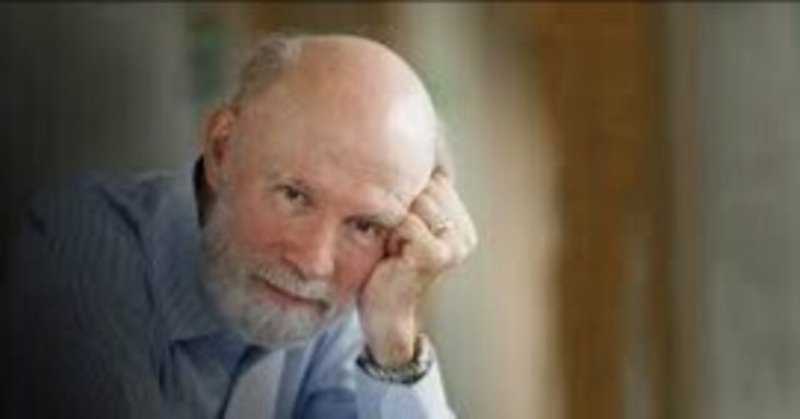
トヨタの秘密 by J.P.ウォマック②
「短期的な儲けでなく、共存共栄の仕組みを作る」
モノもカネもない状況でムダ削減のため知恵を絞るとしても、最終組み立て工場は、工程全体の一部です。1万個以上の部品を作る部品メーカーとの協力も必要でした。大野耐一は、部品メーカーとの関係も徹底的に見直しました。
米国の自動車会社は、部品設計図を作って部品メーカーに渡し、期限を示して競争入札させた上で、最安値メーカーに発注していました。
大野は「この方法はだめだ。部品メーカーの改善や提案意欲を削いでしまう。長期的なお互いの利益も考えなくなり、短期的な儲けを追求するようになる。私たちは共存共栄の仕組みを作る必要がある」と考えました。
大野耐一は、部品メーカーをグループに分けて別々の役割を割り振り、具体的な目標(たとえば、時速100キロで走る車を60m以内で止めるブレーキ。コストは一個15000円)を与えました。
そして、部品メーカー同士で協力して改善策を探るようにさせました。部品メーカー同士は、お互い別々の部品を作っていて競合しないので、積極的に協業を始めました。
「リーン生産方式の本質と実証」
リーン生産方式は、アメリカの大量生産方式と比べて、圧倒的に低コストかつ高品質でした。
ジェームズ・ウォマックは米国のGMフレミンハム工場(大量生産方式)とトヨタ高岡工場(リーン生産方式)の生産性と品質を調査し、比較しました。
結果は、高岡工場のほうが組み立て時間は半分以下、欠陥は3分の1、在庫はGMの2週間分に対し2時間分でした。
トヨタ高岡工場はムダがありませんでした。全作業員が組み立て作業に集中し、作業員の脇には最低限の1~2時間分の在庫品があるのみ。
また、GMでは、ライン停止権限を持つのは上級幹部だけですが、トヨタの作業員は誰でも問題を発見するとラインを止めていました。作業員は「いい車を作る」という目的意識がありました。
私たちは「トヨタ生産方式を実践できるのは、日本人が勤勉だから」と考えがちですが、そうではありません。
ウォマックは、トヨタとGMの合弁企業の工場(NUMMI)でも同じ調査をしました。NUMMIはGMの古い工場を使い、元GM従業員が80%。トヨタから来た上級幹部がトヨタ流で工場を運営しました。このNUMMIの品質と生産性は、トヨタ高岡工場と全く同等でした。
リーン生産方式の本質は以下の3点です。これらを実践できるかどうかがカギとなります。
① 作業の責任を、車に価値を付与する現場作業員にできる限り移譲する。
② 欠陥を発見したら、原因を徹底究明するシステムを持つ。
③ ダイナミックなチームワークを持つ。
以上の3点です。米国のみに生産拠点を作っていたトヨタは、現在は、メキシコ、南米、欧州、アフリカ、中国、東南アジアに工場を持ち、現地従業員がトヨタ生産方式(リーン生産方式)を実践しています。
弱小自動車会社だったトヨタは、フォードやGMから大量生産方式を徹底的に学び、「大量生産方式は使えない」と結論付け、トヨタ生産方式を生み出しました。今や、リーン生産方式(トヨタ生産方式)は、まったく異なる分野にも広がっています。
「トヨタ生産方式の概念」
トヨタ自動車のクルマを造る生産方式は、「リーン生産方式」、「JIT(ジャスト・イン・タイム)方式」とも言われます。
最も短い時間で効率的に造ることを目的とし、長い年月の改善を積み重ねて確立された生産管理システムです。
トヨタ生産方式は、「異常が発生したら機械がただちに停止して、不良品を造らない」という考え方(トヨタではニンベンの付いた「自働化」と言っています)と、各工程が必要なものだけを、流れるように停滞なく生産する考え方(「ジャスト・イン・タイム」)の2つの考え方を柱として確立されました。
「自働化」と「ジャスト・イン・タイム」の基本思想によりトヨタ生産方式は、1台ずつお客様の要望に合ったクルマを、「確かな品質」で手際よく「タイムリー」に造ることができるのです。
トヨタの考える「自働化」、すなわち異常が発生したら機械が止まることの実現には、安全な仕事が確実にできるまで手作業で作り込むことが大切です。
まず人がとことんこだわって手作業でラインをつくり込み、改善の積み上げで作業を簡単にしていきます。
そして、最終的には人間の付加価値がなくなるレベル、つまり誰がやっても同じ作業になるようにしたうえで、それらの作業を「自働化」やからくりで実際の量産ラインに織り込んでいきます。
これを繰り返すことで、機械は簡単な仕組みでかつ安くなり、またメンテナンスにかかる費用や時間も低減、さらには生産量の増減に対応できる「シンプル・スリム・フレキシブルなライン」が可能となるのです。
「ジャスト・イン・タイム」
この「手作業」こそが、技能の原点です。機械やロボットは自ら考え、勝手に進化したわけではなく、匠の技能を移植することで進化することができたのです。
つまり、手作業を通じてモノづくりの原理原則を知り、現場で応用することで改善を積み上げていくと、それが「匠の技能」となります。
この匠の技能に磨きをかけ続け、同時にその匠ならではのカン・コツを機械に織り込む新技術・新工法にチャレンジし続ける「技能と技術のスパイラルアップ」がトヨタの「自働化」です。
お客様の満足感に応えるためには、人間の知恵や工夫が欠かせません。自ら考え、改善に結びつけることができる人材を今後も育て続けることに徹底的にこだわっていきます。
生産ラインには異常を知らせる作業員がいて、異常が見つかると、異常が知らされる「アンドン」といわれる表示盤に示されます。
「ジャスト・イン・タイム」、それは、「生産性の向上」を意味する言葉であり、言い換えれば、「必要なものを、必要なときに必要な量だけ造る!」という精神でもあります。生産現場の「ムダ・ムラ・ムリ」を徹底的になくし、良いものだけを効率良く造るということです。
ムダの徹底的排除の思想と造り方の合理性を追い求め、生産全般をその思想で貫き、システム化したトヨタ生産方式は、豊田佐吉の自動織機に源を発し、トヨタ自動車の創業者(2代目社長)である豊田喜一郎が「ジャスト・イン・タイム」による効率化を長い年月にわたり考え、試行錯誤の末に到達したものです。
その根底に流れているものは「徹底したムダの排除」の思想です。これがウォマックを驚かせ、世界を驚かせた根本精神です。
この記事が気に入ったらサポートをしてみませんか?