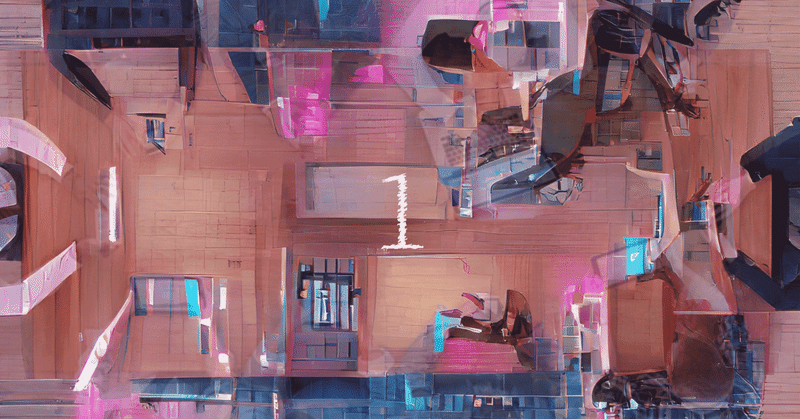
オフィスはデジタルツインになる(1/4)
1回 拡張したオフィス空間
デジタルツイン・オフィスとは
デジタルツインが持つ三つのルート
2回 PDCAに代わる業務フレームワーク
センシングが生命線
日常的管理でこそ生きるセンシング
3回 変わるオフィスデザイン
オフィスの「センシング」
デザイナーの役割が変わる
4回 「可視化」による貢献
ワーカーの「時間マネジメント」を支援
拡張したオフィス空間
「それでもオフィスに行く理由」を考えてきました。
すでにオフィスは、会社が一方的に人数分のスペースを用意する場所ではなく、ワーカーに選ばれてこそ存立できる場所に変わりつつありました。
また、分散社会の中で見通しを確保するため、デジタル空間上にオフィスが必要になり、フィジカルなオフィスと並存するようになっていました。
もはやオフィスに行く理由を考えるまでもなく、拡張したオフィス空間のなかにワーカーは取り込まれています。
デジタルツイン・オフィスとは
現実空間とデジタル空間を跨いだ世界を表す概念には、「デジタルツイン」「ミラーワールド」「CPS」などがあります。
新たなオフィスでは、ワーカーが2つの異なる空間を使い分けていくことになるので、「デジタルツイン」を使うのがふさわしいと考えています。
デジタルツインとは、現実空間で得た人・モノ・環境のデータをデジタル空間に移管して再現することを表します。また、言葉のニュアンスを大事にすると、すべての人やモノがオンラインでつながりデジタル空間で活動すると同時に、フィジカルな現実空間にも存立するという双子状態をしています。
人やモノが於いてある空間(=場所)が双子状に2つある状態が、デジタルツインです。
ここでは、デジタルツインとしてのオフィスについて、いくつかの角度から考えてみたいと思います。
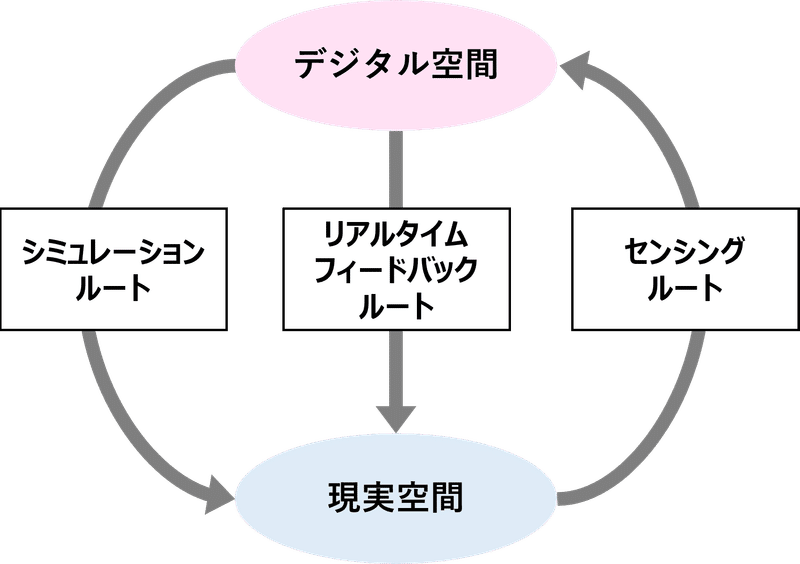
デジタルツインが持つ3つのルート
<センシングルート>
オフィスに限らずデジタルツインは、2つの空間をまたぐように3つのルートを持ち、そこには最低5つの機能が備わっています。
このように3つのルートが両空間をつなぎ循環させることで、両空間は一つの活動空間として人々の活動を支えます。
まず、必要になるのが、現実空間からデータを収集する「センシングルート」です。センシングとは、センサーと呼ばれる感知器などを使って様々な情報を計測して数値化することをいいます。
オフィスにおいては、各所にセンサーを設置し、また、ワーカーにもセンサーを持ってもらい、ワーカーや道具の位置やその時々の状態、そして温湿度や照度など室内環境の状態を、デジタルデータとして常時取得していくことになります。
デジタルツインの議論において、このセンシングは意外と軽視されがちです。しかし、技術的に最も難易度が高いのがこのセンシングです。
例えば、データサイエンスの実践において、データ取得に関するサイエンスやエンジニアリングの扱いは限定的です。
第三の「シュミレーションルート」を成立するためにも、データ取得のためのエンジニアリングに注力していく必要があります。
<リアルタイムフィードバックルート>
こうして取得したデータをもとに、現実空間にフィードバックしていくルート(上図でいえば下向きのルート)は2つあります。1つは「リアルタイムフィードバックルート」であり、もう一つが「シミュレーションルート」です。
「リアルタイムフィードバックルート」の第一の役割は、取得したデータを可視化することです。取得データを「屋内マップ」や「居場所リスト」に表示し、可視化します。こうすることではじめて、フィジカルなオフィスの実態を視覚的に捉えることができます。
このルートの第二の役割は、取得データをもとにしてサービスを生成しリアルタイムにワーカー等に提供することです。
例えば、このサービスとして「トイレ満空表示」があります。朝のトイレの混雑で困った経験を持つ人は多いと思いますが、トイレの扉等にセンサーを取り付けることでブース単位で満空を判断し、屋内マップに表示するとともに、オフィス内に満空表示看板を設置して、リアルタイム情報を提供するものです。
その他にもリアルタイムサービスは数多く提供されています。
<シミュレーションルート>
第三のルートが「シミュレーションルート」です。
「リアルタイムフィードバックルート」との違いは、取得したデータをその場で加工するか、蓄積データとして扱うかの違いです。
このルートは、製造業が先行し、牽引しています。
例えば、工場の増設を行う場合、モデル化した工場でシミュレーションを行うというものです。実際の工場を一度モデル化した上で、計画対象の製造施設をモデル上で増設し、施設稼働のシミュレーションを繰り返し、その結果を現実工場にフィードバックするというものです。
このことは、計画の精度を高めるだけでなく、計画の方法論や、PDCAなどの業務フィードバックの方法論を根本から変えるものです。
しかし、この製造業における画期的な計画論に隠れて、重要なデータ分析が軽視される結果になっています。
実際の製造業の工場は、多品種変動生産とか、変種変量生産といわれるように、様々なタイプの製品を製造するようになっていますが、機械稼働や特に労働時間といった製造原価を製品ごとに振り分けができていないのが現状です。
そのため、原価管理、生産管理、労務管理などの管理は大雑把にならざるをえず、管理が曖昧になり、これが生産性低迷の原因になっているといっても過言ではありません。
そこで、センシングルートを使いデータを製品単位にきめ細かく常時取得することが重要になります。そして、そのデータは、年に数回あるかないかの計画シュミレーションに使うというより、日常的な管理業務の重要情報として扱うことになります。これが生産性を向上させる手段となります。
いずれにせよ「シミュレーションルート」は、デジタルツインのメインルートです。しかし、製造工場の例のように、もう少し詳細に現状と課題をみていく必要があります。
そこで次回(2/4)は、この「シミュレーションルート」について検討していきたいと思います。
(丸田一如)