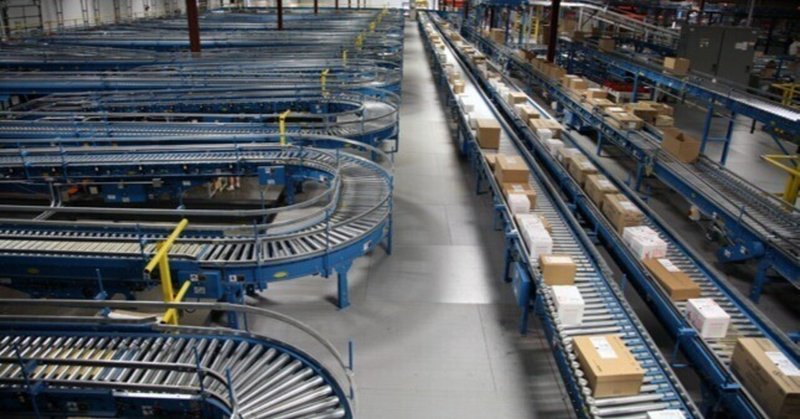
【カイゼン道場】作って終わりではない。SCMの重要性(下)
ここからはSCMを改善すべく、戦略について解説する。
5. SCM戦略
SCM戦略#1:生産方式
生産方式は大きく2つに大別できる。
・プッシュ生産方式
・プル生産方式
プッシュ生産方式は、需要予測に基づき生産計画を立て、それに従う方法である。在庫を前提とするため、欠品リスクは小さいが、需要予測が外れると在庫になるリスクがある。
一方のプル生産方式は、在庫を持たずに売れた分だけ生産する方法である。トヨタ自動車のジャストインタイムがこの代表例である。在庫は抑制できるが、リードタイムが長い製品では、欠品リスクを負うことになる。
どちらの生産方式が優れているというものではなく、製品種類・需要の変動幅から最適な生産方式を選択するものである。
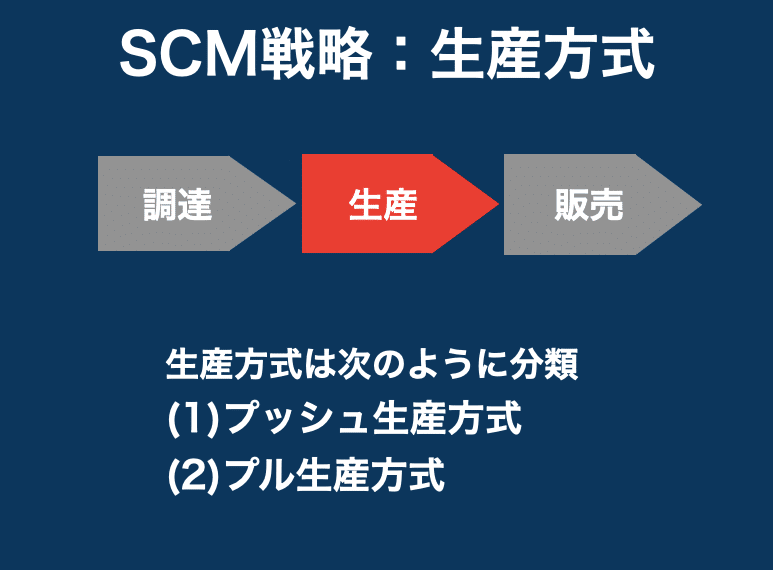
SCM戦略#2:プル・プッシュ混合方式
またプッシュ生産とプル生産を組み合わせる場合もある(下図参照)。製品の共通部分はプッシュ生産で、多様化をプル生産で行うものである。なおこの境界をデカップリングポイントと呼ぶ。
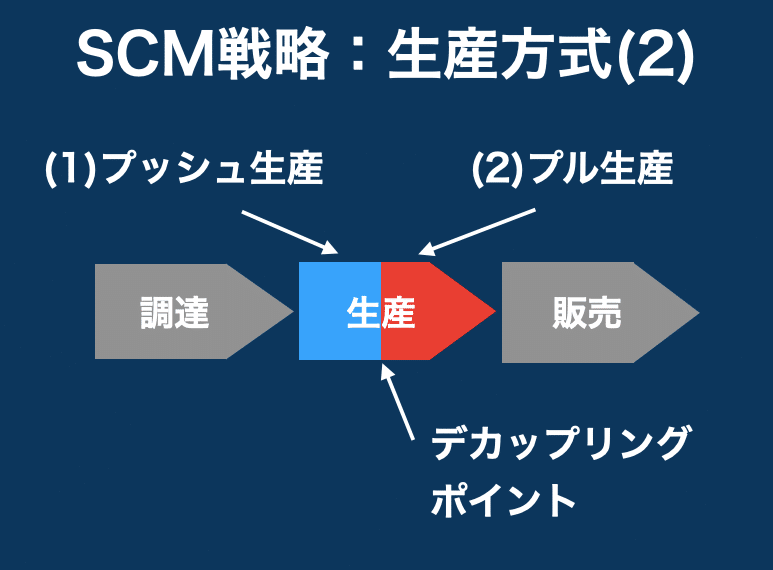
有名な事例として、ベネトン社の後染めセーターがある。白色のセーターを共通部分とし、計画的に大量生産で行う。一方で顧客への販売量に応じて、後染めでセーターの多様化を行う。
この方式を採用した理由は、どの色が、どのくらい売れるかは予測しづらいからである。しかし、セーター自体が売れる量は予想しやすいので、染色前の白色セーターにはプッシュ生産方式を採用する。
顧客の選択肢を増やすために様々な色で在庫を持つと、売れないものは不良在庫となる。そのため売れた分だけ、後染めで補修できるようなプル生産方式を採用した。また後染めならスループットが短いので、顧客要求のリードライムよりも短くできる。
なお、染色前のセーターをデカップリング在庫と呼ぶ。
こう書くと容易に聞こえますが、後染めができる商品作りや後染め工程などSCMに合わせた商品開発や生産工程を構築する技術が必要になる。
SCM戦略#3:ポストポーンメント
もう一つの戦略である。プル生産にあたる多様化を顧客近辺で実施するものである。輸送時間などを更に削減し、スループットを短縮する戦略である。これをポストポーンメント戦略と呼ぶ。
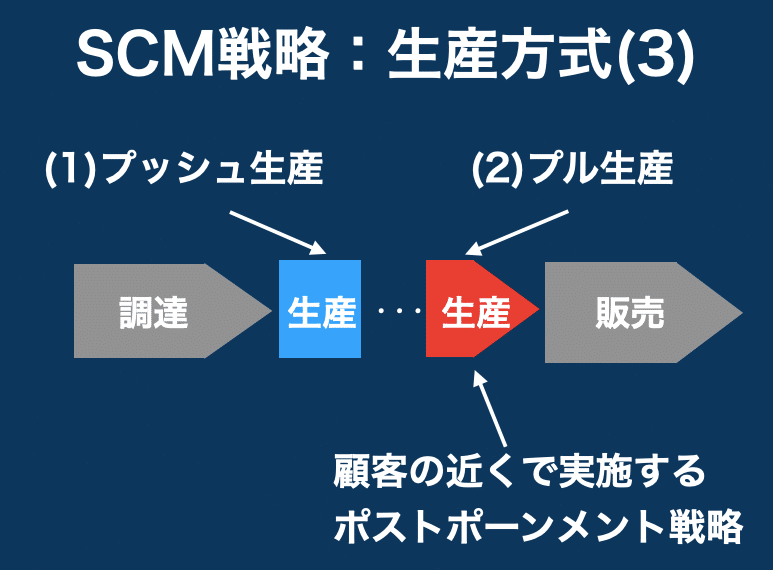
先ほどの後染めセーターを例に取ると、すべての生産を一拠点、例えば中国で行うと、米州・欧州への顧客には輸送期間分のタイムラグが発生し、スループットの短縮には限りがある。
そこで、中国では後染めできる白色セーターだけをプッシュ生産し、欧州の顧客向けにはハンガリー、米州の顧客向けにはメキシコ、といった顧客の近くで後染め工程を実施することで、スループットの短縮ができる。
6. ブルウィップ効果
(1)メカニズム
以前、「SCMを困難にする要因」で挙げた、「多段階意思決定における情報の劣化」について説明する。これは一般には、ブルウィップ効果や鞭効果と呼ばれるものである。
ブルウィップ効果を端的に言うと、個々の在庫点でロットまとめを行うと、上流の在庫点への発注ロットが徐々に大きくなる。それが繰り返されることによって在庫量が増幅し、まるで鞭のような振れ幅を描くのである。下記に具体的に示す。
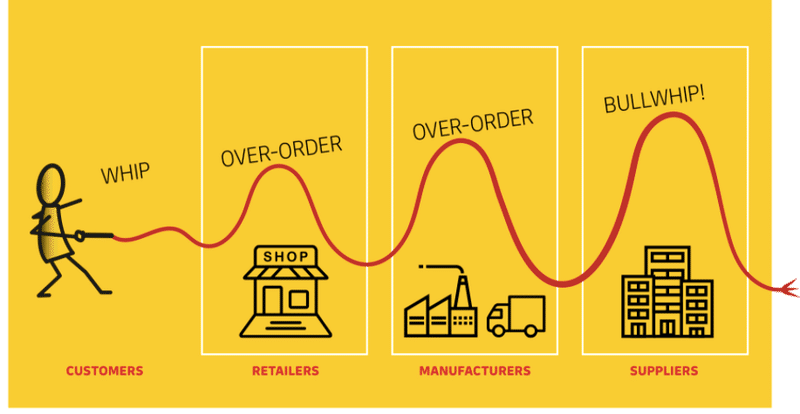
店頭→工場→サプライヤーからなるサプライチェーンとする。顧客が店頭で物を買うことが最初の変動を示す。
これが各営業拠点で集計され、次回配送が1週間先の場合、夫々の営業拠点で1週間先までを予測をし、1週間分の数量で工場に注文を入れる。この結果、工場での見かけの需要変動が図のように最初の変動幅から増幅された結果になる。
その先に目をやると、工場の生産計画が月次で、サプライヤからの納品リードタイムが1ヶ月先となると、工場も1ヶ月先まで予測を行い、1ヶ月分の材料を発注する。その結果、サプライヤーへの注文の変動幅さらに増幅した状態となる。
この増幅した様が鞭のように見えるためブルウィップ効果、又は鞭現象と呼ぶ。
これに対処するためには、在庫点間の情報の共有が必要となり、情報伝達のあり方を検討する必要がある。
(2)ブルウィップ効果の抑制策
このブルウィップ効果を抑制するための方法としてVMI戦略がある。VMIとはVendor Managed Inventoryの略で、ベンダー主導型店頭在庫管理と呼ぶ。
これは上流工程にあたるメーカーらが、直接小売の店頭在庫や物流センター在庫を管理する仕組みである。この方法のメリットは、店頭POS情報をタイムラグなく、EDI(電子データ交換 Electronic Data Interchange)でメーカーに提供することである。メーカーには売れた直後に補充情報が入る。そのため、情報の時間的劣化を抑制することができるのである。
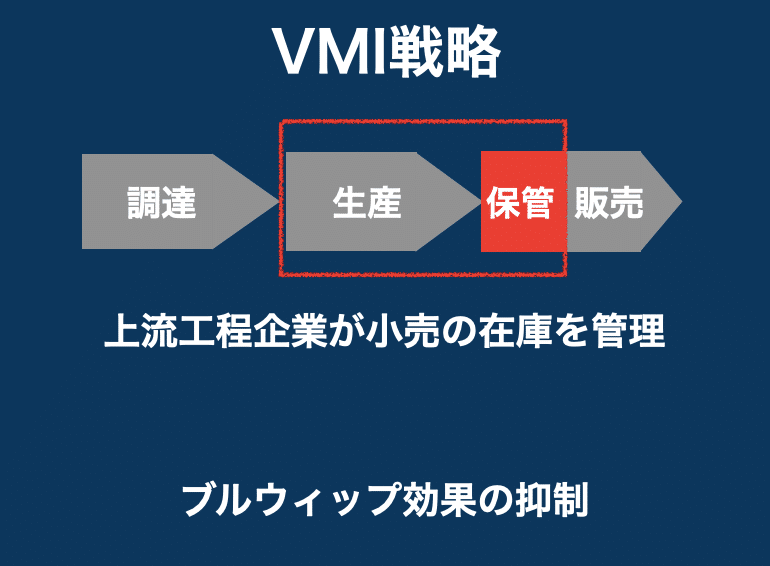
7. SCMが難しい理由
最後にSCMが難しい理由を述べる。原因は各部門が個別最適を目指そうとすることである。例えば、
生産部門:生産ロットを大きくし、段取り替え停止時間を少なくし、設備稼働率を上げる
物流部門:輸送効率を考慮し、ロットサイズを大きくしたい
販売部門:販売機会損失を防ぐために在庫を持ちたがる。
などだ。
これらを抑えて全体最適を目指すのは、トップの心構えが必要である。またSCM改善には、プロジェクト体制を取り、各部門からメンバーをアサインし、全体最適の実現させることが重要である。
8.まとめ
SCMは改善ではなく、「改革」である。時間はかかるが、効果は大きい。トップが率先し、腰を据えて取り組むべきである。
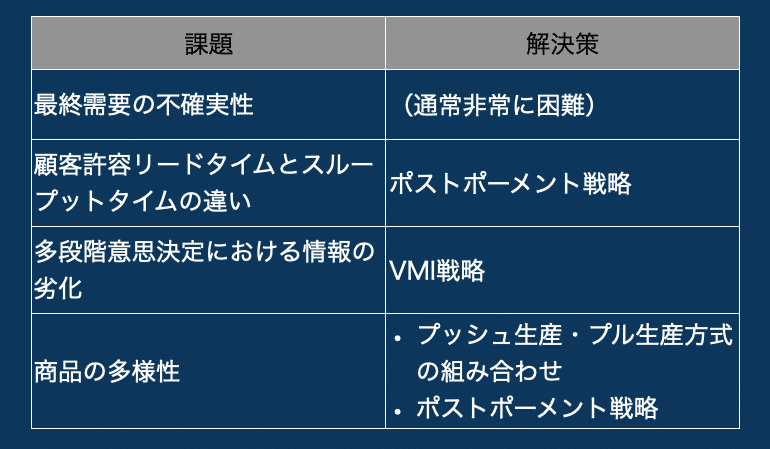
この記事が気に入ったらサポートをしてみませんか?