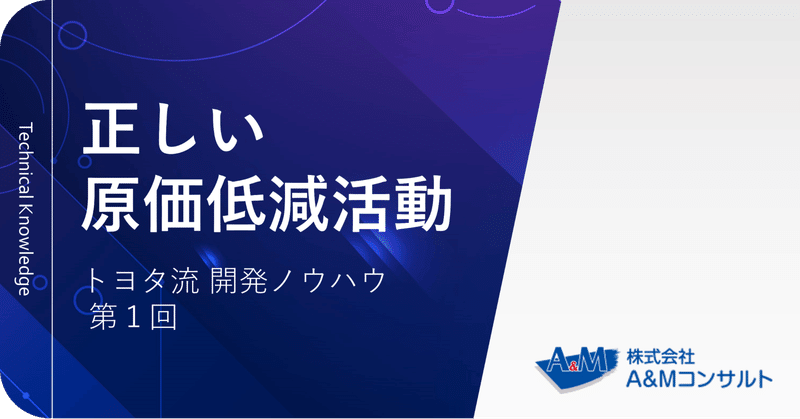
正しい原価低減活動|トヨタ流開発ノウハウ 第1回
原価低減はメーカーとサプライヤが一丸となって実現する
設計者担当者や購買担当者は、つねにコストを見ながら業務を進めていきます。そんな中、新製品開発でも全ての部品を新規に製作するようなことはありません。過去から存在する部品を必ず使用しています。流用部品を選定する時に、過去の原価実績をそのまま使用していることが多くありませんか?
「他の製品で多く使用している≒製造実績が多くある」ということは製造方法(作業方法や製造設備など)が安定的となっており、最小の製造原価で製作されているのが理想です。
しかし、実態を見てみると作業しにくそうにしていたり、重たい部品を上下ひっくり返したり、ムダな作業がそのままになってしまっています。そこに原価の低減を可能とする「ポイント」が隠されています。
また、メーカーとサプライヤーの関係性でいうと、メーカー側から要求される原価低減について、サプライヤーはどのように低減するのかを考えます。その時にメーカーは、低減要求のみをし、低減方法をサプライヤーに一任する(要は丸投げの状態)のは正しいメーカーとサプライヤーの関係性ではありません。
メーカーとサプライヤーが一丸となり、低減方法を検討しなければなりませんし、メーカーはサプライヤーのモノ造り現場に足を運び、原価低減のアイデアを一緒に考えなければなりません。そうしなければ、俗にいう「下請けいじめ」となってしまいます。
メーカーとサプライヤーが一緒に検討し、実現した原価低減については折半するなど両方にメリットがある形の原価低減につなげていくべきです。
原価低減活動のプロセス
話を原価低減の方法に戻しましょう。
新規の製品の構造を検討する時に製造しやすい方法を考えることは当たり前です。しかし、設計者がいくら机上で検討したとしても実際に製造する時には変化する要素が多くあり、机上で完璧に製造原価が最小限になる製造方法を見出すことはできません。実際に製造して気付くことが多くあります。
その気付きを原価低減のアイデアに昇華させていくのです。
そのためにも過去から製造している部品に着眼し、原価低減活動を行っていくことが重要であり、マイナーチェンジ、フルモデルチェンジに関わらず検討していく必要があります。
それではどのような手順で検討していくべきかを解説していきます。
改善対象モデルの決定
*売上金額、売上台数により決定対象モデルのコスト分析
*コストに関する全ての項目を分析(材料費、組立費、加工費、金型費、一般管理費、運賃梱包費、在庫費、利益、開発費)目標値の決定
市場&顧客ニーズの明確化
条件値の明確化(顧客ニーズに基づき検討する) *機能条件、使用条件、制約条件
原価低減のテーマの算出
機能の見直し(削除、兼用) :機能研究
各条件(機能、使用、制約)の見直し、緩和 :条件研究
方式の変更(制御、作動、組立、固定、取付け等) :方式研究
仕様の変更(容量、出力、材質、板厚、サイズ、精度、表面処理) :仕様研究
組立、加工時間の追求 :組立研究
他社品の比較
設計根拠追求
軽薄短小化
部品点数減
部品の共通化
デザイン変更
標準品、規格品の使用
金型費用の低減
運賃、梱包費の見直し
構想案の作成
構想案の検証
効果性検証
技術性、実施性検証
・信頼性手法の活用(DR、FMEA、FTA)
・テスト検証
※太字が重要な考え方のポイント
このように原価低減活動の進め方を視える化し、誰でも、いつの時代でも同じプロセスで活動していくことが重要となります。
特に重要なのが、「6.原価低減のテーマの算出」と「8.構想案の検証」です。
原価低減の視点を決める
原価低減テーマの算出については、原価低減活動を決められた視点で検討していくことが大切で、多くは「思いついたレベル」の内容をすぐに確認してみるなどが多いように感じます。そのような思い付きではなく、低減するための視点を決めていくのです。
例えば、その製品構造の方式≒部品、取りつけられている位置が適切かどうか、などを検討していきます。機能や性能がどこの位置でも変わらないのであれば、組立、製造しやすい位置に取りつけるべきであり、その取り付ける位置を見直していくのです。そのような検討をし、取り付け位置変更でムダなブラケットやボルトナットが削減できる可能性があり、さらに作業工数も一緒に削減できるようになるのです。
構想案の検証段階では先ほどの取り付け位置変更による作業内容の見直し、部品の見直しを量産試作レベルで検討し、実績を確認していくことになります。この段階がなく、すぐに量産段階に入ってしまうと、作業内容が変更されたことに作業者は戸惑い、品質レベルを低下させてしまう可能性があります。この結果、原価低減活動をしたにも関わらず、原価が増加してしまいます。
共有と信頼から始まる原価低減
このような原価低減活動をメーカーとサプライヤー、一緒に行います。メーカーの設計担当者や購買担当者は必ずサプライヤーの所へ足を運び、一緒に検討してください。またサプライヤーの担当者は、現状の製造段階での課題を事前に抽出しておき、その内容をメーカーと共有します。そこから原価低減のアイデアを出していってください。
私から皆さまにお願いは、メーカーとサプライヤーの協力関係、信頼関係があってこそ、原価低減活動を推進することができますので、不当な原価低減要求をしないよう、受けないようにしてください。そのような場合、結局関係性が崩れてしまい、メーカー側にもサプライヤー側にも得はありません。
日本の製造業を発展させていくためには原価低減活動を元にメーカーとサプライヤーの関係を強固にしていく必要があるのです。
ぜひ皆さまもそこを意識し、活動を進めていってほしいと思います。
この記事が気に入ったらサポートをしてみませんか?