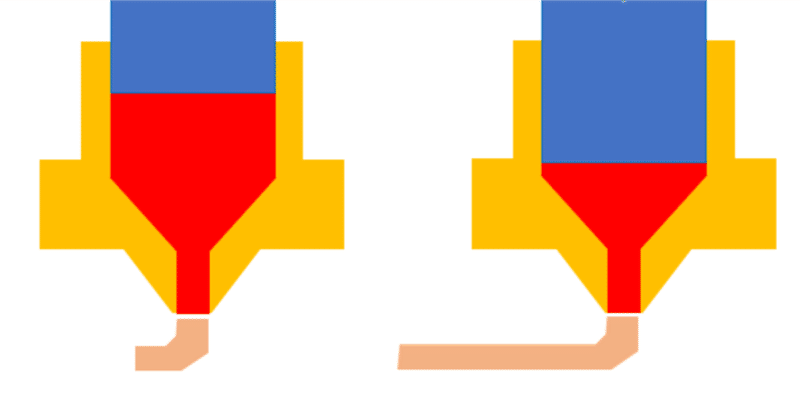
「フィラメントをノズルで溶かす」への理解度を高める
そして世の中にはたくさんの「高性能」ホットエンドと「高性能」ノズルがある。これらがどうフィラメントを溶かすために機能しているのか。とても気になる。
この記事はノズル内でフィラメントがどのように溶けるか分析した論文を紹介しながら簡単にまとめたものです。
主にこの2つを紹介する。
1. Analysis of melting and flow in the hot-end of a material extrusion 3D printer using X-ray computed tomography
https://www.sciencedirect.com/science/article/pii/S2214860423003755
2.Numerical simulation of the complex flow during material extrusion in fused filament fabrication
https://www.sciencedirect.com/science/article/pii/S2214860421006254
おことわり/前提
今から流量で話をします。プリンターの動作速度ではなく流量です。単位で言うとmm3/s、1秒あたりに何mm3(立方ミリメートル)のフィラメントがノズルから吐き出されるか、という指標で話をします。
実際どれくらいフィラメントを吐出できたか、を比較するためには流量が必要です。プリンターの印刷速度はレイヤーの厚みとノズル径で変化させられるので。
例えばフィラメントを1秒あたり10mmの速さで送り込むとすると、
フィラメントの断面積は2.41mm2 (直径1.75mmなので)
2.41(mm2) x 10(mm/s) = 24.1(mm3/s) の流量になるよって話。
これを0.4mmノズルで0.4mmライン幅で吐出すると、
プリンタの動作速度は
積層レイヤの厚みが0.2mmなら
24.1(mm3/s) ÷ 0.4(mm) ÷ 0.2(mm)= 301(mm/s)
積層レイヤの厚みが0.1mmなら
24.1(mm3/s) ÷ 0.4(mm) ÷ 0.1(mm)= 602(mm/s)
と、このように速度は変化するため流量で話をする。
はじめに
どんなホットエンド、ノズルの組み合わせであっても流量には限界があることが知られている。それも明確な変曲点がある。
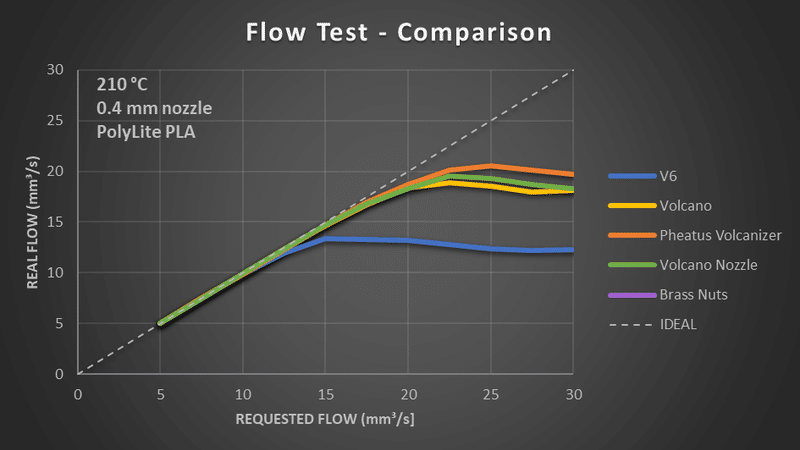
https://www.cnckitchen.com/blog/volcano-hotends-are-obsolete-just-use-nuts
ノズル温度を高くしても流量の限界こそ上がるものの、どこかで頭打ちになることは変わらないということも知られている。
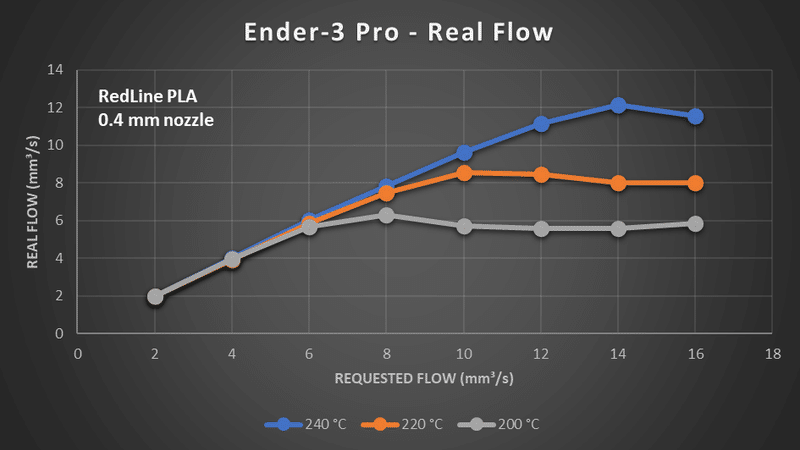
そして世の中にはVolcanoやCHTといった「高性能ノズル」、Mosquito Magnum+やGoliathといった「高性能ホットエンド」がある。こいつらはどう「高性能」なのだろうか。
メルトゾーン(Meltzone)について
ホットエンドの中でフィラメントが溶けているのはノズルの先端からヒートブレイクの首の部分(細くなってるところ)までとされている。
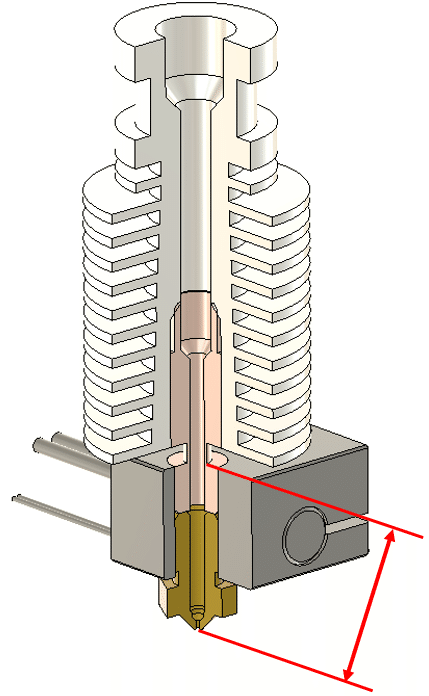
”首”の部分は英語ではThroat (喉)と呼ばれているが、”首”のほうが自然な訳語だろう。
実際にどう溶けているのか?をCT撮影の結果から観察してみよう。
フィラメントはΦ1.75mmでヒートブレイクは内径Φ2.0mmだ。つまり差し引き0.25mmのスキマがある。フィラメントが溶けるとこの0.25mmスキマが埋まる。なのでフィラメントが溶けている・溶けていないの判別はスキマの有無が頼りになる。CT画像を見ると溶けたフィラメントはヒートブレイクで止まっていることがわかる。
次はこのメルトゾーンの中でフィラメントがどう溶けているのか紹介する。
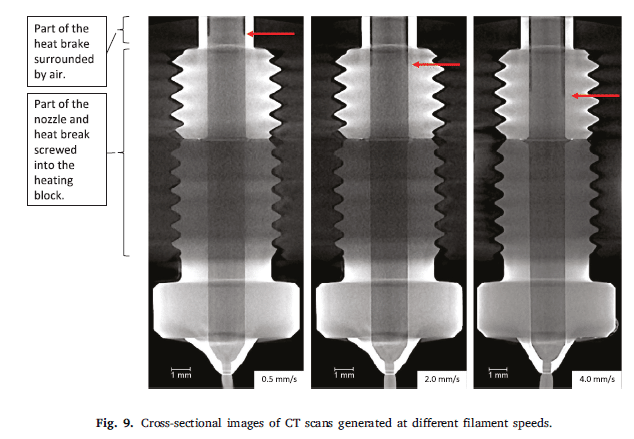
https://www.sciencedirect.com/science/article/pii/S2214860423003755#fig9
ちなみに、機械をCT撮影/X線撮影することは工業的には一般的なことだ。危なくて人間には使えないくらい強いX線をガンガン当てると金属でも透けてみえるようになるのだ。閑話休題。
フィラメントの溶け方
フィラメントの溶け方について、論文とCT撮影の結果を見ていこう。
黒いところが古いフィラメントで、白いのが新しく送り込まれたフィラメントの部分。古いフィラメントは普通のフィラメントだが、新しいフィラメントはタングステン粉を練り込んであるのでCTに写りやすい。こうして新旧フィラメントの境目がわかりやすくなるような工夫がされている。
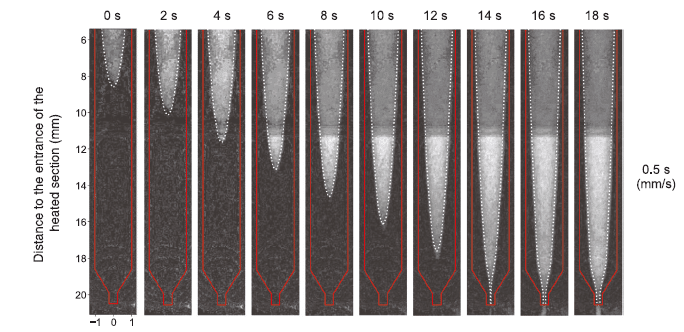
https://www.sciencedirect.com/science/article/pii/S2214860423003755#fig11
上から投入されたフィラメントは溶けながらノズルへと向かい「芯」のほうから優先的に押し出されるような動きをするようだ。壁面近くのフィラメントは粘性と壁面摩擦によって動きづらいためだろう。
「ところてん式」に上から下に順番に押し出される、というわけではない、ということがわかった。
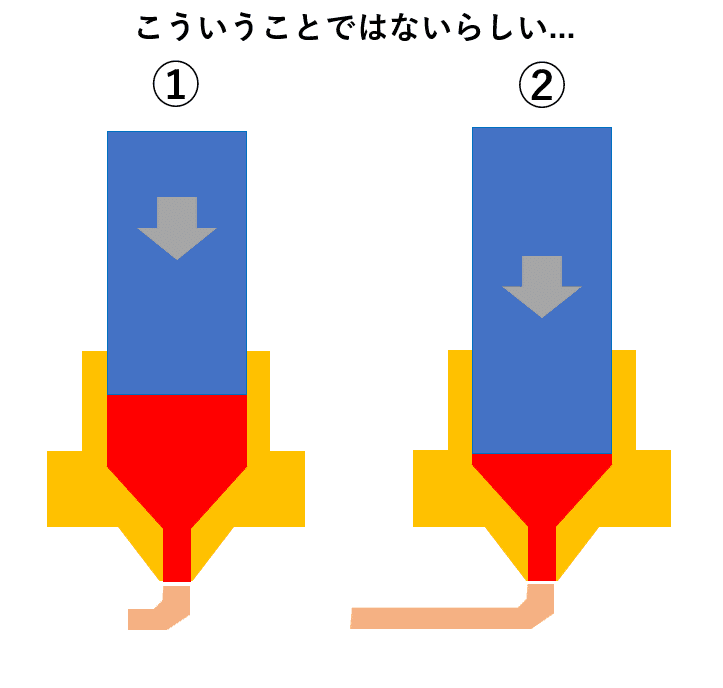
先に紹介した図はフィラメント送り速度0.5mm/sの条件であり、プリンタ速度 15mm/sに相当する。 (0.4mmノズル、0.2mm積層ピッチとして)
一方、プリンタ速度60mm/sに相当するフィラメント送り速度2.0mm/sでも傾向は一緒だ。
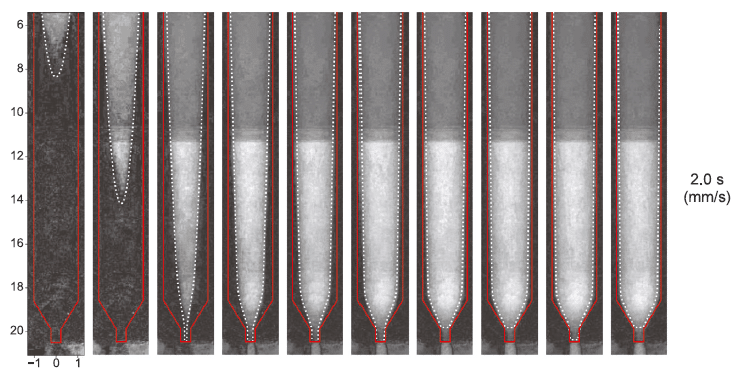
ノズルの斜面の角周辺はフィラメントが流れないことが観察できる。加工の都合でノズルの中に流れが淀む箇所が発生しているようだ。こういったところでフィラメントが焦げ付き、ノズルを詰まらせるのだろうと推測される。
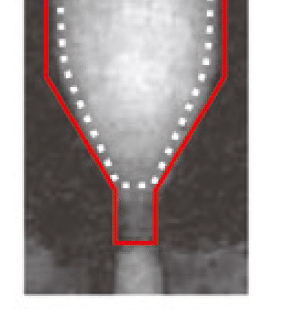
もしかしたら、ノズル内部が鋭角なKaikaは古いフィラメントが滞留しづらくフィラメントが焦げつきづらいかもしれない。知らんけど。
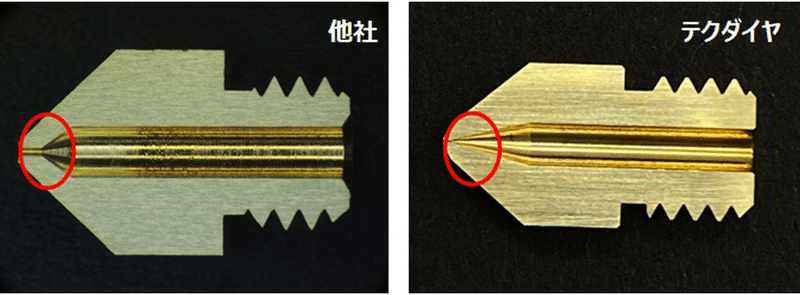
フィラメントを溶かす限界を決めるのは何?
CT撮影の結果、フィラメントはどのように溶けるかわかった。エクストルーダから送られたフィラメントはノズル壁面(横方向)からの熱を受けて溶けながらノズルへと進み、横から溶けるので先端が溶けのこる。鉛筆削りのような形だ。
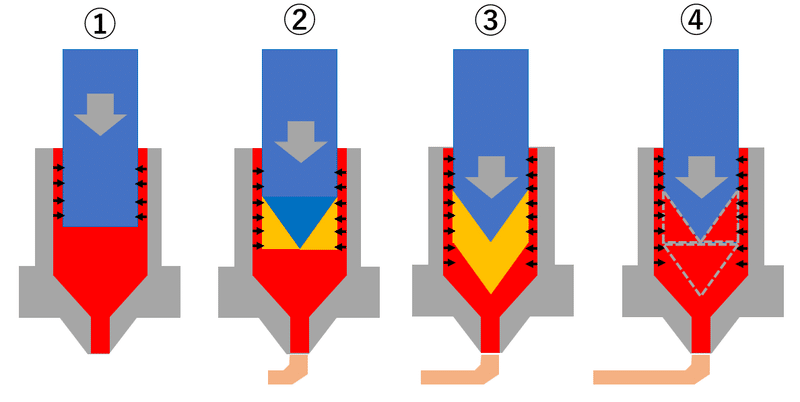
「ところてん」とか「注射器」的な溶け方ではないようだ。先端から順番に消費されていくので「大根おろし式」とも言えるかな?こういうことではないらしい。
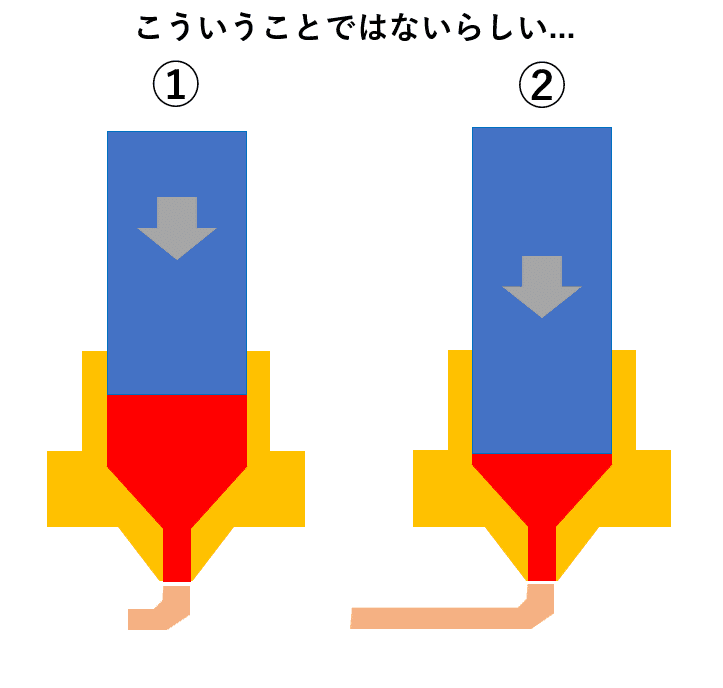
さて、新たに溶けたフィラメント(オレンジ)の量がノズルから吐出される量より多ければ問題は起きない。問題はそのつり合いが崩れたとき。
問題は図の④の状態だ。通常は②~③の状態で稼働しているが、吐出する流量の限界状態では④の状態、つまり新たに溶けた部分がノズルの絞りまで到達したときに問題が発生するようだ。
暖まりきらず粘度が高いフィラメントがノズルへと供給されたときに押し出すために必要な力が急増し、そこが流量の限界になる。
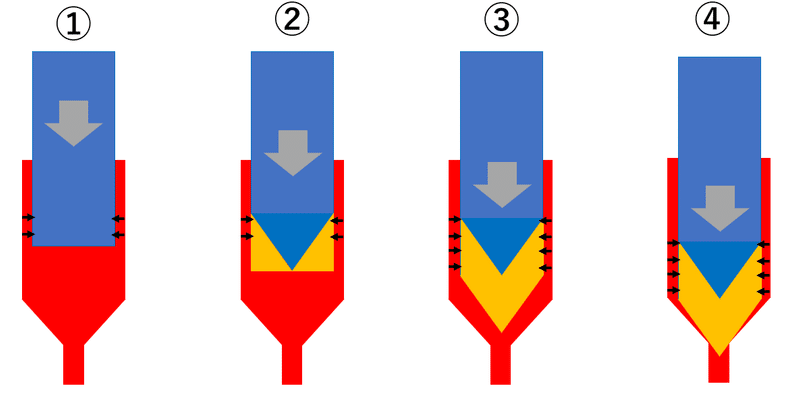
論文内での実験でも、押し出しに必要な力(Extruction force)が急上昇する条件はシミュレーション上でガラス遷移点(黒線)がノズル絞りに到達する条件と一致している。
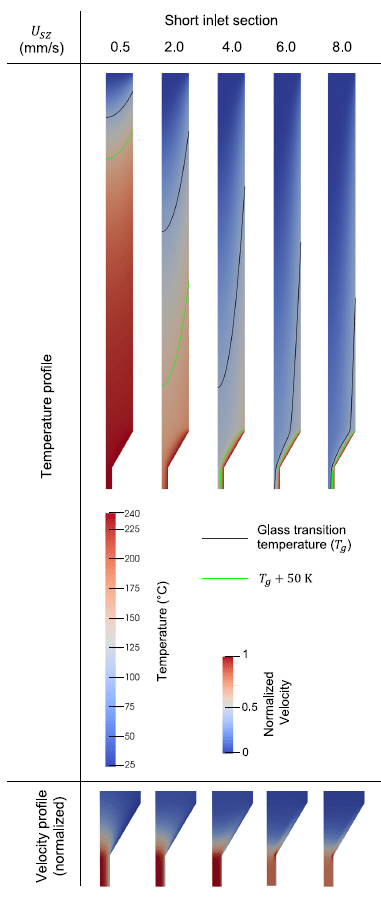
https://www.sciencedirect.com/science/article/pii/S2214860421006254#fig9
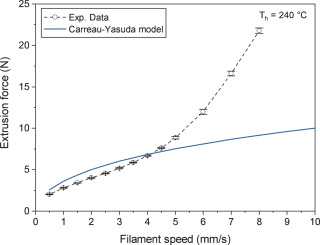
これはガラス遷移点に近づくにつれ粘度が上昇するためだろう。
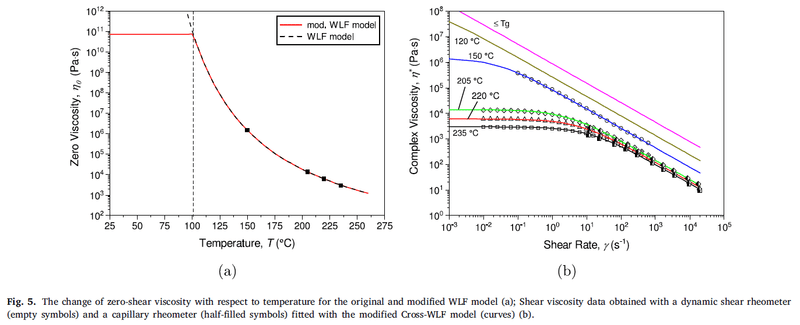
流量の限界を高めるにはどうしたらいいか?
より高い流量で、より速い速度でプリントしたい場合、結局のところ「フィラメントがノズルに到達するまでにガラス転移温度以上まで昇温しろ」というシンプルな結論になる。
例えばV6ホットエンドのメルトゾーン長さはおよそ16mm。プリンタ速度200mm/s(フィラメント送り速度6.6mm/s)ではフィラメントはおよそ2.5秒しか加熱されない。その2.5秒でフィラメントを可能な限り高い温度に加熱する必要がある。
つまるところフィラメントを加熱するために消費される 熱量(J) =仕事(W) x 時間(s) なので
仕事を増やすか、時間を増やすか、というシンプルな2択になる。
仕事を増やす
仕事 Q = 伝熱面の面積 S x 熱伝導率 h x 温度差 ΔT なので、どれかを改善すればよい。
◆CHTノズル
伝熱面の面積S を増やす方法はCHTノズルで実践されている。フィラメントとの接触面積を増やしている。
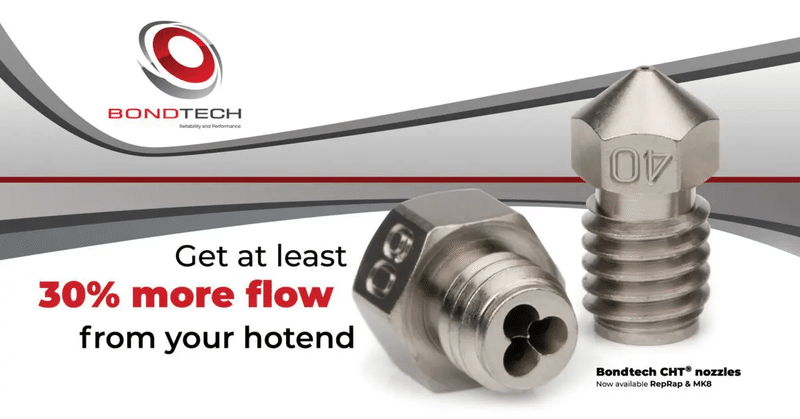
接触面積を増やす試みはほかにもあるのでURLだけ紹介しておく。
https://www.cnckitchen.com/blog/diy-high-flow-3d-printing-nozzle
熱伝導率は高温側と低温側の素材の組み合わせで決まるので工夫の余地は少ない。なお、温度差ΔTはノズル温度を高くすることで実現できる。
時間を増やす
◆メルトゾーンを伸ばす
大多数の「高性能」ホットエンドの方法論だ。メルトゾーンを伸ばすことでフィラメントと熱源が接触する時間を増やしている。
例えばVzbotから派生したGoliathホットエンドはヒートブロックが長く、V6ホットエンドと比べて3倍以上のメルトゾーンがある。ノズルはどちらも同じV6タイプが使われている。
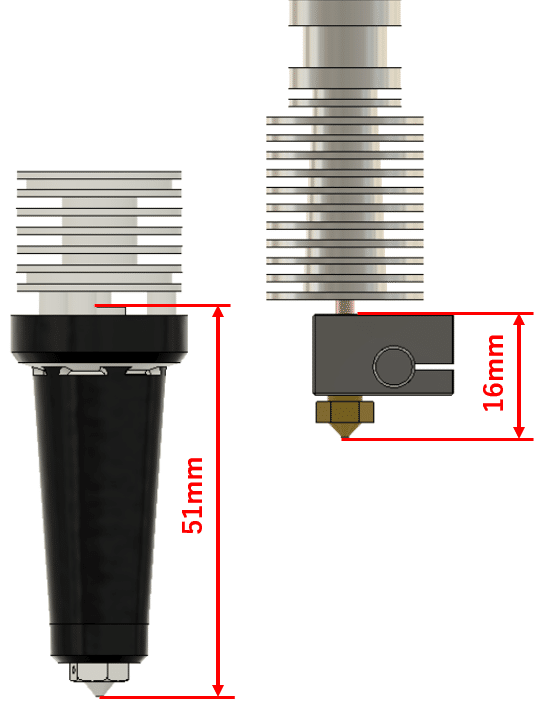
一方でメルトゾーン延長アダプターというものも売っている。
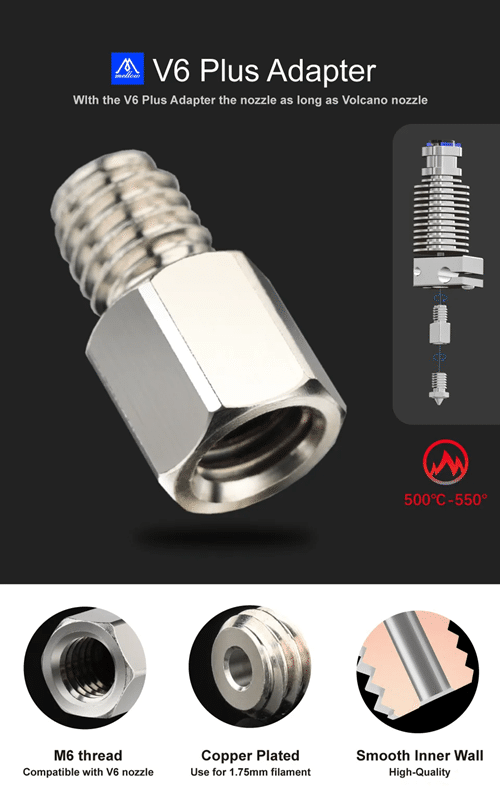
専用品を買わずともふつうのナットをはさめばまぁ別に機能するよねという話もある。
https://www.cnckitchen.com/blog/volcano-hotends-are-obsolete-just-use-nuts
Volcanoノズルなどの長いノズルもメルトゾーンを長くするための手段だ。
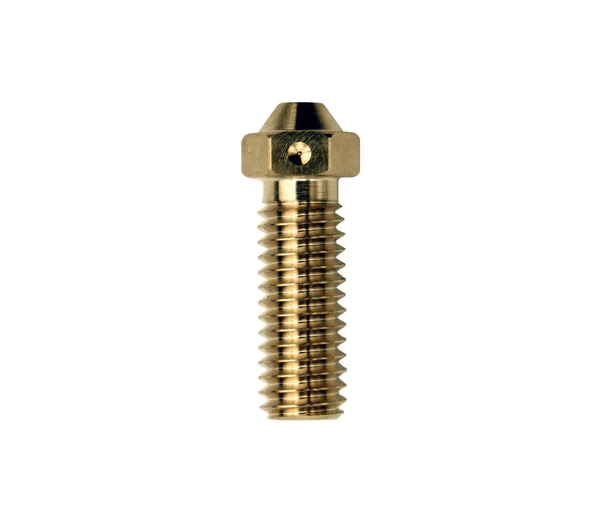
しかし最近のホットエンドではVolcanoノズルはあまり使われなくなりつつある。理由は単純で「別にノズルが伸びなくてもヒートブロック側が伸びればメルトゾーンを伸ばしつつ、安いV6ノズルが使えるよね?」という話だ。
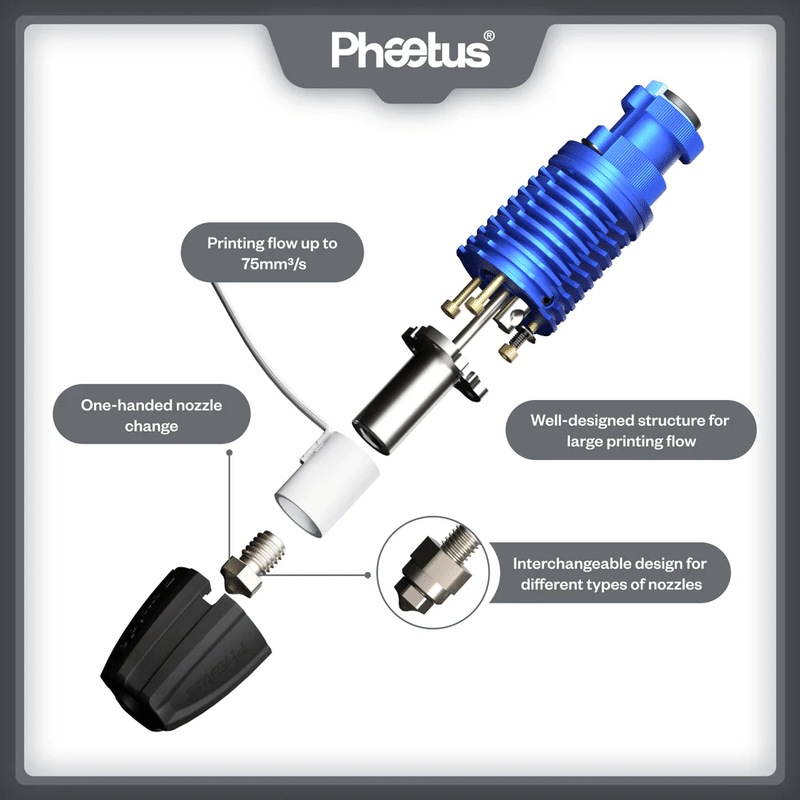
最後に主なホットエンドのメルトゾーン長さをまとめておく。
メルトゾーンの長さはすなわち最大流量を表すといってよい。
15~20mm:V6, mk8/10, CHC, Mosquito, E3D Revo
25~30mm:Rapido HF, CHC Pro,
Mosquito Magnum, TZ (K1, Bambu)
30~40mm:Rapido UHF(34mm) Mosquito Magnum+(39mm)
50~60mm:Goliath(51mm), STD6(55mm), Super Volcano (57mm)
60~ mm:Mosquito Prime(67mm)
まとめ
◆フィラメントはこんな感じに溶けながら押し出される。
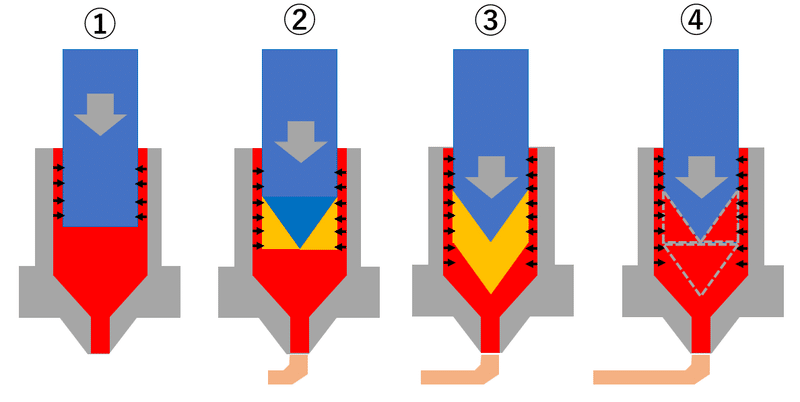
◆流量が高くなるとフィラメントが溶け切らず、温度が低く粘度が高い樹脂がノズルに詰まるので押し出されなくなる。
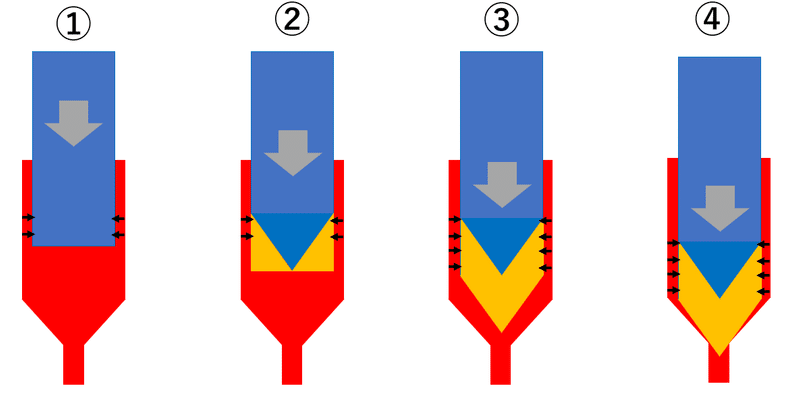
◆より多くのフィラメントを溶かすには2つの方法がある。
①メルトゾーンを伸ばす:ホットエンド交換 or アダプタ
②熱源とフィラメントが触れる面積を増やす:CHTノズル
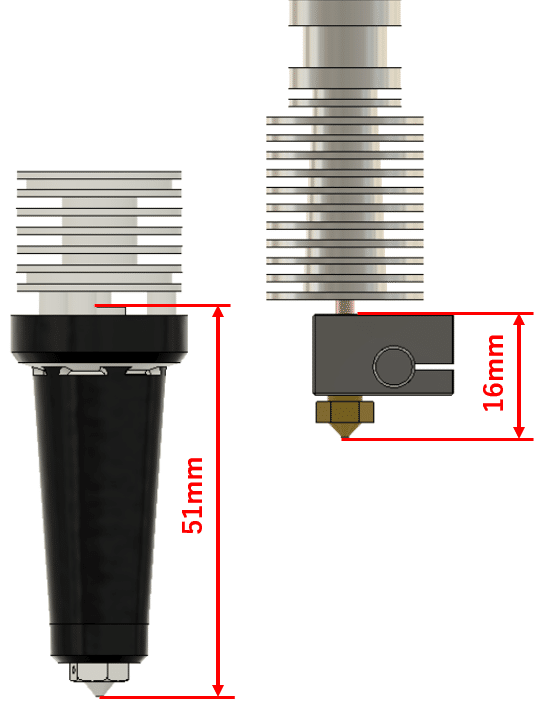
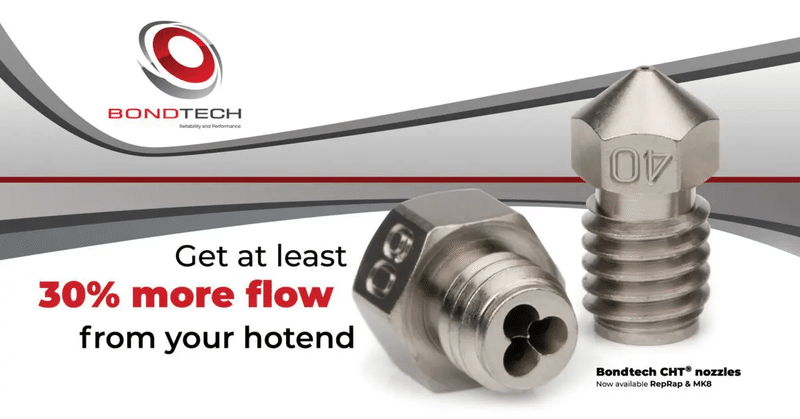
おまけ:空のノズルの中にフィラメントはどう充填される?
Nature3Dさんのわかりやすい記事があるので読んでください。
https://nature3d.net/explanation/clogging_region.html
この記事が気に入ったらサポートをしてみませんか?