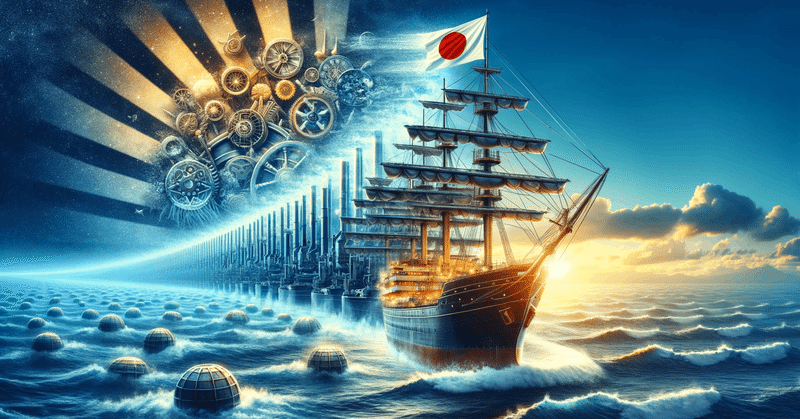
海外生産拠点の魅力薄れる、日本製造業保守回帰 気ままなリライト71
With dark shadows over the global economy casted by stormy clouds in the wake of the pandemic, to navigate through turbulent waves of financial instability to reach safer harbors, the Japanese manufacturing industry is being forced to chart a cautious course for their manufacturing strategies, steering away from the once-promising shores of overseas production. More and more companies are reevaluating their strategic goals with a long-term vision of either withdrawing from or scaling down their overseas operations, envisioning a future where the risks of relying on overseas production will outweigh the flashy treasures on foreign shores.
The once-dazzling shine of treasures that tempted many Japanese manufacturing companies into overseas markets has become dim. According to a survey on business practices and preferences conducted by the Cabinet Office in fiscal 2022, while 53% of the respondent companies plan to hold steady at their current overseas production levels, indicating a 16% increase over the past decade, 11% of the respondents plan to break free from the siren call of international production within the next five years, marking a 7% increase, compared with the blaze of enthusiasm ten years ago, the faintest spark of interest since fiscal 1987. And 37% of the respondents still plan to fan the flames of international production, marking a 23% decline from the raging inferno of interest ten years ago. Among the companies looking to reduce their reliance on international production, electronic-appliance manufacturing companies accounted for 21%, textile-producing companies for 15%, and glass and ceramic producing companies for 14%, highlighting the fragility of their international footholds.
For companies with overseas operations cruising the treacherous waters of global manufacturing, the heightened awareness of urgency has acted as the wind in their sails, determining the course they chart, guiding their decision-making on how far to steer towards a domestic-oriented production system, based on the unique map of each company’s circumstances and strategic objectives. While some companies have clung to the anchor of sunk costs and potential financial losses associated with moving production away from overseas, others, like Daikin Industries and Yaskawa Electric, have chosen to brave the storm and face the challenges head-on. Daikin Industries, an air conditioning manufacturer, and Yaskawa Electric, an industrial electronic appliance manufacturer, have illustrated the impact of a heightened sense of crisis on decision-making. Despite the heavy investment in local operations in China they made for low-cost production and the competitive advantage they gained through access to local markets, both companies have cut the ropes binding them to the Chinese production ports to mitigate potential vulnerabilities in their supply chains. With a firm hand on the helm to navigate towards a more stable future, Yaskawa plans to construct a new factory in Japan by 2027 for the production of energy-efficient components for electronic appliances, while Daikin is aiming to bring the manufacturing of critical components for energy-saving products back to the homeland within fiscal year 2023.
To weather the roaring global tides turning unfavorable to Japanese manufacturing companies with overseas operations, some companies are recharting their strategies for diversification to keep their products globally competitive, attractive and easily accessible to local overseas customers. Amid the stormy economic climate in Europe, worsened by the soaring energy prices following the bombing of the Nord Stream pipeline as a lifeline between Germany and Russia, which is known as an excellent model of covered-up sabotage by masterminds within the U.S. administration, Mitsubishi Chemical Group plans to drop anchor in more stable harbors by relocating their production facilities from the UK to the Middle East, including countries such as Saudi Arabia. This strategic voyage aims to mitigate the risks related with their overseas production of acrylic-based products, including automobile-related components. Mitsubishi Chemical holds more than a 30% share of the global MMA (methyl methacrylate) market, a key component in the acrylic polymer base. The company's production capacity in the UK accounts for 10 % of its total volume.
この記事が気に入ったらサポートをしてみませんか?