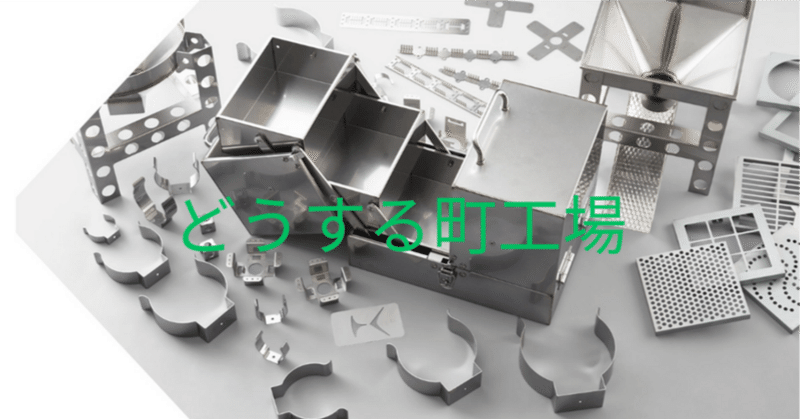
ジョブローテーション:燕三条の町工場の一例
先日、曲げ工程専属のスタッフが、新型コロナウイルスに感染して、1週間ほど休みました。その助っ人として、10数年ぶりにベンダーを扱いました。他の作業者にセッティングしてもらって曲げることはたまにありましたが、自身でセッティングするというのはひさしぶのことです。
機械メーカーは同じアマダ製ですが、昔と比べNCが異なっています。タッチパネルも少しずつリニューアルされて、変更点の方が多いくらいです。
ベンダーは金属の板を折り曲げる機械です。板の厚みによって使う金型が異なってきます。てこの原理を使って折り曲げるので、およそ5倍くらいのV字の台の上に材料を乗せ、上から90度より少し鋭角な金型で押します。V幅が小さい方が負荷が大きくなりますし、V幅が大きくなると負荷が少なくて済みます。但し曲げた部分がぼやけたようになりがちです。
今回私が担当したのは機械の部品で、同じ板厚で似たような形状なものを各1点ずつ数十種類曲げるというものでした。
私が展開図を作成し、プログラムを組んでいる案件ですから、プログラムを作っている段階では折り曲げを想定して、可能な形状を作っているつもりでした。
いざ、曲げ工程に携わってみると、その様変わりに驚いてしまいました。以前はベンダーの金型をセットする際は、上のパンチと下の台をかみ合わせて、既定のトン数をかけて芯をだし、その地点をD0と定義します。それから金型を開いていきながら、どれくらの隙間にすると金型が板を嚙むのか。その後、少しずつ空いた隙間を閉じていきながら、求める角度に折り曲げていきます。NC化されたことでおおよその位置は自動算出されるようになっていました。
現在のベンダーは使用する金型を登録すると自動で位置を算出してくれるため、金型合わせが不要になっていました。但し、誤って間違った金型を登録してしまうと不良の原因になります。
曲げ工程や干渉の有無など画面上で確認できますが、機械の制限値を超えるような無茶な曲げはNCにはねられてしまいます。突き当て部も定かではなくケガキ線に合わせて折り曲げる場合などは、自動で積算された突き当てが明後日の方に行ってしまっていました。
プログラムを組む際にはなんとか形にできると踏んだものでも、実際曲げてみると、いや、とっても曲がらないわ、といったものも複数ありました。
ジョブローテーション
別の工程を体験すると、それまで見えていなかった別の角度から製品を見る事が出来ます。プログラム、曲げ工程だけに限らず、製品ができるまでには複数の工程を経る必要があります。それぞれの工程が特定の担当者が担っているため、知見が高まっていきます。またそれに呼応するように別の工程が見えなくなる傾向にあるようです。
様々な工程を経験することで複眼的な思考が育まれます。視野も広がり、全体を通して製品の加工過程をとらえる事が出来ます。そしてひいては多能工の育成にもつながっていきます。
毎日、同じ製品を代わり映え無く作っていれば、とりたてて新たな技術の習得など必要ないかもしれません。しかし現実は均衡縮小のサイクルの中にあり、ボリュームのある定番商品も最高到達点を超えると徐々に下落していく傾向にあります。どのような商品もいつかは無くなってしまう恐れがあります。かといって新規・新規と飛びつくわけでもなく、現状から少しずつできること・守備範囲を広げていければと思います。
この記事が気に入ったらサポートをしてみませんか?