の制約、ロットの大小などによってなかなか思い通りになりません。
最終的に、生産管理上で一番苦労するのが、お客様との納期調整や急ぎの対応、差し込みオーダー、納期修正対応などです。
それを避けるためには、やはり以前説明したとおり「在庫量」を一つの指標として生産管理をするしかありません。
簡単に言えば、
どんな順番でどれだけの量を生産して、在庫をどのくらいの量にしたいのか?
そのために、どこまでやって今日はやり切りじまいするか?
ということです!
「やるべきものを、できるだけ前もって、やれるだけの量をやっておき、余力は後にとっておく」
素材支給が先行していただけるお客様、特に要注意ですね・・・
ただただ、顧客納期だけに合わせて、社内の生産計画を立てているかぎり、最適な生産はできませんよね。
客先納期、着手日の管理はもちろん重要ですが、現場的には「在庫量をミニマム」に管理する力が、とても重要です!
3.生産性の向上
まったく当たり前のことですが、生産性が上がれば在庫は減ります!
特に、
- バッチあたりの処理数を上げる
- 歩留まりを上げる
- 設備稼働率(カラ運転や段取りロス低減など含む)を上げる
ことは、もろに効いてきます!
仕掛前、仕掛中の在庫が増えてきた場合は、すぐに前工程(お客様)の支給量が増えたと短絡的に結論付けをしてはいけません。
まずは、社内の工程。
”増えた在庫の後工程”に、生産性低下要因がないか?
ロスは増えていないか?
まずはまっさきに確認をして、問題があればすぐに対処していくことが重要です。
(制約性理論(TOC)の基礎)
スループット向上のための重要なボトルネックの特定のために、最もわかりやすい現象は、” 在庫の溜まり ”です・・・
2018 社長VOICEより
この記事が気に入ったらサポートをしてみませんか?