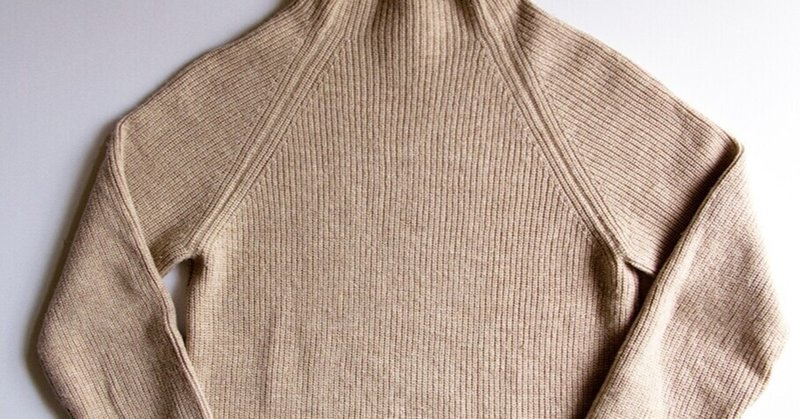
#03 ニット製品のつくり方(成型編)
ニット製品を企画する時、どんな作り方があるのか知らない人、知っていてもそれぞれの作り方に、どんなメリットやデメリットがあるのか理解して作れている人は多くないのではないでしょうか?
そこで、今回から全3編(成型編・カット編・ホールガーメント編)に分けて、ニット製品がどのように作られるのか、それぞれのメリットとデメリットを書きながら紹介していこうと思います。
ここに書かれる事は、私がこれまで関わってきて感じている事なので全てではないですが、「ニットだから成型」とか「ホールガーメントなら色々できる」と思ってた人が、これを読んだ後作るものに対して適切な作り方を選択できる一助になれたら良いなと思います。
(※2020.05.04 メリットその⑤加筆しました)
- 作り方の種類 -
ニットの作り方は、大きく分けて
①成型編みで編まれたパーツをリンキング縫製
②型紙をもとにカットしたパーツをミシンで縫製
③①と②の組み合わせ
④ホールガーメント機による無縫製
の4種類があります。それぞれに得意な面、苦手な面があるので自分が作るものにとって何が有効か考えて選択するといいと思います。
※編み組織によってできる・できないがありますが、今回はそのことには触れません。
一回目の今回は、成型編みを使った作り方について実際に作られる順序で書こうと思います。
- 編み立て -
成型編みは、ニットらしい作り方として昔から作り続けられてきた方法で、編みながら身頃や袖、衿などの形を作っていく編み方です。編み終わるとそれぞれのパーツができ上がっています。手編みで作るニットも、こちらに分類されます。
袖ぐりや肩線、衿ぐりなどのカーブを減らし目や増やし目、引き返し編みなどを組み合わせてカタチにしていきます。
- 縫製 -
そうやってパーツごとに編まれたものを縫い合わせて製品の形にしていきます。成型で編まれたものは耳使い(編み端使い)が基本となり、本縫いのミシンで縫う場合もありますが、多くの場合はニットならではのリンキングという縫製方法で作られます。(編み端が丸まりにくい編み組織の場合は本縫いミシンで縫うこともあります)
リンキングミシンの種類
・ダイヤル式のリンキングミシン
(※下の画像は丸安毛糸HPより転載)
リンキングミシンには2種類あり、円形のリンキングミシンと直線のリンキングミシンがあります。写真のミシンはダイヤル式のリンキングミシンです。ダイヤル式の場合、針(矢)が円形に配置されているので、長い距離の縫い目でも止めることなく縫い続けられます。
ただ、ミシン自体が大きく、スペースが必要だったり家庭用よりも高い電圧が必要だったりで、ある程度規模がある工場で見かけることが多いです。
・八角(やすみ)のリンキングミシン
(※画像は圓井繊維機械株式会社HPより転載)
家庭でも使えて持ち運びがしやすく、電力を必要としないリンキングミシン。ニット産地では内職さんにお願いして縫っていただく文化が残っているので、まだまだ活躍しているミシンです。ダイヤル式は大きいので、置き場所が確保できない工場も使っていたりします。
ただ、ダイヤル式のものと違って針が直線状に並べられ、本数も限られているので、ロングカーディガンなど縫い目の距離が長い物は2回に分けたりしながら縫製します。なので、その分糸の仕末をする箇所が増えます。
どちらのミシンでも、リンキング自体は矢(や)と呼ばれる針に手で1矢1矢挿して縫っていきます。衿などのパーツは、1目1目編み目に矢を入れながら縫うので、ゲージ(※ゲージについては#02の記事を参照)が細かくなればなるほど難易度が上がっていきます。
縫い目も本縫いのミシンとは異なって伸縮性があり、ジーンズの裾にされるチェーンステッチと同じ縫い目になります。チェーンステッチなので簡単にほどけます。
なぜほどける縫い方になっているかは、よくわかりません。縫い方自体に伸縮性をもたせるとチェーンステッチになってしまうのか、『ニット製品はほどいていくと最終的に毛糸玉に戻せる』というニットならではの作り方からほどきやすいようにしているのか。いずれにせよ、ステッチ自体が伸縮してくれるおかげでニットの伸びにある程度ついてきてくれるので、非常に相性の良い縫製方法です。
また、縫製糸にスパン糸でなく、共糸(身頃と同じ糸)や似た素材の糸を使う事ができるので、縫い糸を目立たなくする事もできます。(糸が細いと切れやすいので、ローゲージ〜ミドルゲージの時がオススメ)
ただ、リンキングは本縫いミシンよりも縫製時間がかかってしまうし、生産背景の面でいうと、ゲージが細い製品ほど針や編み目が小さく見えにくくなる為、縫い手さんが高齢化してくると老眼などで縫えなくなってきます。現状、縫い手さんは減少してきているので、今後どう解決していくのか考えていかないといけないと思います。
(※それを解決したのがホールガーメントなのですが、その話はまたホールガーメント編で書きます。)
- 加工〜アイロン -
それぞれのパーツを縫い合わせて形にした後、加工がない場合は最後にアイロンで形を整えて完成です。縮絨や湯通しなどの加工がある場合は、製品のかたちにした後に加工をしてアイロンをします。なぜパーツでなく製品の状態で加工するかというと、
・パーツで加工する場合
①編み終わり
↓
②各パーツ、加工で糸がほどけないように一部仕末
↓
③加工
↓
④パーツごとに仕分け(加工はパーツごとにせず、着分まとめてするため)
↓
⑤残った部分の仕末
↓
⑥縫製
↓
⑦糸仕末
↓
⑧アイロン
となります。それに対して
・製品で加工する場合
①編み終わり
↓
②各パーツ仕末
↓
③縫製
↓
④糸仕末
↓
⑤加工
↓
(場合によって、仕末あり)
↓
⑥アイロン
となり、工程を少なくできたり、製品の行き来を減らすことができます。特に、パーツで加工した場合の④の仕分けは、着数が多くなるほど大変になりますし、量産の場合は取り違いなど間違いのもとにもなるので極力避けるべきだと思います。
また、袖だけとか身頃だけとか、パーツの種類ごとに加工すれば良いんじゃないかと思うかもしれませんが、加工の強弱が一着の中で出る可能性があるためオススメしません。右袖と左袖の加工具合が違うと、見た目やサイズが変わってきてしまうので。
まれにパーツの状態で加工する場合がありますが、多くは加工前の状態だとパーツが大き過ぎて扱いづらいなど、縫製が大変などの理由がある場合が多いです。
このような工程を経て、成型の製品は作られています。
- 成型で作る場合のメリット -
ここまで成型製品の作られ方を書いてきましたが、ここからは成型で作る場合のメリットとデメリットについて書いていきます。
・その①:編み端(耳)をそのまま使用するので、縫い代を少なくできる。
成型を選択する理由の多くがこれだと思います。ニット製品をカットで作る場合、糸の滑脱などの問題から少なくとも縫い代は8~10mmは必要ですが、成型の場合編み端をそのまま縫い代として使用するので、ほどける心配がなく、縫い代を少なくできます。そのためゴロつかず、すっきり仕上げることができます。
・その②:原料のロスを少なくできる
『パーツのかたちに編む=余分なロスが出ない』ため、カットで作るよりも使用する原料を少なくできます。特にカシミヤのような糸の単価が高い場合、糸のロスを極力少なくして原価を抑えたいので成型にする場合が多いです。
・その③:リンキングが伸縮性のある縫い方なので、ニットの伸びについていける
作り方でも触れましたが、リンキングは本縫いのミシンで縫うよりもループのかたちを作りながら縫われる(チェーンステッチ)ため、伸縮性があります。
リンキングミシンの糸調子のとり方も、通常の見た目のキレイさだけでなく伸びも考慮しながら調整できるため、着心地を良くすることもできます。(※縫製する際にどの位の伸びが必要なのか指示を出せるとなおグッド。)
・その④:裁断の工程が無い
それぞれのパーツが、それぞれのかたちに編まれるので、裁断の必要がないです。なので、作業場のスペースが限られていてもできる方法かなと思います。
※カットの場合にかかる裁断の工賃がなくなるから、工賃も減るんじゃ?と思うかもしれませんが、編み上がった後の糸仕末や、縫製にかかる時間がカットの場合よりも長くなるので、必ずしも工賃が安くなるわけではありません。
・その⑤:ファッションマークをつけられる
袖ぐりや衿ぐり(場合によって肩線)などで、目を立てて減らし目をする(内ベラシ)と、目を移したあと(ファッションマーク)が残ります。
ファッションマークはデザインアクセントとして使われることがあり、特に天竺のような無地の場合に多く用いられます。
また、リブや片畦のような編地の場合、ファッションマーク自体はわかりにくいですが、目立てがデザインポイントになります。
- 成型で作る場合のデメリット -
・その①:編み時間がかかる
ただ四角形に編むカットの場合よりも、目を重ねて目数を減らしたり、目を増やしたりしながらかたちを作っていくので編むのに時間がかかります。そのため、編み工賃が高くなります。
・その②:カーブなどのラインの再現性が低い
編み目の大きさによって、再現できるラインが全く異なります。1目1目が大きいローゲージのものと、1目1目が細かいハイゲージのものでは、再現性が高いのはハイゲージの方で、ローゲージは再現性が低いです。特に3Gや5Gは、1目が5~7mm、ものによっては1cmあるのでカクカクしたりします。
・その③:詰められる度目に限界がある
目を重ねたり増やしたりするのに、ある程度糸の引っ張り加減に余裕がないと編みキズが多発してしまうので、「もっと度目詰めてほしい!」と思ってもできないことが多々あります。
特に耳の部分はどうしても伸びて編まれてしまうため、度目で解決できない場合は編み組織を変更した方が良いと思います。
・その④:成型の方がカットで作る場合よりも、使用できる糸の数が少なくなる
これは機械上の制約になりますが、編み機にはキャリアと呼ばれる糸道があり、キャリアの数によって使用できる糸の数が変わります。(機械によって数は変わります。)
カットだと捨て糸で1つ、抜き糸で1つキャリアを使い、残りのキャリアを使って編み組織を考えますが、成型(特にVネックのように衿ぐりが深いもの)の場合、前下がりよりも上を編む際に別のキャリアが必要になるので、捨て糸と抜き糸以外に必ず必要なキャリアが増えてしまいます。その為、四角くガーメントを編む時よりも糸道が減る為、使用できる糸の数が少なくなります。
また、ロット違いの色の差異を無くしたり生産がスムーズに流れるようにする為などなど、様々な理由からパーツごとでなく1着ずつ編み進めることが多いのですが、各パーツによって使用するキャリアの数が変わる場合(配色や形によって)一番多いパーツを基準にするので、使えるキャリアが限られてしまうこともあります。
・その⑤:編む側のスキルが求められる
デメリットの②と③をクリアして、ちゃんとした形にできるかどうかは、編む人のスキルに大きく左右されます。パーツの形に編むということは、パターンの知識と編む技術を摺り合わせながら行う作業なので、型紙を渡しただけでクリアできるわけではないです。
型紙の形にデータを作っていく時、どうしても再現できない不具合(肩の傾斜や袖ぐり、衿ぐりのラインなど)が発生します。特に、柄によっては穴があいたように見えたり柄が途切れたように見えてしまう場合が多々あります。
そんな時、ちゃんと工場側に指示を出せるパタンナーさんがいたり、依頼するブランド側に指示を出せる人がいる場合はいいですが、多くの場合工場側にパタンナーさんがいないことが多いですし、ブランド側も指示を出せないことが多いです。
なので、編む人にはパタンナーと同じ能力(型紙を引く力)が求められますし、編める編めないを繰り返しながら指示された形に近づくようデータ(柄)を作っていきます。
そういった様々なバランスを取りながら形にしていくので、編む人によって見た目(特に衿ぐりや袖ぐりなどのラインや柄の出方)が変わるし、人によってできるできないもあります。
なので、お願いするニッターさんがどのくらいできる人なのかを見極める必要があるかなと思います。
・その⑥:個体差が生まれやすい
ニットはもともと乱寸が出やすいです。同じように作っても、寸法が1cm前後違うことは往往にして起こります。
カットで作る場合、編み地自体のサイズが違っても型紙に合わせて裁断するので大きく寸法が変わることは少ないですが、成型の場合編まれたものがそのままサイズに影響してくるので、乱寸が出やすい編み方だと同じサイズ内で色んな寸法の製品が出来てしまう可能性があるので注意が必要です。
- 終わりに -
色々とメリット、デメリットを書きましたが、ちゃんと理解すればカットやホールガーメントとは違った、成型の製品にしか出せない雰囲気や着心地のニット製品ができるので、是非挑戦して欲しいなと思います。
デメリットの多くは企画の仕方(デメリットを許容出来るような編み組織やデザインの選択など)や企画側と工場側のコミュニケーションで解決できることが多いので、企画する人はニッターさんに沢山相談して知識を吸収して欲しいですし、ニッターさんはどういう所が企画者のこだわりポイントなのかやりとりを通じて理解できるとより良い製品が出来ると思います。
長文になりましたが、お付き合いありがとうございました。
次回#04は『ニット製品のつくり方(カット編)』になります!
いただいたサポートは、活動費に使わせていただきます。