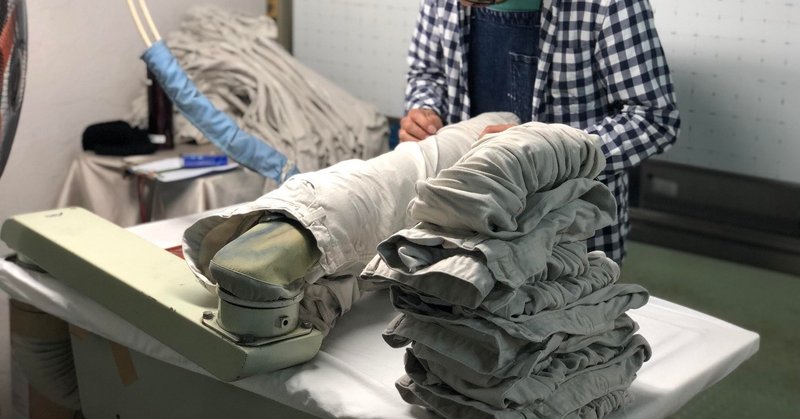
【Vol.1】そこは驚くほどに、「人」が働く世界で #えぶりツアー
以前からちょこちょこ告知していた通り、今月頭にEVERY DENIMの島田さんにアテンドいただいて、店舗メディアメンバーのみんなで岡山に工場見学へ行ってきました!
私は大学時代に管理会計を専攻していたこともあって人より工場見学に行く機会が多かったのですが(原価計算とかやるから)、実はファッションの現場にはほとんど行ったことがなく、はじめて見るもの・聞く話・知ることばかりで情報量が大変なことになったので複数記事に分けてお届けします。
今回お邪魔したのは、デニムの染色や加工をされているニッセンファクトリーさんと
▲今回案内してくれた島田さん。3人くらい子供がいそうな貫禄ですがまだ20代です。何の話だ。
デニム生地を製造する篠原テキスタイルさんの2つ。
まず、今回2つ工場に行かせていただいて一番衝撃を受けたのは、
えっっっっっこんなに人が仕事してるんや!!!!!!!!!!
ということ。
これまで私が訪れた工場はどこも消費財系もしくは車や製鉄関連ばかりだったので、普通にイメージする「ザ・工場」そのものだったんですね。
そのイメージが前提にあり、なんなら生地から縫製、加工までひとつの工場でほぼオートメーションでできるものだと思い込んでいた私にとっては想像以上の手作業工程の多さに驚きを隠せませんでした。
どのくらい手作業かというと、例えばジーンズのちょっとだけ白く薄くなってる部分も一枚一枚こうして職人さんが作業していて、
はじめからヒゲが入っていたりシワ加工されているものも、こうして手作業でシワを作ってアイロンを当てているという。
ちなみに上記の作業ではこういう「型」みたいなものがあって、これに一枚一枚ジーンズを履かせて作業するんですね。
シワの加減に細かい要望があるのはもちろん、女性用や男性用、ちょっとしたサイズ感によっても使う型が異なるので、なんとこのシワ加工に使う型だけでこんなにストックが!
\ ド ド ン /
(もちろんこれもほんの一部だそう)
商品じゃないもののストックもこんなにたくさん持たなきゃいけないなんて…!と震えました…。
あとすごく細かく工程が別れていたのも印象的でした。そういえばたしかに店頭に並んでるジーンズってほんとにいろんな加工の種類があるよな…と改めて思ったり。
もちろんそもそもの染色やすべてに共通する加工は機械でやっているのですが、ベルトコンベアで自動的に運ばれていくようなイメージを持っていた私にはすべてが衝撃すぎました。
▲今回工場を案内してくださったニッセンファクトリーの中西さん。あらゆる質問にとても丁寧に答えてくださいました…!
あと、染める色もお客様のオーダーにあわせた色がでるように毎回実験をしている、という話も衝撃でした。
ジーンズといえばブルー〜ネイビーのイメージが強いですが、そういえばホワイトジーンズだってあるし、ここ最近カラースキニーも人気だし、意外といろんな色が使われているんですよね。
実際、ニッセンファクトリーさんの会議室に展示されていたジーンズはめちゃくちゃカラフル!
▲染めについて説明してくれる島田さんの図
しかも全体を単一に染めるだけじゃなくて、ちょっとコーデュロイっぽい加工とかもできるという。
ちなみに染色って1回その色を作ってしまえば終わりだと思っていたら、繊維によって色の出方や風合いが変わるので、なんども染めの実験を繰り返してイメージの色味にあわせていくのだそうです。
配合が1%変わっただけで色の出方がだいぶ変わるという話が途方もなさすぎて、よくぞサジを投げることなく・・・!という気持ちになりました。
もちろん職人さんたちは知識やこれまでの経験からだいたいの目星はつけられるのだろうけど、『どこまでお客様の要望に近づけられるか』って本当に職人の領域ですよね。
色の出方を試すときは、小さな布をこの機械にいれて、一気にいろんな薬品を試してみるのだそう。いやもう、染めと加工だけでも語ることありすぎる…!
この加工の現場を見て改めて思ったのは、やっぱりファッションが消費財と大きく異なるのは『同じものを大量に作る』という要望がそう多くないところだな、ということ。
毎シーズン流行色も変わるし、ブランドのテーマデザイナーの感性にあわせて、それぞれいろんな要望があって、毎回その要望に答えていく必要がある。
特に最終工程は個性がでる部分なので、あの工程はいれてほしいけどこれはいらないとか、ここは他とこう変えて欲しいとか、たくさん要望があって、それに答えるにはラインで流すよりもこうしてフレキシブルに人が動く方が結果として効率がいいんだろうな、と思ったり。
生産リードタイムを短くするためにオーダーが入ってから製造しよう、と口で言うのは簡単だけど、こうして実際に加工の現場を見ると、そう簡単にオーダーでものが作れるわけじゃないんだよな、という当たり前のことを考えさせられました。
これはやっぱりどんなに言葉で説明しても腑に落ちて理解できるものではなくて、その空間を体験しないとわからないことだなと。
この体験を経た上で、どうすべきなのかを理論立てて考えられるようになりたい。
ちなみにもう一箇所お伺いした篠原テキスタイルさんでは、織りの工程だけあってずらーっと機械が並んでいて
『おおお、私の知ってる "工場"や〜〜〜〜〜〜〜〜〜!!!!』
と喜んでいた、のです、が・・・!
あれ、思ったより、、、遅い…!?!?!?!?!?
最新の織機って目にも止まらぬ速さでどんどん織りあがっていくのかと思っていたら、実は数ミリずつ、本当にちょっとずつしか織れないことにまず衝撃…!
でも実際は横糸がものすごいスピードで移動していて、昔の機械と比べてもすごい速さなんだ、ということがだんだんわかってきました。
生地って機械にかけてしまえば数時間で織れるのかな〜とふんわり考えていた過去の私、あほかと。
ちなみに糸さえあればすぐに織れるものではなく、機械にかける前にもいろんな準備があるので、なんだかんだ数週間〜1ヶ月くらいかかるのだとか。
そして一番衝撃だったのが、なんと縦糸はすべて手作業で変えているということ…!
写真に「4,320本」と書いてある通り、4000本以上の糸を一本一本針に通さないと生地が織れないなんて、、、そんなこと私学校で習わなかったよ、、、!!!
3本で根をあげる自信がある私としては、今回一番衝撃を受けた事実でした。
ちなみに熟練の職人さんでも数日がかりの作業だそうで、通常は縦糸はそのままで横糸だけ変えることで風合いや色味を変えたりするとのこと。
もちろん、まずは最終消費者であるお客様にとってベストなものを作ることが大切なのですが、こういうところで工数が増えるとそれだけ原価にものってくるわけで、そのバランスを見ながら依頼する知識が発注側にも必要なんだな、と改めて感じました。
でもさっきも書いた通り、この感覚はやっぱり現地に行って、機械や職人さんたちの作業を間近で見ることでしか得られない部分がたくさんあって。
日々テクノロジーの進化に関するニュースを見ているとなんでもテクノロジーによって一瞬で解決できそうに思えるけれど、『こうすればいいじゃん』ですぐに変えられるものばかりではなくて、それを理解した上で実感を伴って『考える』とは何か、について、岡山から帰ってきてずっとぐるぐる考えていました。
私はまだ何も本当の意味では『知らない』し、でも全部を知ることは不可能だと理解した上で、学びながら考えて、私なりに答えを出していくしかないのだなと。
言葉にするととても陳腐になってしまうのだけど、『作る』を感じるはじめの一歩が今回のえぶりツアーだったなあと思います。
ということで、だいぶ長くなったので、お話を聞く中で学んだ『産地』というエコシステムについての話は、vol.2に譲りたいと思います。
今日のおまけは、工場見学を通じて感じた『仕事の選択肢』について。
(今回はえぶりツアーの単発マガジンと店舗メディアマガジンのみでの公開となります!)
サポートからコメントをいただくのがいちばんの励みです。いつもありがとうございます!