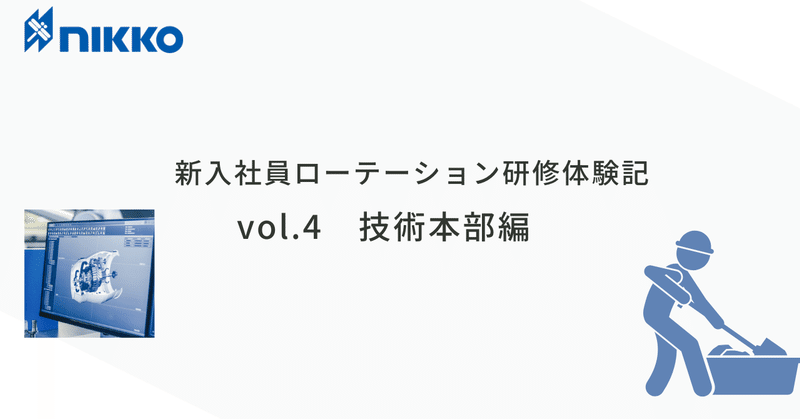
新入社員ローテーション研修#4 技術本部編
広報SOです('ω')ノ
「新入社員による、ローテーション研修体験記作成企画💮」
第4弾として、技術本部研修(2週間)の体験記を営業部門に配属予定の新入社員に作成いただきましたので紹介します。
1週目
1日目 開発1・4・5課
バーナー関連の開発を手掛ける開発1課では、バーナーやキルンの構造のほかに、水素やもみ殻を燃料として用いた次世代機開発の説明を受けました。聞けば2050年までにCO2排出量実質0を実現するとのこと。
「プラントが排出したCO2は、先進技術で責任をもって処理する」と宣言されているのが印象に残りました。
おっ男前すぎる。。。メーカーの矜持😎を感じ取りました
その後はバーナーの加熱?の火の軌道??をシミュレーションしているところを見学させていただきました。
はい。お察しの通りあまり理解できませんでした😅
いつか理解できるよう、日々邁進していきたいです!
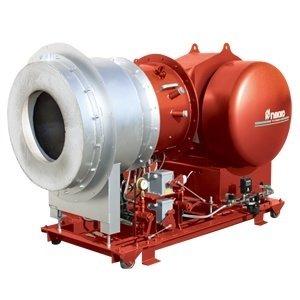
1~3課の構想を応用して新製品を生み出す4課では、「オカモチくん」をはじめとした絶賛開発中の製品の説明を受けました
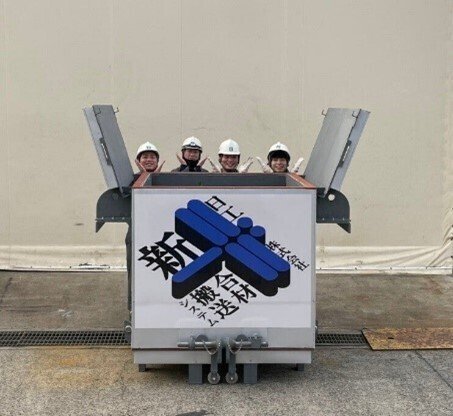
オカモチくんの開発経緯や試行錯誤の数々を聞くのは純粋に楽しかったです!
実物を見てみたいなぁ~。
▼オカモチくんの記事はこちら!
開発5課では特許等の知的財産の管理について学びました。
新たに開発した技術の特許申請や、その技術が今ま で他社や自社の特許と重複していないか調査をしています。
膨大なデータの中から出願調査をする苦労は、お話を聞いてるだけでもひしひしと伝わってきました😳
2日目 開発2・3課
ミキサを手掛ける開発2課では、ミキサの構造やコンクリートの作り方の説明を受けました。
そして、ホバートミキサでセメントペースト作りを体験させていただき、スランプフローを測りました!
混和剤を入れた場合、入れなかった場合の2パターン実験を行ったのですが、混和剤を入れると粘度も強度も格段に上がりびっくりしました😲
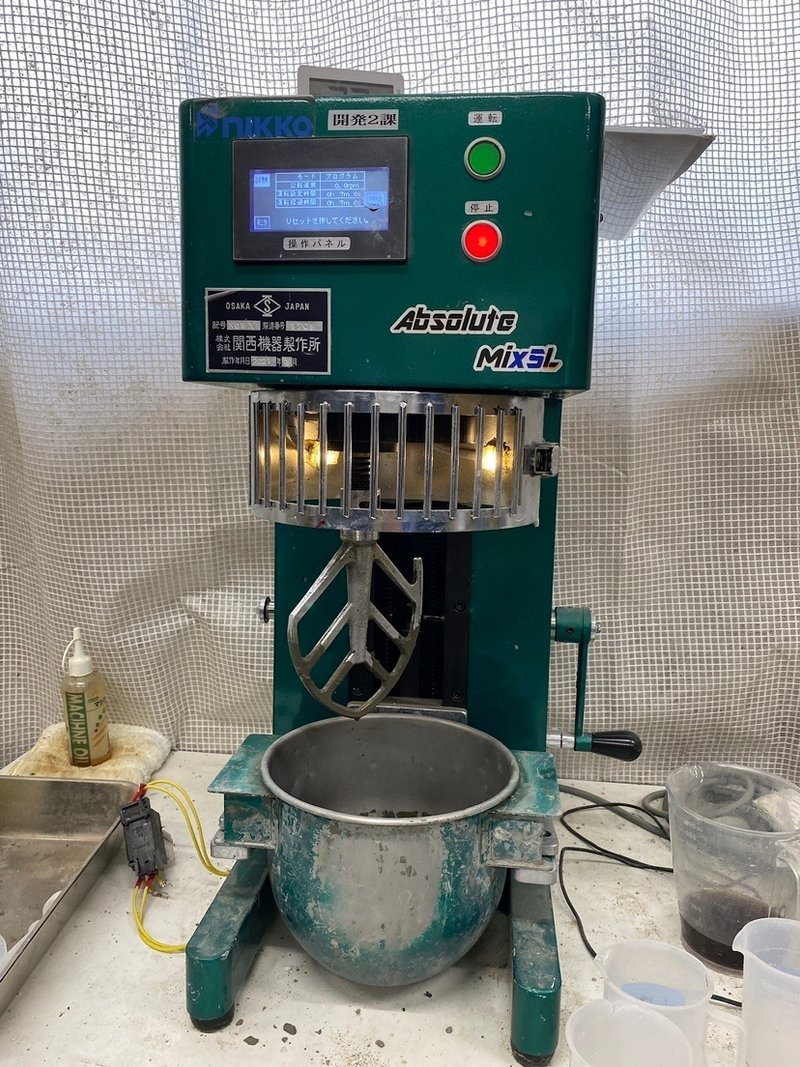
百聞は一見に如かず。
実験から1か月半たった今でもセメントペーストの作り方は脳裏に焼き付いています😀
センサを取り扱う開発3課では、アスファルト再生材の性状測定センサ等多くの製品を絶賛開発中であると説明を受けました。
業界の人材不足を補うため、プラントもDXが進んでどんどん発展していっているんですね😳
「一歩先行くエンジニアリング」体現のため、日々技術を磨かれている部署だと感じました!
3日目 機械設計1・2課
アスファルトプラントを担当する機械設計1課の方々からは、
長年の試行錯誤の末に、「Value Pack (VPシリーズ)」が生まれたことを聞かせていただきました。
トップシェアであることに胡坐をかかず、他メーカーが目を背けがちだった環境問題にいち早く目を向け、技術を磨き続ける姿勢に感動しました!
私も日工とともに成長していかなければ!
機械設計2課の方々からは、バッチャープラント(BP)の構造を設計図(CAD)を交えて解説していただきました。
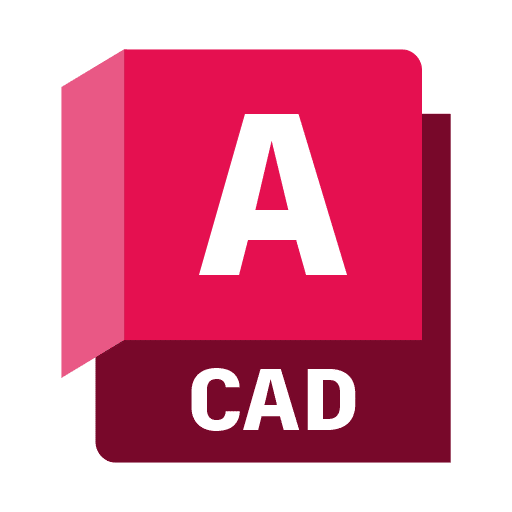
設計図には複雑に線と数字が入り乱れていて、何が書いてあるか全然分かりません。。。
おれ文系だから理解できんかぁ~🙄とか言い訳を考えていると
「君たちもCAD使えないとダメだよ」と言われ絶句😨
営業配属とはいえ、メーカーの社員ですから当たり前な話ですね。
がんばって学んでいきたいと思います✊!
4日目 機械設計3課、一級建築士事務所
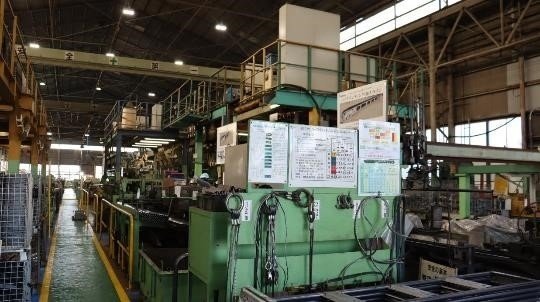
ベルトコンベヤや環境製品を取り扱う機械設計3課では、工場見学にたくさん連れ出していただきました!
日工のベルコンはモジュラーコンベヤと呼ばれるもので、様々な地形・用途に対応しており、単品はもちろんプラントとセットで年間数千台売れていきます😲
そのため工場もライン化しており、溶接や裁断はロボットが行っているんです!
「PETRIS」というペットボトルと缶を選り分ける製品についても紹介していただきました。
聞けばリサイクルセンターの人材不足を解消したいと営業部の方が提案し
開発、製品化に至ったとのこと。
ドラマチックですね☆彡
~PETRIS実験体験記~
<準備物>
A:スチール缶・アルミ缶・ペットボトル
B.Aをラベリングした箱
<実験>
①ペトリスにAを入れ、選別する。
②Aが正しいラベルの箱に何個入っているかを計測、おおよその選別率を算出
<結果>
実験時は、仕分けを行うエアノズルや箱の配置の影響などにより、あまり選別率は高くありませんでした。
そのため、まだまだ改良の余地があると思いました。
一級建築士事務所での担当者からのお話はとても印象に残っています。
建築士の視点からプラントの構造計算、法令遵守の面でサポートなされている方で、
働く心構えとして「大型建機を取り扱う中で『売れればいい』という思考は持たないでほしい。人の命も預かることを忘れないで。」というお言葉をいただきました。
営業としてもこの気持ちだけは忘れず、仕事していきたいです。
5日目 日工電子工業株式会社
1週目最終日は本社を飛び出してピクニックに行きました!🥪
というのは冗談で、グループ会社の日工電子工業株式会社(京都府長岡京市)にお邪魔させていただきました。

最寄駅(長岡京)から歩いて20分ほどの所にあり、いい運動になりました🙄
各種プラントの制御盤や、新製品の遠隔制御装置「Remoop」を実際に見せていただき、貴重な体験となりました。
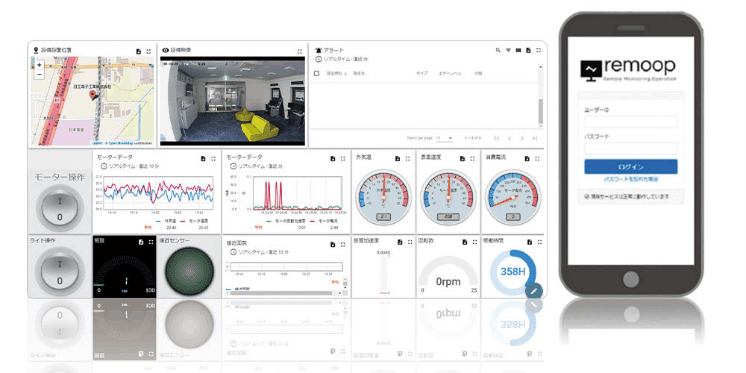
制御盤はもちろん、今後はRemoopも売れ筋の商品となるので営業として知識を付けておかないといけませんね!がんばります✊!
1週目終了です😎
2週目
1日目 EG1課 グローバル推進課
この日はエンジニアリング部の研修で、EG1課とグローバル推進課の研修を
受けました。
EG1課は、AP(アスファルトプラント)関係にて、技術部の窓口となり見積もりや図面の作成を主業務として行っているとのこと !
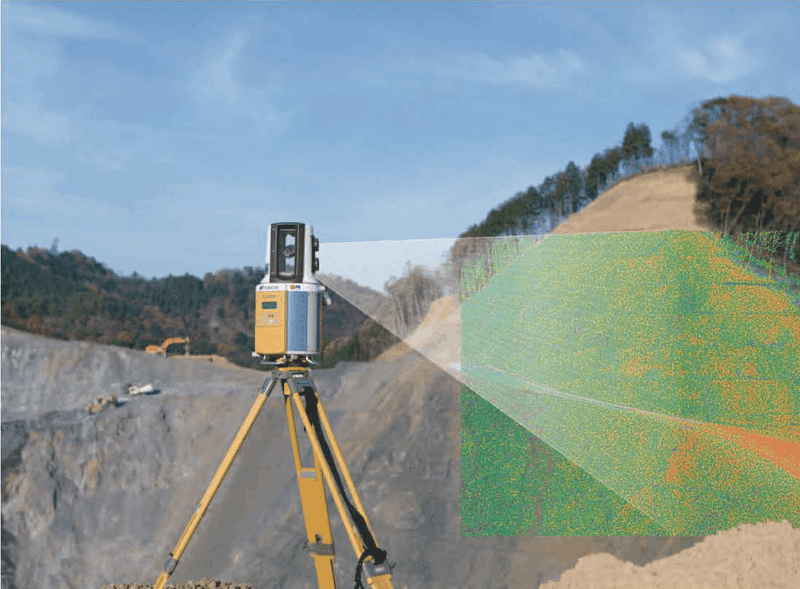
この日の研修では3D測量を体験させていただきました!
図面を作成する上で現地の測量が必要で、そこに活躍するのが3D測量です。
グーグルマップのストリートビューのようなものが作れます!
自分が写り込まないように測量しないといけないのですが、後から確認するとしっかり自分が写っていました、、とても楽しかったです!
グローバル推進課は海外市場を拡大するための部署で、直接現地に行き市場調査などを行っているそうです🛫
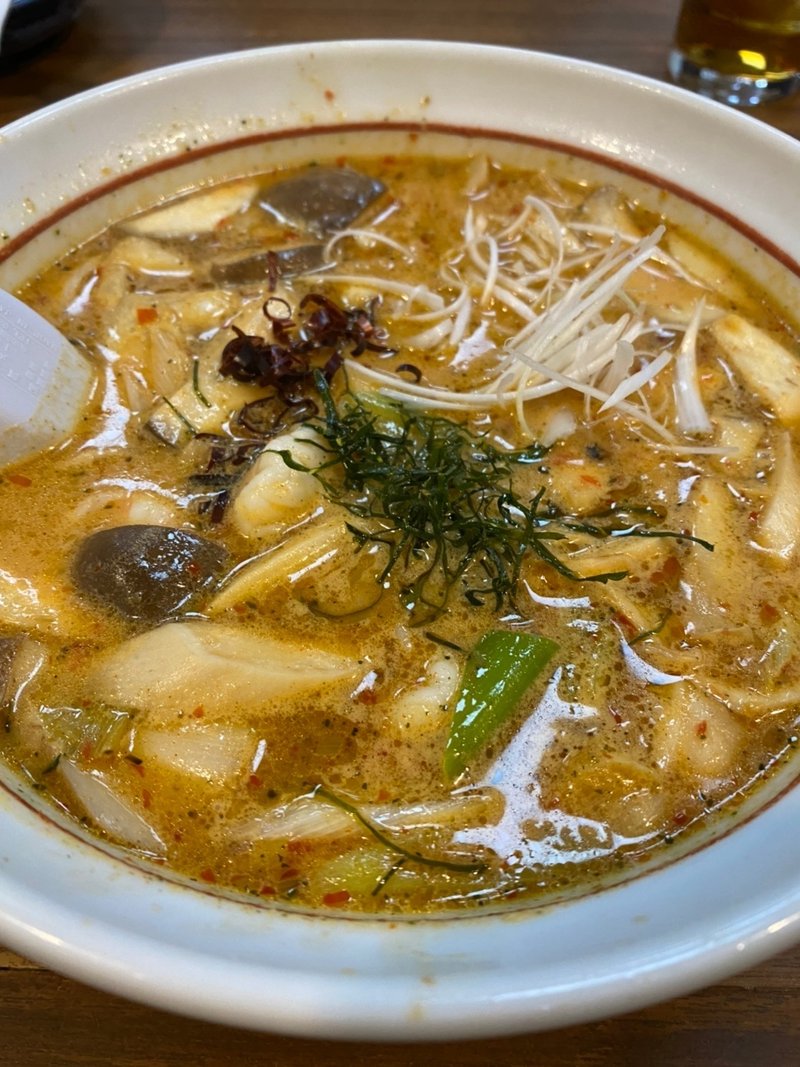
タイではライバルメーカーも多く差別化を図るため、コスト削減、海外向け標準プラントの計画をしているとのこと。
現地では移動に時間がかかるため朝が早いとか、、、海外好きにはもってこい🧳!(早起きの人もgood)
2日目 EG2課 EG3課
EG2課では改造、改修の案件を取り扱っているそうです!
社内では「04(ぜろよん)案件」と呼ばれていて、何だかカッコイイ!
実際に「原図検討会」に参加させていただきました。
原図検討会とは現地での現状確認やお客様の要望をもとに、解決策を考える会です!📝
2年目の先輩が現地調査をもとに提案をしている姿を見て、かっこいいなと感じました!
その後、出荷待ちの製品も見学させて頂き非常に勉強になりました。
EG3課では 日工のコア技術である「加熱・混練・搬送・制御」を活かして製品設計を行っています!
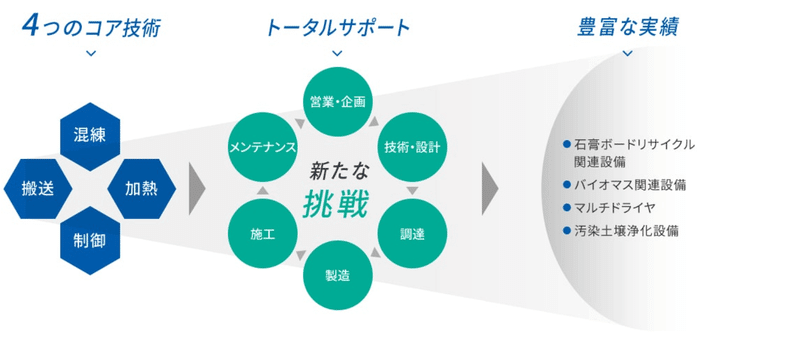
オーダーメイドかつ、前例のない装置の開発を行うため、1案件に3年近くかかるとか💦
例えば、エコタンカル製造装置という製品を開発したのですが、当製品は排水・排ガスを利用することで、商品の低コスト化・CO2削減を可能にしているエコな製品です♻
時代はカーボンニュートラル!
▼エコタンカルについては、以下の記事をご参照ください▼
3日目 制御設計1課 制御設計2課
制御設計1課はAP(アスファルトプラント)の制御設計業務を行っています!
バーナの温度制御も担当しており、研修中に温度制御の件で電話対応している姿も見ました!
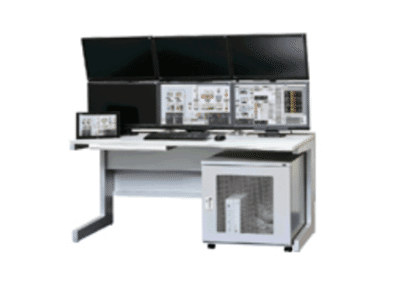
石や砂などの量とその含水率を考慮し火力を調整することで適切な温度を維持しているそうで、高度な技術が詰め込まれています!
操作盤はとてもスタイリッシュでかっこいいです~
次の週から東京研修に行く予定だったので、東京のおいしいご飯屋も教えてもらいました(^^)🍚
制御設計2課では主にBP(生コンプラント)の制御設計業務を行っているとのこと!電気回路のプログラミングを体験させてもらいました!
初めての挑戦で楽しかったですが難しかったです、、技術の方すごいなと感心しました。
4日目 制御システム
制御システム課では操作盤の企画・システム開発を行っています!
今までたくさんの操作盤がリニューアルされており、現在も改良化を進めているとか(^^)
最新の操作盤ではディスプレイの背景色を変更出来たり、配置を変えることが出来たりと、カスタマイズできるようになっていました!
プログラミングの練習もしました!
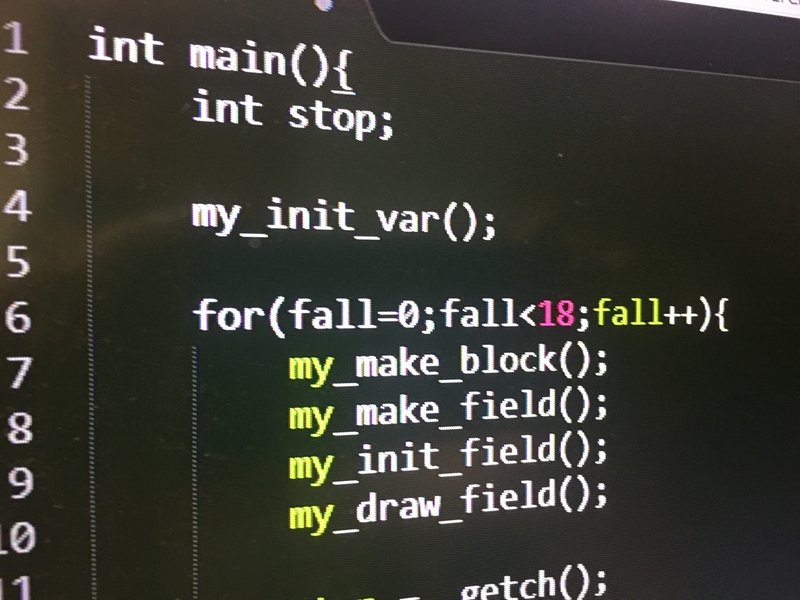
「C#言語」を使って頑張りましたが、関西弁しか習得していないのでさっぱり、、、🤷♂️プログラミング恐るべし。。
5日目 標準プロモーション課 設計品質管理課 原価積算課
標準プロモーション課では製品の標準化を促進しています!
APの「VPⅣ」は最新の標準製品であり、立体的に空間を使うことで小さい土地でも配置可能になっている画期的な製品!
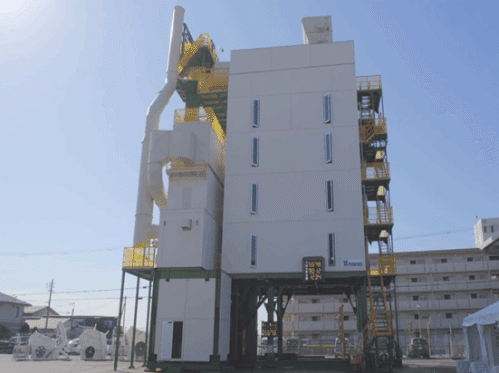
標準化された製品を販売することで、設計費・時間などのコスト削減・利益UPにつながるとのこと👏!!お金は大事ですよと(^^)
設計品質管理課ではクレーム処理・対策を行っているとのこと。
原因究明・再発防止に尽力中!
利益UPにはクレーム撲滅がかなりの近道。
クレームをなくすことで私たちのボーナスもUPですね😁!!!
また、新人時代のやらかしエピソードもたくさん聞かせていただき大笑いさせていただきました🤣🤣(超高級車をレンタルしたり、墓地の隣のホテルを予約したり、、)
原価積算課では製品完成までにかかる費用を計算しているそうです!
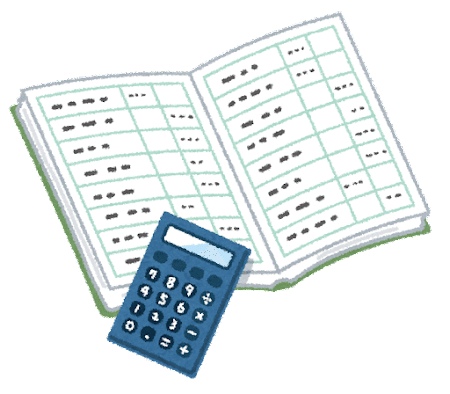
私たちの人件費・資材費・外注費など全てのお金を計算して原価を出していて大変そう、、社是にもあるように「適正利潤」を追求することが大事だと感じました。
安くしすぎても、高くしすぎてもダメ✖ 色々なものが値上がりしていて原価も高くなっていくんだろうなーと感じました、、😐
技術本部研修を通して
「プロフェッショナル!!」というのが私の印象です!
また、技術部内での異動が多いらしく、課が違うけど知り合いという方が多いと思いました。
会議やミーティングの数も多く、どんな仕事でもコミュニケーションが大事だと痛感しました!
それにしても技術本部の方々のマウスがデカくて高そうでした、いくらするんだろう🤔🤔??
技術本部のみなさん、ありがとうございました!
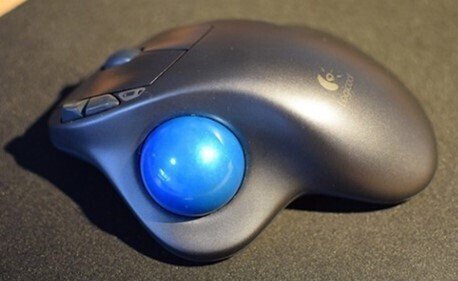
(広報もきになるぞ・・・!!「
ハイスペックマウス使ってる人は広報まで。)
ライター:新入社員🌸
協力:技術本部