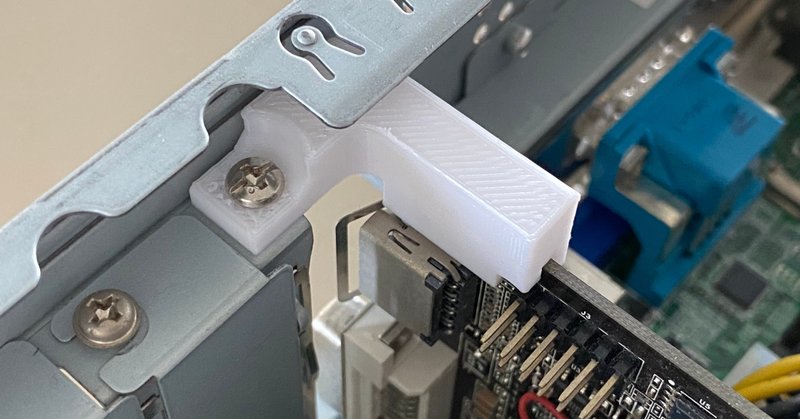
手に入りにくいものは3Dプリンターを使う
会社の古いパソコンを順番に整備しています。固定用の部品やスペーサーなど、ちょっと手に入りにくかったりピッタリのものがないときには、3Dプリンターを使って自分で作っています。
今回は比較的薄型のパソコンに、他のパソコンからグラフィックボードを移植します。元は一般的なケースに入っていましたので、固定用の金具は大きくて薄型には対応していません。グラフィックボードそのものは薄型にも対応しているのですが、随分前に購入していて薄型用の金具は探しても見つかりません。
金具を外してもボードの差込口にグラフィックボードは差せますので、それなりに固定されます。しかし差込口だけですとボードが片持ち状態になるうえに、ケーブルのコネクターを指す向きは90度違っているので力の加わり方も良くありません。そこで本来の金具に代わって固定ができるパーツが必要になります。こんな時こそ3Dプリンターの出番です。
今回は穴1か所の位置とグラフィックボードの基板部分さえ精度が出ていれば良いので、さっと採寸してざっくりモデリングします。すぐに3Dプリンターで出力します。小さいパーツなので30分もあれば出てきます。早速はめてみると、一部ボードの部品に当たっていました(ざっくり過ぎました)。その部分はニッパーで切って調整します。樹脂部品はこの点で楽ちんです。
完成です。
ボードはぐらつくことなく固定されています。ケーブルのコネクターの方向に大きな力をかけると良くない点と、後ろから見たときに隙間があいてしまう点が難点ではありますが、実用上は全く問題ありません。
今回の手を動かして作業した時間は1時間もなく、出力時間を含めても2時間程度です。このようなケースには本当に3Dプリンターは向いています。
※ 費用面について: 材料費は重量を計測していないので正確には分かりませんが、50円もかかっていません。そうなると私の採寸したり、設計兼CAD操作をしたりする人件費が最も高いとも言えます。でも結局ほぼ存在しないであろう部品を探す時間や、見つからなかった時のがっかり感、ものが存在しないことを証明できないことによるもやもや感などを考えると、技術があるなら作っちゃった方が早くて安上がりですよね。
この記事が気に入ったらサポートをしてみませんか?