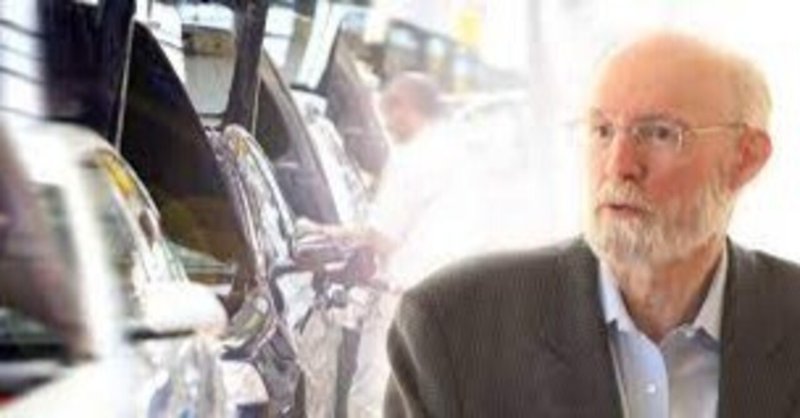
トヨタの秘密 by J.P.ウォマック①
「トヨタの秘密を暴露した驚異的な本」
今や、世界一といってよい自動車メーカーの「トヨタ」は、なぜこのような成長を遂げ、高品質の自動車を作り続けることができたのか。自動車大国、自動車王国であるアメリカは日本から押し寄せるトヨタの輸出する自動車が素晴らしいものであることを、1980年代に気づき、徹底的にトヨタ自動車を研究しました。
その結果、トヨタの秘密が判明し、それを一冊の本にして世に出しました。それが、ジェームズ・P・ウォマックとダニエル・T・ジョーンズ、ダニエル・ルースなどの共著による『リーン生産方式が、世界の自動車産業をこう変える。』(1990年)という書籍です。
世界11か国語に翻訳された本著を、世界の人々はむさぼるように読み込んでいきました。高品質を生み出す製造業における「ヒミツ」が、細かく、的確に書かれていたのです。モノづくりの匠の技の伝統を誇ってきた日本の精神やシステムがいかなるものであるかを、世界の企業人たちはこの本から学びました。
「無駄を省くトヨタの精神」
ジェームズ・ウォマックの名前は、『リーン生産方式』の本により、一躍、世界中に知られることとなり、彼は、その本の改訂版を2007年に出版しています。トヨタ生産方式をリーン生産方式と命名したその意図は何であったか。
「リーン」(lean)には「贅肉がなく引き締まって痩せている」という意味がありますが、その意味のごとく、トヨタ生産方式は、無駄を徹底的に排除しているという点に最大の特徴があります。
無駄を省くには、何が無駄であるのか、何が無駄になっているのかを知る必要があります。
機械は「言われたとおりに(仕組まれたとおりに)」動くしかありませんから、何が無駄であるかを発見するのは、人間であるはずです。
「無駄の発見」がなければ、無駄を省く方法も出てきません。機械任せの製造工程で、何が起きるかを鋭く見張る人間の存在がものを言います。
一見、スムーズに流れている生産工程のように見えても、トラブルが発生するときがあります。そのとき、機械は動き続けるのではなく、その異変を感知し、合図を出さなければなりません。
そして、そういうとき、機械は一時的に、停止する必要があります。そのまま動き続けていると、不良な製品がどんどん作り続けられるということになり、そういう部品を最終工程の組み立て作業の中に組み込んでいくと、最終完成品は完成品ではなく、不良品になり、出荷できなくなります。
今、一例をあげましたが、最高品質を目指す精神があれば、また顧客が満足する商品をお届けする精神があるならば、異変を察知したところで、その原因を探り、修正を加える作業に取り掛からなければなりません。
不良品を作るために機械を作動させ続けることはできません。こういう無駄をトヨタは、主なものとして、7つを掲げました。
生産現場の7つの「ムダ・ムラ・ムリ」は、①加工のムダ、②在庫のムダ、③不良・手直しのムダ、④手待ちのムダ、⑤造りすぎのムダ、⑥動作のムダ、⑦運搬のムダ、
この7つの頭文字を読み、「かざふてつどう」(カザフスタン鉄道?)と暗記して、現場に潜む7つの無駄に対処するのです。現場作業員たちの注意深さと熟練度が重要であることは言うまでもありません。
「ウォマックはトヨタのリーン生産方式を世界に発表!」
ジェームズ・ウォマックは、ハーバード大学で修士、MIT(マサチューセッツ工科大学)で、日本、ドイツ製造業比較研究」によって博士の学位を取得し、MITで教授として、教鞭をとりました。
日本社会で生まれたトヨタ生産方式が、「リーン生産方式」としてグローバルに展開され、さらに、製造業の枠を超えて、様々な分野で応用されるようになった現実を知るとき、日本人がトヨタ生産方式を知らずにいるのは、非常にもったいない気がします。
ウォマックが、トヨタ生産方式を客観的にアメリカと比較分析し、そのすごさを徹底解明してくれたことは実に有難いことでした。
ウォマックは、『リーン生産方式が世界の自動車産業をこう変える』の中で、車の生産は、①手作り生産方式 ⇒ ②大量生産方式 ⇒ ③リーン生産方式の流れで発展してきたと述べています。
手作り生産方式は、19世紀末までの車作りです。大量生産方式は、20世紀初頭、ヘンリー・フォードがT型フォードの生産で実現しました。
リーン生産方式は、まさに、トヨタが開発したものであり、トヨタ自動車を世界の頂点へと押し上げた究極の生産方式と言えるでしょう。
「アメリカ式のムダ、トヨタ式のノームダ!」
1950年代から60年代、当時のトヨタは今とは違って、戦後に車の生産を始めたばかりの自動車会社で弱小と言ってよいものでした。
1950年、若き技術者の豊田英二(のちのトヨタ自動車会長)は、米国フォードの工場を視察し、3か月間ですべてを学び取りました。
「生産の天才」と呼ばれた大野耐一も、デトロイトの自動車工場を何度も訪れていましたが、この二人は、「米国の大量生産方式はムダだらけだ。まだまだ改善できる」と言い、まったく同じ感想を持ち帰りました。
そうは言っても、当時の日本経済は戦争で壊滅して、お金もなく、最新設備を導入した大量生産方式を真似るなど、到底無理な話で、ないない尽くしの状態が偽りのない現実でした。
ゆえに、徹底的に知恵を絞り出すしかなく、トヨタが考えた方法は、米国のように工作機械を大量に設置して部品を作るお金もなく、当時、トヨタの生産台数は数千台だったので、1台の工作機械を血が滲み出るような創意工夫をして使いこなし、車を組み立てるために必要となる様々な部品を作らざるを得ませんでした。
このお陰で、コストが下がりました。必要な部品だけ作るので在庫コストが消えます。組み立て前に作る部品が少ないため、ミスもすぐ目に入って気が付きます。作業員は以前よりも品質に気を配るようになり、不良部品が大量に出回ることもなくなりました。
「問題が起きたら即ラインを止めよ」と、大野は指示を出し、早めに不良品を見つけて問題を解決するので、コストは大きく下がります。出荷する完成品の品質も向上し始めました。
リーン生産方式は、モノもカネもない状況でムダ削減のために知恵を絞るところから始まったものでした。
アメリカは派手に工作機械を並べて作りながら「不良品は最後に見つけ出して直せ」と命令し、不良品を大量に出していました。ムダが多く、コストも跳ね上がっていました。日米、ムダに差が出たのです。
この記事が気に入ったらサポートをしてみませんか?