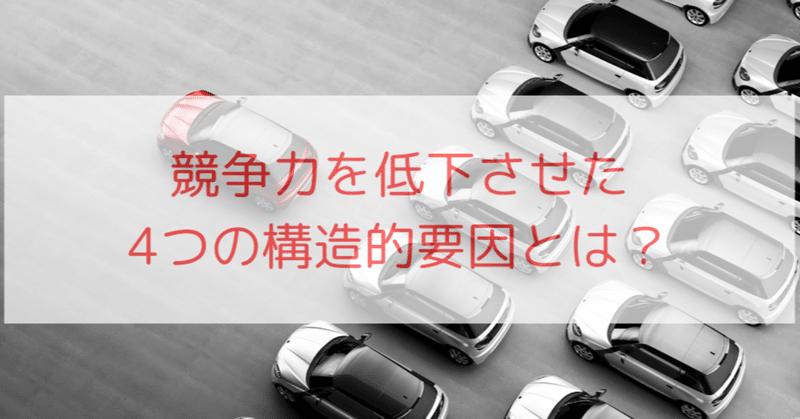
日本の製造業の競争力を低下させた構造的要因
前回の投稿では、「日本の製造業の成長を促した構造的要因」について書きました。
約30年前。
製造業の先進国として世界を魅了し続けた日本の製造業ですが、
現在は、先進国としての地位を失いつつあります。
今回は、「日本の製造業の競争力を低下させた構造的要因」について投稿したいと思います。
<日本の製造業の競争力を低下させた構造的要因>
21世紀はアジアの時代と言われる中で、
もっとも大きく成長したのが中国企業です。
『フォーチュン』が発表する「グローバル500」では、
1995年時点では3社だった中国が
2012年には72社と日本の68社を抜き、米国に次ぐ2位に躍り出ました。
さらに、2016年には100社の大台を突破して、
2019年には米国を抜き首位に立ちました。
ランクインした中国企業の9割が国営企業で、
エネルギー、インフラ、金融などの業種が多い状況です。
その他のアジア諸国に目を向けると、
台湾のEMS最大手の鴻海精密工業を筆頭に、仁宝電脳、広達電脳、台湾積体電路製造(TSMC)などのエレクトロニクス・電子機器メーカー。
韓国からは財閥系が変わらず強い状況ですが、
サムスン、現代自動車、LG、SKなどがランクインしています。
いずれも2000年代以降に、日本企業が競争優位を失った分野となります。
以下では、日本の製造業の競争力を低下させた要因を分析します。
1.円高と生産拠点の海外移転
戦後長らくブレトンウッズ体制の下で、1ドル365円に固定された為替相場は、日本の製造業の対米輸出にとって有利に作用していました。
1971年のニクソン米大統領による金ドル交換停止により変動相場制に移行すると、急激な為替変動を望まない西側先進国間の協調介入が行われましたが、1995年4月に1ドル79円75銭の最高値を付けるまでに円高は進みました。
こうした円高基調に加えて、1970年代から韓国・台湾・香港・ASEAN諸国などのアジアの新興国が経済発展に舵を切り、食料品や繊維などの労働集約的な産業から順に日本企業が進出をしていきました。
1980年代に入ると、改革開放経済へと転換した中国も、外資合弁による外国企業の誘致を積極的に行うようになり、日本企業も沿海部を中心に安い労働力を求めて進出していきました。
こうした流れを示しているのが、直接投資額の推移ですが、日本企業全体の海外直接投資残高を1996年末と2022年末で比べると、約704%増と8倍にまで規模が膨らみました。
製造業部門に焦点を当てると、1985年のプラザ合意を機に伸び始めており、日米貿易摩擦の激化による米国現地への生産移転などの影響が一部ありますが、基本的には円高による製造コスト削減を目的としたアジアへの移転が進んでいったのがわかります。
こうした流れはその後も変わらず、
1990年代前半は10%以下であった製造業における海外現地生産比率は、
2012年には20%を超えており、この間に倍増しています。
新興国の製造業の生産高が、先進国を初めて上回ったのは2014年のことになります。
こうした新興国には、メキシコやブラジルといった北中南米の国々、あるいは冷戦終結後自由主義経済圏に組み込まれた中東欧諸国や旧ソ連邦の国も含まれますが、2000年代に年平均10%の経済成長を遂げた中国を含むアジア諸国の存在感は圧倒的です。
この間に成長した韓国、台湾、ASEAN諸国を含めたサプライチェーンネットワークが構築され、東アジア地域内の貿易額は
1984年の約1,000億ドルから
2016年には約2兆2,000億ドルと
20倍以上に拡大し、そのうち中間財の占める割合も65%に達しています。
製造業の実質付加価値額を地域別に見ても、2008年のリーマンショック後の回復過程で、南北アメリカや欧州を抜き去り、圧倒的な優位を築いています。
この間に構築されたアジア域内の分業は、日本からアジア諸国に中間財を輸出し、相手国で組み立て加工を行い再輸出するという体制がとられたが、こうした役割分担も新興国の技術力の向上やグローバル企業の台頭によって構図が変化してきています。
こうした構造の変化を見る上で有効なのが、
経済協力開発機構(OECD)が定義する
グローバル・バリューチェーン(GVC)参加率という指標です。
GVC参加率は、
前方参加率と
後方参加率に
分けて見ることが有効です。
前方参加率が高い国は、
自国の輸出総額に占める中間財の輸出額が高く、
後方参加率が高い国は、
他国から中間財を輸入する額が自国の輸出総額に対して高い国となります。
上記の構成をアジアの製造業で見ると、
当初は日本が他国に中間財や資本財を輸出して、他のアジア諸国はこれらの輸入に基づいて組み立て加工を行うという構図でした。
その後、研究開発の拠点を輸出先の市場に近い場所に移した方が効率的であるという考えが進み、アジアにおける日系企業の研究活動が活発化しています。
これによって、現地採用人材の転職などを通じて、
現地企業への技術移転が進みました。
また中国は、クロスボーダーM&Aによる積極的な技術獲得を行っており、2010年代後半以降にはハイテク分野でのM&Aが半数以上を占めるようになっています。
「中国製造2025」でも、次世代情報技術、高性能NC工作機械とロボット、航空・宇宙用設備、新素材、バイオ医薬・高性能医療器械といった最先端技術を含む分野が重点領域として指定されています。
2.日本企業の資本蓄積の低下
高度経済成長期の日本の製造業は、安定した国内金融システムから供給される低金利の融資や株式の持ち合いによる安定した事業環境により、高度な資本蓄積を実現して競争力を高めていました。
こうした条件の変化は、1979年の外為法改正から始まったといわれていますが、もっとも大きなインパクトは、バブル経済崩壊による不良債権処理の過程で行われた株式持ち合いの解消と「金融ビックバン」と呼ばれた大規模な規制緩和でした。
企業の資金調達は、
銀行融資による間接金融から株式や社債による直接金融へと移行をし、
経営者は外国人株主や機関投資家が唱えるROA(総資産利益率)や ROE (株主資本利益率)などに配慮した資本活用を余儀なくされました。
この結果、経営者は自社の上げた利益を内部留保して将来的な生産力拡大に向けて再投資するよりも、配当やキャピタルゲイン獲得のための金融投資なども活用しながら、短期的利潤の獲得に邁進することになりました。
こうした株主資本主義とそれに基づいた短期的利潤の追求が、資本蓄積にどのように作用したのかは議論が分かれますが、実際にこの間の日本企業では、保有する総資産に占める金融固定資産の割合が高まっており、製造業においても株主に対する配当性向は上昇する傾向にありました。
1990年代以降の日本の製造業では、
資本装備率が上昇をする一方で、資本生産性が低下するという現象が見られました。(図-4)
図―4:日本の製造業の資本装率備推移(規模別平均、単位:万円/人)
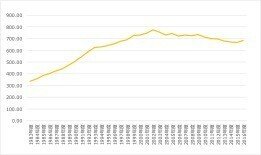
資本装備率は労働者1人当たりの有形固定資産の比率を指しますが、これは生産工程のオートメーション化や業務におけるITの活用などで省人化が進み、単位労働当たりの資本ストックが増えていることを意味します。
資本生産性は資本ストック1単位が生み出す付加価値額を示しており、この数値が低下しているということは設備投資などを含む資本ストックを効率的に利用できていないということになります。(図-5)
図―5:日本の製造業の資本生産性推移(規模別平均、単位:%)
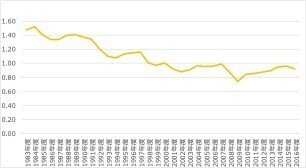
資本装備率が上がっているにも関わらず資本生産性が上がらないのは、労働生産性が低いということも意味しており、これは日本の製造業が解決すべき課題のひとつと言えます。
3.日本の労働人口の減少と労働生産性
日本の人口構成上、生産労働人口は1995年をピークに減少を続けています。
生産労働人口の減少は、経済成長に不利に働くと見られがちですが、単位労働当たりの労働生産性を向上させることで逆転が可能となります。
日本全体の労働生産性を、労働者1人当たりの生産性と時間当たりの生産性の両方で国際比較をして見ると、
1990年に労働者1人当たりの労働生産性が13位まで上昇しましたが、
その後は20位前後で推移をしており、OECD加盟国では下位の方に低迷しています。
2021年の比較では、コロナ禍で落ち込んだ労働生産性の回復が十分に進んでおらず、
就業者1人当たりでは29位に、
時間当たりでも27位にまでランキングが落ちました。
日本の労働生産性を産業別に見ると、
一般的にサービス業に比べて製造業は生産性が高いといわれています。
ただ、その製造業も2000年から2020年までの20年間の年率平均の上昇率を見ると、日本の1.4%に対して
米国と英国が3.0%、
フランス1.6%、
ドイツが1.3%です。
トヨタ生産方式などの優れた現場力を持ちながらも、
これらをデジタル技術やAIなどのテクノロジーと効果的に結びつけていくことができていないことが読み取れます。
労働生産性を考える上でもうひとつ重要なのが、従業員への教育投資です。
1990年代後半以降、終身雇用制や年功序列などの日本型雇用システムの変革が求められ、長引く不況の中で若年労働者の採用が抑えられるなど、過去30年間で従業員教育を取り巻く環境は大きく変化しました。
その中で、2004年の製造現場への労働者派遣解禁には注目する必要があります。
2008年には56万人とピークを付けましたが、
翌年にはリーマンショックの影響で半減し、その後再び増加に転じました。
コロナ禍の一時的な落ち込みはありましたが、
2022年には41万人にまで拡大しています。
派遣労働という仕組みは、
雇用の調整を進めやすくし、労働者の働き方の柔軟性を促進するというポジティブな面がある一方で、生産現場の技能や暗黙知の共有が進みづらくなるという弊害もあります。
合わせて重要なのが、従業員に対する人材投資です。
GDPに占める企業の能力開発費の割合を国際比較すると、
日本企業は1995年の時点でも欧米各国と2倍以上の開きがあります。
さらにこの割合は徐々に低下しており、
逆に増加傾向にある各国との差はますます開いてきています。(図-6)
図―6:主要国のGDPに占める企業の能力開発費

近年、日本企業でも人的資本経営や従業員のリスキリングといった課題に注目が集まっているが、DX人材の育成のみならず全般的に従業員教育に力を入れていく必要があります。
4.失われつつある技術優位性
日本の製造業で資本装備率が増加しているにも関わらず、
資本生産性が低下している点はすでに指摘した通りです。
ここでは改めて、TFP(全要素生産性)に着目して分析をします。
まず全産業のTFPを国際比較すると、
1992年の対米比61.9%をピークに格差が縮まっていません。
欧州諸国が対米比80%~90%で推移しているのと比較しても、
低い水準にとどまっています。
製造業は1990年代まで対米比90%以上で推移しており、
2009年時点でも84.4%と全産業に比べて高い水準でしたが欧州諸国と比べると低い水準です。
2009年時点の対米比を業種別に見ると、
一般機械で116.3、
輸送用機器で96.6(いずれも米国を100とした場合)と
そん色はありませんが、
電気機器では71.7と大きく差をつけられています。
このように、製造業においても国際的に後れを取っている要因としては、先に述べたような資本蓄積の伸びが鈍化していることに加えて、資本の利用効率の改善や技術革新(イノベーション)が足りていないことが推定されます。
イノベーションについて、
世界における位置づけはどのようになっているのでしょうか?
世界知的所有権機関(WIPO)が毎年発表している国際イノベーション力指標(GII)を見ると、2023年の日本のランキングは13位でした。
米国(3位)、
英国(4位)、
ドイツ(8位)、
フランス(11位)といった欧米諸国だけでなく、
アジア諸国の
シンガポール(5位)、
韓国(10位)、
中国(12位)にも抜かれています。
この状況の打開は容易ではありませんが、
例えば90年代以降世界をリードしてきた、
対GDP比のR&D支出額を増加させることは1つの方法かもしれません。
1990年代に民間への導入が進んだITは、インターネットが元々米軍の軍事用ネットワークであったように、軍事技術の民生転換として産業界に大きなパラダイムシフトを引き起こしました。
日本はITやインターネット関連の規格仕様に関する競争では敗れましたが、製造業におけるIoT化などの応用技術は元来日本が得意としてきた分野です。
デジタル技術やAIの積極的な活用により、市場ニーズに適した製品を迅速に展開できれば、高い付加価値を提供できるようになるかもしれません。
■ 「ものづくり先進国」の地位を再評価される可能性を秘めている
ここまで戦後日本の製造業を振り返ってきましたが、日本企業を苦しめてきた円高水準は緩和され、新型コロナウイルス感染症やウクライナ紛争を機に始まっているサプライチェーンの見直しは、再びかつての輝きを取り戻す契機となる可能性があります。
1990年代以降は「失われた30年」と評価されることが多いですが、日本の製造業には高い国際競争力を保持している分野も多くあります。
今回、課題として明らかになった
「資本の効率的活用」
「人材投資」
「イノベーション」
これらの問題に取り組むことで、再び「ものづくり先進国」としての地位を取り戻すことができるのではないでしょうか。(山縣敬子・山縣信一)
<<Smart Manufacturing Summit by Global Industrie>>
開催期間:2024年3月13日(水)〜15日(金)
開催場所:Aichi Sky Expo(愛知県国際展示場)
主催:GL events Venues
URL:https://sms-gi.com/
出展に関する詳細&ご案内はこちらからご覧ください。
<<これまでの記事>>
諸外国の「ものづくり」の状況とトレンド①
諸外国の「ものづくり」の状況とトレンド②
諸外国の「ものづくり」の状況とトレンド③
日本の製造業の歴史を紐解いてみる
日本の製造業の成長を促した構造的要因とは?