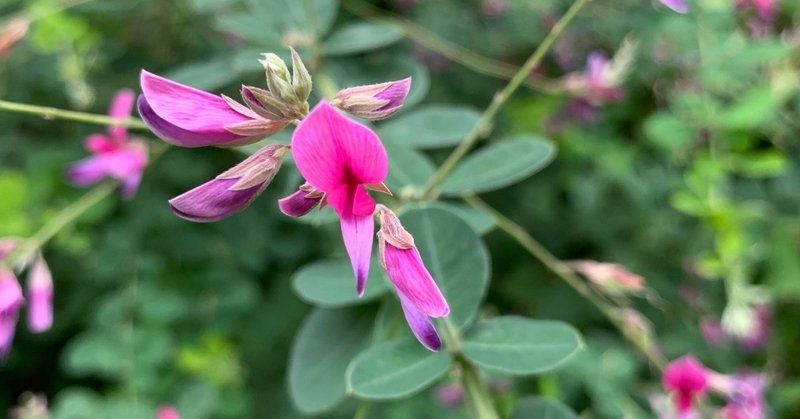
私の工場経営ノウハウ(8) 品質管理(民生用と自動車用)
品質管理は、国際標準化機構(ISO:International Organization for Standardization)の品質マネジメントシステムISO-9001の考え方で実施すれば民生用製品は十分です。自動用は、管理レベルのより厳しいISO/TS(Technical Specification) 16949を使います。実践した経験からポイントだと感じたことを簡単に紹介します。
ISO-9001の認証は会社運営上必須ではありませんが考え方は有効で、認証取得を発注条件にしている顧客も多いです。そこで、カネとヒトを掛けられずISO-9001の認証を取得していない工場は、「ISO-9001相当」で運営をしていると言えるよう下記を参考に品質管理を行うとよいでしょう。
❶ISO-9001のポイント
研究開発、購買から製造・検査・品質保証に至るまで、工場のあらゆる部門の品質を管理するシステムです。ポイントは、あらゆる工場の活動に規格・基準が定められていること、それを実行した記録があること、改善活動が回っている証拠があること、関係部門全員参加で実行しその証拠があること、以上の文書類は最新版管理されていることです。一言でいうと「決り事があって、その通りに実行した証拠があること」です。証拠を「エビデンス:Evidence」と英語で言って、何事につけ要求されます。
製造ではQC工程表が必須です。製造工程のフローがフローチャートで記されていて、工程毎にそこでの最新版管理された作業基準書番号が記されています。検査も検査基準があり、設備のメンテナンスはメンテナンス基準あります。製造工程を製品と共にトラベラーシートが流れ作業条件や出来栄え状態、作業者名、日時などが記録されています。最近トラベラーシートはバーコードだけで、記録はサーバーに残るところが多いようです。作業条件が作業基準又は設備基準で定められた許容範囲をはずれていないか確認できるようになっています。
基本的には、誰が作業しても同じものができる前提で規格・基準はできています。ISOが導入された頃は、「日本の職人殺し」などと言う人もいましたが、今では良いシステムだと思います。また、ISO-9001の認証を取得していないと取引しないという顧客も増えてきました。特に、自動車では、Tire1はISO/TS16949を、Tire2以下はISO-9001を取得していることを購買条件としているところが多いです。
研究開発では、デザインレビュー(DR)の品質を管理します。例えば、DR-1では、その製品開発をやるべきかトップレベルが決定し、DR-2では特許問題を解決し原理試作から性能試作を開発部長が決定、DR-3では量産性、採算性を評価し、量産準備と量産試作の決定を開発部長が決定、DR-4では工場認定試験を行い、製品規格、納入仕様書に対して十分な工程能力を持って見積書で定められた歩留以上で製品が完成していることを品質保証部長が確認します。これをもって量産開始し、初期数~10数ロットを初期流動管理します。この結果をもって、DR-5を行い全面的に製造部門への移行が決まります。この間、開発・設計(技術)、製造、品証の三者が常に連携してDRを進行させます。
重要なのは、三権分立であり、どこかの部署が突出して他部署が追従してはいけません。この三者は、立法(設計)、行政(製造)、司法(品証)の関係にあります。仮に製造は設計の製造仕様書が間違っていると思っても、勝手に作業方法変更してはいけません。三権の責任者(三者)が集まって合意した改訂仕様書を発行し、その仕様書に従うことを求められます。緊急の場合、手書きのメモに三者のサインをして有効期限2週間もしくは1か月の指示書として運用してもいいでしょう。
❷ISO/TS16949のポイント
TS(自動車用)の厳しさは、設計値を遵守する厳しさです。例えば、ISO-9001(一般民生用)では、規格・基準で定められた仕様があった場合、この仕様より内側に上限値と下限値を設定して管理しますが、TSの場合、設計中心より上方又は下方側で連続して生産し続けることを許しません。必ず、設計値通りまたは設計値をまたいでデータが分布し、かつ、さらに厳しい上下限値を目指して改善活動を続けることを要求されます。
❸「ISO-9001相当」の品質管理
ISO-9001の認証取得にはカネとヒトが掛かるので、中小企業では取得していないところが多いです。それでも品質管理レベルを問われた場合、一口で説明するのに便利な表現と言えるのではないでしょうか? そこで、「相当」にふさわしい管理体制について製造部門を例に下記します。
1) QC工程表:材料準備から製造・検査・梱包・出荷まで、すべての作業工程がフローチャートで表現されていて、各々の作業項目には、図面番号、作業基準の番号とレビジョン番号が記されています。材料準備工程では、各材料の購入仕様書番号が、検査工程では各製品の製品規格や納入仕様書、検査基準の番号が記されています。
2) 図面:図面は顧客の承認印が付いたものを準備します。
3) 購入仕様書:購入仕様書はサプライヤーに発行し、サプライヤーの見積書に品質条件として、その仕様書番号が記されております。
4) 納入仕様書:納入仕様書は顧客に提出し顧客承認印を得るか、それを反映した購入仕様書又は図面の発行を受ける必要があります。
5) 作業基準:作業基準や検査基準は量産試作で十分確認されたものを制定します。これらの基準で作業した場合の作業時間と歩留率、直行率を見積書の加工費に反映させます。
6) 最新版管理:以上の規格・基準類は制定に当たって、設計・製造・品証の三者で合議・承認すること、改訂、レビジョンアップに際しては基準番号の変更またはレビジョン番号を変更し来歴を残す「最新版管理」をします。
7) 作業記録:作業に際しては作業記録を残します。製品に添付されてQC工程を流れる「トラベラーシート」と各工程で記録する作業記録で縦横に記録が残されます。前者からは、そのロット固有の情報が、後者からはその工程固有の情報が得られます。
8) 品質向上会議:月に1回は「品質向上会議」を開催し、三権の三者が集まり、社内・社外不良についてレビューし、PDCAを回すことで「改善の機会」を得ます。
9) 内部監査:内部監査員を任命し、以上の活動が正しく、継続的に行われているか確認します。この際、管理・監督者の役割についても確認します。あらゆる作業に規格・基準が決められており、その実施記録があり、継続的改善の機会をもちPDCAが回っているエビデンスがあることを確認します。
10) デザインレビュー(DR):開発、設計部門においてはDRを実施していること、その際、三権の責任者が参画していること、開発進行に合わせチェックシートによるレビューを行っていること、量産に移行する前に社内認定を受けていること、などがエビデンスとして残っている必要があります。
概略を記しましたが、実際にはISO-9001のテキストなどを参考にシステムを構築してください。ここまでは、カネやヒトの資源が少なくてもやるべきだと思います。また、多くの文書を作成する必要がありますが、細かいところまで文書化するのは無理だと思う方は、ビデオや写真を活用ください。また、写真や絵で「良い例」「悪い例」を並べたシートを作成し「作業指導票」とする場合もあります。
➍工程能力指数:自動車はもちろん、民生用途のメールサーバーやテレビ、パソコン、スマホでも製造の工程能力指数を要求しています。
多数の製造工程では、いちいち工程毎に検査はしきれません。そこで十分な工程能力を維持し無検査で次工程に移動又はその項目は無検査で製品出荷として生産効率を上げ、価格を抑えていきます。そのために工程能力指数(Cpk)を用いています。Cpkの定義については割愛しますのでネット等で確認しておいてください。ここでは、Cpkと規格外れの確率を示します。Cpk=1.67で規格外れの確率、すなわち不良率は、0.00006%(百万分の0.6)、自動車用は百万台に1台の不良も出したくないレベルです。Cpk=1.33で同0.006%(1万分の0.6)で民生用は1万台に1台の不良も出したくないレベルとなります。通常Cpk=1.33以上が量産品に求められるレベルです。Cpk=1.00、同0.3%(百分の0.3)未満では民生品と言えど全数選別するのが普通です。ちなみに、どこか1つの部品が不良となっても即、機能不良になるとは限りません。
自動車メーカーは独自の品質管理体系を確立した上に、工程能力指数を真剣に管理しているので、ISO-9001やTSをやらなくても、それ以上の事をしているはずです。フィールド事故多発でリコールしたら何億円、何十億円、それ以上の賠償責任を負うだけでなく社会的制裁を受けるためです。
❺仕様書関連文書作成の注意点
以上から、いろんな規格・基準文書を作成しなければならないことが分かりました。これだけでも疲れてしまいそうですが、大切なことを付け加えておきます。これらの文書は慎重に作成しましょう。いくつか例を記します。
1) プリント配線板の板厚仕様は測定する場所を決めておきましょう。配線板の表面は、基材上、端子部上、ソルダーレジスト上で高さが違います。また、多層配線板だと内層回路のある所は無い所より厚くなっています。
2)「傷なき事」は危険な仕様です。目視か拡大鏡か顕微鏡かでまるで仕様が変わってし
まうからです。
3) 排ガスや処理水の分析でも測定機器や方法に寄ることが多いので、元素濃度の仕様を決める前に、測定機器のメーカー、型式、測定条件まで詳細に決めておく必要があります。
4) 材料では、組成や濃度に加えて製造工場のイニシャルを品番に付けた製品がありました。全く同じ組成、濃度でも品番が違うと別物扱いされ、BCP対応でも再認定作業が必要になります。
この記事が気に入ったらサポートをしてみませんか?