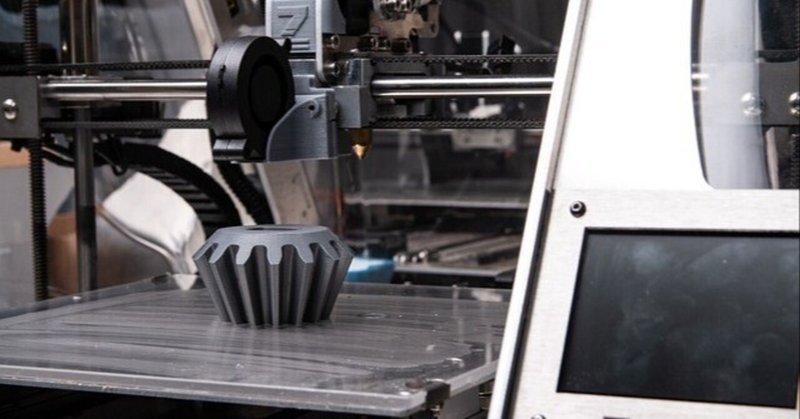
3Dプリンターを利用するデザインに慣れていく
直前の記事で自転車用のパーツを3Dプリンターでいくつか造ってみて、ちょっとずつですが3Dプリンターに適したデザインがなんとなくぼんやり感じられるようになってきました(随分自信のない表現になっていますが)。
私はどうしてもこれまで経験のある製法の考えに囚われています。良く使う製法としては、板金と樹脂成形(インジェクション)で、どちらも板厚、肉厚が一定になる形状が基本となります。樹脂成形であればボリューム感のある形状も外観としては可能ですが、製法としては肉厚一定ですし、抜き勾配や部品の分かれ目やPLを常に気にしておく必要があります。
これらと全然違う製法として、樹脂や金属の切削、鍛造や鋳造などもありますが、これも形状としての制限がいろいろあります。ブロー成形など私が経験したことのない製法もありますが、いずれにしてもこれまでのデザインや設計の蓄積が、私の常識として活かされてもいれば自由な発想を縛ってもいると思います。
(何も知らない方が自由な発送ができて良いデザインになるという考え方には反対です。国際政治を経験していない外務大臣の方が、自由な発想で理想的な国際社会を実現できるのでしょうか。色々経験して知って、それを乗り越えてこそ、良いものを生み出せると思います。)
3Dプリンターで造るものは、今までの常識が通用することもありますが、大きくガラッと考え方を変える必要もあります。積層式であったり、内部の構造(ラティス)の自由度が高いなど、板金と切削ほどの製法による違いがあります。
これまでの考え方とは違っていると頭では分かっていても、でもやっぱり手(考えるのだから頭ですが)は今までと同じ方法を踏襲しようとします。このあたりは実際にデザイン・設計をしてみて、現物になるのを確認して、改良点を見つけて反映させてみる、の繰り返しをしないと身(頭)につかないのでしょう。
弊社のクライアントさんの設計部の方の多くは3Dプリンターを使用するようになっています。すでに設計はすべて3Dになっており3Dデータはあるので、3Dプリンターでどんどん試作を作られています。でも今のところインジェクションで製作する部品の試作としての3Dプリンターの利用になっていることがほとんどです。
一般的な製造現場としては量産として3Dプリンターを活かす段階には来ていないと思いますが、このあたりの技術の進み方は早いので、あっという間に3Dプリンターを量産でも利用する状況になると思います。そして各メーカー、設計者が試行錯誤しながら3Dプリンターに適した形状や構造の経験を積み、ノウハウが貯まっていき、それが業界で共有されていくことで、
ますます3Dプリンターで造る量産品が一般的になっていくことが容易に想像できます。
さらにジェネラティブデザインと3Dプリンターの相性はとても良いので、また設計手法としても全く違った考え方も必要になりそうです。
楽しみな状況ですが、私個人は着いていくのに必死です。
この記事が気に入ったらサポートをしてみませんか?