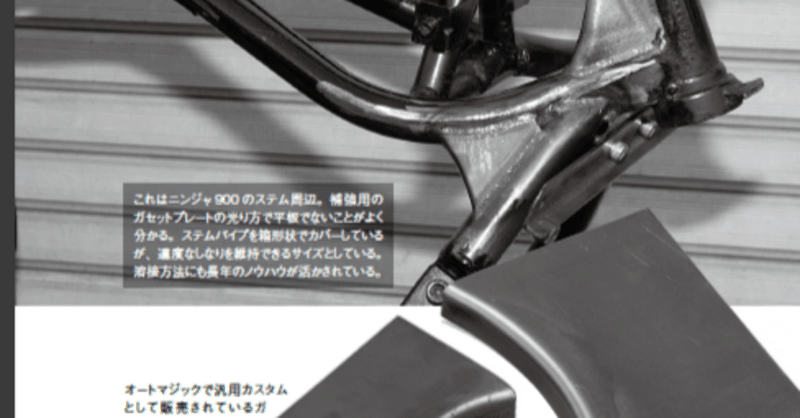
■AUTOMAGICイズム■ 第三章・フレーム補強にどんな意味があるのか?
昨今のカスタムシーンでは、エンジンのパワーアップや、タイヤやサスペンションのグレードアップとセットで考えられているフレーム補強。だが本当に補強が必要なバイクがどれほどあるのか、その効果を実感できるライダーがどれほどいるのか? 玉石混淆のカスタムバイク業界にオートマジックの荒木代表があえて問う。
全国のカスタムバイクショップで製作されたコンプリートマシンで、定番メニューのように行われるのが「フレーム補強」である。ショップ独自の経験やノウハウか、過去の有名なレーサーを参考にしたのか、はたまたバイク雑誌に掲載された他のショップのカスタム車からアイデアを拝借するのか知らないが、「チューンナップされたエンジンのパワーを受け止めるため、何十カ所の補強を入れました」的なコメントとともにその仕事ぶりを披露している。
見るからに弱々しい鉄フレームの絶版モデルに、太いラジアルタイヤや剛性の高いサスペンションを組み込むためにはフレームも補強して当然という感覚なのだろうが、ユーザーもバイクショップも本当にフレーム補強が必要だと思っているのだろうか? あるいは、フレーム補強とは何なのかという根元的な事項を理解しているのだろうか?
オートマジックとして20年以上に渡ってカスタムバイクを製作しながら「何を今さら……」と思う読者もいるかも知れないが、実際のところ巷に溢れるカスタムバイクを見ると、正直そう感じることが多い。フレーム補強とは、弱い部分を補うための「手段」であるはずなのに、いつの間にかそれ自体が「目的」となっているような風潮が蔓延しているように思えてしまう。目的のための手段であるはずが、手段自体が目的化してしまえば「何のために?」という根本的な部分が欠落してしまう。
ただ単に、やらないよりやった方がベターなんじゃないか、カッコ良く見えるからいいんじゃないか、というドレスアップ的な感覚で捉えているならそれでも良いだろう。だが、そう割り切るにはコスト的にもったいないし(作業項目として決して安い仕事ではない)、メリットだけではない可能性があることも、ユーザーは知っておくべきである。
ならば、オートマジックではフレーム補強をどう考えるのか。このテーマを語るには、前提として絶版バイクのスタンダードフレームの性能について触れておかなくてはならない。なんでもかんでもまず補強ありき、では他のカスタムショップと違わないからだ。
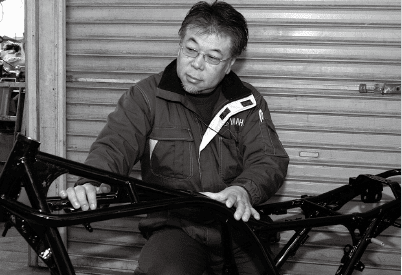
【ステムとスイングアーム交換でフレームの剛性感がアップする!?】
カスタム市場の人気絶版車といえば、今も昔もカワサキZ系が断然トップで、その周辺にニンジャやCB、カタナなどが点在する図式となっている。Zが製造された1970年代と現在を比較すると、環境や性能面で大きく異なるのが路面コンディションとタイヤだ。幹線道路の平均スピードが今ほど速くなく、グリップだって低かった路面を、剛性が低く細いバイアスタイヤのZで走ったところでサスやフレームが負けるほどの大荷重を与えることはできなかった。せいぜい、盛り上がったマンホールを乗り越えた時にハンドルや車体にオツリを感じる程度で、要するに当時はバイクの性能と走行環境がバランスしていたのだ。
ところがZやCBが絶版車となりカスタムの素材として注目されるようになった1980年代後半には、パーツのトレンドや走行環境が昔とは一変した。当時の最新モデルの純正パーツを流用したカスタムが流行り始めたのだ。その頃は現在と違って、足周りからフレームまで一気に改造というパターンは少なくて、最初はフロントフォークもスイングアームもZ用純正パーツのまま、ホイールとタイヤだけをアップデートするというやり方もポピュラーだった。
すると、太いタイヤとキャストホイールで見た目の迫力はアップしたが、相反してブレーキングやコーナリングでの車体の挙動が不安定になった。幅広で剛性の高いラジアルタイヤが路面から受ける力を、ノーマルのサスペンションとフレームが受け止められなかったのだ。
そこで次のステップとして、フロントフォークとスイングアームも新しい年代の純正パーツに交換、具体的にはZ1にヤマハFZR1000やスズキGSX -R1100の前後足周りを装着した。 すると、タイヤとホイールを交換しただけの時に感じた不安定な挙動はピタリと影を潜め、車体全体の剛性感が大幅にアップしたのだ。1990年代の初め、オートマジックではFZR1000やGSX -R1100用足周りを組み込ん
だZ1カスタムを数多く製作したが、街乗り主体のオーナーのほぼ全員がこの仕様のカスタム車に大満足してくれて、フレームの弱さを指摘されることはほとんどなかった。 車体の安定性が低下すると、すぐに
その原因がフレームにあるという人もいるが、実はこれが間違いであったことに我々自身も気づかされたのだ。
純正の足周りで、フレームのヨレとしてライダーを不安にさせていた原因は、フロントフォークのインナーチューブが貫通するアンダーブラケットだった。Z1の場合、アルミ鋳造製のトップブリッジとスチール製のアンダーブラケットが組み合わされているが、特にアンダーブラケットの剛性の低さが車体の挙動の不安定さを誘発していたのだ。
それを実感できる簡単な実験がある。Z1のアンダーブラケットにインナーチューブを差し込んでフロントフォークをこじってみると良い。アンダーブラケットが驚くほど簡単に捻れることが分かるはずだ。変形しやすいアンダーブラケットに比べて、アルミ製のトップブリッジは硬いため、インナーチューブは両者でしっかりクランプされて位置決めされているように見える。だが、走行中に加わる荷重によって、フロントフォークのストロークとは別にインナーチューブがアンダーブラケット自体を前後左右に押してしまい、それがステム周辺の剛性感不足を感じる原因となるのだ。
スイングアームも同様だ。Z1のスイングアームは当時としては一般的なスチール製の丸パイプで、純正タイヤとの組み合わせでは問題はない。だが、グリップ力が高く、構造的にも強固なラジアルタイヤを装着したことで、タイヤからアクスルシャフトに伝わる力は格段に増大する。直進状態でリアタイヤが地面に垂直に回転している状態から車体を傾け始めてから旋回に移行するまでの僅かの間、リアタイヤは直進状態を保とうとしている。グリップ力が高く、幅広化によってトレッド面のクラウン形状が緩やかなタイヤを装着することで、クラウン部をトレースする移行時間が長くなるため、アクスルと左右のアームの動きにズレが生じるのだ。その結果、スイングアームに旋回横Gが働いてリア周りの性不足を感じさせる原因となった。
GSX -R1100用の足周りを装着することでシャキッとした剛性感が出たのは、つまりGSX -R用の三つ又とスイングアームの剛性が利いていたわけだ。だからこそ、このパーツを装着しただけで、ほとんどのオーナーがフレーム補強なしで運動性能に不満を感じなかったのだろう。ちなみにアルミ製の角形スイングアームを純正装着した1100カタナの場合、180㎜サイズのラジアルタイヤを装着しても、リア周りがヨレることはなかった。これもまた、華奢に見える鉄フレームでも、スイングアームの剛
性が十分なら補強なしで使えることを示すエピソードである。
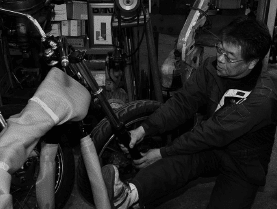
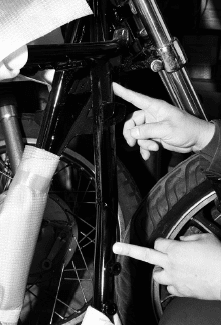
【チューニングマシンの潜在能力をアップさせるのがフレーム補強】
では、いかなる場合でもフレーム補強は必要ないかと言えば、そういうわけではない。車体に加わる荷重から考えて、街乗りにおいては必要がない、言い換えれば補強の恩恵を感じることは難しいが、サーキットのようなグリップ力が高い路面を走行したり、超高速でコーナリングをするような状況では、太いタイヤやグレードの高いサスペンションが受け止めた力がフレームに伝わり、フレームにストレスを与えるようになる。
そうした状況で感じられる不安定なうねり感や挙動が、フレームそのもののたわみである。また、エンジンパワーを極端に上げれば駆動系やエンジンマウント、スイングアームピボットに強大な力が加わり、それによってよじれやたわみが発生することもあり、このようなマシンの場合には適切なフレーム補強が効果を発揮する。
高速でのコーナリングの際、フレームに搭載された重いエンジンは旋回横Gによってダウンチューブ側に押しつけられている。この力が極端に大きくなるとフレーム自体がたわんでしまうが、それに至る前段階では一定量変化した後に元の位置まで復元しようとする。この変形と復元の動きが連続的に発生する時に、フレームのよじれやたわみとして認識できるわけだ。
塑性変形と弾性変形という言葉を聞いたことがあると思うが、走行中のフ
レームにはエンジンやサスペンションから、いくつもの方向の力が加わっている。厳密に言えば、フレームはいつも外力を受けて弾性変形を繰り返しているが、サスペンションやタイヤでは吸収できないほどの外力が加わったり、エンジンやライダー自身が過大な荷重となった時に、フ
レーム自体が大きく弾性変形を起こすと考えると、よじれやたわみを理解する一助となるだろう。
文頭で、フレーム補強を行う際には目的が必要だと書いたが、この弾性変
形の特性を変えることこそがフレーム補強の目的である。同時に、街乗り中
心の走行ではフレームを変形させるほどの荷重を与えることが難しいという
のが、すべてのカスタムバイクにフレーム補強が必要ではないと僕が考える理由である。
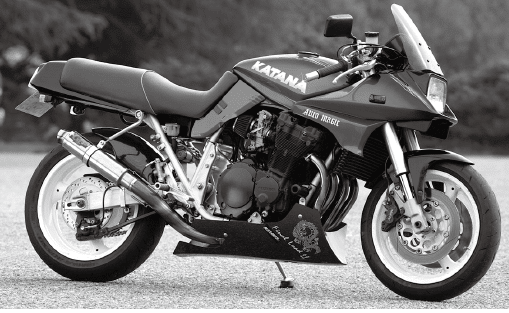
ただその反面、グレードアップした足周りやパワーアップしたエンジンのパフォーマンスを最大限に発揮させることを前提に、あらかじめフレームを補強しておくこと自体は、マシン全体の潜在能力を高める点では有効だと思う。 最近では走行性能向上というより、皆と同じ標準カスタムのために行われているように思えるフレーム補強も、いろいろと奥が深いことが分かるだろう。そこで次ページでは具体的なフレーム補強の位置や方法、さらにあまり知られていない功罪についても解説しよう。
【衝撃を効果的に分散させるのがフレーム補強の真髄】
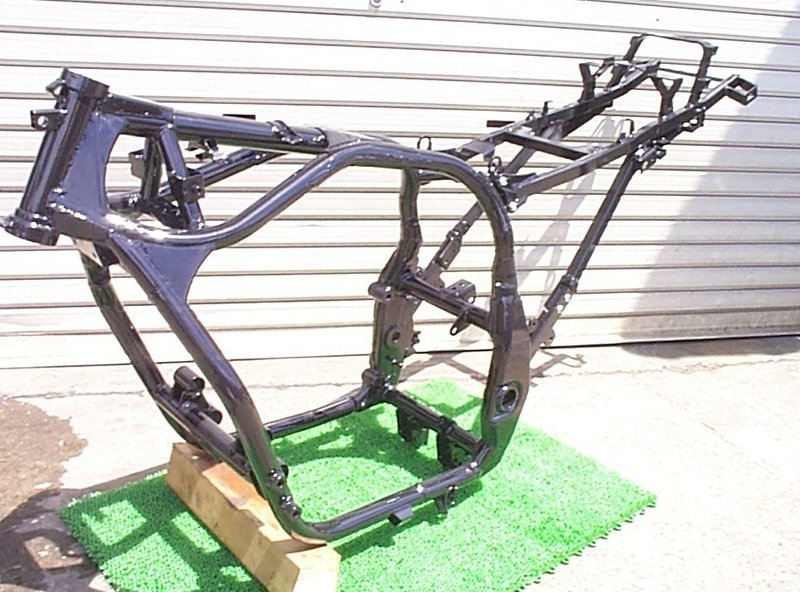
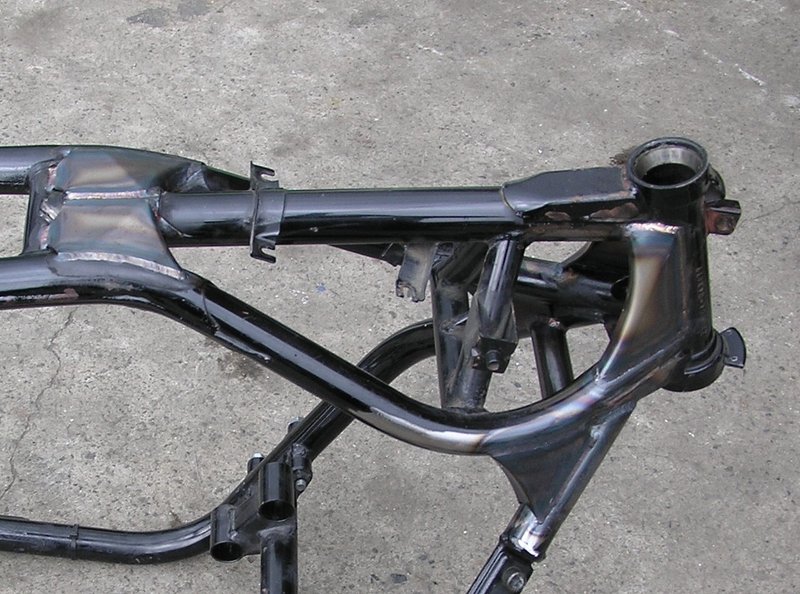
スタンダードのZ1フレームにFZRやGSX -Rの足周りを装着するだけ必要十分な性能を得られることが分かり、前述の通りオートマジックでは多くのカスタムマシンを製作した。フレームの溶接加工は必要最小限に押さえる選択は、溶接によって余計な熱を加えない、フレームの再塗装を省けるなど、機能面や製作面などいくつものメリットがあった。とはいえ、サーキット走行やレースを見据えたチューニングを行う上では、フレーム補強が必要になるのも明らかだった。
オートマジック開業当初、周囲にカスタムバイクショップはほとんど存在しておらず、フレーム補強といっても参考になる作例はごくわずかだった。そんな状況で補強作業を進める際に役立ったのは、自社内でフレーム修正を行うことで蓄積した実績とノウハウだった。カスタム時にはフレームジグとして活用した自作の修正機は、開業から5年間ほどサーキットや一般道での転倒車両のフレーム修正用としても活用しており、大きな衝撃による様々なダメージを見ることができたのだ。現在カスタムショップの看板を掲げるショップでも、修正を通じてフレームの特性を実体験したところは少ないのではないだろうか。
当時は鉄フレームのCBX400FやZ400FXからアルミフレームのTZRやFZRまで多くのバイクを修正した。30㎞/hで転倒した車両と100㎞/hでぶつかった車両では、フレームが受けるダメージは当然まったく異なり、同じ30㎞/hでも当たり方や当たり所によって想像以上に深いダメージを負うことも、現物を通して知ることができた。
転倒したバイクが他のクルマや縁石、壁面に衝突する際、その衝撃は車体の弱い部分を壊しながら変形していく。フロントから突っ込んだ場合なら、フォークが折れ、ステムが曲がり、ステアリングヘッドパイプが変形する。最終的にフレームが変形する際も、ハンドルの切れ角や車体の姿勢によって、変形の仕方も実に様々だった。スチール製のアンダーブラケットが想像以上に軟らかいことや、ステアリングステムが車体の剛性感に重要な役割
を果たしていることも、そうした経験から分かった事実である。
そして、数多くのフレームを修正していく過程で、衝撃を受けたフレームがどのような部分にストレスを蓄積するか、言い換えれば弾性変形が塑性変形になりやすいのはどのあたりかということが、徐々に見え始めてきたのである。我々が体得したフレーム補強のノウハウは、外部から力が入った結果を見ることで、そこから逆に補強すべきポイントを見つけるという方法で、これは一般的なバイクショップではまずできないやり方だ。当時はバイクメーカーの衝突テスト以上に損傷後の車輌を分析・解析してきたと思うし、しかも観察、解析するだけでなく試行錯誤しながら直してきた。
こうしたノウハウにより、オートマジックでは他のショップとは異なる、独自のフレーム補強方法を開拓できたのだ。
【折り曲げ、カールしたガセットで複数方向からの力を受け止める】
具体的なフレーム補強ポイントとしてよく知られるのが、ヘッドパイプ周辺である。ダブルクレードルフレームならバックボーン部とアンダークレードル部のパイプが集合する部分で、フレームにとって要となる箇所でもある。
絶版車の純正タイヤとフロントフォークはいずれも細く、加わった荷重をそれぞれのパーツで吸収して逃がすことができたが、カスタムによって太いタイヤとフォークを装着することで路面からの荷重がまともにフレームに伝わるようになった。走行中のヘッドパイプにはフロントタイヤやフロントフォークから力が加わり、前後左右あらゆる方向にスリコギのように動いている。その動きは目視確認できるほどではないが、それぞれのパイプが起こすバラバラの弾性変形を適度に規制することで、ヘッドパイプ周辺の剛性感を確実に向上させられる。 補強に用いる部材として一般的な材料
がガセットプレートである。フレームパイプが交差や接合する部分を広範囲で強化する事を目指し、今まで定番だったパイプ補強の「点」から「面」への補強に変えた。さらには単なる平面補強ではなく、オートマジックが立体強化タイプにしたのがガセットのボックス形状化である。
部位によってガセットプレートを折り曲げ多面化することで、突っ張り棒の役割とねじれの方向の力に対しても動きを規制できるようにした。
特にステムパイプ周りの補強は、単純な平板ではなくパイプ部分を抱え込むような手法で補強を行い、複雑な動きを多面的に規制できるように工夫を凝らしている。フレームが交差するような構成の部位やメインフレームのアール形状のパイプ間に多くの面を介在させながら一方向以外にも効果が発揮される。
当初市販化する際に、この補強材はネーミングもされておらず各雑誌メディアに聞き回ったが誰も的確な答えが得られず、クルマのモノコックフレームの補強方法に似たものがあったのでバイク業界でも『ガセット補強』として市販化した元祖である。今では多くのカスタムバイクショップがこれを定番手法としている。
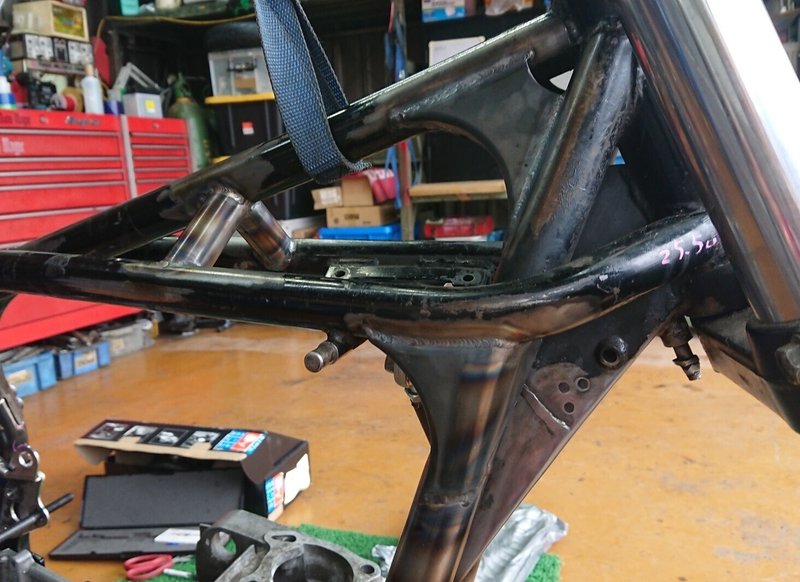
【フレーム補強の真髄は加わった衝撃の「分散」にあり】
こうしたフレーム補強で我々オートマジックが目的としているのは、入力した外力の的確な「分散」である。フロントフォークを通じて伝達された力がステムパイプに加わると、エンジン上方のバックボーンを通じてスイングアームピボット部に向かって進む。ここでステムパイプ部分だけをガチガチに固めてしまうと、受けた力をバックボーンに分散できず、硬くて乗り心地の悪いフレームになる。フレームが持つべき弾性まで阻害されてしまう。
フレーム補強というと、どうしても補強する部分に注目しがちだが、重要なのは強い部分と弱い部分を意識しながら、衝撃や応力をフレーム全体にきれいに分散させて、妙に突っ張ったり跳ねたりせずに元に戻るように仕上げることだ。こうしたテーマを考える時、僕が引き合いに出すことが多いのが釣り竿や自転車のフレームである。いずれも適度なしなりを持たせることで機能を果たしていることは、考えてみれば分かるはずだ。釣り竿から魚の引きを受け止めつつ逃がすしなりを廃してしまえば、竿が折れるか糸が切れるしかない。
カスタムバイクを製作する際のフレーム補強も同様で、いたずらに頑強な補強箇所を増やして固めれば性能が向上するというのは大間違いだ。固いだけのフレームは乗り心地が悪く、タイヤやサスペンションへの依存度が高まり、限界を超えてしまった時の挙動が速くなりすぎるきらいがある。
こんなことを考えながら作業を行っているショップがどれほど存在しているのか分からないが、実は見よう見真似で行われたものも少なくない。実際「どう見てもコレはまずいだろう」と言った施工例も数多く見てきたし、やり直してきた。先に書いたように、絶版車に現行モデルの足周りを装着するだけで想像以上の効果があるため、フレーム補強の効果があまりなくても、バイクの走りが良くなってしまい、さらには一般的な技量のライダーが街乗りする程度ではその恩恵を正しく理解することは難しいため、ショップ側も効果の有無がはっきりしないまま作業しているという場合も多いのだ。
太いリアタイヤを装着するためにバイクのフレームの肝心要の左ピボット部分を削るザグリ加工も、今ではカスタムの手法としてはポピュラーになった手法ではあるが、ピポット部の厚さを半分になるほど削り落として左右均等の強度が確保できるわけがない。バイクという乗り物のほとんどは、車体の全重量をピポットシャフトで受けて、車体を押して前進している。そしてリヤアクスル、カウンターシャフト、車両重心などなどに対して最も重要な存在がピポットの位置や強度であることを知っておくべきだ。
【カスタムするなら功罪両面を理解したい】
ショップもユーザーもよく分かっていないフレーム補強は、毒にも薬にもならないならまだしも、やり方次第で毒になってしまうこともある。
第一の注意点はフレームに加わる熱だ。ガセットを装着する際に溶接熱が加わることで組成が変化し、本来の粘りが低下して溶接部周辺が割れやすくなる。ガセットを貼り付ければ貼り付けるほど、フレームパイプの強度にムラができてしまうのだ。またガセット溶接部にTIG溶接のビード跡をしっかり残そうと頑張って過剰に熱を入れてしまうと焼きなまし状態になり軟化してしまう。さらにビードと母材の境界部分に小さな溝ができて、これがクラックの原因になってしまう。施工にはさまざまなノウハウが必要なのだ。
第二の注意点は、溶接時に避けて通れない素材歪みの問題だ。溶接を行うと、冷却方法によっては素材が引っ張られて歪みが出ることは知られているが、そのセオリーを無視して数多くの溶接箇所を追加すれば、フレームがどう変形するか想像もつかない。最悪のケースは、フレームの左右を片面ずつまとめて補強してしまうパターンである。ステムパイプ周辺~バックボーンであれば、右側ばかりにガセットを溶接し続ければ、ステムは右に振れてしまう。そしてこの状態から左側をまとめて溶接しても、必ずしもステムが車体中心線に戻ってくるかどうかは分からない。お客様から儲ける為に施工項目を増やしたあげく、イジリ壊しては意味がない。
金属の特性を把握した切開、再生、補強はショップの腕の見せ所だ。最低条件の必要なスキルを持って施工するべきなのだが、フレーム補強後にバイクが真っ直ぐ走らなくなってしまったという例も少なくない。ユーザーはバイクショップで行う作業現場を実際に見る機会は少ないだろうから、いろんな情報でそのショップの技術レベルをリサーチして見極める能力も求められる。オートマジックではDFC -フレームの製作工程で沢山のフレーム切断することを経て、むやみやたらに入れたフレーム補強が大きなストレスを与えていた事例も知ることができた。もちろん、ノーマルフレームだとして
も例外ではない。
それ以前に、フレームの曲がりも修正もできないまま作業するショップがあるのも大きな問題である。オートマジックではフレームジグ上で溶接後の歪みも抜いた上で仕上げているが、修正機を持たずにフレームに溶接を行った後、どのようにつじつまを合わせているのか是非とも聞いてみたいほどである。また、フレームジグを自作して設置したとしても、それだけではフレーム修正はできない。
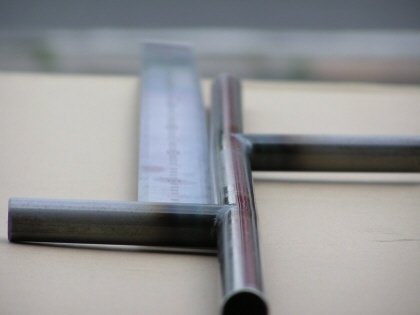
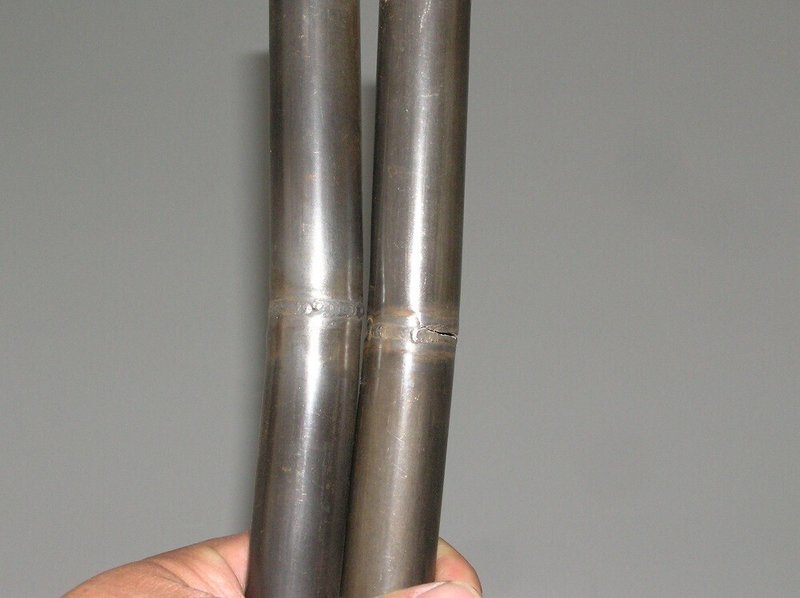
我々もまだまだ勉強中ではあるが、カスタムショップの中のいったいどれほどが、フレーム補強を本当に理解し施工しているのだろうか。レースでもストリート用のカスタムでも、デメリットを感じないから効果があるというのは正しい論法ではないはずだ。我々も自らのノウハウである真髄部分を明かすことはできないが、それでもここで紹介したような功罪を挙げることはできる。ただ格好だけ真似してドレスアップ補強をしているショップには、もっと研究してオリジナルのテクニックを生み出してもらいたい。 ボルトオンカスタムから一歩高みに踏み出したようなイメージでフレーム補強に憧れを抱くカスタムファンも少なくないようだが、何故フレーム補強を行いたいのかという目的意識をしっかりと持った上で、確かな技術力を持ったショップを見極める目を養うことも重要だろう。
【フレームパイプの厚さを非破壊検査する】
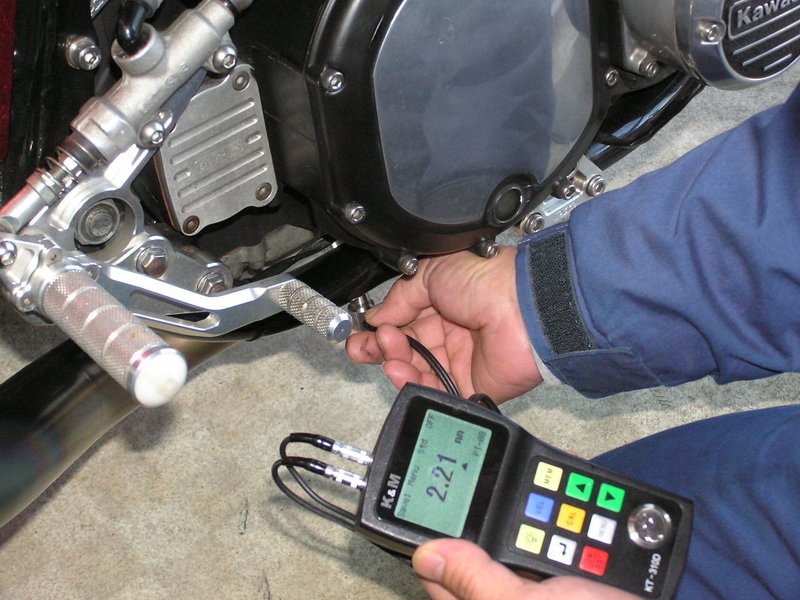
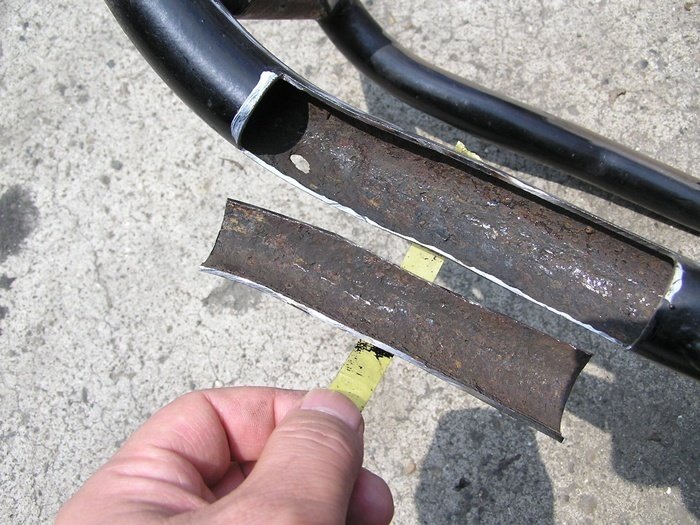
この記事が気に入ったらサポートをしてみませんか?