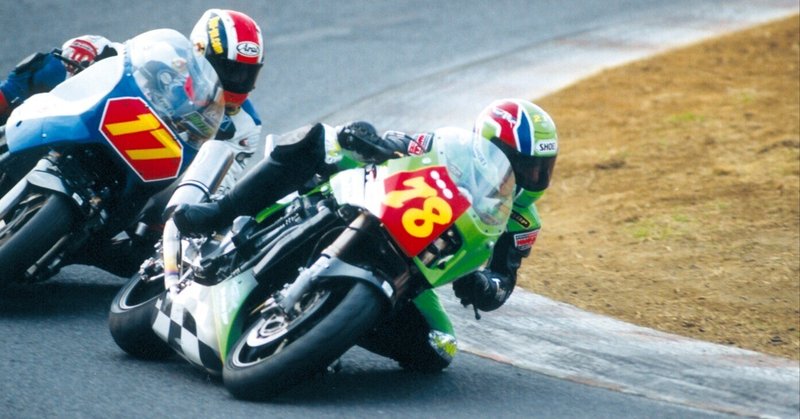
■AUTOMAGICイズム■ 第六章・DFCでカスタムをもっと自由に その1
序章:純正パーツ流用、エンジン移植とカスタムの内容が大がかりになっても、あいかわらず補強や加工レベルから抜け出せなかったのがフレームだ。独創的なカスタムマシンを製作するためには、スタンダードフレームの壁を超えなくてはならない。そうした考えからオートマジックが開発したのがDFC=デュアル・フレーム・コンバインドである。
このコラムで何度も語ってきたが、他人が思いつかない着眼点や発想で、独創的なアイデアをカタチにするのがカスタムバイクショップがあるべき姿であると思う。ビジネスとしてショップを営むからには、バイクユーザーが希望する仕様でカスタムを行うことも必要だが、それだけに終始せずユーザーや他のカスタムショップに刺激を与え、関心を呼び込むような仕事を続けなければならない。マンネリ化が進むことでカスタム文化は停滞し、ユーザーからも飽きられてしまうのは目に見えている。
僕は常々そう考え続けており、世の中の流れとタイミングを計算して新たな提案を行ってきた。バイクの骨格であるフレームに大胆にメスを入れ、新たなディメンションや価値を作り出す「DFC=デュアル・フレーム・コンバインド技法」もそのひとつだ。
二台分のフレームを継ぎ合わせて新たなフレームを生み出すというと、いわゆる「ニコイチ」を想像する読者も少なくないだろう。この技術を発表した時、エンドユーザーだけでなく周囲のバイクショップからもそうした声は聞こえてきた。しかし我々のDFCはそんな安っぽいものではなく、バイクカスタムをこれまでよりさらに自由に、新たな次元で実現するために作り出した技術である。
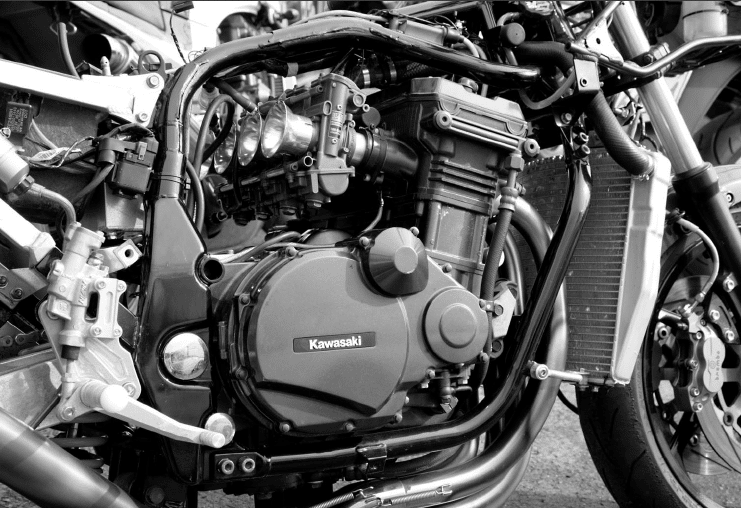
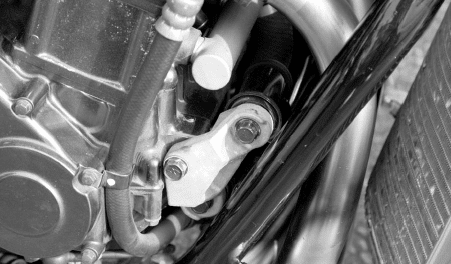
流用できる。 純正パーツを効果的に流用することで
フレー ム剛性アップと信頼性を両立できる。
【サーキットでは使えない強度不足のアルミサブフレーム】
DFCの原型が世に出たのは1999年、ツインリンクもてぎで行われた「もて耐」参戦用マシンが最初だった。それ以前からスズキカタナ用フレームに油冷エンジンを搭載したカスタムマシンを手がけていた我々は、GSF1200用スイングアームピボットをカタナ用フレームに移植したマシンを製作した。そうすれば後部エンジンマウントやスイングアームの流用が簡単にできると思ったからだ。ところが車体のディメンションを深く考
えず作業を行ったため、スイングアームの垂れ角やサスペンションセッティングの帳尻合わせに苦労するハメになった。しかし苦労すると同時に、この経験から「バイクはピボットとヘッドパイプを要としたアライメントSETである」という僕なりの定義ができたのである。
そしてその翌年、2000年のもて耐において、GPZ900Rニンジャのフレームモディファイ技法としてカタチになったのがDFCの第一作である。きっかけはチューニングショップであるパワービルダー( 現在ではTOTのトップチームのひとつである)からの協力要請で、強度不足のサブフレームを何とかして欲しいというものだった。
この頃(現在でもそうだが)、ニンジャ用の定番カスタムパーツのひとつにアルミ製ボルトオンサブフレームキットがあった。
エンジンの前側にダウンチューブを持たないダイヤモンドフレームのニンジャのフレーム剛性を上げるのと、サイドカウルとアンダーカウルを外した時の見た目の良さが人気の商品だった。
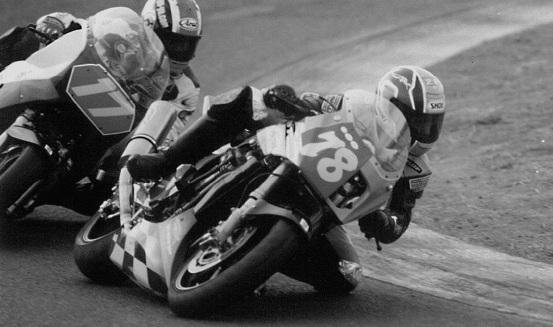
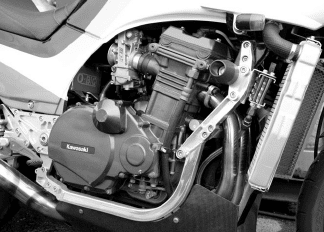
同様に、ニンジャのチューニング手法として広がりつつあったのが、後継モデルである水冷GPZ1100用エンジンの移植だった。ニンジャと同じサイドカムチェーンの腰下で、ニンジャよりコンパクト化されたヘッド周りを持つGPZエンジンは、最初から1100㏄の排気量を持つこともあって、比較的手軽で効果的な純正流用カスタムだった。
ところがニンジャとGPZエンジンは、フレームへのマウント位置が異なるのだ。具体的には、ニンジャエンジンはシリンダーヘッドとダイヤモンドフレームがマウントされるが、もともとダブルクレードルフレームに搭載されたGPZエンジンは、クランクケース前側にマウントがある。従って、GPZエンジンを搭載するためのサブフレームキットには、GPZエンジン用マウントが装着されているのだが、サーキットをレースペースで走行すると
何度補修してもサブフレームにクラックが入って使い物にならないというのだ。
考えてみれば、M8程度のボルトで固定されたアルミ製パーツが純正スチールフレームの強度に叶うはずもなく、レース用にチューニングされたGPZエンジンのストレスはすべてサブフレームに集中してクラックが入るのは当然だ。要するに、強度部材としては期待できないアクセサリーパーツに過ぎなかったわけだ。ちなみに、アルミダウンチューブ+スイングアームピボット兼用のバックステップを使用してエンジンを載せ替えるというカスタ
ムは定番の手法であり、その手順を示すことで公認車検を取得することができる。サーキットを走れば割れてしまうアルミサブフレームでもお墨付きがもらえてしまうのだ。まさかと思うかも知れないが、これも事実である。
【ダウンチューブのみ流用から効果の高いDFCへと発展】
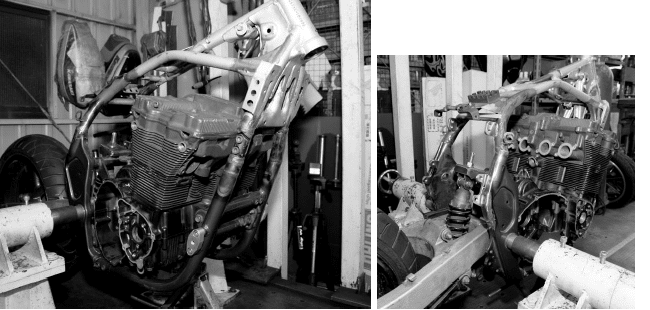
ヘッドパイプ周辺の溶接を変更せず、2分の1以上の 基本骨格を残すという
陸運局の解釈に従いつつ、
カタナのディメンションをもっとスポーティに変更する。
ディメンションを自由に設定できるのがDFCの大きな利点である。
サブフレームが割れると聞いた僕が直観的に考えたのは「だったらクロモリパイプでダウンチューブを作ればいい」というものだった。見かけ倒しのアルミ削り出しよりも、フレーム素材に近いクロモリ材の方が、よほど強度があるはずだ。またボルトオンというマウント方法も見直して、フレーム全体でエンジンの荷重を支えられるようにしようと思った。
アイデアはすぐに浮かんだものの、当時はレースが間近に迫っていて時間が無く、とてもクロモリ製サブフレームをワンオフ製作している余裕はなかった。そこで気づいたのが、工場の裏に積んでゴミとなる予定だったGPZ1100用フレームだ。ニンジャに搭載するエンジンがGPZ用なのだから、そのエンジンが乗っかっていたフレームも利用できないか、と着眼したのだ。
これならダウンチューブにラバー付きのエンジンマウントが最初から付いているし形状もGPZエンジンにピッタリなのだから、流用はもってこいだ。同時にスイングアームとピボット近辺までの一式を使えば、
リア側のエンジンマウントもGPZ用でいけるはず。前年のカタナフレーム+GSFピボットの組み合わせで、スイングアームピボットを中心としたディメンションの重要性を痛感していたから、ドライブスプロケットが付くカウンターシャフトと
スイングアームピボット、それとリアアクスルシャフトの位置関係は純正のディメンションを大きく変更しない方がセッティングを出しやすい。
そんな経験もあったから、僕はGPZフレームの下半分、つまりダウンチューブの途中からスイングアームとピボットの上までを使い、その上にニンジャフレームの上半分をかぶせて完全なダブルクレードルフレームを製作することにした。とはいえ2台のフレームを都合良く接合できるかなんて誰もチャレンジしたことのない領域なので、エンジンを収める空間やニンジャフレームとの相性など全くの手探り状態だった。
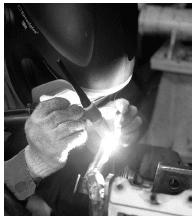
ノウハウが必要だ。
ジグ でガッチリ押さえつつ、歪みを逃が すように溶接を行うことで
ビシッと 芯が通ったフレームが完成する。
それでも物は試し、案ずるより生むが易しの精神で2台のフレームを切ってみた。ここで役に立ったのが、オートマジック開業時に独自に設計したフレーム修正ジグである。フレームの測定や修正を行うジグは、シート高、メインフレームとエンジンのクリアランス、理想のキャスター角度、ピボットとヘッドパイプ間の距離設定など、試行錯誤でおっかなびっくりながらデメリットのでないディメンションを決めるのにとても役に立った。逆にいえば、このジグがなければDFCは完成しなかったといっても過言ではない。
この経験を元にDFCの可能性を確信した僕は続く2001年、テイスト・オブ・フリーランスF-ZEROエクストラクラスにDFCニンジャでエントリー、初参戦初優勝を達成。これが契機となりDFCへの注目度が一気に高まったのだ。
【自由な発想を邪魔する外野の声には耳を貸さない】
その一方で、この手法に対する疑問の声や陰口めいた意見があったのも事実である。レースに参戦することでポテンシャルの高さを証明し、極限的なテストによる耐久性を示し、実際に優秀な成績を獲得することでショップとしてのステイタスを得る。そうしたプロセスが街乗りカスタムにフィードバックされることでブームが生まれて新たなカスタム文化や価値が創造されることを狙ってきた。
ところが、保守的というか頭の固いショップの中には、フレームを切ってまで改造するのはどうか、あれではニンジャと呼べないとまで言う者もいた。ではサーキットを思い切り走れば割れてしまうアルミサブフレームをユーザーに提供し続ける姿勢はどうなのだろうか。そんなシビアな使い方をするユーザーはごく一部だと反論(僕に言わせれば言い訳だ)するかもしれないが、最終的にそういう壊れ方をする製品をサブフレームとして供給しようとする姿勢の方が、ユーザーに対する裏切り行為であると思う。
もちろん、創業当初から公認車検に対して人一倍のこだわりを持つ我々は、このDFCが街乗りバイクとして合法なのか否かも陸運局に確認している。その結果、DFCは切開鈑金や移植鈑金の範疇に入る作業であるというのが先方の答えだった。例えば、転倒して車線外に滑り出てダウンチューブやエンジン下のパイプを縁石にぶつけて潰してしまった時、そのパイプが再生不可能な場合は同程度の強度を持つパイプや同機種の同部位を移植鈑金するのは、補修上問題のない手法である。
この移植鈑金の範囲を拡大してダウンチューブからスイングアームピボットまで切開して移植したものがDFCであると解釈されたのだ。だからといって、車台番号が打刻されたヘッドパイプだけを切り取って他のバイクに移植することは許されない。それはチューニングやカスタムではなく明らかな違法行為である。それもあって、陸運局からは「ヘッドパイプに接合している溶接部分は剥がさず、ヘッドパイプを含めた2分の1以上の基本骨格は残しなさい」という付帯事項が付くことになった。アルミサブフレームを用いたエンジン移植で公認車検が取れることは先述したとおりだが、DFCニンジャは割れる可能性能あるアルミをスチールに、細いボルトを溶接へと、材質と接合方法を変えたものだというのが陸運局の解釈なのである。
こうした手法を思いつかなかった、あるいは実践できない人々のヤジには耳を貸さず実現化に至ったのがDFCだ。次号ではこのDFCが持つポテンシャルについて、さらに具体的に紹介していこう。
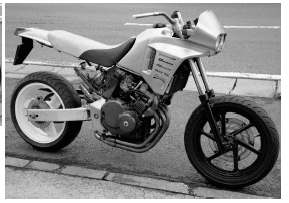
お 客さんからのオーダーで製作しているのはホン ダAX-1とホーネットを
合体させたDFCである。
オフモデルがモタード的なオンロード寄りにカ スタムされるのはあるが、
4気筒のオンロード モデルがオフ風になるのが斬新だ。
この記事が気に入ったらサポートをしてみませんか?